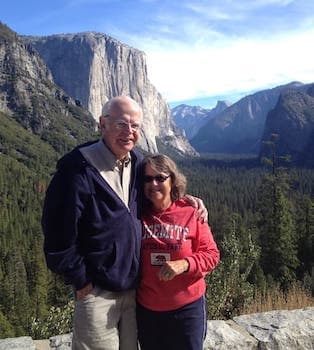
Curated with aloha by
Ted Mooney, P.E. RET
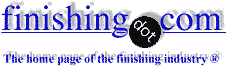
The authoritative public forum
for Metal Finishing 1989-2025
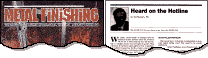
-----
Mill Scale Removal Q&A
Tip: Readers want to learn from Your Situation 🙂
(little can be learned from abstract questions, so many readers skip them)
Q. If you forge HP&O steel will it put mill scale back on it?
J smith- Missouri
September 7, 2022
A. Hi J. Forging -- per se -- will not cause mill scale. But the conditions you expose the steel to might. Red hot steel which is not protected from the oxygen in the atmosphere acquires a mill scale from those oxidizing conditions.
Luck & Regards,
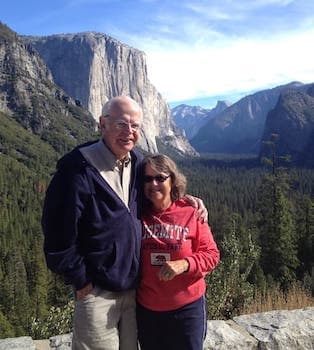
Ted Mooney, P.E. RET
Striving to live Aloha
finishing.com - Pine Beach, New Jersey
⇩ Related postings, oldest first ⇩
Q. I have read with interest about a product called "Picklex® [affil links]" which can supposedly remove mill scale from hot-rolled steel. Does anyone have experience with this product and does it work as advertised?
Joe Lang- Tualatin, Oregon
2000
A. Hi, Joe.
We can't do testimonials to or criticisms of proprietary products on this largely anonymous page ( huh? why?). But if anyone has links to peer-reviewed literature about this product, or comments on the general technology, we'd be happy to see them.
Ted Mooney, P.E.
Striving to live Aloha
finishing.com - Pine Beach, New Jersey
A. The EPA did an in depth study on this. The following is a link to the report. I am going to be using it shortly so I will follow up.
www.epa.gov/nrmrl/std/mtb/pdf/web-powdercoatarticleversion1.pdf
- Jacksonville Florida USA
July 12, 2011
----
Ed. note Feb. 2015: Sorry that link is now broken :-(
Thanks, Darwin!
We linked to the original report on letter 24256 back in 2003; thanks for the link to the followup study.
Yes, please do give us some feedback, hopefully including some actual cost figures, after you've implemented it.
As a plating consultant and columnist for plating journals for decades, I established the regular routine of checking up each month on the success stories printed on the front covers of the metal finishing journals 3 years earlier. The shine had worn off in the majority of cases; hopefully that will not be the case here. It would be interesting to hear from you in 3 years as to whether you are still using it, or to hear from someone who installed it 3 years ago and is still using it.
Regards,
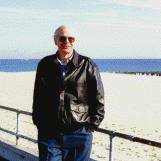
Ted Mooney, P.E.
Striving to live Aloha
finishing.com - Pine Beach, New Jersey
Q. Hi everyone.
We are trying to remove mill scale from steel prior to a powdercoat. What acid is the best to use for the removal of mill scale and rust? I seem to recall that Sulfuric acid is a good one for mill scale, but doesn't do the job on plasma edges. Just looking for some confirmation on my memory.
Thanks!
James Hanley- Seattle, Washington
2001
A. Hi,
The "most pleasant" acid to use would be an inhibited phosphoric acid based pickle. It can be used in stainless steel eqpt and is compatible with the following phosphate process. It is also less likely to rust stain compared to the other acids. If by plasma scale you are referring to laser cutting, then there is no problem.
Roger BridgerWalterisation UK Ltd - Croydon, UK
A. Yes, you are right. Sulfuric acid is one of the common acids used to remove mill scale and the another is hydrochloric acid. The former is cheaper and efficient in the most case, but highly dense scale, such as plasma edges. The critical difference among both acids is working mechanism. Sulfuric acid penetrate per crack in scale layer and works underneath scale rather than dissolving scale and rust, but, on contrary, hydrochloric acid does.
Jun Zhang- Cincinnati, Ohio, USA
Removing gray scale on hot-rolled steel
Q. I am an entrepreneur in the field of Surface coating of Steel. My plant is located in India. Of late I am getting large sheet-metal parts having sheet thickness of less than 1 mm for coating.
Shot-blasting to removes gray oxide scales from surface is ruled out as it distorts the component. I am forced to do HCl acid pickling to remove the scales. But using HCl has seriously corroded the plant structures and equipment around. Besides, work-atmosphere is hazardous.
Is there any other cheap method to get rid of the gray scales? What are the methods used by large manufacturing companies to remove mill-scale?
Technocrat and entrepreneur, coating plant - Pune, India
October 15, 2009
A. There are alkaline rust removers and electrolytic alkaline rust removers. You need to do some testing before you commit to anything as some scale requires a permanganate prep step which I find to be less than wonderful to use and to maintain.
You could try a lower strength sulfuric acid and you could try it electrolytically. There are blends of acids that are proprietary
(more expensive) that work.
Finally, the blast will work if you lower the pressure and use one of the carbide grits. You need to do each side equally which will nearly eliminate the warping.
- Navarre, Florida
A. Mahesh, 10-15 percent sulfuric acid at any temperature over about
55 °C works fine. Sulfuric acid does not release free acid into the air like hydrochloric does. It will actually work at any temperature down to ambient, but the lower the temperature, the slower the cleaning. We find that 55-60 °C is fine - at that temperature, it removes mill scale from hot-rolled structural sections in around 15 minutes which suits the operation of the shop.
Whichever acid you use, you must add an inhibitor to it, which allows the acid to attack the scale but severely retards attack on the base metal itself.
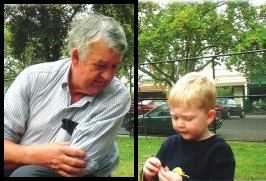
Bill Reynolds [deceased]
consultant metallurgist - Ballarat, Victoria, Australia
We sadly relate the news that Bill passed away on Jan. 29, 2010.
A. Ya Bill, sulfuric acid is a good option compared to HCl, but at elevated temperature it also creates fumes in the atmosphere. Besides, is it not more harmful to the Human skin?
Use of Inhibitors I guess will work well.
I learned that some branded companies sell pickling acid in a particular combination of both Sulfuric acid and HCl. Is it true?
Surface coating - Pune, India
A. Sir:
You need a copy of my article on the Selection and Use of Pickling Acid Inhibitors which is published in the journal METAL FINISHING. The proper inhibitor reduces acid fumes by 90% to 99%. Obviously you need to know the proper concentration and temperature to use either acid (HCl or H2SO4). I have experimented with mixtures of HCl and H2SO4 and did not like the results. It is true that HCl fumes fill up a plant from the ground up, whereas H2SO4 properly inhibited the fumes are local around the acid tank and not nearly so corrosive to the entire building and equipment.
Regards,
Galvanizing Consultant - Hot Springs, South Dakota, USA
Q. Use of Sulfuric acid is working fine and better than HCl. What should be the suitable Effluent treatment for used Sulfuric acid in this case?
Mahesh Behra [returning]Surfactant Solutions - Pune, India
November 1, 2009
Q. I have a customer looking for a easy, quick test to determine if all the mill scale has been removed.
Joel BialekSell Inspection Equipment - Lapeer, Michigan
September 14, 2011
Tip: Readers want to learn from Your Situation 🙂
(little can be learned from abstract questions, so many readers skip them)
Q.
When hydrochloric acid pickling mild steel what is the loss of weight owing to removal of mill scale and rust.
- kolkata, west bengal, India
October 9, 2021
A. Hi Vikash.
I would not know how much mill scale and rust was on your steel, of course, but yes, the weight loss from pickling is equal to the amount of mill scale and rust that was on the steel assuming 100% of the mill scale and rust gets removed and assuming that the inhibitors employed are sufficient to insure 0% attack on the steel.
Luck & Regards,
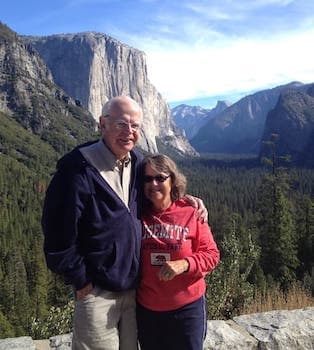
Ted Mooney, P.E. RET
Striving to live Aloha
finishing.com - Pine Beach, New Jersey
A. Hi Vikash,
You could quantify the loses to the base metal by conducting an etch rate test.
Using a rust free, degreased, cleaned steel test panel of the alloy you process:-
While wearing gloves to prevent contamination of the panel, Measure its dimensions, calculate the surface area in centimeters.
Weigh the panel to at least 3 decimal places of a gram.
Record that weight.
Place the panel on a wire, then in the descale solution for the same length of time that the parts are in the descale solution.
Remove, rinse and dry the panel.
Weigh the panel again as before.
Subtract the second from the first weight.
Then calculate the weight lose per standard area, such as sq.ft (929.03 sq.cm), sq.decimeter (100 sq.cm), sq.metre (10,000 sq.cm), depending on your or any specification requirements.
This will tell you the etch rate of the base metal, and wether you need to add any inhibitor to the descaling solution.
Best of luck
- A foresaken rock in the irish Sea
Tip: Readers want to learn from Your Situation 🙂
(little can be learned from abstract questions, so many readers skip them)
Q. That is right Dear Mr. Ted. What I am trying to understand is that for a freshly rolled steel having no rust and just mill scale or a very light layer of fresh yellow rust, then what should be the weight loss if we consider that pure steel has not been attacked.
vikash goel- kolkata, west bengal, India
October 23, 2021
A. Hi again. Okay, it sounds like you're not really talking about HCl or inhibitors, or pickling or etching then ... you're asking how much mill scale or yellow rust should be expected/anticipated/allowed on freshly rolled steel.
• https://weldingacademy.online/2019/10/01/the-mill-scale-on-steel-and-welding/ says the thickness and composition will vary based on rolling temperature.
• medium.com/@bestadwise/everything-about-mill-scale-9bf2a59fec85 and www.corrosionpedia.com/definition/780/mill-scale say it tends to be about 1 mm thick.
• millscale.org claim to be world experts on this and should be able to help you.
But please tell us your situation rather than keeping this so abstract and hypothetical :-)
Luck & Regards,
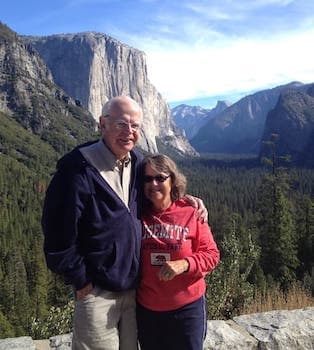
Ted Mooney, P.E. RET
Striving to live Aloha
finishing.com - Pine Beach, New Jersey
Q. Dear Mr Ted,
My query being new to this industry could have been a bit abstract. But I am really not able to understand is that for a freshly rolled steel or having light yellow rust once it is pickled with HCl with due inhibitors and the steel is completely clean for the purpose of hot dip galvanizing then what should be the average loss of weight of steel.
Further after galvanizing what is the increase in weight that one should ideally get against various microns of coating .
Please help me to understand this. Or you could kindly refer me a book on hot dip galvanizing also.
Thanking you in anticipation of a favourable reply.
- Kolkata West Bengal India
October 26, 2021
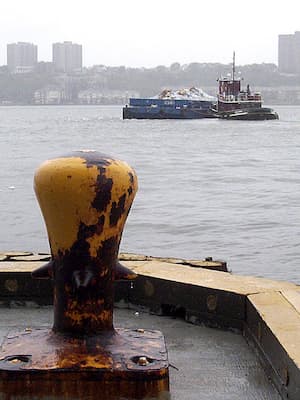
A. Hi Vikash. You're pretty much asking the same question again that has already been answered. And you already asked about the weight gain from galvanizing under topic 49676 and it was answered there. Maybe the problem is that you're not appreciating that metal finishing, including pickling of steel and galvanizing it) is "surface finishing": how much gets removed or added doesn't depend on the weight of the pieces you are processing, it depends on their surface area.
A mooring bollard might weigh a metric ton and have a surface area of a square meter. That same metric ton of steel if rolled into sheet may have a surface area 50X as great. Even after estimating the scale as being 1 mm thick, which it may or may not be depending on many factors, 1 mm of scale on the surface of the bollard surface would weigh under 1 kg and the mill scale on the sheet steel may weigh over 50 kg.
You ask about weight of galvanizing vs. various microns of coating. But this question usually applies only to coils which are galvanized in continuous coil-to-coil lines, complete with wipers of some sort, such that thickness is controllable to x grams per square meter. In the case of hot dip galvanizing of discrete components there is no such control; there is some dependence on silicon content and so on, but in general you get what you get, and Geoff Crowley estimated in thread 49676, but you will get something like 50X as much weight gain on the sheet metal than the bollard because the surface area if 50X bigger.
Luck & Regards,
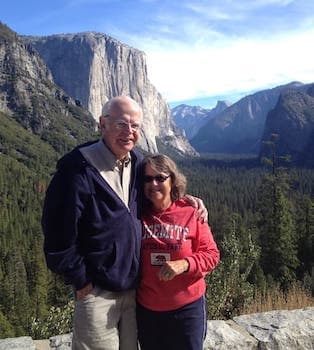
Ted Mooney, P.E. RET
Striving to live Aloha
finishing.com - Pine Beach, New Jersey
Q, A, or Comment on THIS thread -or- Start a NEW Thread