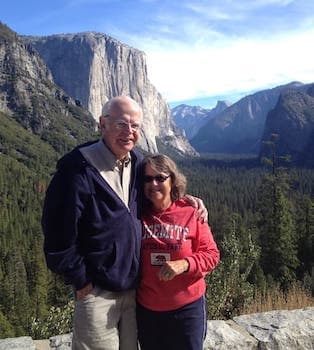
Curated with aloha by
Ted Mooney, P.E. RET
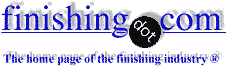
The authoritative public forum
for Metal Finishing 1989-2025
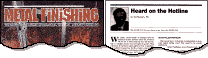
-----
Alkaline Cleaning
Q. Our finished plated hardware is put through a pre-clean prior to use. This pre-clean is a mild alkaline cleaner followed by a low pH surfactant. While the part is in the surfactant you can see the part start to tarnish. This will happen on EDNi, Chrome, or Silver. Has anyone had a problem with coatings tarnishing during pre-clean, and does anyone have a suggestion on how to eliminate the problem.
Garry Pickettaerospace - Los Angeles, California
1997
1997
? Gary:
Just what metal are these parts that are "pre-cleaned"? Is this done pre-plate? What is the purpose of the acidic solution? Is it to dry the parts, rinse them spot free, seal or rust prevent? Those answers may help me to help you.


Craig Burkart
- Naperville, Illinois
A. Gary, The process you are describing tends to let me think this is a preplate operation, however I think this is after plating. If so, why are you using the low pH surfactant? If this operation is to clean residual manufacturing soils I would suggest staying with the mild alkaline solution but go directly to a R/O or D.I. rinse. The make up of the water will have less of an acidic state than what you have now. Bob
![]() Bob Utech Benson, Minnesota |
![]() Ed. note: Bob is the author of: "High Performance powder Coating" on eBay or AbeBooks or Amazon [affil links] |
Q. Need recommendations for cleaning process/chemical (alkaline) for removing ash and heavy rust/scale after parts are cleaned thermally.
Steven e Morganengine systems/ - Latham, New York
1999
A. Hi Steven. Assuming that you are talking about steel parts, you'll probably want an alkaline electrocleaner operating at about 200 °F. The parts will probably be anodic.
Something that you may know, but other readers may not, is that people don't formulate their own alkaline cleaners today. Rather, they buy a proprietary from a plating process supplier for two reasons: firstly, so they get the benefit of the suppliers decades of development experience because cleaners are fairly complex, involving saponification, wetting and emulsification, deflocculation, chelation/sequestration, buffering, and inhibition. Second because the supplier will have a test lab to run samples; you don't want to design a cleaning line based only on theory, and want to build a line which employs chemistry that you have tested.
After the alkaline cleaning and rinsing, you will require an acid activation step. Often 25% (or so) HCl will serve, but again testing is required. Good luck.
Regards,
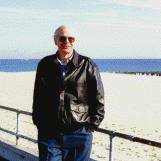
Ted Mooney, P.E.
Striving to live Aloha
finishing.com - Pine Beach, New Jersey
Cleaning oily parts for brush plating
Q. I have a main shaft from an old motorcycle that is worn a bit. I'd like to brush plate the worn spot with nickel to build it up a few thou. Being as how this has been in oil its entire life it might be tough to get it degreased. Someone on here mentioned a hot alkaline bath; what is meant by alkaline bath? I also read I might have to hit it with sulfuric acid. After that would I need to copper plate first, then nickel? Thanks in advance
dave smith- phoenix Arizona usa
September 16, 2016
A. Hi Dave. I'd scrub it with a tampico brush and pumice and a solution of hot water and dishwasher detergent. Then I'd dip it in 25% or so HCl. Then nickel plate it. Don't try to copper plate it.
Hopefully, before trying to plate a few thousandths of an inch of nickel on a shaft, you'll acquire some experience on scrap parts before trying this. Because, while its drop dead easy to use a brush plating kit to plate a little gold onto an automotive emblem that a plating shop has pre-plated with nickel, some people might not realize that it's quite another thing to nickel plate a dirty, raw steel main shaft. Good luck.
Regards,
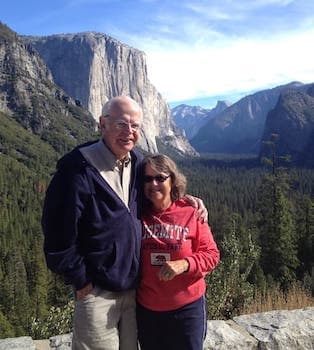
Ted Mooney, P.E. RET
Striving to live Aloha
finishing.com - Pine Beach, New Jersey
September 2016
Q. We used to clean some of our parts with CLEPO 88-A which is 45 - 55 % disodium metasiliate and 3-8 % sodium tetraborate, but it got discontinued. The manufacturer is replacing it with a product called New Dimensions Supreme which is made up from these constituents: inorganic filler, alkyl phenol, proprietary silicates and propanol.
Has anyone used this? If you used it, did it affect your wastewater treatment system? Please share your experience. Thank you.
- Sioux Falls, South Dakota
September 11, 2019
A. Hi Al. We can't post comments about specific brands & proprietary products (why?), but if anyone has experience with successful or unsuccessful wastewater treatment of these types of constituents they're encouraged to respond of course.
Regards,
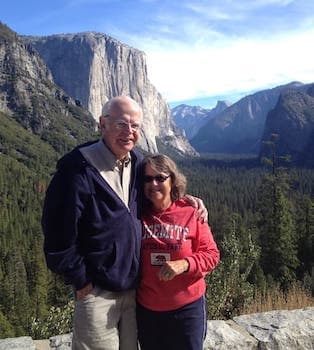
Ted Mooney, P.E. RET
Striving to live Aloha
finishing.com - Pine Beach, New Jersey
September 2019
A. Hi there Chris! I haven't personally used this but be aware you are going from an inorganic cleaner to one with organic solvents in it, and if the organics break through into your effluent, you could have compliance problems. This is also enough of a 'process change' that you will want to declare it to state/local water authorities and see what they require for additional testing once you bring it on line. In our area we would have to apply for a pretreatment license update and can't use organics because it would violate a VOC testing exemption we currently hold based on a fully inorganic process. Definitely research how this applies to you before committing to a specific cleaner. Good luck!
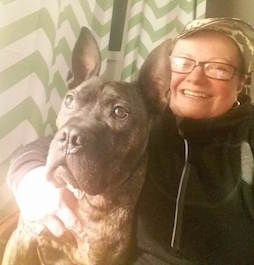
Rachel Mackintosh
lab rat - Greenfield, Vermont
September 13, 2019

Q, A, or Comment on THIS thread -or- Start a NEW Thread