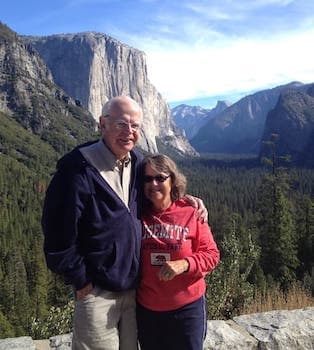
Curated with aloha by
Ted Mooney, P.E. RET
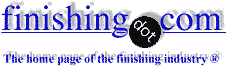
The authoritative public forum
for Metal Finishing 1989-2025
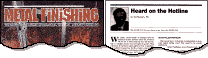
-----
Hydrogen Embrittlement in Plating
Q. We have had problems with a metal clip, and it is said to be due to "hydrogen embrittlement". What is hydrogen embrittlement, and how do you avoid/alleviate it?
Michael MarshallIndianapolis, Indiana
1996
1996
A. Hydrogen embrittlement is a phenomenon that affects high-strength steel. Hydrogen--often from pickling or plating--invades the grain structure of a high strength steel, making it brittle and subject to catastrophic failure.
The best approach is to avoid or minimize processes that cause hydrogen embrittlement. The second best approach is to bake the parts to drive the hydrogen out, preferably very soon after plating. Some people feel that some degree of permanent damage occurs during the time between plating and baking, and that it is thus vital to bake immediately. Others feel that the old standard "bake within 24 hours" is sufficient. ASTM Committee B-8 spent a lot of time on this problem, so I think their specs are highly trustable.
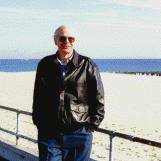
Ted Mooney, P.E.
Striving to live Aloha
finishing.com - Pine Beach, New Jersey
A. Michael: We have had some experience with the phenomena of hydrogen embrittlement. A good reference book is "Hydrogen Embrittlement and Stress Corrosion Cracking" [on Amazon or on AbeBooks affil links] by Gibala & Hehemann (ASM Publication). It is quite detailed and informative.
Brian CardwellFord Motor Company
1996
Q. I am looking for articles on "Hydrogen Embrittlement" in the plating process.
John M. GrimesCutler-Hammer
1996
A. Over the years, the Airline Plating Forum has had several papers given on the subject. Available thru the AESF bookstore. There is a stray article in the plating magazines. Seems to me that the big book ASM library had some information on it. You might check the index for the various Sur-Fin abstracts. These probably will be more technical and less practical.
James Watts- Navarre, Florida
1996
Do corners and high current density areas get more hydrogen embrittlement?
Q. During plating, are the corners of objects preferential sites for hydrogen and therefore more susceptible to hydrogen embrittlement?
David M. FrenchCharlotte North Carolina
1998
(includes 7 papers / 34 pages on electroplating)
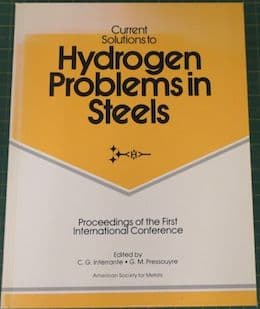
on eBay or
Amazon
(affil links)
A. Yes and no. Since the edges (corners) are high current density areas, they plate much faster, so more H2 is generated there, so it will be a little more prone to problems there. In high stress deposits, the additional thickness puts the parent material under a lot more stress, so will tend to have more problems there.
A stress riser like a tiny cut from a razor blade in masking on a high tensile strength part will be much more prone to fail. Inadequate radius at flanges are very prone to failure. The end result is a failed part, but the root causes are wildly different.
James Watts- Navarre, Florida
1998
A. The amount of Hydrogen Embrittlement absorbed during electroplating is related to the current density on the cathode surface of the article being plated. Higher current density areas will evolve more Hydrogen gas and therefore the potential for embrittlement is higher. Edges will normally be higher current density than flat surfaces. Edges that are on bottom rows of racks will most likely have higher levels of absorbed Hydrogen. In most cases of electroplating, edges will have higher preferential sites for Hydrogen Embrittlement. Maintaining optimum electroplating efficiencies and additions of wetting agents are variables that can help reduce embrittlement by Hydrogen gas.
Bill BoatrightMorrisville, North Carolina
1998
A. Higher current densities will definitely produce more hydrogen per metal deposited, but...
Some processes (for sure low embrittlement cadmium, but maybe some others too?) use high current densities on purpose in order to produce porous plating that allows for easy hydrogen molecule escape during the subsequent bake.
In general I do not think that areas where most of the hydrogen is absorbed would suffer higher danger of embrittlement: metal is a "transparent" media for protons (hydrogen atom's nucleus), therefore the bulk of the plated part (even the non-plated part of it, if masked) will be equally prone to embrittlement.
The question remaining - where it may break? - in the point of maximum stress, even if that portion of the part is not plated.
This is just an opinion...
Max Steincaptive metal finisher - Montreal, Québec, Canada
1998
How to identify hydrogen embrittlement?
Q. How does one determine if breakage is caused by hydrogen embrittlement? We have parts which are made from 1074 steel, .0135" thick, which has been formed (into a question mark shape) and then heat treated to RC 44-47. These parts can be bent without breakage. However after zinc and bake, they do break when bent pretty far back in the large radius area.
How does one determine if the breakage is caused by hydrogen embrittlement? Or is it possible that just by plating these parts, they will become more prone towards breakage?
Andrew Robertssprings - San Leandro, California
1998
A. If you had access to a Scanning Electron Microscope (SEM) and someone with experience in analyzing for Hydrogen Contamination it could be possible to show breakage was caused by Hydrogen Embrittlement.
However, since you say the parts are not breaking before plating but are breaking after, the possibility is strong that hydrogen embrittlement is occurring in your parts. Have you baked the parts for hydrogen embrittlement relief immediately after plating and before bending.
Greg Haatajahelicopters - Fort Worth, Texas
1998
A. You have about as close to 100% probability as you will ever get that you have a classic H2 embrittlement problem.
Bake as soon as possible after plating. The longer the H2 is trapped between the plate and the base metal, the further it penetrates the steel and the harder it is to get out.
Do not flex the parts even a tiny bit taking them off the rack!
If you are baking, get there sooner and bake longer or at a higher temp.
After bake a very quick dip in a mild (weak) nitric solution will activate it enough that it will take a chromate. Consult your chromate vendor and do some trial and error testing to see how weak you can get by with.
James Watts- Navarre, Florida
1998
A. A considerable amount of work on hydrogen embrittlement has been conducted and published in the literature. Some important work was done and published by scientists at the Naval Air Warfare Center. The bottom line is: it is nearly impossible to remove all of the hydrogen that has been introduced, using common baking methods. Once the damage is done, it can be reduced to some extent. The amount of damage and reduction will depend on dozens of variables such as the part, its material, coating, process, amount of hydrogen generated and absorbed and combinations thereof. Relief is likely to be inconsistent. This inconsistency could be reduced by porosity in the coatings.
Mandar Sunthankar- Fort Collins, Colorado
1998
A. Hydrogen embrittlement is typically manifested as "delayed fracture" at static stresses, which would be contrary to immediate failure during bending. Your parts, however, are quite susceptible to hydrogen damage and may be cracked during plating if the parts have sufficient residual stress from heat treating. A static load test with less deflection than will cause immediate cracking could be definitive.
Another alternative to consider is possible embrittlement due to the baking process. This material is susceptible to tempered martensite embrittlement, usually from exposure to temperatures from 400 °F to 700 °F. I would avoid baking at temperatures above 375 °F.
I agree with Mr. Sunthankar that baking is not 100% effective. The extreme susceptibility of this material to cracking by hydrogen embrittlement would suggest to me that an alternative corrosion protection would be prudent.
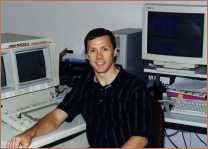
Larry Hanke
Minneapolis, Minnesota
1998
Alternatives to Plating to Minimize Hydrogen Embrittlement
A. If hydrogen embrittlement is of concern, you may want to consider mechanical plating and/or galvanizing. I have been involved in many studies comparing zinc electroplating, hot dip galvanizing and mechanical -- and mechanical does not impart hydrogen.
Ray DeloreyCambridge, Ontario, Canada
1998
A. One of the best systems for coating that do not have any hydrogen embrittlement is the Thermal Diffusion zinc coating system. Google it and you'll learn quite a bit.
Dorian Shifman- Charlotte, North Carolina
2006
----
Ed. note: Thermal Diffusion is an upgrade to the older process called Sherardizing, which is discussed in many threads on this site.
Can heat treating cause hydrogen embrittlement?
Q. Could you please let me know if there is a possibility for hydrogen embrittlement to be introduced into my parts during this heat treat process:
Material: .012" ± .001" C1050 Annealed Spring Steel
Heat Treat: Austempered to Spring Temper Rc 38-42
I know that I have a hydrogen embrittlement problem induced by my plater due to improperly calibrated ovens for baking off the hydrogen. I need to know if there are other ways for hydrogen to be introduced into my stampings.
Adam Rubin- Brockton, Massachusetts
1999
1999
A. I really do not want to get in the middle of an argument, but will express my opinion.
I have never heard of hydrogen embrittlement being caused by bake.
Uncalibrated ovens probably did not contribute much to hydrogen embrittlement of your parts because bake relief is really wide open as a function of time and temperature. 375 °F for 4 hours is + or - 25 °F as a common relief.
Two things cause more grief than a few degrees difference.
1. The time between plating and into the oven. For spring material is should be as soon as possible. The 4 hour book value is really too long. The longer you wait, the harder it is to get out and the more damage has been done.
2. The acid activation or etch contributes more to embrittlement than the plating process does. For spring steel I would use periodic reverse or anodic electroclean followed by a very short, say 10 second dip in a conventional hydrochloric or sulfuric acid tank. I have done cyanide and acid cad without a failure of notch bar testing at some very high tensile strengths.
If these are not critical parts to safety, I would bake them for 24 hours, possibly 48 for better reliability and use them. These are tiny parts that can be nicely run in a lab oven at a very low cost with a decent recovery of the unbroken parts.
James Watts- Navarre, Florida
1999
A. To answer part of Mr. Rubin's question (can austempering cause hydrogen embrittlement?):
I would say no, especially if the austenitizing (not the quenching) is done in salt. If the austenitizing is done in an atmosphere furnace (typically endothermic gas at 40% H2), then some hydrogen is absorbed by the metal. I suppose one could argue that this might cause HE. I know it can cause delayed quench cracking in parts quenched in media such as water or oil, and although hydrogen levels are probably much lower than in "classical" HE, it could be called hydrogen embrittlement. I doubt very much that cracking would occur in an austempered part because the residual stresses and residual hydrogen levels are typically much lower due to the gentler quench rates and the residence time at the austempering temperature.
In other words, it's hard to imagine austempering causing HE, and I think most metallurgists and heat treaters would agree they've never identified such an occurrence or even suspected the possibility.
John UllmanDoes GM4345M Phos & Oil require de-embrittlement?
Q. When 1050 material is processed to an Rc range of 40 - 48 and subsequently plated to GM4345M commonly referred to as Phos & Oil, what is the correct practice with respect to baking this porous plating?
Is baking necessary, or is delay in use after plating sufficient to allow the H2 to outgas? If delay is sufficient, what is the recommended period of time for delay?
What role does acid concentration play in processing the Phos & Oil in the cleaning tanks? A common standard seems to be to stay under 30%, is there a recommended concentration? What is it?, and is there a maximum that should not be exceeded to avoid hydrogen embrittlement?
Time in the tank is controlled to under 10 minutes.
L.C. WoodDetroit, Michigan
1999
A. Bake- You have to conform to what the spec calls out.
Many specs would not call for a bake at an Rc of 40. I do not remember doing one at Rc48, so cannot be of any help there.
Many people will not refer to phosphate as plating, since you are not depositing a metal or alloy.
Acid normally will be as strong as you need to do the job, but no stronger. Time is a tradeoff with acid strength. You have to specify the acid when you talk %'s. Sulfuric acid has two H's, so is basically twice as strong as hydrochloric (muriatic). Some people use mixed acids.
Acid etch is a major contributor to hydrogen embrittlement, so any etch should be the minimum to get by on hard parts.
If you use an acid etch, You really need to use a proprietary Ti compound additive to the last rinse prior to phosphate. Normally, you will get a lousy phosphate if you do not. I have heard of a very few that have avoided it.
James Watts- Navarre, Florida
1999
Q. We manufacture and electroplate automotive safety hardware and are very well aware of the "critical" stress relieving requirements. However, we also have a large volume of parts which are sub-contracted for E-coating that do not specify any stress relieving requirements. My question is: "If similar pre-cleaning cycles and materials are used for the cleaning of steel parts for electroplating and/or e-coating, how come e-coated parts do not specify a post bake to relieve any possibility of hydrogen embrittlement during the processing"? It appears to me that the temperature and time required to bake the paint film is not sufficient to remove induced hydrogen.
Rodney C. Todd, CEF- Ontario, Canada
1999
A. What kind of steel and what is the hardness? Usually embrittlement is not considered a problem below Rockwell C-40 or 180 ksi, although some callouts go as low as C-30. How hot and how long is the bake cycle for your E-coat? Have you run any test specimens? We have found tempered Belleville washers to be simple test pieces. Easily compressed and you can run a large number for statistical reliability,
C.A.Smithaerospace - Nashville, Tennessee
1999
----
Ed. note: Thanks, C.A.! That Belleville washer idea sounds like a great suggestion.
(you are on the 1st page of the thread) Next page >
Q, A, or Comment on THIS thread -or- Start a NEW Thread