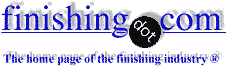
-----
Electropolishing and/or bright dip for aluminum
Q. We are looking for a bright dip and/or electropolishing solution which might be used for small aluminum parts. Any help or advice will be greatly appreciated.
Wilbert E. Medinaelectroplating shop - Antilles
1998
Ed. note: This RFQ is outdated, but technical replies are welcome, and readers are encouraged to post their own RFQs. But no public commercial suggestions please ( huh? why?).
A. If you cannot get a proprietary solution from our Chemicals directory, you might try a copy of The Canning Handbook [on eBay, Amazon, AbeBooks affil links]. A "Brytal" process for high purity aluminum, using sodium carbonate and trisodium phosphate ⇦ on eBay or Amazon [affil links] , is used with the parts made anodic. Phosphates may be a problem for your wastewater discharge permit. Other electropolishing solutions for aluminum are phosphoric acid, proprietary based.
For bright dipping, phosphoric acid/Nitric acid based solutions have been used. These solutions generate copious volumes of corrosive gases during the bright dip operation, then might need a desmut in nitric acid.
These processes can create a lot of waste solution. Langford and Parker in Analysis of Electroplating and Related Solutions [on Amazon, ... on AbeBooks affil links] show how to analyze the bright dips. I wonder if some of our readers can offer experience in recovery/regeneration of acids.
I used an electropolishing solution for stainless steel only once, it was a nonproprietary acid mix; it absorbed moisture from the air, which made the solution grow in volume, after which it etched the parts. It really was the wrong way to go. Most of the time, we would waste effort in the electropolishing tank, then liquid hone the parts afterwards with glass beads.


Tom Pullizzi
Falls Township, Pennsylvania
1997
Brytal Process
Q. Please give me more details about the Brytal process for Aluminium brightening.
Deepak Ratan- India
1999
A. Hi Deepak. Brytal® was a registered trademark of British Aluminum Ltd. Sorry, I wouldn't know if the trademark is claimed by anyone; I don't follow the chicanery of corporate trading closely enough -- heck, I'm still trying to find my promised American Can Company pension, which is probably currently being spent on after-dinner cigars by some corporate muckety-muck in Greenwich :-)
The Brytal process is for 99.8 percent super purity aluminum, and the basics are to make the work anodic at 45 to 90 ASF in a 185-195 °F solution of sodium carbonate and trisodium phosphate ⇦ on eBay or Amazon [affil links] . The parts must be subsequently desmutted -- please try to get your hands on the Canning Handbook that Tom references. Good luck.
Regards,
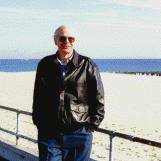
Ted Mooney, P.E.
Striving to live Aloha
finishing.com - Pine Beach, New Jersey
November 2013
Aluminum Brite-Dipping is a Nasty Process
1998Sir,
We are a fellow anodizer, and we do bright dipping.
Unless you have a lot of work for it, I do NOT recommend setting it up in your plant. The fumes are horrible and they corrode everything around it.
David A. Kraft- Long Island City, New York
A. Aluminum is commercially brightened in a solution of phosphoric and nitric acids or phosphoric/sulfuric/nitric acids. The extraction of the gases produced is a part of the process and hundreds of companies do this on a daily basis. The nitric acid evolved must be collected and many air discharge permits require scrubbing of the air stream to remove the NOx especially NO2.
Lee BranchRichmond, Virginia
1998
1997
I must side with David on this one, Lee. By any measure, bright dipping of aluminum is nasty business. If Wilbert needs to bright dip aluminum, by all means he can do it! But please don't think in terms of a solution that an anodizing shop plops into an available pre-dip tank -- spend some time at bright dipping facilities to understand what a bright dipping system implies before committing and getting in over your head.
Bright dipping requires a ventilation system that is very different than the kind that most anodizers and platers envision (fully enclosed garage, not lip exhaust). It involves fume scrubbers which must be far more effective than those that most anodizers are familiar with because highly soluble NOx fumes rather than simple acids and alkalis must be removed. It requires material handling equipment suitable for operation in a heavy NOx environment (how will you repair it if it breaks down inside that NOxious garage). It demands secondary containment in an immediate and compelling way -- double walled 316L stainless steel tanks -- that most plating and anodizing shops are not familiar with.
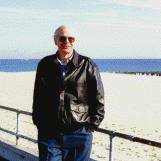
Ted Mooney, P.E.
Striving to live Aloha
finishing.com - Pine Beach, New Jersey
A. I would recommend Electropolishing as an alternative to the brite dip. We have perfected the electropolishing of Aluminum and have offered this service to our customers. The results are better and regulatory requirements are minimal. We have no air quality issue from our proprietary process solutions.
Dave MortensonFreemont, California
1998
Thanks Dave. Can you recommend any books or journal articles or provide any data for Wilbert which might explain how electropolishing of aluminum is done?
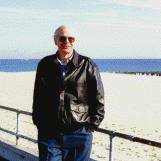
Ted Mooney, P.E.
Striving to live Aloha
finishing.com - Pine Beach, New Jersey
1998
A. Mr. Medina:
adv.
Our company is a vendor of electropolishing chemicals, and we offer baths for handling most wrought aluminum alloys. We also furnish equipment and technical expertise to support the chemical products. We are listed in the suppliers directory on this web site, but we can also be reached at our own web site, which is linked to from there.
Regards,
Ed BayhaMetal Coating Process Corporation - Charlotte, North Carolina
RFQ: I need to purchase some nitric acid-based solutions for cleaning/polishing of aluminum. Could someone please point me in the right direction?
Sarah C [last name deleted for privacy by Editor]- Redford, Michigan
December 21, 1998
Ed. note: This RFQ is outdated, but technical replies are welcome, and readers are encouraged to post their own RFQs. But no public commercial suggestions please ( huh? why?).
Q. I had decided to start my own electropolishing plant for that I need the whole information from you, such as how much space will be required for a plant, what chemicals are used, their proportion, what to add to clean the chemicals.
The total details is what I want.
Raju Suryawanshi- India
2000
A. Hi, Raju. Your best bet may be to get hold of a good book on electropolishing, such as the Electroplating Engineering Handbook ⇦ this on eBay, AbeBooks, or Amazon [affil links] , or sign up for an electropolishing course such as are offered by Metal Coating Process Corporation, or make contact with a consultant on the process. Readers of this forum will generally put in a few minutes to try to answer questions that can be addressed in that time frame, but "total details" is a very tall order for a public forum :-)
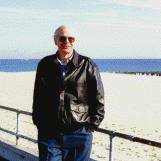
Ted Mooney, P.E.
Striving to live Aloha
finishing.com - Pine Beach, New Jersey
2000
Q. Dear Sir,
Greetings. I am doing electro brightening process on aluminium in a solution of sulfuric and phosphoric at a temperature of 65 °C. While dragging out the hollow pipe from the electrolyte oxidation happens or some etching happens on the surface.
I have read a lot that its a really difficult process to monitor but still I have gone for it. Doing so I am finding myself in big trouble.
Please guide me that how can I avoid the oxidation or etching that is happening on the section. Thanks a Lot. Waiting for your beautiful replies. I trust this site very much.
Regards,
- Pune, Maharashtra, India
January 17, 2013
Ed. note: This RFQ is outdated, but technical replies are welcome, and readers are encouraged to post their own RFQs. But no public commercial suggestions please ( huh? why?).
January 21, 2013
Q. Dear Mr. Ted,
I gone through the above replies and got a little idea about it. Frankly speaking I had read those before posting my query also. I generally first use search engine of your website and then only shoot my question.
Actually there are 2 types of chemical polishing.
1) Bright dip
2) Electro brightening.
In first scenario Nitric acid is been used along with phosphoric and sulfuric and the job is treated at 97 °C. This process fumes out hazardous Nitric oxide, for which we need a good non-conventional scrubber to arrest it.
In second case only sulfuric and phosphoric are been used at a temperature of say 70 degrees and current applied may be 10 amps per sq feet. This does not involve those harsh fumes as earlier cited in case 1.
The biggest challenge I am facing is oxidation or etching of Job while dragging out during electro brite process. I heard some proprietary solution which arrests such problems but economically they are not viable and I also doubt them.
Is there any other alternative to solve this difficult problem.
Regards
- Pune, Maharashtra, India
January 24, 2013
A. Hi. I agree with your analysis about the undesirability of chemical brightening if it is possible to avoid it. I've been involved with engineering of 3 or 4 aluminum bright dip facilities over my career, and I hated them all :-)
I am away from my office and my books for a while, but my recollection is that ASM Metals Handbook Vol. 5.
has an excellent chapter on the topic of chemical polishing and electropolishing of aluminum. If you can get access to it, it may have insights that lead you towards solving this problem. I can't necessarily share your opinion that proprietaries are unaffordable, because we must ask "compared to what?", and the alternative is often unviable.
Regards,
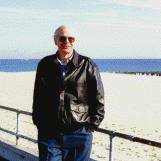
Ted Mooney, P.E.
Striving to live Aloha
finishing.com - Pine Beach, New Jersey
Q. Dear Mr. Ted,
Thanks a lot for your answer. Was little late in replying; sorry for that. Will check whether can I get access to that handbook and will also love reading it.
I wanted to ask one more thing, does mild caustic etch after brightening solve the oxidation problem. I have not tried at my end but will give it a try.
Once again thanks a lot for replies.
Regards.
- Pune Maharashtra India
February 9, 2013
A. Hi again. Sorry, I have personally seen electro-brightening of aluminum only once in the field, and tbriefly. I'm not aware of the possible sequences. We'll have to hope that a reader who is actually familiar with it will offer some advice.
Regards,
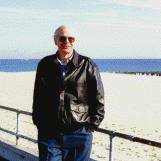
Ted Mooney, P.E.
Striving to live Aloha
finishing.com - Pine Beach, New Jersey
February 10, 2013
A. Hi,
I'll answer the question about mild caustic etching at the end of these notes.
The problem with electropolishing of aluminium in phosphoric/sulfuric acid is that the mixture is an etchant. During electropolishing an oxide films forms on the aluminium and prevents etching. The oxide film continuously forms and dissolves. If the current is too low or is stopped, the oxide is lost and etching commences. When the work is removed from the bath, the oxide will dissolve and unless the parts are rinsed quickly enough, etching begins.
What actions can be taken to avoid etching?
Years ago when environmental matters were of less concern, the answer would be to add chromic acid to inhibit chemical attack on the aluminium.
Now we must attempt to maintain the oxide layer during the transfer to the rinse. Some actions to try are:
1) Transfer the work as quickly as possible.
2) Lower the operating temperature of the bath to slow the rate of dissolution.
3) Produce a thicker oxide film by raising the anodizing voltage toward the end of the processing: to do so throughout the processing, would result in more heat generation and possible pitting.
4) Increase the proportion of phosphoric acid in the mix.
If you succeed in transferring the aluminium without etching, you may have some residual oxide film. This may give a "white bloom" especially after anodizing. To remove the bloom, the mild caustic etch is used after rinsing.
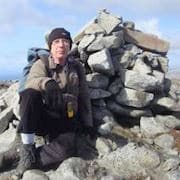
Harry Parkes
- Birmingham, UK
Q. Dear Mr. Harry,
Thanks a lot for your valuable reply. Sir I wanted to know one more
thing: will electro-brightening will give us more gloss or chemical
bright dip ? I mean which process will give us more gloss.
Thanking you in anticipation.
- Pune, Maharashtra, India
August 5, 2013
A. Hi Bhagyashree. Actually, Harry answered that one in letter 51410, "Electropolishing of Aluminum vs Bright-dip", and details can also be found in the ASM Metals Handbook volume previously referenced: electropolishing can give better gloss, but the difference is small except on very pure aluminum, and most of the difference is masked by the limited transparency of the anodized film anyway. To respond in practical terms: telescope mirrors are electropolished, but streetlight reflectors and hubcaps are usually chemically bright dipped. Good luck.
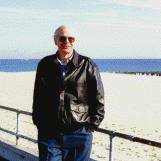
Ted Mooney, P.E.
Striving to live Aloha
finishing.com - Pine Beach, New Jersey
August 7, 2013
August 13, 2013
Dear Mr. Ted,
Thanks a lot for the guideline and it was very specific and practical answer.
Now my planning will be very much easier.
Regards
- Pune, Maharashtra, India
Q. I have an application where we are glass beading some aluminum camera parts with a #11 fine glass bead and then need to brighten the finish a bit prior to anodizing. I know that the old bright-dip finish is no longer considered environmentally friendly and has been largely done away with. Can anyone suggest a process that is currently an accepted mainstream practice for mild brightening of the matte finish after glass beading?
The glass beading is used to remove all traces of the toolpaths but leaves a matte finish. The customer wants the finish brightened a bit before anodizing.
Any suggestions would be greatly appreciated.
- Surrey BC Canada
November 6, 2013
adv.
Lyle,
Contact me for possible testing. We can suggest eco-friendly electropolishing method for aluminum reflectors or similar products.
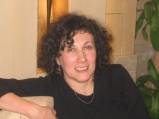
Anna Berkovich
Russamer Lab

Pittsburgh, Pennsylvania
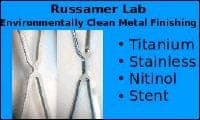
November 18, 2013
A. Dear Sir,
You can go for electro brightening process where nitric acid is not used at all. You have to just provide a DC current to the electrolyte of sulfur and phosphor. The operational temperature can be as low as 70-80 ° C. So no nitro oxide fumes.
The only problem is that you have to quickly put the job into rinsing water or else oxidation streaks appear on it.
Regards
- Ahmednagar, Maharashtra, India
November 20, 2013
Q. Dear sir,
Please let us know how many square feet of job can we do in 35 kgs of phosphoric acid since we are using a lot of chemical in bright dip.
Thank you,
- Bangalore Karnataka India
March 21, 2014
A. Hi,
There is no simple, single answer to your question. However, I'll try to offer some guidance. As you give no information on the make up of your brightener, I will have a guess at it's composition. Even If I guess wrongly it should not make too much difference.
The 35 kg phosphoric acid will make about 20 litres of brightener. The area of aluminium that can be treated in one litre usually falls within the range 15 to 30 square feet per litre. So, the value for 35 kg phos acid is 300 - 600 sq.ft.
The brightener usage is that removed by drag-out. The actual amount used will be determined by drainage back into the bath, how easily the work can be drained and rack area.
A most important point to consider as to whether your plant is being used efficiently is the aluminium content of your bath. As the aluminium concentration rises there will be a loss in brightness and eventually the finish will not be satisfactory. Ideally the drag-out and subsequent replacement with new brightener will hold the aluminium content just below the point where brightness becomes unsatisfactory. You must determine where that concentration lies for your work. So, if you have a low aluminium concentration, look to reducing drag-out. If the aluminium becomes too high, check if the processing time can be reduced while still retaining an adequate finish. Otherwise reducing drag-out is counter productive.
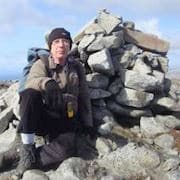
Harry Parkes
- Birmingham, UK
March 27, 2014
June 10, 2014
Q. I want to know if there is any relation between cathode and anode area, in the electropolishing bath. Is lead the ideal cathode?
João Baptista- Diadema, São Paulo, Brazil
Q, A, or Comment on THIS thread -or- Start a NEW Thread