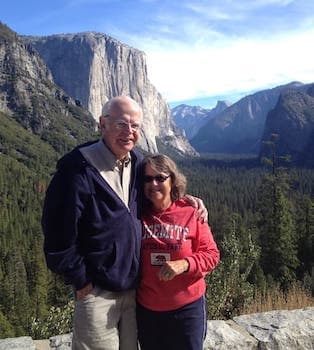
Curated with aloha by
Ted Mooney, P.E. RET
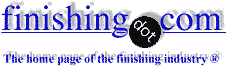
The authoritative public forum
for Metal Finishing 1989-2025
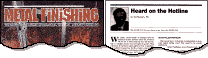
-----
Anodizing of titanium: Type II alkaline vs. Type I decorative?
Q. We want to anodize titanium using an alkaline anodizing bath. Who can give us the formulation of an alkaline anodizing bath? We want to get a gray coating.
Any advice would be appreciated.
J.H. PenningsTNO Institute of Industrial Technology - Netherlands
1998
A. See AMS 2488. The anodizing is performed in an alkaline solution of pH >= 13. Unlike anodizing of aluminum, the colour is not uniform and almost not controllable. Depending on the alloy (and solution?!), we are getting yellow to blue through grey appearance.
Max
captive metal finisher - Montreal, Québec, Canada
! With titanium in a bath of trisodium phosphate ⇦ this on eBay or Amazon [affil links] you get the most beautiful color of blue imaginable. All you need to do is to immerse the part, turn on the current and voilà, bright blue. Not gray but close?
Dave Fairbourn- Sandy, Utah
1998
A. A true grey from TSP (trisodium phosphate ⇦ this on eBay or Amazon [affil links] ) is not probable.
Brown, blue, silver, yellow, purple and green are possible at voltages up to 200. There are several different shades possible for each. Precise color requires precise voltage control. It anodizes nearly instantly. Surface prep makes a significant difference in the luster or look of the product. Does not need any further protection after anodize.
From 10% to 3% solutions are recommended.
James Watts- Navarre, Florida
1998
A. Thanks Dave and James! To minimize readers' confusion, though, we need to explain that there are two general types of titanium anodizing.
• The acid, neutral, or TSP anodizing that you are describing is a very thin and very colorful diffraction coloration for decorative jewelry and similar applications.
• The "alkaline anodizing" that Max speaks of is a heavy, wear-resistant, anti-galling surface for engineering applications.
My guess (but it's only a guess) is that J.H. Pennings is interested in the process that Max addressed.
Ted Mooney, P.E.
Striving to live Aloha
finishing.com - Pine Beach, New Jersey
Ed. note: Both processes are described in pretty good detail as the thread continues ...
Q. A magazine called Xtreme R/C Cars will publish an article on titanium anodizing in an upcoming issue. Sorry I don't know what month, but issue 4.9 I think.
I am interested in titanium & alum anodizing, and would like to obtain a red color. Any info is greatly appreciated.
David ThomasonGlendale, Arizona
1999
![]() |
A. Hi David. Anodizing of aluminum is an utterly different process bearing virtually no similarity to anodizing of titanium. In aluminum anodizing the color comes from the application of dyes; whereas in titanium anodizing no pigments or dyes of any sort are involved, as is discussed further on. |
A. The color red is not possible with titanium anodizing nor is black. Apparently neither exists in the spectrum created by the oxide layer formed on the surface. The color exists only as reflected light.
Dennis Rand- Plymouth, Massachusetts
A. Hi. Black is not possible from diffraction coloration, but somewhat red-ish or at least pink is possible on titanium -- some of these colors are low saturation pastels, not bright and vivid.
The anodized layer is actually translucent white, almost transparent, rather than any color. What happens is that when light hits the component, part of the light reflects off the top surface of the anodized coating, and some of it penetrates the coating and reflects off of the bottom surface of the coating and back through the coating again. The result is that the portion of light that travelled through the coating travels further and is out of sync and the two reflected waves "interfere", canceling out some of the colors from the white light, leaving these tones. Depending on what voltage was applied, the coating thickness varies, and thus the color. The term 'partial wavelength' is sometimes given to such coatings.
Regards,
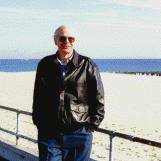
Ted Mooney, P.E.
Striving to live Aloha
finishing.com - Pine Beach, New Jersey
Q. I am anodizing a 6al-4v titanium medical device blue, yellow & green. These parts are subjected to 250 °F steam autoclaving for sterilization. Some of the parts after two cycles of autoclaving (40 min/cycle) are beginning to change to the next color. (yellow - magenta, blue-clear). This is only happening in a few parts but I need help into why it is happening and how to stop it. If anyone has suggestions I would appreciate the help.
Jim Johnson, Sr.Design Eng.- carlsbad, California
2000
adv.
We can produce and reproduce stable and controllable colors for titanium anodizing. Technology is ready for licensing.
You can see shades available on our web site. Black color can be obtained also, but this is a different technology.
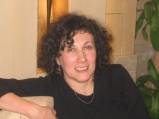
Anna Berkovich
Russamer Lab

Pittsburgh, Pennsylvania
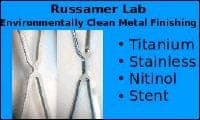
by Yoshiki Oshida
on AbeBooks
or Amazon
(affil links)
Q. Dear Sirs,
I am a manufacturer of Orthopedic Implants made of S.S. 316L and Ti-6AL-4V ELI. I am looking for Anodize per AMS 2488 Type I Colors (Pink, Gold and Green).
It will of great help to me if you can tell me the procedure for it.
Thank you.
- Delhi, India
2006
Q. I am new to the anodizing process and am having problems anodizing titanium green. The pieces are about 2 and a half inches long and are a half inch wide. When I anodize these pieces in other colors I have very little to no problems. I was wondering if this could be environmentally affected (humidity) or is this a normal problem for larger pieces.
Terry Donnalsonhobbyist - Lititz, Pennsylvania
2006
Ed. note: Green is apparently difficult. There is quite a bit of discussion of that further down the thread and on thread 7926, "Anodizing titanium to green color -- Q&A's". You may also wish to search the site for 'anodize titanium green'
Need exact composition of bath for AMS2488 Type 2 anodizing
Q. Alkaline Anodizing of Titanium Ti-6AL-4V. I am looking for the exact bath solution for what I have been told is a type II anodize per AMS 2488D.
I understand that it is >=13 pH and that the temperature is controlled to ±2 F and that voltage is the controlled characteristic, but WHAT is the chemical?
medical device industry - Huntington, Indiana
2007
A. Hi, Vicki. I know this sounds rather strange but ...
... even though the alkaline anodizing process is covered by that AMS spec, some of the details for successful alkaline anodizing are proprietary trade secret.
You have to either:
• send the parts to a shop which knows how to do it. Tiodize is the best known but there are several others,
• retain a consultant who will give the information to you, or
• figure out these details for yourself
Unfortunately, even though the process is loosely described in the AMS spec, you will not find the required details in published literature nor in public forums. Sorry, but there it is :-)
Regards,
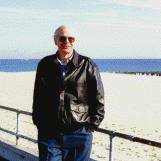
Ted Mooney, P.E.
Striving to live Aloha
finishing.com - Pine Beach, New Jersey
Q. Dear sir,
I try to anodize titanium size 1" x 4" to pink and green color by use TSP and borax
⇦ this on
eBay
or
Amazon [affil links]
but the color is not pure, for pink color will have light blue and green color will have yellow. And it is not shiny like gold, purple or blue that I do by the same method. What solution do I have to use for high voltage anodized and what method should I use?
Thank you and very best regards.
Thita M. ( from Thailand )
- Bangkok, Thailand
May 2, 2008
A. I see several comments pertaining to Grade II Titanium and obtaining green color.
Grade II in volume on racks can be vexing.
A common defect is a failure to obtain even color.
Color can have a 'Ghosty" appearance when viewed inclined and under a bright light.
A coupon was anodized, resulting in an uneven green color. When measured, the oxide thickness is uniform over the coupon.
Theories are, a change while anodizing of the um/Volt applied, and/or the um/second.
According to theory, these changes result in an anodized layer of mixed Titanium Oxide of TiO2, TIO3----X
Another theory is a change in cubic structure; i.e., anatase to rutile.
I call it "The Grade II Blues".
- Minneapolis, Minnesota
April 27, 2012
Q. We can do titanium anodising Green, Blue, Purple, silver, etc.
But yellow and black is nitride treatment, not anodising.
We need help of anodising red for titanium, as we now have pink color, but not red.
titanium - Ningbo, China
December 7, 2008
A. Hello Fun. If you understand where the color comes from, as described above, you understand why pink is relatively easy and a bright red does not seem possible. However, James Watts suggests that surface preparation is very important; and it seems to me that if the surface is very highly polished and thus highly reflective before anodizing, you should get somewhat more vivid colors.
Regards,
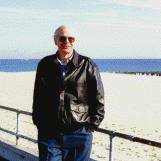
Ted Mooney, P.E.
Striving to live Aloha
finishing.com - Pine Beach, New Jersey
Q. Hi,
I wonder if someone could instruct me as to what solution is best to achieve an anodized silver finish on 6AL-4AV grade 5 titanium.
I would also appreciate information on setup and procedure i.e. precleaning procedure, anode/cathode ratio, suitable materials for cathode and jigs. I also need information on voltage/time and amps.
I would be very appreciate if anyone could provide this kind of information.
- Birmingham, west midlands, United Kingdom
Q. We are doing golden, blue, pink, green, and yellow -- but how to do black colour?
manoj pavasiya- Bombay, India
February 12, 2009
August 17, 2009
Q. I am doing Ti-6AL-4V type II anodizing, but a few days ago during the process, the parts got a pink color and then the type II anodizing process stops in the parts but not in the titanium racks.
Tatiana Riosmedical instruments - Medellin, Colombia
May 31, 2012
A. Type II titanium anodizing will have uniform gray color. Some companies produce anodized parts covered by "fur" that requires additional removal step.
adv. We produce hard anti-galling coating clean and ready for use. There is a possibility to grow the coating very thick for application where dielectic surface is required.
The color anodizing is always thin, and can serve mostly for color coding. The uniformity and consistency of color anodizing depends only on initial surface activation. This step can be conducted either electroless or under electrical current in a separate tank. Both methods are fine. As soon as the titanium surface is ready, it does not matter what anodizing solution you select for the final coloring. It can be oxalic acid or sodium wolframat or similar solutions available from the vendors. Be sure to final rinse the colored parts in diluted alkali solution, in order to prevent colors fading.
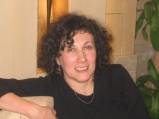
Anna Berkovich
Russamer Lab

Pittsburgh, Pennsylvania
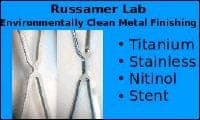
Why can't I achieve reliable green titanium anodizing?
Q. I am currently using sulfuric acid and sodium tungstate as my solution in my anodize tank. I get green sporadically. Need help on getting it all the time. My rectifier is 0-100 volts. I was getting it at 86.5 volts but now I am all the way up into the 90 volt range and I keep losing green. Need help.
Penni Higgens- Perkiomenville, Pennsylvania, USA
September 17, 2014
A. Hi Penni. Jon Quirt has specifically discussed your particular problem of consistent green anodizing above and, although he doesn't offer an exact answer, he does offer food for thought.
Also, please see letter 7926, "Anodizing titanium to green color -- Q&A's". Good luck.
Regards,
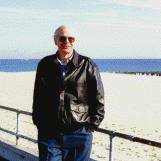
Ted Mooney, P.E.
Striving to live Aloha
finishing.com - Pine Beach, New Jersey
Can't obtain light grey in titanium anodizing
Q. Hi, we are doing anodizing on medical device implants, and we do type II, and achieve all the colors except Light Gray titanium-like colour Kindly help us for this.
We are doing thicker hard gray colour already.
Awaiting your prompt reply,
Regards
- Ahmedabad India
October 3, 2014
Hi cousin Raju. Penni is standing in line immediately in front of you, also hoping for a prompt reply to a problem that you say you've already solved :-)
While we await an expert who can help you, can you please offer her some tips? Thanks!
Regards,
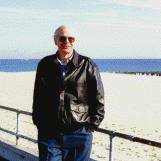
Ted Mooney, P.E.
Striving to live Aloha
finishing.com - Pine Beach, New Jersey
October 2014
A. Grey type II anodizing for color or for hard surface quality -- these are completely two different processes.
Grey color can be obtained in sulfuric acid. This process is easy and fast. Customers for disposable medical parts are quite happy with such anodizing.
Grey hard titanium anodizing 2488 type II is more complicated, requires proprietary conditions. Some companies advertise their equipment and chemicals for hard titanium anodizing. However in reality they hardly produce reliable and repeatable coating on more than one titanium part.
Concerning green coloring - anodizing green goes on high voltage (starting 70V). In order to reach this voltage without gassing, titanium surface must be free of iron (from cutting tools), and must be heavy saturated by fluorides. Saturation can be conducted either by electroless method, or under electrical current is special proprietary solutions. Some titanium alloys are not prepared well for coloring by standard electroless methods, and require careful preparation in electrolytic bath. Such bath does both -- removes remaining iron, and loads titanium with fluorides.
adv. Contact us for more information.
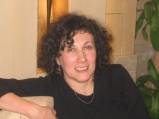
Anna Berkovich
Russamer Lab

Pittsburgh, Pennsylvania
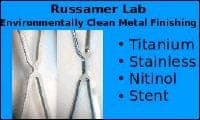
![]() |
A. Hola, la mayoria de los anodizadores de titanio utilizan soluciones acidas, pero nosotros estamos utilizando soluciones alcalinas, el color del anodizado es mas firme pero esta desfasado con cerca de d0s volts, por ejemplo para el azul con acido es de 18 volts, mientras que con solucion alcalina es de 20 volts, con soluciones alcalinas es mas lento el anodizado y lo puedes controlar mejor. victor solis neri- guadalajara, jalisco, mexico September 29, 2014 ---- |
A. Type I anodizing is color spectrum processing on titanium.
Type II anodizing is the hard coat process on titanium.
Implant alloys are mainly Ti6Al4V material specifications. The process is listed under AMS 2488 I believe.
Type II Ti hard coat processing is very much proprietary in both process and chemistry parameters. Takes a bit of patience and research but it can easily enough be figured out. I put together two different bath chemistries that produce high production numbers of high quality product. I can process many pieces at the same time with no shade variance in the grey coating. Most OEM's are looking for a lustrous dark grey in the final finish.
If you anodize then you already know that green is the hardest spectrum to maintain repeatability on. Different chemistries produce different colors at different voltages. My green spectrum hits between 92 and 95 volts before I go into pinks. Hot pink as well. Blue ghosting or spots I think is the biggest issues with the greens. Teals are within a very small voltage parameter and have nothing to do with the blue problem in green. Oxide growth is uniform so surface roughness can play a factor in higher voltage colors. Shorter etch times can leave the surface too smooth to achieve the perceived green color over the entire substrate. Too rough of a substrate can cause interference in light refraction because the peaks and valleys are too far apart for an even refraction. The oxides created are still uniform in thickness which creates highs and lows in the oxide finish causing the interference or crossing of rays that may appear as spotting or ghosting. Maintaining close tolerances in chemistry and voltage parameters is very important in achieving green repeatability. I run several shades of every color to include green. Organic and inorganic oxide removal before the color tank is a major player in high voltage green. Most cleaners will not remove the organic contaminant of the oxide formed due to heat created in the milling processes of the part. I process implant geometries so etch removal of the contaminants can cause undersized critical dimensions. My etch rates are slower so pre-cleaners and deoxidizers are a must before etching even begins.
I believe the grey color you are looking for in type I Ti color anodizing is called 'grey green'. I run that color quite often. In my chemistries, it's found between silver and sea foam. Cold baths create better colors!
Medical device surface finishing - Memphis, Tennessee, USA
Titanium anodizing difference between Type I, Type II, Type III
Q. What is the difference between Titanium anodizing Type I, Type II and Type III?
And where can I find some data of the refractive and absorbance index of TiAl6V4 and of TiO2?
I want also to ask what are the most common electrolytes for color anodizing?
Armin HuberStudent - Bruneck, Italy
February 25, 2016
Q. Hi.
I use trisodium phosphate
⇦ this on
eBay
or
Amazon [affil links]
for titanium anodizing; but when I want to achieve green my solution starts to hydrolyze. why?
- kish island/iran
January 25, 2018
Q. Hello I am working on improving output of a Type II titanium anodization process, which is quite difficult seeing as how Type II information is very difficult to find.
The situation I am encountering is Type III anodization spots appearing along the Type II of the parts (screws in my case.)
They are clearly 'blue' and usually show up in the head of the screw.
Any ideas as to what might cause this? The occurrence is seemingly random on any screw in any spot of the racking (occurrence is not biased towards a position.)
- Monroe, Washington
November 2, 2021
... I would also like to mention this issue appears to be more likely dependent on the *size* of the screws (larger screws don't seem to have this problem occur as often.)
My operator likes to describe it as "there's not enough mass to the screw" for the anodization process to occur, but I'm not sure what the basis is for this. At first I thought it might be air bubbles or something like that occurring in the bath, but even so, the bath is constantly agitated and bubbles that form should pop quickly.
Another thought is that when the Type III anodization oxide film forms, that prevents additional Type II anodization oxide film to form in the same area. When the voltage is set to ~15-25V, that's when the Type III 'blue' shade occurs, but the rectifier's current/voltage should be ramping up beyond that quickly.
- Monroe, Washington
... There appear to be two different modes of failure.
One in which the blue spots appear in random spots along the edges of the features. Another mode of failure is where the blue tint covers the entire face of the part (see picture).
The blue appearing along the feature of the edges gives some support to my operator's thought that there's not enough surface area/mass for that section to get properly Type II anodized and ends up being Type III anodized. Talking to a QE, he believes it's because the surface tension in these areas is higher and preventing solution from reaching it. He proposed more agitation or a mid-cycle agitation, but a manual mid-cycle agitation is not realistic considering how high current/voltage ramps can be for Type II. Another thought was that as the type II layer is being built up, there's more resistance forming at the contact points, preventing the part from building the complete Type II layer on the head of the part - (why the head, I'm not sure.) Perhaps for the spottiness, it's a lack of proper cleaning in those areas, but I'm not sure.
Because the problem is seemingly random, it's difficult to troubleshoot as well. It's independent of the size of the order, supposedly dependent on the size of the individual part, but I don't have anywhere near enough parts to do lots of testing. More thoughts to come soon.
Lawrence Lau [returning]- Monroe, Washington
A. Lawrence --
regarding why it happens in the head: it is likely due to the intricate nature of the features there. Also, you said it happens more on smaller parts, which could support this hypothesis. From that vantage point, it is probably a cleaning, bubble surface tension or parts orientation situation.
I have not experienced this exact issue yet but here are some ideas that might bring you closer to finding the issue:
Do the parts pass a water break test prior to anodizing? Check your cleaning process, maybe you are not removing all substances from manufacturing left in the screw head.
How are the parts oriented during the process? Does this orientation allow any bubbles that might form to break off and float to the surface? If you can see into the tank during or after processing: can you see bubbles that adhere to the parts?
Depending on the type of your agitation and how much it may jiggle smaller parts, it could be the part's contact areas are only intermittently in contact with your fixture or the contact areas are getting anodized, increasing electrical resistance. Although, this would only explain parts with a low layer thickness but would not explain the patchiness so I wouldn't expect this to be a real problem.
In any case, our operators do a mid-cycle agitation to free any bubbles formed after approx. half the anodization time, but we do colored oxide layers with a low voltage so the risk is much smaller, as you stated earlier.
I do not know of a commercial solution for a mid-cycle hammer whack or similar to break away formed bubbles, but maybe someone else here can point you in the right direction.
Keep us updated!
Eric
Manufacturing Engineer - Hildesheim, Germany
A. Lawrence,
adv.
If you are interested in investing some money into upgrading the type II anodizing for titanium, you will have a reliable and fool-proof process for any size and shape.
Different alloys, different colors
Anodized 3-D printed titanium rings
These parts can pass AMS 2488 test on durability. You will definitely save money and time in a long run, skipping the frustration of anodizing process going wrong. Bonus: the anodized parts do not require additional "fur" removal step. Contact me for details.
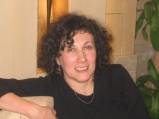
Anna Berkovich
Russamer Lab

Pittsburgh, Pennsylvania
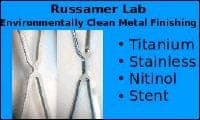
Thank you for the detailed response Eric.
It's interesting that this issue does not seem to occur during Type III anodization but does for Type II. I would think that given the similarities between the development of the oxide films that similar issues would also occur...
I like the idea of a water break test, but I'm not sure how that would be performed on these parts, given how small they are. I do not think I would be able to test water break on the head or on the thread of the screws. I am currently updating the cleaning process, so perhaps that will yield results when it comes to the blue in the head issue. If that does, I'll be sure to update the thread.
The parts are oriented in a rack (seen partially in my first picture in my first post) and the parts are dropped in to the bath perpendicular to the surface of the bath. The wire mesh should not allow for any bubbles when passing through the water bath. The bath has near constant water flow and agitation, so bubbles may form but leave quickly. I cannot see into the tank during processing and there is a safety switch (so that if the tank is opened, the process will stop). Perhaps I will try varying degrees of agitation.
Right now, I will hope that the updated cleaning processes clears up any anodization issues I see.
- Monroe, Washington
RFQ: I want to invest in a Type 2 anodizing plant but don't know how much to invest?
Jianjiao chenspring, TEXAS
May 5, 2022
privately respond to this RFQ
Ed. note: As always, gentle readers: technical replies in public and commercial replies in private please (huh? why?)
Hi Chen,
adv.
Please contact me directly. We license the know-how of the 2488 proprietary titanium type II anodizing process. Also upon request we provide the know-how of black titanium technology.
Both technologies require off-shelf equipment and cheap chemicals.
Our metal finishing technological processes successfully work all over the world. References upon request.
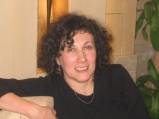
Anna Berkovich
Russamer Lab

Pittsburgh, Pennsylvania
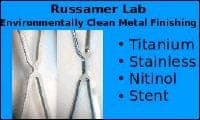
Q. Hello friends,
I would like to know the Titanium grade/alloy to be used for titanium anodizing, as we are using HF and HNO3 as etching solution, and as per my understanding HF will etch Titanium material.
Any good suggestion in this regard is most appreciated.
Thank you
Manager - Karnataka, India
March 20, 2023
A. Hi.
Many different grades/alloys, maybe all, including CP (chemically pure), can be anodized. Apologies but your question is abstract and requires a lot of guessing, so it's hard to proceed.
What type of anodizing are you doing and why? Decorating earrings, making watch dials, building wear-resistant machine parts, medical implants? Am I correctly guessing that you are currently unsuccessful in reliably etching it? Maybe some parts are etching properly and others aren't but you don't know what grade/alloy they are, and you're guessing that the problem is that they are different grades?
Please try your best to forthrightly describe exactly what you are trying to do and in what way it isn't working. If you would rather not do that for proprietary reasons, you can view topic 50566, "Titanium chemistry in HF and HNO3 chemical milling" which attempts to explain what goes on chemically in Nitric-HF etching of titanium; it may be helpful to you in sorting out whatever problem you are having. Thanks!
Luck & Regards,
Ted Mooney, P.E. RET
Striving to live Aloha
finishing.com - Pine Beach, New Jersey
Q. Dear Ted
Thank you for prompt and detail response,
Yes more details are required to address this,
Apart from this could you suggest the Racking material to be used for Titanium anodizing(Ti-6Al-4V) in sulfuric acid bath, and HF and HNO3 as etchant solution.
Thank you
Manager - Karnataka, India
March 23, 2023
Q, A, or Comment on THIS thread -or- Start a NEW Thread