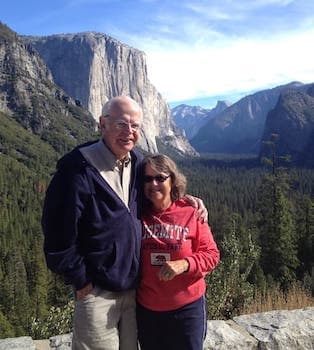
Curated with aloha by
Ted Mooney, P.E. RET
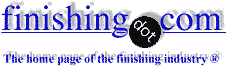
The authoritative public forum
for Metal Finishing 1989-2025
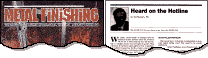
-----
Copper plating onto steel in a small shop
I build steel drums, musical instruments born in Trinidad and popular throughout the Caribbean. The drums have been traditionally built from 55 gallon oil barrels. They are hammered into shape and chrome plated. I have been building drums and silver plated several with ok results.
chrome lead side shot
spiderweb lead with hibiscus
chrome lead close-up
My problem is that the hammering leaves the steel (very low carbon) with a grainy, porous surface. I sand and polish the steel (starting with a 120 grit flap wheel on a 5000 rpm grinder) to a mirror finish, except for the pits and some scratches that I may have (oops!) put in the steel during sanding. I want to do this in my shop as I'd like to keep the drum tuned before it is final plated, minimizing the retuning effort, as it takes about 24 hours to fully tune a new drum, and about 8 hours to retune a drum after it has been to a chrome shop.
My questions are: Can I copper plate the steel in my shop, then sand/polish the copper to a mirror finish? I've read that the steel should have a strike coat of nickel first - is this necessary? I need excellent adhesion to the steel as the drums must be periodically retuned by striking them with hammers, flexing the steel - the hammers are coated with duct tape to prevent surface scratches. I've seen brush plating systems that seem economical - $500 or less - will these work - can I also possibly plate silver and polish this to a mirror finish?
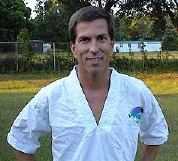
Keith Kropf
steel pans - Gulf Breeze, Florida, USA
I love both the looks and the sound of these! You could copper plate them, Keith. Unfortunately, this would need to be cyanide copper (very toxic and dangerous) because acid copper does not have adhesion on steel. Copper is relatively easy to buff, and well suited to closing up the kind of porosity you describe.
A way to do it without cyanide would be to first nickel plate, then acid copper plate the nickel, and buff the copper; then plate another layer of nickel in preparation for the chrome. A final possibility is to plate it with a heavy layer of nickel, which would 'self level' for brightness and not require buffing -- which is how most truck bumpers are plated today.
Decorative brush plating of large items is possible, but it is rather like excavating a foundation for a house with a teaspoon.
Good luck.
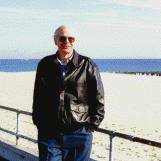
Ted Mooney, P.E.
Striving to live Aloha
finishing.com - Pine Beach, New Jersey
April 14, 2008
I was under the impression that the standard method for chroming was to first electroplate with copper, then nickel, then chrome. All electro. No nasty chemicals.
It's relatively simple to build an electroplating rig (my brother and I used to copper and silver-plate things at random in the bathroom with old AC to DC adaptors), and the resultant finish will be identical to whatever it is covering.
A home unit would just take longer (hours, maybe a day or two) than the 5 seconds it takes in a chrome shop (where they can ionize multiple pounds of metal per gallon into the dip tank)
- knoxville, Tennessee, USA
April 17, 2008
Thanks, Nathan. We have an Introduction to Chrome Plating on line here; you are correct that decorative chrome plating always includes nickel and chrome electroplating, and may start with copper electroplating.
But you are not correct about "no nasty chemicals". The copper electroplating would be a cyanide solution as previously mentioned. Cyanide is the fastest acting poison known, ingesting a few drops will kill instantly. And the chrome plating is done from concentrated (about 32 oz/gal) chromic acid (H2CrO4) -- this is toxic, carcinogenic, and highly regulated hexavalent chromium.
Regards,
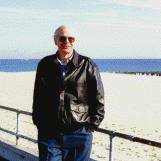
Ted Mooney, P.E.
Striving to live Aloha
finishing.com - Pine Beach, New Jersey
Q, A, or Comment on THIS thread -or- Start a NEW Thread