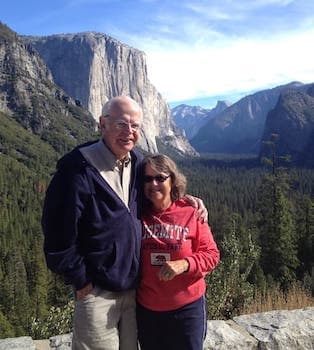
Curated with aloha by
Ted Mooney, P.E. RET
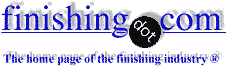
The authoritative public forum
for Metal Finishing 1989-2025
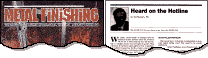
-----
Mil-DTL-5541 / Mil-C-5541 testing per ASTM B117
RFQ: MIL-DTL-5541
[⇦ this spec on DLA], paragraph 3.6.1 and 4.4.1 on corrosion resistance testing.
Looking for labs where we can send samples of conversion coating testing per 3.6.1 and 4.4.1, Table I
Manufacturing - Jacksonville Florida
May 23, 2023
privately respond to this RFQ
Ed. note: As always, gentle readers: technical replies in public and commercial replies in private please (huh? why?)
⇩ Related postings, oldest first ⇩
Q. When we do our monthly testing of Chromate per MIL-C-5541 E Class 1A and Class 3 using test panels we occasionally fail the salt spray test per ASTM B117. Our most consistent failure is for Class 3.
Does anyone have any ideas or suggestions on what we might do or where we can find some more information to pass this testing?
Jim S [last name deleted for privacy by Editor]- Minneapolis, Minnesota
2001
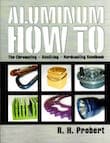
Aluminum How-To
"Chromating - Anodizing - Hardcoating"
by Robert Probert
Also available in Spanish
You'll love this book. Finishing.com has sold almost a thousand copies without a single return request :-)
A. There are several factors that affect the successful processing of panels that will pass the corrosion resistance test. The first place to look is the cleaning process. If the aluminum is not properly prepared, there may be discontinuities in the conversion coating. The second place to look would be the Chromate itself. Is there contamination? Is the process being performed in accordance with the manufacturers recommendations? Finally, I have had experiences with poor quality test panels. Another potential cause would be if the salt spray test is being applied to the panels at 15 degrees (As specified in ASTM B117) or at 6 degrees (As specified in MIL-C-5541). It is imperative to understand that the Class 3 coating is not going to be as corrosion resistant as a Class 1A coating. I hope this gives you some insight into solving your problem.
Best of Luck.
Ira Donovan, M.S.F.Kansas City, Missouri
A. We had the same problem before, tried to figure out what was wrong for about a year but without luck. Until I read repeatedly the technical brochure of the product we were using (Alodine).
There was a mention of post treatment. We inquired and asked for sample which they sent. It was a liquid that is supposed to be mixed with the final rinse. We had 100% passing mark ever since!
Dado Macapagal- Toronto
![]() |
A. I do not see a mention of post treatments anywhere in MIL-C-5541 or in MIL-DTL-81706 [⇦ this spec on DLA] . Products used to conform to MIL-C-5541 must be tested to meet the requirements of MIL-DTL-81706 [⇦ this spec on DLA] and be listed on QPL-81706 [⇦ this spec on DLA]. Can a sealer be used and still certify the resulting coating to MIL-C-5541? If so, why not use a can of spray furniture polish to enhance the corrosion resistance? Chris Jurey, Past-President IHAALuke Engineering & Mfg. Co. Inc. ![]() Wadsworth, Ohio ![]() A. Jim, I have a few suggestions ... 1st. Mil-C-5541E allows for use of 6061-T6 test panels for Class 3 coatings and alloy 6061 typically performs better in Salt Spray than alloy 2024. 2nd. Cleaning and treatment of the panels prior to chromating is very important. The most common culprit (from 30 years of testing) is the deoxidizer/desmutter tank. There are many reasons why a deoxider tank may not be working at full strength. We have seen all sorts of causes from the simple (drag over from the etch) to the bizarre (someone adding used automobile radiator fluid to the tank). There are a multitude of other possible causes that can be reducing the corrosion protection capabilities of your chromating process. If given a few more details, I may be able to narrow down your main culprit(s). Josh Taylor, C.E.F.- Baltimore, Maryland |
MIL-C-5541 Periodic Testing
Treatment &
Finishing of
Aluminium and
Its Alloys"
by Wernick, Pinner
& Sheasby
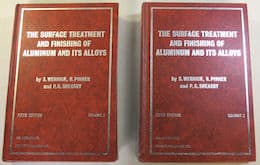
(note: this book is two volumes)
on eBay or
AbeBooks
or Amazon
(affil links)
Q. If the corrosion resistance testing cannot be performed with an actual production run, can the panels be ran separately? MIL-C-5541 states that the 35 days are exceeded, all the periodic tests are to be ran prior to production. If this happens our customer has to wait one week (168 hours). Customers are not going to wait. We will lose the order. What else can be done?
Gary FoxDirector, Quality Assurance - Santa Ana, California USA
June 11, 2015
A. Hi Gary,
MIL-DTL-5541 is very prescriptive; test pieces must be run with a production lot. It is sometimes impractical and, if it is greater 35 days since your last production run you will either have to run at risk or wait the 35 days. Even then, because of the way the specification is written you will need to process parts at risk with the test pieces, as we come back to the need to process with a production run.
What you could do is ask for a deviation from MIL-DTL-5541 to allow you to run the test pieces separately and within the 35 day window, meaning that production can be continued.
Aerospace - Yeovil, Somerset, UK
A. I'm looking over MIL-DTL-5541. It seems to be done with continuous production in mind, with the monthly (not exceeding 35 days between) testing. If anything fails a test, all "traceable and retrievable" parts produced since the previous round of testing are rejected. If the line has not been in production for over a month, then you are starting with a blank slate and perform the first round of testing immediately ("at the restart of production", not "prior to production").
You don't give much info on your situation, other than it's impractical to include the test specimens during the production run for the order. If you get this order, would you be starting up the line after over a month of shutdown? Would the order itself take more than 35 days to complete? Why are you unable to send a batch of test specimens through in between batches of the actual parts?
I don't see anything that actually says you have to wait the one week for the salt spray test results before doing anything else, only that if the results come back as a failure, you have to collect everything you can that was processed and scrap them. This is what Brian referred to as "running at risk", but the standard seems to be entirely designed for that, no part is ever run without risk since even with a continuous production, any "traceable and retrievable" part at any time can be rejected if the next testing cycle produces a failure.
I also don't see anything that actually says the test specimens must be run in the same batch as production parts, only that they must go through all the same processes as the actual production parts. It seems to be the general expectation that they will be run separately, though sequentially or concurrent, with the production parts.
You may have to be more specific about what your actual difficulty here is.
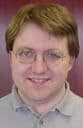
Ray Kremer
Stellar Solutions, Inc.

McHenry, Illinois
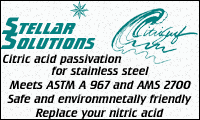
Q. Is anyone familiar with MIL-C-5541, Class 1A? Specifically, Salt / Spray testing, results.
Michael BerlutaQuality - Hugo, Oklahoma USA
February 4, 2016
Hi Michael. As you see, we appended your question to a thread on the subject and we have dozens other such threads. Yes, hundreds of our readers are familiar with the topic. You should probably be using MIL-DTL-5541 these days. What is your situation and your question?
Regards,
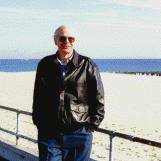
Ted Mooney, P.E.
Striving to live Aloha
finishing.com - Pine Beach, New Jersey
Q. We use a three bath (with rinses in between) system. A soap (caustic), Deoxidizer and a Hexavalent Chromate. We have gone several months without a Salt / fog test failure. Recently we have had two failures in a row. The most recent failure was with a fresh Chromate bath. This seems to go in cycles. We will go for months or a year or two without a failure, then for no apparent reason, we have a couple failures in a row and like the most recent, with fresh chemical. Actually, I was hoping to find an outfit to come to our location in S.E. Oklahoma, evaluate our system and help come up with a root cause analysis for these failures. There are many variables, of course, such as increased production demands, possible city make-up water problem to name a few. When my weekly titration tests reveal contamination or weakening concentration levels, I replace with fresh chemical. Sometimes we pass the monthly tests when it appears we shouldn't and other times we fail, when we do not see how it is possible.
Regards,
Michael
- Hugo, Oklahoma, USA
![]() |
A. A common reason for failure when all else appears okay is over etching. Minimize time or reduce concentration in your caustic cleaner and try again. ![]() Jeffrey Holmes, CEF Spartanburg, South Carolina A. The single most frequent reason for failing salt spray is in the raw panels to start. Look at your panels with a 10X loop. When you come back, tell us the alloy. Also tell us whether the chromate you are using is on the Qualified Products List. ![]() Robert H Probert Robert H Probert Technical Services ![]() Garner, North Carolina ![]() |
![]() |
- Hugo, Oklahoma USA A. Michael - Colorado Spsrings, Colorado A. Good day Michael. Aerotek Mfg. Ltd. - Whitby, Ontario, Canada |
Q, A, or Comment on THIS thread -or- Start a NEW Thread