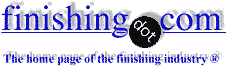
-----
Switching from post-plate to pre-plate
1998Q. My vendor is proposing a cost reduction of ~ $ 8.00 to the power supply Tray used in our unit. This will consist of changing the material from a post-plated material to a pre-plated material.
What difference that will make in term of material quality and performance?
Thanks.
Cliff B [last name deleted for privacy by Editor]A. Hi, Cliff. Normally, the cost advantages of preplating accrue from the fact that the raw material is plated as a continuous strip instead of individual parts which must be jigged. That greatly reduces material handling cost, especially labor cost. The downside is that when you shear pieces out of this, or put holes in it, there will be no plating on the edges.
Whether an unplated steel edge will be a satisfactory finish depends on what metal you are electrodepositing, the environment, and the application. Zinc, for example, is anodic to steel and can galvanically protect those bare cut edges to a good degree; whereas nickel plating is cathodic to steel and the edges will rust aggressively as the exposed steel tries to galvanically protect the plating. Unless you can roll it under to keep it away from the elements, or the environment is benign (indoor, air conditioned) nickel preplate is unlikely to be acceptable.
So, if the trays are zinc plated and will be used indoors, chances for success are very good. Best of luck.
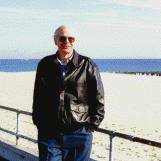
Ted Mooney, P.E.
Striving to live Aloha
finishing.com - Pine Beach, New Jersey
1998
A. Hi Cliff,
It would be extremely helpful to us if you informed us of the materials of construction and the plated materials. In addition to sheared edges, if the material is to be worked in a forming operation the plating may crack and delaminate as well, unless the deposition process has been specifically tuned for a workable deposit. Electronics mfgrs. runs into this as pre-plated IC leads must survive trim & form operations.
Regards,
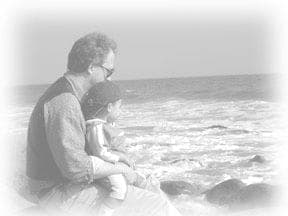
Dave Kinghorn
Chemical Engineer
SUNNYvale, California
1998
We have been stamping pre-plated tin on steel for the consumer electronics industries for years and have never had a problem with cracks or delaminations.
M. DAVID1998
A. I have spoken with mechanical engineers and designing for many electronics OEM's, and there is definitely a trend toward using preplated material. Personal computers and other chassis are now frequently made from preplate; the exposed steel on the sheared edges is not a problem to them. I am talking about companies like HP etc.
Regards,
Pat Kelly- Danboro, Pennsylvania
1998
A. Thanks Pat. The folks above are using preplate, so it can certainly be feasible.
But it still depends on the environment and the plating material. Zinc is sacrificial, and protects steel despite the exposed edges; plus, most personal computers are exposed to very benign environments.
Using a non-sacrificial plating like tin or nickel with exposed edges in a less benign atmosphere is a problem though. As an extreme counter example, I've seen electronic controllers on the plant floor in a plating shop where integrated circuits actually broke off the board (all 16 legs) in under 3 years (that couldn't have been a great environment for people either). The acceptability of preplate and its bare edges is a matter of specific cases.
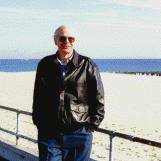
Ted Mooney, P.E.
Striving to live Aloha
finishing.com - Pine Beach, New Jersey
Q. We make switch-mode power supplies for telecommunications and have always used zinc plating with chromate conversion. Recently we have discussed going to pre-plated steel. Does anyone know exactly what kind of pre-plate the Personal Computer manufacturer's are using. From what we can tell it looks like it would do the job for us. Is it as good as zinc chromate for corrosion protection? Any responses would be appreciated.
Thanks,
Peter Stern- Burnaby, BC, Canada
1998
A. I represent the United States largest producer of preplated strip products. We supply a wide range of pre-plated nickel and zinc products into the automotive, electrical, computer, household, and office equipment markets. Not every application can be switched to preplated, but a great deal of them CAN and DO.
Mike Hartmansteel strip - Warren, Ohio
1999
Q. I am investigating the use of pre-tinned amp clips for making an electrical connection. Currently we use post-tinned clips. I have read that often materials are post-tinned to prevent corrosion. Would that be the same reason with CuZn 30? Thank you.
Brandt WillinghamProduct Engineer - Fresno, California
December 18, 2008
Q. My company designs and manufactures electronic equipment for the television broadcast and post production industries. The rack mounted frames I design were once CRS, zinc plated, then masked and painted (powder coat). Since about 7-8 years ago, I heard of more usage with pre-galvanized steel sheet (GalXC from USS Posco in Pittsburgh, CA) from companies like HP and decided to give it a try. We were mainly a domestic company and never saw a problem with the material in the controlled studio environments our products occupy.
But every so often we would have a demo unit come back after much travel mileage and we would see the white rust on the brake marks of bent flanges and even finger prints that white rusted as well. Things got worse with units that traveled internationally, especially Asia. Those units even showed red rust on the exposed sheared edges and punches. Since, our products have gone international and I am obviously concerned with using unfinished pre-zinc plated steel. I have even seen impact to the metal just while sitting in their shipping crates waiting delivery from a shipping dock. As I mentioned before, someone who handled the product with perhaps high acidic sweat(?) on their hand and fingers produced accelerated white rust. I hand delivered 2 frames back to USS Posco to show how extensive these particular units degraded. They sent them away for some chemical analysis and it was determined the white rust, particularly the hand and finger prints, were caused by some form of caustic or acidic substance, perhaps a cleaner of some sort. I am investigating my options, whether it is chromating (trivalent) the GalXC, chromating then powder coat, or go back to CRS and zinc plate after fabrication.
The problem with post zinc is the cosmetic inconsistency. Cost savings dictated the change to GalXC and the alternatives to further protect it will add cost. I would like to hear if anyone is on a reverse decision from using unfinished prezinc steel.
Dan ReiswigMechanical Engineer - Grass Valley, California
February 23, 2010
A. Hi Dan. If powder coating is doable, you might add it to international units. Post plating probably will not match the corrosion resistance of pre-plate plus powder.
Regards,
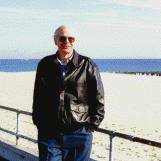
Ted Mooney, P.E.
Striving to live Aloha
finishing.com - Pine Beach, New Jersey
March 17, 2010
A. I've had numerous experiences with conversion from post-plating to pre-plate . . . as an engineering manager at HP and Eaton . . . and as VP/Dir of Engineering at 3 metal fabricating companies . . . now managing projects at a manufacturer of medical products.
Post plating is a big headache to the fabricator. Most have to send parts outside for plating. They have to be counted, packaged, shipped, tracked, expedited, recounted on return, detrashed, and often put back into the production process. Parts get lost and damaged. It is expensive, problem prone, and adds one week to inventories and lead times. Your fabricator does NOT like doing this for you.
In the 1990's, ASTM A591/A591M (now ASTM A879 ) electrogalvanized steel became popular for electronics equipment. It has a very thin zinc coating. The appearance was much better than the "garbage can" look of hot dip galvanized steel.
In recent years, the appearance of ASTM A653 has improved dramatically. It now commonly has a smooth, spangle-free appearance. Its zinc coating is several times the thickness of electrogalvanized, which translates into improved corrosion protection.
Punched and sheared edges will be exposed steel. A small amount of zinc tends to be smeared across the edge. Galvanic action causes zinc to partially protect bare steel in near proximity. Edges may show discoloration (rust) over time, but is usually minimal.
Post plating offers the benefit of depositing zinc on the edges of the part. However, it can bring a host of other problems. Many process variables in the plating process offer opportunities for defects. Plating can look bad or simply peel off. If you can find a good plater with reliable delivery, pay him well.
As a fabricator, I was presented with many designs from high tech customers. Over time I learned that whenever the customer specified Zinc & yellow chromate, it meant the customer had abandoned continuing engineering of the product or was technologically uncompetitive. Zinc & yellow chromate came to mean "old technology" and "dinosaur".
Certainly, your design will be the major factor in deciding how to coat your product. Be very careful that you don't choose post-plating because "that's the way we've always done it." . . . or "our customers expect it." That's not true anymore.
- Watertown, Wisconsin
Thanks for the great update, Mark, you make many excellent and informative points that are very easy to agree with!
The only thing I take issue with is a prejudice against zinc plating plus chromating as a "dinosaur". Cyanide zinc plating is unheard of today, as is ammoniated acid zinc, and there is strong continuing movement to alkaline zinc plating. That means that very few plating shops are using the plating process they were using just a few years ago. And with the impact of RoHS, almost no shop in the world is using the hexavalent chromating technology they were using less than five years ago; they are using thick film trivalent chromates or silane and zirconium topcoats completely unheard of a few years ago -- spanking new plating technology, followed by spanking new conversion coating technology, followed by spanking new top coating technology is hardly "dinosaur" stuff :-)
Rather, zinc plating simply remains the least expensive plating process, yet it offers cathodic protection -- which so few other processes do. So, if the driving force behind the widespread switch to preplating is, as you say, cost reduction, it hardly seems fair to criticize post platers for not moving, for no reason whatsoever, towards a more expensive finish when the finish they are offering is already superior but more expensive than the preplate they are competing against :-)
But, yes, a plating shop which decides to do alloy plating like zinc-cobalt, zinc-iron, zinc-nickel, or tin-zinc rather than plain zinc plating has at least taken a first small step away from the "commodity" market, where they are constantly beat to death by penny-pinching multi-national OEMs; plating shops are almost certainly better off recusing themselves from that market :-)
Thanks and Regards,
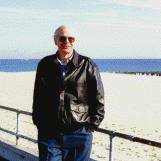
Ted Mooney, P.E.
Striving to live Aloha
finishing.com - Pine Beach, New Jersey
March 17, 2010
RFQ: We are a thermal printer manufacturer. We build desk top printers as well as OEM mechanisms and kiosk mechanisms. We have been using preplated material for years with very good success. We use a galvannealed material that has a higher zinc content.
We would prefer to use what the Japanese use if I could figure it out. It is a lighter gray color and appears to have an anti- fingerprint coating on it. I have been told that this coating is acrylic and increases the shear edge protection. I don't know. I want to be competitive with products from around the world and in order to do so, I want their material.
A. BTW the cost reductions that have been mentioned are conservative.
David Dezse-Lewis Center, Ohio, USA
February 10, 2010
Ed. note: This RFQ is outdated, but technical replies are welcome, and readers are encouraged to post their own RFQs. But no public commercial suggestions please ( huh? why?).
Q. This is a question along the lines of the pre-plate vs. post plate scenario. We know the pre-plate is cost effective but how do they compare in terms of conductivity? Our company is potentially making some changes from post plate to preplate material but I am unaware of the differences in conductivity of the two processes. Am I going to have EMI issues as a result of the switch with everything else being equal?
Corey Brenner- Colorado Springs, Colorado
April 13, 2011
A. Hi Corey. I'm sure the suppliers of pre-plate have had that question before and can address it for the specific material you have in mind. My bet is that there is no difference.
Regards,
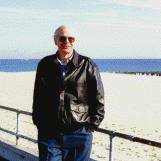
Ted Mooney, P.E.
Striving to live Aloha
finishing.com - Pine Beach, New Jersey
Q.
Dear Sir,
We are using electrogalvanized material for one of our parts.
After the trimming process there will be no coating and we are doing the ultrasonic cleaning after the mechanical process is completed to clean the parts. After a few days slowly it is getting red rust in the edges. Please tell us is there any solution where we can come out of this issue.
Regards
- Bangalore, Karnataka, India
February 12, 2013
A. Hi Kishore,
Two suggestions, firstly cut the parts before electrogalvanising, that way there will be no bare edges after treatment.
Secondly look at the possibility of brush plating (often also called Selectron or Dalic plating, although these are brand names rather than the process) the edges.
Aerospace - Yeovil, Somerset, UK
February 15, 2013
A. Hi Kishore. In addition to Terry's good advice, you might simply make sure that the parts are promptly and thoroughly dried. Additionally, sometimes the most economical solution is to use preplate, but to roll/turn the edges so the bare edge is not visible and exposed. Good luck.
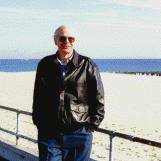
Ted Mooney, P.E.
Striving to live Aloha
finishing.com - Pine Beach, New Jersey
February 15, 2013
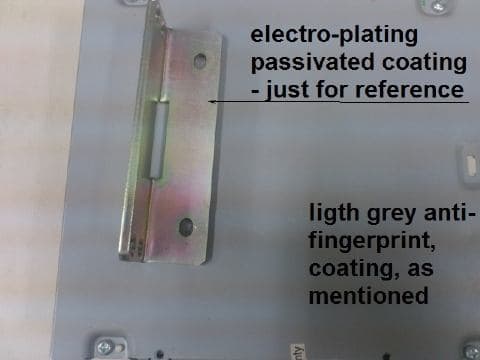
Q. Hi,
I'm looking for a standard of a pre-plate coating that is very commonly used in electronics and PC industries, which a colleague referred as:
That is exactly what I want, but I couldn't find any information (besides your topic) or detailed specification or any Standard (international or not).
Does anyone know a technical specification or standard about that preplate material? If it helps, here is a picture of an example of part with this material.
Thanks in advance.
Ivam AguilaSao Paulo / Brasil
Ed. note: This RFQ is outdated, but technical replies are welcome, and readers are encouraged to post their own RFQs. But no public commercial suggestions please ( huh? why?).
Preplate plus powder coating for high end audio components
Q. Hi,
We are powder coating CRS for very high end audio products, high cosmetic requirements. We are having rust problems with one supplier but not another, identical specs. Callout is for EG CRS for the substrate. One supplier says he can't laser cut EG because of escape gases. True? Also, can the finished part, which is a u-shaped 12G wrap ~ 12"L X 8"W X@.5"H, be EG'ed post machining? Thank you Sir!
- Boulder, Colorado, USA
September 25, 2014
A. Hi Woody. If the vendor doesn't want to laser cut zinc coated steel, that's up to him -- it won't do much good to interject third parties. And as for the differences between the two vendors, that's another thing I can't help you with :-(
I can say, though, that there is no difficulty in zinc electroplating the finished components if you want to go that way. But I can also say that your existing preplate, with a proper pretreatment and proper powder coating should be very highly rust resistant, even with bare edges because powder coating on bare steel can be excellent, and with preplate you're a big step beyond that. Good luck.
Regards,
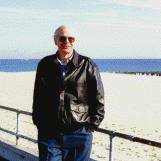
Ted Mooney, P.E.
Striving to live Aloha
finishing.com - Pine Beach, New Jersey
September 2014
Preventing corrosion on edges of preplated material by "smearing" during shearing
Q. I am searching for info about not needing to be touch up edges to prevent corrosion development.
I am looking for an article that had been published about corrosion not developing on thin pre plated material (20 gauge or below) after shearing due to the thickness being so thin, and "a small amount of zinc tends to be smeared across the edge", with "Galvanic action causes zinc to partially protect bare steel in near proximity" .
I would appreciate if I can get this article.
Thanks,
- San Jose, California
August 6, 2015
Q, A, or Comment on THIS thread -or- Start a NEW Thread