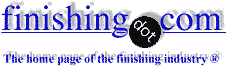
-----
Chrome Plating on Aluminum
1998
Hi,
I'm from El Salvador, C.A. and my question is how I get Hard Chrome onto aluminum base, please tell me about the chemicals to make the solution for activate the aluminum.
Thank you.
Remberto BritoReproqui S.A. de C.V.
1998
Activating of aluminium:
The aluminium article should be cleaned in a non caustic cleaner,then given a light pickle in 10-25% sulfuric acid, then dipped for 30-60 seconds in a zincate bath(see formulation below). For best results the article should then be cyanide-copper plated(3-4 mins) then placed in the hard chrome bath with the current switched on.
NB: Rinse well in between all of the above stages.
Zincate Bath Formulation:(to make 1 litre)
caustic soda ⇦liquid caustic soda in bulk on Amazon [affil link] .............525 g
Zinc oxide...............100 g
ferric chloride ⇦ on eBay or Amazon [affil links] crystals.1 g
Rochelle salt (potassium sodium tartrate) ⇦ on eBay or Amazon [affil links] .........10 g
Dissolve in the caustic soda first very carefully as this gives off alot of heat.Then dissolve in the Zinc oxide. Finally add the ferric chloride ⇦ on eBay or Amazon [affil links] and rochelle salt.
This process has given excellent results for me in the past.
Richard PalmerRio southern Electroplating
Hi, my name is Victor, I am going to be starting a project on my car, a 1996 Mitsubishi 3000GT SPYDER VR-4. I was wondering if someone there could help me. I am going to try to bond a thin layer of real Aluminum on a smooth surface of (primered) sheet metal, plastic, composites, & Carbon Fiber. My question is, can it be bonded by some type of glue adhesion, chemical bond, Plated on (like Chrome/Gold Plating), sprayed on melted hot as a liquid (which I doubt, without melting the plastics, & composites), or sprayed with an Aluminum based paint? At this point I plan to then polish it to a brilliant shine, then clearcote it. The reason I want to go with a Polished Aluminum look, & not a Chrome look is because IMHO Polished Aluminum looks better (not as mirror-like). I thank you for any information you can provide. =)
Best Regards,
Victor L.
Victor Lopez- Springfield, Massachusetts
2000
Aluminum cannot be deposited by electroplating except under very special circumstances that are at odds with your needs.
It is theoretically possible to deposit pure aluminum by a process called Ion Vapor Deposition (IVD) but even if you could afford to have it done, your car wouldn't fit in the chamber.
Cars are painted for reasons of practicality, I'm afraid. There are practical reasons why you don't see plated or aluminized cars, although at least one stainless steel DeLorean was gold plated.
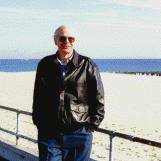
Ted Mooney, P.E.
Striving to live Aloha
finishing.com - Pine Beach, New Jersey
2000
I also would like to plate some car parts (just the wheels however). I was wondering if any body could explain or give suggestions as to how to plate Aluminium wheels. I would like them a color similar to silver (not gold or bronze etc.).
Any advice is appreciated.
Ryan Buckingham- Winnipeg, MB
2000
Hi, Ryan. Please see our
Introduction to Chrome Plating. But since you promised that any advice would be appreciated, I'll give you some: forget it
A budget of several hundred thousands dollars to build a small facility to chrome plate aluminum wheels would constitute operating on a 'shoe string'. Plating of aluminum wheels is something that must be done by major enterprises operating in factories; it cannot be done as a mini-business because of regulatory issues as well as scale.
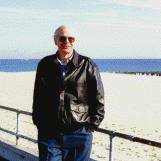
Ted Mooney, P.E.
Striving to live Aloha
finishing.com - Pine Beach, New Jersey
2000
2002
Hello,
My job is aluminum plating (polished plating) . The formula I was using is non- economical due to its primitiveness . In the meantime , my workshop has been semi- closed by the government on account of environmental pollution , and in order to pursue my work, I want to change the plating method and am looking for a new and high - standard formula with minimum or without heat during work . The primitive plating formula I was using is as follows:
Electrolyte composed of phosphoric acid ( 95% ) and nitric acid ( 5%), Which I used to anodize inside a steel tub under 80 °C with 1500 rectifier unit. In the second stage, I used to put the anodized plates in side thermal tub filled with water and crystal color for coloring.
95% + 5%
H2 P04 + HN03 + 80 °C temperature
Phosphoric acid + Nitric acid
The following are the disadvantages of this formula:
1.The ingredients of this formula are costly
2.As a result of heating , the ingredients of the formula vaporize in the air.
3.In case a partial change is brought in the ingredients of this formula ( in the percentage of the materials or the necessary temperature), irreparable damage takes place and as a result the aluminum profile is lost and only the silica under the profile remains.
4.The weight of profile is reduced even under ideal conditions.
5.The plating which is done according to this formula takes place under experimental time ( depending upon the diameter of the stuff of aluminum profile), and since this time is experimental, the changes in the time of taking out the profile from electrolyte solution causes many defects in the quality and brightness of the stuff.
In vies of the above I am in need of the formula recommended by you, in which the electrolyte, percentage of materials, and the time of taking out the profile from inside the electrolyte has to be specified. your formula should not be thermal, as far as possible, and should have the highest quality and brightness. Also, please introduce the type of rectifier which my work under this formula. Awaiting your response.
Thank you very much,
JahangirKhan- Pakistan
Q, A, or Comment on THIS thread -or- Start a NEW Thread