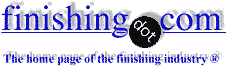
-----
Hydrogen Embrittlement in Plating
Quickstart:
Plating processes are not 100% "efficient"; rather, some portion of the applied electricity creates hydrogen gas and oxygen gas rather than depositing metal. This hydrogen can enter the component and cause embrittlement of some metals -- most commonly high strength steel.
In addition, anodic electrocleaning and acid pickling steps earlier in the electroplating process can cause the same problem. Those causes can be somewhat reduced by employing cathodic electrocleaning rather than anodic, and by using proper inhibitors in pickling baths.
The most common solution is to bake the parts for a reasonably long time, but within a rather short window before the damage is done, with those baking specs sometimes dependent on the particular steel. Some ultra high strength steels cannot safely be electroplated.
< Prev. page (You're on the last page of the thread)
Q. Once parts have been determined to have hydrogen embrittlement failure, is there a way to "save" the parts? I have heard several different theories from; the embrittlement can still be baked out, to re-strip and re-plate the parts, to the parts are junk. Is there a definitive answer out there?
Kevin Almquist- Danielson, Connecticut
1999
A. Once the material is found to have a H/E problem, the micro-structure has already sustained damage due to the "migration" of the trapped hydrogen (very small cracks). Re-working the parts will not correct the damage. This is only my opinion, but one based upon "ACTUAL" experiences related to H/E failures. My definitive answer would be "SCRAP" the affected product, try to define and correct the "ROOT CAUSE" and try again. This has been my experience.
David L. Dowfastening systems - Automotive - Detroit, Michigan
Multiple threads merged: please forgive chronology errors and repetition 🙂
What is the mechanism of hydrogen embrittlement?
Q. I am looking for any reference information about hydrogen embrittlement (mechanism).
nina [last name deleted for privacy by Editor]- Halifax, Canada
2000
Tip: This forum was established to build camaraderie among enthusiasts through sharing tips, opinions, pics & personality.
The curator & some readers who publicly share their info will be less likely to engage with those who don't.
by Jack Dini
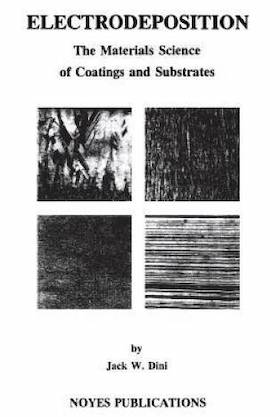
on eBay or Amazon
or AbeBooks
(affil link)
A. There are many good books on this subject that you can research for your project, Nina. If hydrogen embrittlement related to metal finishing is your issue, Jack Dini's "Electrodeposition - The Materials Science of Coating and Substrates" has a very interesting chapter on the mechanism.
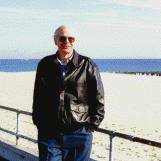
Ted Mooney, P.E.
Striving to live Aloha
finishing.com - Pine Beach, New Jersey
A. The basic situation is one little hydrogen atom lost inside the metal matrix (crystal), it takes up almost no room, can move easily through the crystal and causes very little stress to the crystal structure.
Then it meets another hydrogen atom, they're dead happy to meet each other and join to become one molecule of hydrogen gas. Gas takes up about 1000 times the volume, so the molecule puts a lot of localised stress on the crystal, a few more molecules in a few more places and then the trouble starts.
Ian Brookeuniversity - Glasgow, Scotland
Q. I am doing a failure analysis on galvanized quench and tempered steel (.22C/1.32 Mn). I have read where the acid bath can cause hydrogen embrittlement in high-strength steels. Is it common to see failure due to hydrogen embrittlement in quench and tempered steels (Yield strength = 116 ksi)?
David Reinhart- Longview, Texas
2000
Q. Hello-
What's a good test to establish whether or not the failure is due to Hydrogen Embrittlement (for fittings)?
Is a sustained load test for 72 hrs with 85% max. allowable load a good criterion?
Fittings are made from 8740 steel, Heat treat to 170-190 ksi and CAD plated per AMSQQP416 and subsequently baked for 23 hrs.
KA
A Kamal- New York, New York
2000
Q. Hello,
I am a student studying corrosion engr., I am presently studying hydrogen embrittlement, I like to know about the possible testing method of hydrogen embrittlement. If anybody can help me, I will really appreciate it. Thanks
B. Kannan- India.
2000
Q. I am interested in plating of metal parts and the hydrogen embrittlement that may occur and also the relief of stress in such parts by baking.
Specifically, I ask if the stress relief occurs without baking and by the mere passage of time and, if so, what time is normal or does the part remain capable of failure until baked?
If the metal parts plated are not stress relieved after plating, does the metal and/or the plating process present some danger of brittleness and/or failure?
Jim McBroom- Nashville, Tennessee
2000
A. Some of the above questions were separate threads which we've merged into this existing thread.
Hydrogen embrittlement under plating does not relieve itself ever, because the problem isn't the presence of hydrogen (which, yes, I suppose might dissipate over time), it's the damage that the hydrogen did to the metal. Baking must be done very shortly after the embrittling process, preferably immediately.
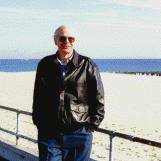
Ted Mooney, P.E.
Striving to live Aloha
finishing.com - Pine Beach, New Jersey
Q. I have conflicting reports from 2 test houses on analysis of screws with sheared heads. One opinion is hydrogen embrittlement and the other is high core hardness. Is there a definite diagnosis tool for hydrogen embrittlement.
James Wardle- Newcastle, UK
2001
Q. Is there hydrogen after chromating or before? When is hydrogen produced in a steel? Does the appearance of hydrogen depend on the chrome on the steel or depend on the proper steel (tensile strength?)
Alberto [last name deleted for privacy by Editor]- Rosario, Santa Fe, Argentina
2002
A. I think you mean chromium electroplating rather than 'chromating'
Hydrogen enters steel during casting, cleaning by most common acids (except nitric), cathodic electrocleaning, electroplating, heat treating in reducing atmospheres and some welding processes. It can be a serious problem in highly stressed, high strength steels. There are several embrittlement mechanisms, but basically, the hydrogen adds to internal stresses and accumulates at defects, leading to failure at even low loads. The hydrogen embrittlement danger increases with increasing hardness and decreasing part thickness for a given type and amount of plating.
Hydrogen build-up is especially high in hard chromium plating from Cr+6 solutions due to the low cathode efficiency (large amperage required). The amount of hydrogen liberated at the cathode (workpiece) surface is proportional to the plating thickness. Steel of ultimate tensile strength 150 ksi or greater having residual stresses from machining, grinding, hardening, etc., should be stress relieved or shot peened prior to plating. Steel having a tensile strength of at least 160 ksi or HRC 36 shall be given a hydrogen bake-out at 191 °C (375 °F) or higher for 3 or more hours as soon as possible after plating. See QQ-C-320B or AMSQQC320 CHROMIUM PLATING (ELECTRODEPOSITED), for more details.
- Goleta, California

Rest in peace, Ken. Thank you for your hard work which the finishing world, and we at finishing.com, continue to benefit from.
De-embrittlement process
Q. Please give advice on standard hydrogen de-embrittlement process. Please also advice on the material which have bypassed hydrogen de-embrittlement process. How can we correct it?
PRABHUNATH SinghHEAD FINISHING - Rohtak, Haryana, INDIA
2007
![]() |
A. Prabhunath, Aerospace - Yeovil, Somerset, UK A. Hydrogen de-embrittlement process is to let escape Nascent Hydrogen from the surface of substrate which gets preferentially co-deposited with the basic deposit sought. Process Manager - Ghaziabad, UP, India |
Q. I work in the fastener industry and this subject of hydrogen embrittlement comes up often with parts that are plated.
Over a period of time won't the hydrogen bleed out, or has the damage been done and the parts are scrap?
fasteners - Itasca, Illinois
2007
A. Hi, Richard. We appended your inquiry to a thread which answered it.
It's not the hydrogen that is the problem, it's the damage that the hydrogen has already done to the steel. Good luck.
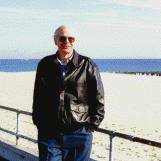
Ted Mooney, P.E.
Striving to live Aloha
finishing.com - Pine Beach, New Jersey
Q. Does zinc electroplating also affect the strength of the nuts? Surely a bolt would fail somewhere outside the nut and thread. This question purely because Electro Galvanized Zinc Blue nuts do look so much better than mechanical plating.
Chris Vermaakracing - Heidelberg, Gauteng, South Africa
February 25, 2010
A. Hi, Chris. Although failure of a nut sounds less likely than failure of a screw, I do not accept the implication that failure won't happen in the nut. Picture the screw being made of high strength steel and the nut being made of glass :-)
Electroplating has no effect on soft mild steel, but does cause hydrogen embrittlement of high strength steel. Baking immediately after plating may solve the problem, but it may not -- a statistically valid testing regimen is necessary in order to know for sure.
Regards,
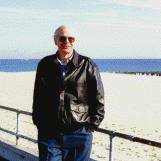
Ted Mooney, P.E.
Striving to live Aloha
finishing.com - Pine Beach, New Jersey
Q. Hi,
Any Standard or OEM Approved for the Paraffin test to conclude the Hydrogen de embrittlement test?
- Salem, Tamilnadu, India
June 15, 2011
Q. We clean parts in solvent with a pH value 10 to 11; it is definitely not acidic. But Army says it will cause high strength steel hydrogen embrittlement. I just do not understand. You?
David Ho- Milford, Connecticut, USA
November 6, 2013
A. Previous entries in this thread have alluded to the phenomenon which I will describe forthwith: In electroplating, the article being plated is cathodic; and at this cathode, metal is deposited. But there is also cathodic inefficiency in which hydrogen gas is generated; the electroplating seals the hydrogen into the article being plated. So even if the parts never see a pH below 7, there can still be hydrogen embrittlement.
P.S.: After reviewing this thread, I should add this postscript: A few inquiries asked how one can be sure that failure is due to hydrogen embrittlement. One telling characteristic of hydrogen embrittlement is intergranular failure (metallurgists call it "rock candy"), which is clearly evident under strong magnification (roughly 500x or 600x). More rounded asperities in the fracture face would contraindicate hydrogen embrittlement. I have seen respected testing laboratories conclude that plating + breaking = hydrogen embrittlement. That is sometimes the case, but sometimes not. You have to look at the fracture face.
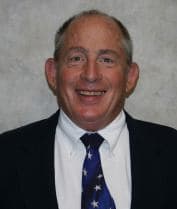
Tom Rochester
CTO - Jackson, Michigan, USA
Plating Systems & Technologies, Inc.

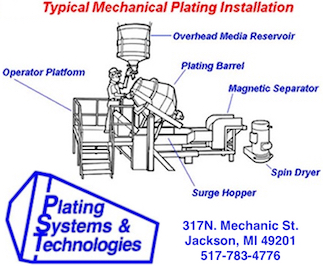
Very interesting postscript, Tom, which I had never heard before.
Regards,
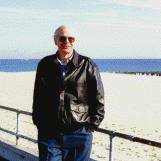
Ted Mooney, P.E.
Striving to live Aloha
finishing.com - Pine Beach, New Jersey
A. There is a phenomenon known as caustic embrittlement and is commonly associated with things that use very concentrated forms of caustic solution, or the solution is used under forcing conditions. I haven't seen anything that says pH 10-11 would be a problem unless you are using the solution as a cathodic cleaner, in which case you can generate hydrogen for embrittlement.
Brian TerryAerospace - Yeovil, Somerset, UK
Q. My initial question may be not clear; sorry about that. We are CLEANING parts, not plating parts. We just simply clean parts in ultrasound tank with Omegaclean solvent (by Omegasonics). Thanks.
David Ho- Milford, Connecticut, USA
November 20, 2013
A. For hydrogen embrittlement to occur, generally two factors must be present: (1) a mechanism for producing hydrogen, and (2) a process that seals the hydrogen into the substrate. Since neither of these two factors would appear to be present in your process, one can reasonable assume that it is hydrogen-embrittlement-free.
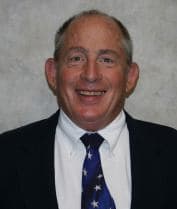
Tom Rochester
CTO - Jackson, Michigan, USA
Plating Systems & Technologies, Inc.

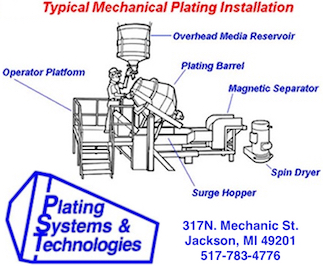
Q. Out of curiousity, is the 'process that seals' required? I always thought that just exposure such as cathodic cleaning or acid etching was sufficient to pose a risk.
Willie Alexander- Colorado Springs, Colorado
A. Hydrogen generated during cleaning or pickling (or etching) is usually considered "self-relieving" in that the hydrogen can escape easily. That is why phosphating and mechanical plating (to name two non-embrittling processes) are considered non-embrittling processes. Parts tested immediately after plating may exhibit transient hydrogen embrittlement, but this goes away as the hydrogen escapes at room temperature without baking.
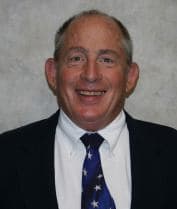
Tom Rochester
CTO - Jackson, Michigan, USA
Plating Systems & Technologies, Inc.

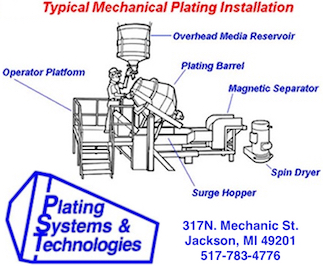
November 26, 2013
Is hydrogen embrittlement a problem if plated parts are stripped immediately?
Q. If parts are plated, and the plating is stripped almost immediately due to a plating defect, is hydrogen embrittlement still a concern, given that the "sealing process" has been conducted but removed soon after?
Rob Ogden- Jamestown New York USA
September 29, 2015
A. Current 'best practice' is to bake within one hour of plating. If your 'almost immediately' is within one hour you have a defensible position if the parts break. And they might.
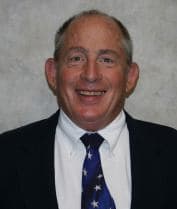
Tom Rochester
CTO - Jackson, Michigan, USA
Plating Systems & Technologies, Inc.

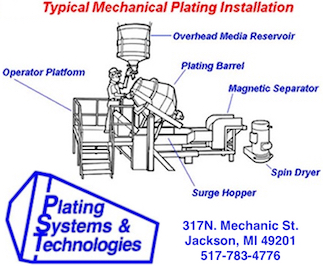
Q. Is anybody aware of a simple test to validate that hydrogen embrittlement was not introduced into a batch of helical compression springs (not necessarily a full proof test but one that will catch provide some assurance against gross processing errors). We have many zinc electroplated music wire springs produced for our products. I know of simple bolt tests where a sample qty is torqued to 80% of failure, let rest under load for 24 hours, release torque and reapply same torque. A break is a strong indicator that HE is present. For more assurance, check again at 48 and 72 hours. I am considering a specification that the supplier load the springs to solid height for 24 hours and a break is a failure. Possibly add a release and reapply step. However, every spring is different and the stress at solid height might not be significant enough to induce an embrittlement failure. Thank you
Scott BrownCurtiss Wright - Portland, Oregon, USA
March 15, 2017
A. Hi Scott,
Do you employ a de-embrittlement step after plating? If not, 8 hrs. in an oven at 200 °C will remove hydrogen that can lead to embrittlement. So a test should only be needed afterwards for verification if you wish. This should be done as soon as possible after plating, no more than 4 hrs. and preferably within 1 hr.
Best regards
- A cold rock in the Irish Sea
March 20, 2017
Thanks for the reply Mark. The supplier does do a bake after plating. And I intended for the embrittlement validation test to come after that.
- Portland, Oregon
March 20, 2017
A. This is not responsive to your question but it is relevant. I'd recommend reading ASTM B849-02 and ASTM B850-98.
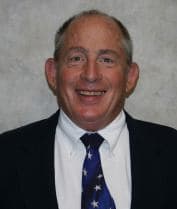
Tom Rochester
CTO - Jackson, Michigan, USA
Plating Systems & Technologies, Inc.

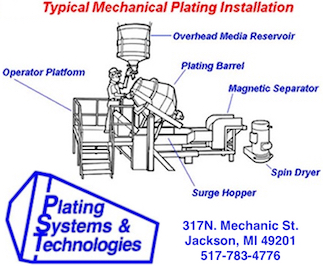
A. Hi Scott,
There is a test you can do.
If you plate notched bars alongside the springs they can be used to test for embrittlement, via tensile testing.
ASTM F519 will tell you all you need to know about the test and what constitutes a pass or fail.
Good luck
- Cold snowy rock in the irish sea
March 22, 2017
Thanks Mark. BTW, you'd better stick to plating -- I don't think you'd be good at real estate sales.
Regards,
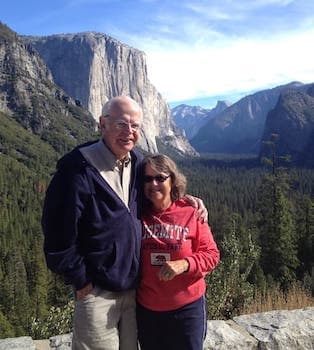
Ted Mooney, P.E. RET
Striving to live Aloha
finishing.com - Pine Beach, New Jersey
Q. I am planning to carry out hydrogen de-embrittlement baking for a set of parts -- a cycle of 200 °C for 8 hours.
The parts can only be plated one at a time due to their large size (zinc nickel plating on a high strength steel). The plating cycle is 1 hour but the baking duration is 8 hours -- hence cycle time mismatch for production planning.
I need to know whether it would be permissible to interrupt the baking process during hydrogen de-embrittlement for a short while, in order to open the oven doors and add another component into the oven, so that I can plan production for at least 2 parts one after the other. The oven can hold 2 parts at a time.
The oven temperature would probably drop from 200 °C to 100 °C in the interval when the doors are open.
It might take another 20-30 minutes for the temperature to climb back up to °C.
Will the drop in temperature due to the interruption adversely affect the HE process ?
Thanks in advance!
- Belgaum,Karnataka, India
March 8, 2017
A. Hi Ravi,
I would suggest adding time to the eight hours. The addition would be equal to the amount of time the item was not heated at 200 due to re-loading, perhaps thirty minutes as mentioned in your post.
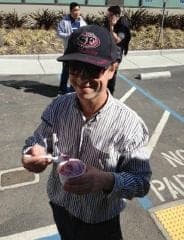
Blake Kneedler
Feather Hollow Eng. - Stockton, California
Thanks a lot, Blake. Appreciate your response. It is immensely helpful.
Q. Although it has appeared once earlier on this thread, albeit in a very brief manner, I would like to ask again the following:
If we have to strip the part immediately after plating for rework, does it need to be de-embrittled before replating? If yes, how many hours; which standard clearly mentions the times and temperatures for stripping rework? Would be using HCL solution say 20%, for stripping.
- Belgaum, India
Silver Plating fails notchbar tests despite hydrogen embrittlement relief before & after plating
Q. THIS IS ELVIS INDARTE. IN THE LAST THREE MONTHS I'M HAVING PROBLEMS WITH HYDROGEN EMBRITTLEMENT FAILURES IN TESTING NOTCHES FOR SILVER PLATING. THE STRESS RELIEF IS DONE IMMEDIATELY IN A 15 MINUTES PERIOD AFTER PLATING AND I BAKE THE NOTCHES 375 °F FOR 8 HOURS PRIOR TO PLATE AND 375 °F FOR 23 HOURS AFTER PLATE. THE PARAMETERS OF THE SOLUTION ARE GOOD WITH A LITTLE HIGH CARBONATE. I AM STOPPED WITH THE SILVER PLATE UNTIL I GET A SOLUTION, CAN SOMEBODY HELP ME? I DON'T NOT WHAT TO DO?
Elvis Indarte- college point, New York USA
May 12, 2017
![]() |
May 13, 2017 I'm not a big fan of testing surrogate parts. If you have real world parts that break even though the surrogate parts are okay, you are still in trouble. And if the surrogate parts break and the real world parts don't, you are almost certainly okay. But this is only my opinion. ![]() Tom Rochester CTO - Jackson, Michigan, USA Plating Systems & Technologies, Inc. ![]() ![]() Hi Elvis, Aerospace - Yeovil, Somerset, UK |
Q. Most of the information I read regarding hydrogen embrittlement after plating references an electrolytic plating process, such as electrolytic nickel plating. We process many parts and have them plated using an autocatalytic (electroless) nickel plating process per ASTM B733. Is there a difference in hydrogen embrittlement levels after an electrolytic plating process versus an electroless process?
Robert DiamondL3 Narda-MITEQ - Hauppauge, New York, USA
December 5, 2017
A. Hi Robert!
In thread 82/54 our colleague James Watts gave an ambiguous answer about this topic. EN does add some hydrogen to the structure of the metal, but less than electrolytic nickel. The hydrogen forms in the pickling process prior to plating, and the nickel layer traps it in the metal structure.
Baking is the only way you can reduce the hydrogen levels, and the risk of part failure.
So, it depends of your part prior to plate (shape, hardness, material, microstructure) and how it is used (torque, tension clamp, friction coefficient) to assess risk and need of baking to relieve embrittlement.
ASTM B733 guides you in choosing the best pretreatments and baking processes in order to minimize risks of failure by hydrogen embrittlement.
Best of luck!
Regards!
TEL - N FERRARIS - Cañuelas, Buenos Aires, Argentina
Q. Hi,
My plating supplier made a process error, parts that were already baked, was re-baked again.
Process flow should be HT -> Plating -> Baking -> Chromating.
Actual process HT -> Plating -> Baking -> Baking
I would like to know if the parts can directly go to chromating or we should do HT process -> Baking again?
Press Stamping, Heat Treatment and Plating - Bekasi, West Java, Indonesia
October 10, 2019
A. Hi Ahras. To my knowledge the temperatures used for hydrogen de-embrittlement are much lower than for heat treatment. So baking, whether done once or twice, should not affect the heat treatment. However, you may find it difficult to chromate the plating if a lot of time has gone by.
Regards,
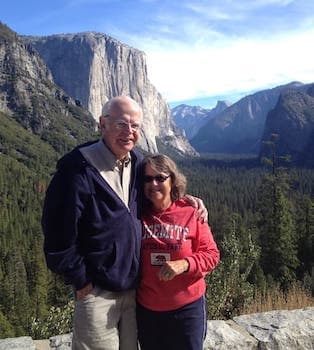
Ted Mooney, P.E. RET
Striving to live Aloha
finishing.com - Pine Beach, New Jersey
Does Metal Spraying Cause Hydrogen Embrittlement?
Q. John from South Africa here. I am molybdenum spraying Titanium Ti-6AL-4V wing attachment pins and would appreciate it if I could find some guidance on whether baking is required to remove hydrogen after plating. Temperature and duration would be appreciated. Thanks.
John BrindleAviation - South Africa
November 8, 2019
Q. I have a bolt that is 15-5PH H/T 180-200 KSI that has hydrogen embrittlement occurring after hard chrome plate. The part is processed in two plating operations. One operation is to plate the shank and the other to plate the washer pad (underneath the head of the bolt). The part gets activated in sulfuric HF anodically and then plated. Plating time is 6-12 hours per operation. Parts are baked before plate for 4 hours at 375 °F and after plating for 24 hours at 375 °F. The part goes in the oven after plating within 2 hours.
Hydrogen embrittlement is occurring in the threads after plating. Do you have any ideas why is hydrogen embrittlement occurring? Can hydrogen embrittlement be reduced by activating the part in chromic acid etch or in the plating tank?
- Torrance, California, USA
December 5, 2019
A. Hi Orlando,
Embrittlement is time-dependent. You have a break in plating, which, I assume, is being used to strip masking and reapply masking to other areas before continuing plating. If this is the case, I would suggest you need two de-embrittlement operations, after each plating operation. This should eliminate the risk of embrittlement due to the break in plating.
Aerospace - Yeovil, Somerset, UK
Q. I am constrained to use sulfuric HF for activation, alkaline cleaner for cleaning the part, and chrome plating solution. The only thing I can do to reduce HE is baking in the oven. Seems not to do anything increasing the bake time. Any suggestions?
Orlando Castillo [returning]- Torrance, California
December 14, 2019
A. Orlando,
Did you follow the AMS2759/9?
If you follow it I think that the problem will be solved.
AEROSPACE - SAO PAULO, BRAZIL
A. Hi. It sounds like you have no choice but to modify the cleaning, masking, plating cycle Orlando. It seems to me that Brian is implying that the HE damage is done before the parts even get to the oven, such that by then baking can't fix it. Sadly --
"The Moving Finger writes; and, having writ,
Moves on: nor all thy Piety nor Wit
Shall lure it back to cancel half a Line,
Nor all thy Tears wash out a Word of it." --Omar Khayyám
Good luck and Regards,
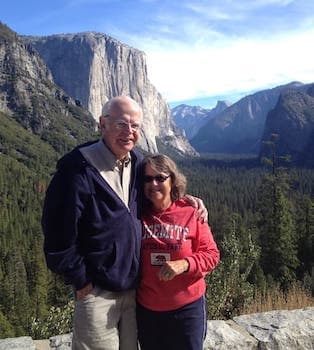
Ted Mooney, P.E. RET
Striving to live Aloha
finishing.com - Pine Beach, New Jersey
A. Hi Orlando,
Your answer from Dec. 14 does not refer to Brian's recommendation from Dec. 6.
Let me explain: To prevent hydrogen embrittlement (HE) the baking must begin ASAP after plating and never more than 4 hours after plating. Otherwise H atoms join to H2 molecule and cannot diffuse out of metal matrix.
So, if you have two different locations to plate, you have to bake the part after each plating step.
- Lod, Israel
Hydrogen embrittlement relief is softening our carburized parts
Hello, I work in the automotive industry and have been working in supply management for about 4 years.
Right now I've been facing a problem with H.E. on a bracket - lift hook, material is steel 1008 (low carbon) with a thickness of 4 mm.
Initially the process flow was: STAMPING > CARBURIZING > TEMPER > PLATING
After a focused analysis because of fracture problems, we found that the parts were going into failure due to Hydrogen Embrittlement.
So now the current process flow is: STAMPING > CARBURIZING > TEMPER > PLATING > BAKING (8 hrs at 140 °C).
However, I've noticed that the surface hardness of the final product changed as well. From min. 58 HRC (old process) to min. 40 HRC (current process).
Does this make sense? Can we say we are expecting a reduction on the surface hardness after a baking process for HE Relief of 8 hours at 140 °C + 4 hours of natural cooling?
Thank you!
- San Luis Potosi, Mexico
October 7, 2020

Q, A, or Comment on THIS thread -or- Start a NEW Thread