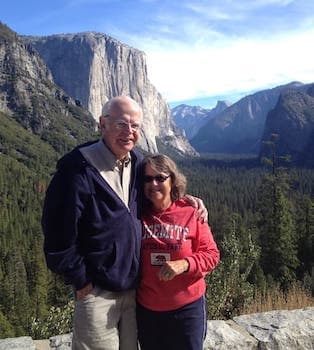
Curated with aloha by
Ted Mooney, P.E. RET
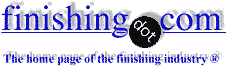
The authoritative public forum
for Metal Finishing 1989-2025
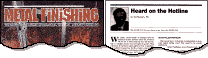
-----
Alodine 600 vs. Alodine 1200
Q. Dear Sirs,
What is difference between Alodine 600 and Alodine 1200 ... application? properties? Can Alodine 600 be used as alternate for Alodine 1200? Thanks for your attention.
Best regards,
Eri Rusli- Jakarta, Indonesia
2002
2002
A. Eri:
You sent me scampering back to the archives on this one. Some facts first:
Alodine 1200S~ Powdered Material
Spray Application
Used 6.3 lbs./100 Gallons
Temp: 70-100 degrees F.
Time: 15 Sec. to 1 minute.
Color: Light Iridescent gold to Tan, depending on aluminum alloy.
Alodine 600~ Powdered Material
Spray or Immersion Application
Used: 12.5 lbs./100 Gallons
Also: 9.9 lbs./100 Gals.(Toner 22)
Toner not used to meet Class 3 of AMSC5541.
Color: Light Iridescent Gold to Tan, depending on aluminum alloy.
The differences seen are that the #600 can be applied by an immersion dip, while the #1200 is applied by spray. A toner is used with the #600 and not with the 1200S I hope this helps.
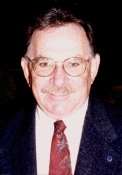

Ed Budman [dec]
- Pennsylvania
With deep sadness we advise that our good friend Ed passed away Nov. 24, 2018
A. Eri,
Mr Budman is correct in his answer about the concentrations of both chemicals. But both can be used in Spray or Immersion applications. The primary difference in the two chemicals is the issue of coating weight. The Alodine 1200 will produce a heavier film than the 600 will. The Aerospace industry uses the 600 chemical on areas that require electrical bonding.
Thanks I hope this helps.
Steve Adams- Cedar City, Utah
2002
Q. Hello,
I'm currently using Alodine 1200 for electrical bonding. According to Steve, Alodine 600 is better for this application -- but is the Alodine 600 resistant to corrosion? The equipment concerned is to be embedded in an aircraft and must resist salt spray.
Thanks
Véranith LYequipment manufacturer - Toulouse, FRANCE
2004
A. Hello,
The Alodine 600 resists corrosion. Alodine 1200, 1200S, 1201 shall be used where maximum corrosion protection is required for surfaces to be painted or left unpainted.
Alodine 600, 1000 shall be used for corrosion protection where low electrical resistance is required and the installation and assembly it must be accomplished within 24 hour limit.
Don't forget exposed electrically bonded assemblies or installations shall be sealed.
Jose Manuel- Sevilla, España
2005
Q. Hello,
Is there anybody who have paint adhesion problem on Alodine 1200S? Is this Alodine 1200S's nature, missed surface preparation before paint application or wrong inorganic treatment application?
Thanks for your help.
- Ankara, TURKIYE
2007
A. Yes, I have faced terrible paint adhesion issues when dealing with Alodine 1200S. Would you like to know more?
Shazli RANISME Aerospace Malaysia - Sg Buloh, Selangor MALAYSIA
March 31, 2008
Q. What is the difference between these two treatments. In which situation do we use Alodine 1200 instead of Alodine 1200S ?
ANDRE TORTOCHAUTproduct designer - FRANCE
July 24, 2008
A. Hi Andre. letter 3369 includes an explanation which should answer that immediate question. But remember that these are not dictionary words or generic terms; they are Henkel trade names -- so they mean whatever Henkel decides they mean, and that could change! Good luck.
Regards,
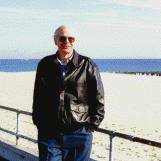
Ted Mooney, P.E.
Striving to live Aloha
finishing.com - Pine Beach, New Jersey
July 26, 2008
Q. Our customer engineering drawing calls out Alodine 600 per BAC5719 type 1 class D, while our facility only has Alodine 1200S of BAC5719 type 1 class A. So we are wondering whether we can substitute Alodine 600 type 1 class D with Alodine 1200S type 1 class A?
Marshall Zhangengineer in special process - Nanchang, China
July 20, 2011
![]() |
A. You absolutely cannot substitute one for the other. What you can "try" to do is to get your customer to give written permission or a waiver. - Navarre, Florida July 25, 2011 A. You cannot just substitute one product for another without first obtaining customer approval to do so. This is especially true for Aerospace applications where any change may have catastrophic effects on aircraft performance. Aerospace - Yeovil, Somerset, UK July 26, 2011 |
Q. Whether Alodine 600 reacts with interfaying sealant PR870 C12.
Kindly clarify.
- Bangalore, India
February 22, 2012
Hi Vadivel.
You can contact Henkel to see what they say. For a number of reasons readers are often hesitant to respond to abstract questions; so please explain the details of your situation. Thanks!
Regards,
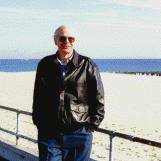
Ted Mooney, P.E.
Striving to live Aloha
finishing.com - Pine Beach, New Jersey
February 22, 2012
A. Hello folks!
Alodine 1200S can be replaced by 600 as far as I know.
Best Regards
- Chihuahua, Mexico
August 1, 2012
Q. Can anyone please post the required parameters of Alodine 1000 vs the Alodine 1200 as presented from the previous posts. Thank you.
Roger Palma- Clark Freeport Zone, Pampanga, Philippines
December 12, 2012
A. Hi Roger. Alodine is a tradename for Henkel products and they are free to change the formulation, the operating parameters, or anything else at any time. Thus, although it can be interesting to get general impressions from users, we should not rely on years-old postings for operating parameters! Please request a current technical data sheet from Henkel. Good luck.
Regards,
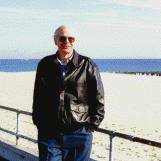
Ted Mooney, P.E.
Striving to live Aloha
finishing.com - Pine Beach, New Jersey
December 12, 2012
Thank you for the feedback Ted. Best Regards.
- Clark Freeport Zone Pampanga, Philippines
December 19, 2012
Which is more paint adhesive Alodine 600 or Alodine 1200S?
Q. Which is more paint adhesive Alodine 600 or Alodine 1200S?
basavaraj paerospace - India
June 26, 2015
A. All the other replies notwithstanding, I just got off the phone with Henkel Aerospace Technical Help as I had a drawing requirement of coating to the MIL-C-5541 spec with "Alodine 600 or equivalent". The chemistry difference between the two is that the 600 has some "complex cyanides" in it that the 1200/1200S doesn't - more environmentally unfriendly.
The 600 - in either Class 3 or 1A can be sprayed, dipped or brushed. The 1200 can be sprayed, dipped, or brushed in only Class 1 work - Class 3 work must be dipped.
From the standpoint of producing the corrosion protection or electrical conductivity properties, the products are "equivalent" if recommended process times are followed. The 600 takes longer to develop the desired properties than the 1200 does.
- Gardena, California, USA
April 13, 2017
Q. I would like to apply a yellow/gold conversion coating to various aluminum suspension and drive train components. Primary objectives are both corrosion resistance and appearance. The parts are cast and extruded components. Alodine 1200 is not really doing the trick based on my test pieces.
Is there a good and easy way to clean these parts that will properly prep them for acceptance of the conversion coating? And, second question, which conversion coating would provide the best appearance and corrosion resistance?
Boyd Engineering - Athens, Texas
November 28, 2018
A. Hi Robert. There are other vendors of chromating solutions, such as Chemetall, Macdermid, Sur-Tec, and a number of others, but we don't recommend brands or sources (why?). Rather, I'll note that all of these vendors offers good chromate conversion chemistry.
Another thing to note, though, is that the Alodine 600 and Alodine 1200 mentioned on these pages are hexavalent and not RoHS-compatible. You may want to contact Henkel or another vendor about a more eco-friendly trivalent chromate product.
When you say Alodine 1200 is not doing what you want, odds are strong that the problem is inadequate pretreatment or process control rather than Alodine 1200 being a marginally performing product :-)
If you are not with a metal finishing company, the easiest path to a satisfactory finish may be to farm out the work; very few OEMs do their own chromate conversion coating these days. But the process sequence is usually mechanical treatment followed by non-etch alkaline cleaning, followed by etching and de-smutting before chromating. Different alloys may require different pretreatments. We have dozens of threads here about chromate conversion coatings on aluminum, including some with photographs.
Regards,
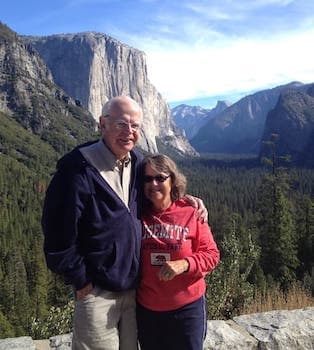
Ted Mooney, P.E. RET
Striving to live Aloha
finishing.com - Pine Beach, New Jersey
November 2018
Q. Ted, thank you for the quick reply. This is a home shop project. The parts are from a 2012 C6 Corvette. Never tried this before, so learning as I go. I agree that prep seems to be the key. However, the transmission and the integrated transaxle are castings and completely assembled. I do not know what alloy the castings are. I am not going to disassemble them. I am therefore somewhat limited to blasting the surfaces and then chemically prepping.
Would appreciate any advice on prepping the castings however, as I indicated I do not know the alloy. The drive shaft torque tube test piece I have is an extruded tube welded to a casting. I'll keep trying things on this test piece. If I can't get the appearance I want with conversion coating I'll have to paint everything.
- Athens, Texas
November 28, 2018
A. Hi again. If you're going to do it yourself, use a scrub brush ⇦ this on eBay or Amazon [affil links] with pumice ⇦ this on eBay or Amazon [affil links] and a little detergent for the cleaning (wear plastic/rubber gloves because a single finger print is a problem, then rinse and Alumiprep 33 ⇦ this on eBay or Amazon [affil links] , then rinse and Alodine ⇦ this on eBay or Amazon [affil links] , then rinse and dry (better to just drip dry in a hot dry room than overheat because above 140-160 °F can be a problem.)
Regards,
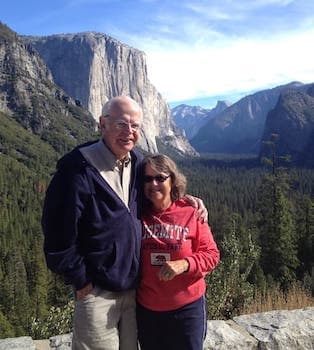
Ted Mooney, P.E. RET
Striving to live Aloha
finishing.com - Pine Beach, New Jersey
November 2018
A. Hello Robert,
There's some bad news and good news about your conversion coating project:
Bad news first. Conversion coating on castings is always going to be a bit more of a challenge due to inherent properties of castings -- the alloys will have more Si, which inhibits effective coating. That's not to say it isn't done; we do it here all the time -- it's just uglier as a finished product, and won't be as resistant to salt spray corrosion for as many hours as an extrusion type alloy coated under the same conditions. That being said, your Alumiprep step is critical in minimizing this effect. The results are likely to look different on a casting vs. an extrusion.
But the good news is that as a preparation for paint, chromate conversion coatings are fantastic! In fact, this is one of their more common applications -- and the castings we do here are almost all destined for the paint booth. Paint will adhere better, and a small scratch won't be nearly as likely to turn into a peeling mess in a few years.
So even if you don't like the look of your finished conversion coating, consider it time well spent :)
Good luck with your restoration, that's gonna be great!
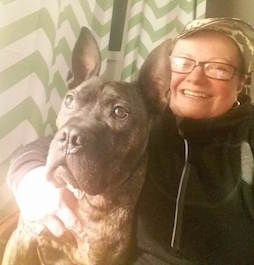
Rachel Mackintosh
lab rat - Greenfield, Vermont
November 29, 2018
November 2018
Excellent posting, Rachel.
Regards,
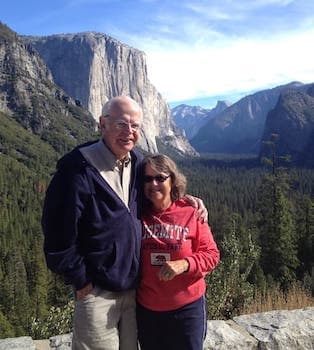
Ted Mooney, P.E. RET
Striving to live Aloha
finishing.com - Pine Beach, New Jersey
November 29, 2018
Q. Rachel, Thank you very much for the info. If I can get a reasonable yellow/gold appearance my plan is to clear coat the parts with a product called "Diamond Clear". It is a "direct to metal" application so should work well and assist in long term corrosion protection.
Next step on my test parts is to try good cleaning and prep per Ted's instructions and apply Alodine 1200. After that I am going to apply the Diamond Clear. I will post pictures if it works well.
Thank you again, Robert
Boyd Engineering - Athens, Texas
Q, A, or Comment on THIS thread -or- Start a NEW Thread