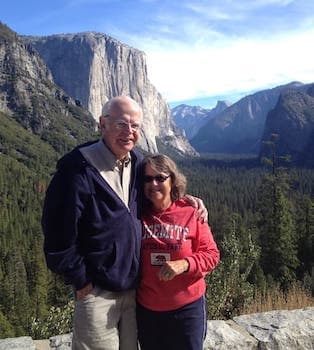
Curated with aloha by
Ted Mooney, P.E. RET
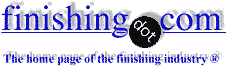
The authoritative public forum
for Metal Finishing 1989-2025
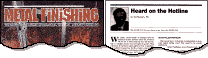
-----
Writer needs info for a piece on powder coating on hot dip galvanized fabrications
I'm a technical writer, doing an article for FABRICATOR Magazine, a NOMMA publication. I'm interested in talking with someone who has done powder coating on hot dip galvanized fabrications...the subject of a forthcoming piece. At the very least you'll get some free publicity from all the members of the Nat'l. Ornamental Misc. Metals Assn. Phone 262-790-2670, e-mail cera@execpc.com
John C [last name deleted for privacy by Editor](Freelance Writer) - Brookfield, Wisconsin
Ed. note: This RFQ is outdated, but technical replies are welcome, and readers are encouraged to post their own RFQs. But no public commercial suggestions please ( huh? why?).
I have done some powder coating on hot dipped galvanized parts. These parts were used for outdoor usage. The company that produced the raw dipped tubes actually had a proprietary type material that was applied to the surface as it was raised out of the process. This final proprietary topcoat was a clear material that was supposedly intended for increased protection of the bare product from the elements. My concern was that we ran the raw tubes through a 6 stage caustic washer and I was afraid this material would cause problems. I called the tube manufacturer and talked to two separate people, one person said they try and apply as much thickness of the material as they can and the other person told me they try to put the material on as paper thin as they can. The tube company would not tell me what the material was. MSDS only said proprietary. Testing showed that it was comparable to most pretreatment. I did have some problems with this material flaking a bit. It caused cosmetic defects on parts and the flaking was visible when closely viewed. I believe that when companies spent monies to purchase quality pretreatment systems, utilization of the pretreatment should be made to the actual surface of the substrate. Once these hidden proprietary coatings are applied, the pretreatment system is of second nature and the control process is taken away from the manufacturing facility. Just thought it might be interesting for some of the readers....
![]() Bob Utech Benson, Minnesota |
![]() Ed. note: Bob is the author of: "High Performance powder Coating" on eBay or AbeBooks or Amazon [affil links] |
Q, A, or Comment on THIS thread -or- Start a NEW Thread