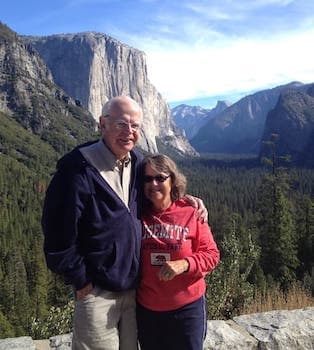
Curated with aloha by
Ted Mooney, P.E. RET
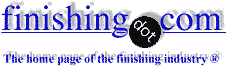
The authoritative public forum
for Metal Finishing 1989-2025
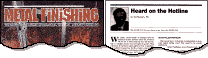
-----
Non-cyanide Copper Plating
Quickstart:
The simplest copper plating solution is acid copper sulfate; we have many threads about it. But it has a very serious limitation: in general, it can't be used on steel & iron because it spontaneously "immersion deposits", meaning the copper steals electrons from the steel, causing some steel to go into solution and copper to plate out. The adhesion is poor, and can be visualized as the surface you are trying to adhere to is dissolving.
The traditional way to do copper plating on steel was to use cyanide-based chemistry, but cyanide plating is declining in popularity because it is poisonous and heavily regulated. Alternatives include pyrophosphate copper, proprietary alkaline formulations, or nickel plating the steel before doing copper plating.
Q. Hello Everyone,
I want to set up Acid Tin plant for brass components (barrel). I need to do copper flash up to 3 microns for barrier. I want to set up Cyanide-Free Alkaline Copper Plating bath, is it suitable for Brass components? Or is cyanide plating the only option? Please suggest.
Thanks,
Shop Employee - India
January 1, 2025
Tip: This forum was established to build camaraderie among enthusiasts through sharing tips, opinions, pics & personality.
The curator & some readers who publicly share their info will be less likely to engage with those who don't.
A. Hi Sam
I wouldn't wander out on my own with a home-brew, but I don't think there is any reason a proprietary non-cyanide alkaline copper would work. There are also proprietary nickel strikes for brass if nickel isn't objectionable for some reason.
Luck & Regards,
Ted Mooney, P.E. RET
Striving to live Aloha
finishing.com - Pine Beach, New Jersey
⇩ Related postings, oldest first ⇩
Q. Hi, Does anyone have any experience with using EPI / Electrochemical Products Inc. [a finishing.com supporting advertiser] 30/30 non-cyanide copper solution to plate small, white metal (tin-lead alloys and zinc) castings in barrels or on racks?Thanks
Ken F1997
Tip: This forum was established to build camaraderie among enthusiasts through sharing tips, opinions, pics & personality.
The curator & some readers who publicly share their info will be less likely to engage with those who don't.
A. I think that alkaline non cyanide copper operates only on steel and not on zinc castings.


Sara Michaeli
Tel-Aviv-Yafo, Israel
A. Ken, I'll have to disagree with the people who indiscriminately knock all non-cyanide copper processes. I have experience with the EPI / Electrochemical Products Inc. [a finishing.com supporting advertiser] E-Brite 20/20, the predecessor of the 30/30 bath. It did all the things the manufacturers claimed and then some - I successfully electroformed with it. The bath operates at a pH of (if memory serves) around 9.5, has great adhesion to steel, nickel, etc. you can plate out of it directly onto aluminum (naturally, no adhesion unless you zincate, but who cares when all you want is to electroform). I know people who use the 30/30 bath and are quite happy with it.
Hope this helps.
Wishing you luck, PlaterB
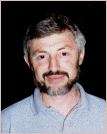

"PlaterB" Berl Stein
NiCoForm, Inc.

Rochester, New York
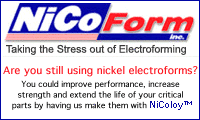
? Just out of curiosity, are you using an Acid Cu bath or are you using Cu Pyrophosphate? I know Cu Pyro has excellent throwing power but, I've only used it on Wire helices. I'm not sure about SnPb or Zn.
I will do some research and see what I can come up with.
Laura FatkeKen,
I use EPI 30/30 alkaline copper strike.
Works good but you have to keep ph within range. If you cannot maintain pH it causes copper anodes to polarize and stop plating.
Electroplating Consultant - Sterling Heights
March 5, 2025
Multiple threads merged: please forgive chronology errors and repetition 🙂
Non-cyanide copper plating thickness limit
⇦ Tip: Readers want to learn from Your Situation 🙂
many readers skip abstract questions.
Q. What is the practical upper thickness limit for a functional copper plating on mild steel using a non-cyanide process?
Kirk Cooper- Sidney, Ohio
2003
A. Hi, Kirk. Copper electroforms have been built at least 1/4" thick, maybe more. So the answer is that there is probably no realistic upper thickness limit to copper plating. If you pose the details of your own situation we can surely help further. Good luck!
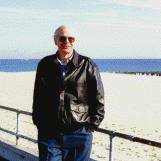
Ted Mooney, P.E.
Striving to live Aloha
finishing.com - Pine Beach, New Jersey
A. Ted is correct. The question is so broad. When you say non-cyanide, you open the door to several chemistries (sulphate, pyrophosphate, fluoborate). Of those, the one most used to develop thick plates is the sulphate. A practical limit could be how much roughness can be tolerated on the outer surface. Without additives, which tend to increase stress and can lead to cracks, thus limiting thickness, 1/8" can be done with no more roughness than a piece of coarse emery paper. Beyond that, you can go up and end with something that resembles a coral or a sponge.
Guillermo MarrufoMonterrey, NL, Mexico
Q. The key to my question is non-cyanide plating. For a commercial plater, plating a steel part which will be torch-brazed, what is the thickest copper plate you would feel comfortable putting on using a non-cyanide process?
Kirk Cooper [returning]- Sidney, Ohio
by N. Kanani
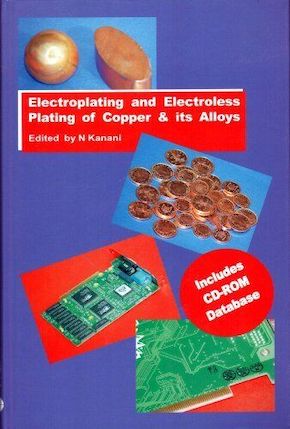
on AbeBooks or
eBay or
Amazon
(affil links)
A. Please tell us what you are trying to do, Kirk.
Can you start with copper pyrophosphate then finish with bright acid copper? Can you buff mid-process to smooth it back up. Do you need 1/4" thick, or is 1/8" enough ... or would you be satisfied to reach 10% of that?
An often-used approach is to nickel plate first, then you can directly plate a simple copper sulphate ⇦ this on eBay or Amazon [affil links] solution very very thick. Is a nickel strike objectionable in your application for any reason?
I guess I'm just saying that I'd prefer if your inquiry could start: "Here's what I am trying to do: ..." :-)
Good luck and thanks for your patience.
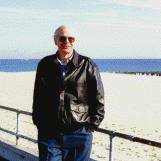
Ted Mooney, P.E.
Striving to live Aloha
finishing.com - Pine Beach, New Jersey
Q. OK - I consider myself sufficiently chastised for lack of detail :-) Here's what I am trying to accomplish: copper plate a mild steel part which will later be brazed to another part. For environmental and process flexibility reasons, I desire to minimize or eliminate use of cyanide in the strike or the plating bath. Desired plating thickness ranges up to 0.002". Aesthetic function of the plating is secondary, but it should have a surface finish (Ra) not exceeding 0.0005". Brightness is not critical, but consistency of appearance is. Hardness should be similar to that of a cyanide-based process. Thank you.
Kirk Cooper [returning]- Sidney, Ohio
A. Apologies, Kirk! It isn't our intention to hassle, just to say that the more detail provided, the more helpful the readers are usually able to be.
You may already realize that acid copper cannot be deposited directly onto steel surfaces because it will "immersion deposit" and offer virtually no adhesion (it won't survive brazing). If you can't use a cyanide strike, you would need to try either a pyrophosphate copper strike or a nickel strike.
Then you can finish with an acid copper (sulphate or fluoborate). I don't think .002" is a technological hurdle at all as, when I was involved in the stripping of the copper from the William Penn city hall tower in Philly, we discovered that they had plated copper at least 20 times that thick a hundred years ago.
It should be possible to directly plate .002" of a pyrophosphate or other copper in a single step. I don't know enough about it to comment, but Berl Stein has done electroforming with it; you could inquire of a supplier of that process like EPI / Electrochemical Products Inc. [a finishing.com supporting advertiser]. But a nickel strike followed by acid copper would work fine too. Best of luck with it!
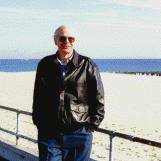
Ted Mooney, P.E.
Striving to live Aloha
finishing.com - Pine Beach, New Jersey
Analysis of alkaline non-cyanide copper bath
Q. Dear all,
We are doing alkaline non-cyanide copper plating and would like to know the correct method to analyze the copper content by means of titration. Copper content in bath ranges from 8 - 12 g/L.
Can anybody suggest ?
Thanks,
Simon LiSky Chemicals Limited - Kwai Chung, NT, Hong Kong
2004
A. Hello.
ANALYSIS OF COPPER --
REAGENTS: Ammonium persulphate, concentrated ammonia ⇦ this on eBay or Amazon [affil links] solution, PAN-indicator (1-(2-pyridylazo)-2-naphthol, 1 gr/l ethanol
PROCESS: pipette [pipettes on eBay or Amazon [affil links] 5 ml bath solution into a 250 ml Erlenmeyer beaker, add approx. 25 ml deionised water and 2-3 gr ammonium persulphate. Stir the solution for about 15 min. Add 5 ml of the concentrated ammonia solution; the colour turns to dark blue. Add another 50 ml deionised water and 4-6 drops of the indicator(don't add more. The changing of the colour will be worse). Titrate with 0,1 N E.D.T.A from dark blue to greenish-grey
CALCULATION:Consumption in ml * 1,27 :...gr/l Cu
By the way... How is your bath (performance)? And is it difficult to control? And have contamination problem? And can you plate zamac (zinc die castings)?
Could you answer these questions?
Good luck.
Emre Tuna- Turkey
Non-Cyanide Copper Plating of 14 ga Mild steel art work
Q. I visited a job shop that makes ornamental parts. You have seen them - the little garden animals and things like lizards and kokopelli's, etc. They currently use copper plating and then coat with a clear coat to preserve. I wonder if a non-cyanide process for plating 14 ga mild steel and then clear coating would work - do you see any problems? What other treatments can be applied to the plated parts to impart color changes such as darkening, aging and various antiquing finishes? Trying to stay environmental friendly from a simplicity in process and regulation perspective.
John Moritzequipment sales - Vancouver, Washington, USA
2004
A. The typical acid copper baths (copper sulphate or copper fluoborate) cannot be applied directly to steel because they won't adhere, for reasons more complicated that you probably are interested in hearing in the first round. There are copper pyrophosphate and other proprietary baths available from several suppliers; these are a bit more finicky than cyanide baths, and I can't guarantee they will discolor with heat in the same way, but they are worth investigating.
Another alternative is to nickel plate first, then acid copper plate. Again, whether this will aesthetically discolor exactly the same way as cyanide copper would need to be determined.
by Hughes & Rowe
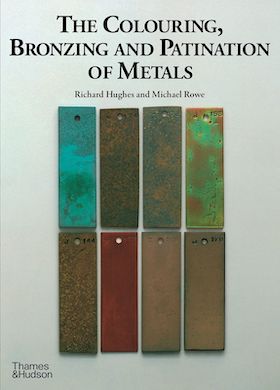
on eBay or
AbeBooks
or Amazon
(affil links)
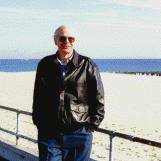
Ted Mooney, P.E.
Striving to live Aloha
finishing.com - Pine Beach, New Jersey
A. There are lacquers from companies like Agate that have some fantastic metal-like colors without the evils of plating. Check with them for the level of UV stabilization that the have/need.
You might also acquire the book on patinas in the book section at this site (not that bad priced and lots of pictures). Sort of a minimum library for an artist ⇨
- Navarre, Florida
Q. I am trying to electroplate mild steel with copper for an art project. I managed to get a little of the copper to plate but it seems that the dark "coating" on the steel prevents the copper from bonding easily and it just wipes off.
Is there a way to purchase sheets of steel, up to 16 x 20 inches, that does not have this "coating"? Is there a way, other than grinding, to get it off?
- Roslyn, South Dakota, USA
January 11, 2013
A. I think that when you say dark coating, you are referring to the mill scale on the steel. You can avoid this by buying cold rolled steel rather than hot rolled steel. Alternatively, you can remove the scale by sand blasting, grinding or with a solution of sodium bisulfide and water. You will find this acid salt sold as a pool additive (lowers pH).
Justin Kumph- Philadelphia, Pennsylvania
Q. I am trying to plate alkaline non cyanide followed by Acid copper and bright Nickel.
But after heating at 130 °C for 30 min. it is getting blisters at LCD areas.
What may be the probable cause as in alkaline cu the thickness is 10 to 15 micron?
Akhilesh
Electroplater - Ludhiana, Punjab, India
May 8, 2018
A. Hi Akhilesh,
Please clarify if blistering happens between base substrate and alkaline non cyanide Cu or alkaline non cyanide Cu and acid Cu or acid Cu and bright Ni deposit.
Possible cause could be improper activation of base substrate prior electroplating or Cu oxidation prior following plating or poor Ni deposit ductility.
Regards,
David
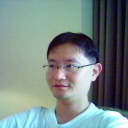
David Shiu
- Singapore
Q. Hi Shiu,
It is from base to alkaline copper layer.
The substrate is Zinc Diecast and the activation is 2% HF solution for 20 seconds.
The blister is coming only after heating the substrate up to 130 °C.
Akhilesh.
Electroplater - Ludhiana,Punjab, India
May 10, 2018
A. Hi Akhilesh,
You may prolong zinc die-cast activation (or even with electrolytic activation) or plate cyanide Cu strike to improve adhesion.
Also, you may remove organic or metallic impurities from alkaline non cyanide Cu bath to minimize blistering at LCD area upon baking.
Regards,
David
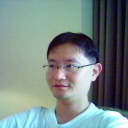
David Shiu
- Singapore
Thanks, Shiu.
- Ludhiana,Punjab, India
Step by step plating guide for novice
Q. I was thinking of plating some mild steel barrel bands (gun parts). How would one start and is there a step by step guide to this for the Novice?
Devlin English- Floral City, Florida
February 14, 2019
A. Hi Devlin. You might google for "hobby plating supplier" and see if they have a booklet for you or an instruction manual you can buy. But as we've all learned from trying to follow even the simplest step by step assembly instructions for a table or a child's toy, the vocabulary can kill you.
sometimes on
AbeBooks or Amazon
(affil links)
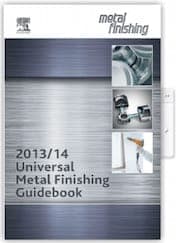
free pdf is currently available from academia.edu
Electroplating instructions will talk about rectifiers and anodes and cathodes and electrolytes and bus bar and addition agents, and so on, making "step by step" difficult, so it may be best to read a couple of our introductory papers here to learn the lingo. Our "How Plating Works" is for elementary school kids; "Faraday's Law" moves on to high school level; and "Intro to Chrome Plating" addresses practical real-world issues. Spend 20 or 30 minutes on those three and I think you'll be ready to ask step by step questions or consult stuff like the Metal Finishing Guidebook .
without getting quickly lost :-) Good luck.
Regards,
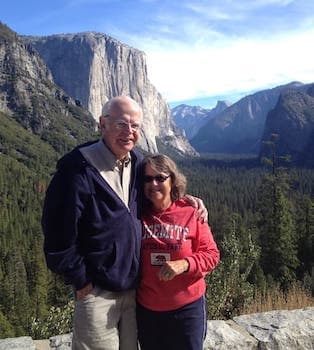
Ted Mooney, P.E. RET
Striving to live Aloha
finishing.com - Pine Beach, New Jersey
Thank you Ted Mooney. I hope you make the North Shore. I will follow the path and get back with you soon with a Blue Million Questions.
Thanks,
Devlin
- Floral City, Florida
Q. Ted Mooney
My Cathode(s) can or should I hang them from copper or stainless or titanium? Table II on page 271 seems to be the most effective and the most pain to dispose of... I like the life and Integrity of Cyanide but not so much the risk and by-product. So what about the EPI / Electrochemical Products Inc. [a finishing.com supporting advertiser] line of products? Any ideas, are they "User friendly"? Single container and all that sounds great and great price point on the 30/30. But how do they perform as durability, is it Cu? Will it ox up and get that patina?
You're the literate one in this, I'm the dummy
Devlin
- Floral City
A. Hi Devlin. You should use copper wire to hang the parts.
Whatever workable copper plating solution you use, I think you will get a plating of good copper metal and that it will patina.
The basic issue is that it isn't possible to electroplate steel from a simple acid copper plating solution because it will have no adhesion (copper is more noble than iron and will deposit on it spontaneously with no electricity, as in the high school chemistry experiment of watching iron nails get covered with copper by simply immersing them in a blue copper sulphate solution), so ...
To usefully electroplate steel with copper you need to either electroplate the steel with nickel first, or you need to use a copper plating solution which complexes (ties up) the copper so it cannot spontaneously deposit. Cyanide copper plating (very dangerous) is the most popular method for industrialists, copper pyrophosphate plating is another industrial method but hard to control without a good lab, and proprietary solutions like the EPI / Electrochemical Products Inc. [a finishing.com supporting advertiser] solutions are another.
I personally don't think electroplating is a great hobby, because it can be dangerous & expensive, the results are likely to be poor, and there is much to be learned before you can generalize (employ what you've learned to somewhat different situations) -- but some people apparently enjoy it as a hobby, especially if limited to a narrow field like plating or electroforming jewelry :-)
Regards,
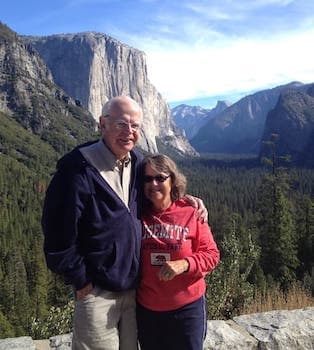
Ted Mooney, P.E. RET
Striving to live Aloha
finishing.com - Pine Beach, New Jersey
Q. Thanks Again Ted, such a Huge Help. I didn't mean to sound obtuse. I have adjustable amp power supplies. I wouldn't try to do this without the benefit of electricity. It was the formulation you see. That's all in the past as it were. I've a more "techie" question on mix calculations:
1.5 gallon Glass lab jar 84 oz 30/30 16.8 30/31 67.2 H2O is there anything I've missed in the mix? 120 °F (hotplate) air agitation, 3.5amps, 4.3 minutes. .02 in 6.3 oz parts on Cu wires / 9.5 oz Cu wire pieces in Ti basket. Anything I missed?
Do the parts need to be "in the white" as in Bluing-free or can I copper over the Bluing as it is a Salt Acid process?
Devlin English [returning]- Floral City, Florida
A. Hi Devlin. When you're using a proprietary like this one, people don't actually know what is in the formulation; you have to follow the technical data sheet from the supplier. I know that's tricky because you're not going to be obeying the letter of the law regarding anode material, etc., and I doubt that EPI / Electrochemical Products Inc. [a finishing.com supporting advertiser] will be periodically analyzing the solution for you ... so you might consider getting a Hull Cell so you can really see what's going on with the bath.
You cannot copper plate over the bluing because the plating must build onto the substrate metal, not onto oxides. I think the best option for hobbyists is to nickel strike first, then acid copper plate.
Regards,
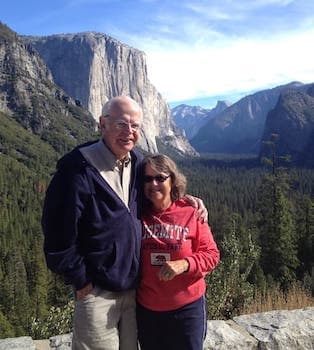
Ted Mooney, P.E. RET
Striving to live Aloha
finishing.com - Pine Beach, New Jersey
Q. Sir our requirement is copper plating more than 250 microns on MS strip and rod. Is it possible to get this thickness in cyanide-free alkaline plating?
chhavi ram- Delhi, India
December 16, 2019
A. Hi Chhavi,
We appended your question to a page where the subject has been discussed with a lot of "ifs, ands, & buts". The usual approach to copper plating on steel is to strike with copper cyanide, copper alkaline non-cyanide, or nickel first -- and then to do the bulk of the copper plating with acid copper plating. But Berl says this thickness is no problem for a proprietary alkaline non-cyanide plating bath, and when Berl says something can be done it's invariably because he's personally done it.
Regards,
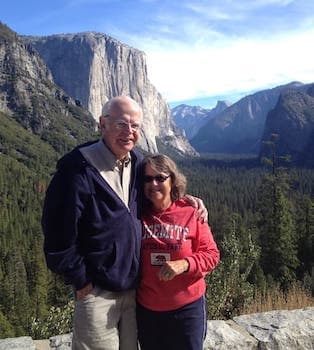
Ted Mooney, P.E. RET
Striving to live Aloha
finishing.com - Pine Beach, New Jersey
Q. Hello all;
I have over 40 yrs. in the finishing industry, but have been retired for over 10 years. In my time, cyanide Cu strike was the generally-used starting point for many finishes and treatments. I am looking for a non-cyanide strike suitable for hobbyist use for (non-exclusive list) multiple base metals: steel, aluminum, zinc die castings, bronze and brass -- with the intent of building thickness and other properties with Cu sulphate for restoration purposes. For multiple reasons, I wish to avoid using Ni. Have never used alkaline Cu for this (or any other) purpose. Is this a suitable starting point for plating the above-mentioned metals? Thank you.
- Chandler, Arizona USA
June 2, 2020
A. Hi Patrick. Absolutely.
But newbies reading this may not recognize some things which you do, like the need for proper pretreatment, and the fact that it is not possible to do alkaline copper plating (or most other platings) directly on aluminum, stainless steel, or titanium.
Regards,
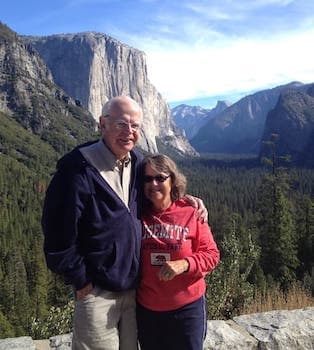
Ted Mooney, P.E. RET
Striving to live Aloha
finishing.com - Pine Beach, New Jersey
A. Yes it is certainly possible to deposit copper at 250 microns. The most common non-cyanide bath is sulphate based and this can easily produce good deposits up to 1.25 mm thick; after that, it may become a bit nodular and even stressed. You can also use Periodic Reversal pulse plating, which will give even better deposits. Other non-cyanide baths include pyrophosphate and fluoborate; I would avoid the latter as it is very corrosive and toxic, so stick to the simple solutions - copper sulphate based systems.
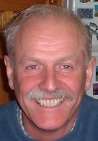
Trevor Crichton
R&D practical scientist
Chesham, Bucks, UK
Q. Hello all.
I was introduced to pyrophosphate copper in approximately 1970, using it as a "shield" for selective heat treatment. By '76 or so, I had also used it extensively for mfg. of printed circuits. I never used it afterwards, but at the time, I was not aware of any pyro Cu strike formulations. As a matter of fact, I often had it "drummed into me" that you couldn't plate w/ pyro directly onto steel (didn't stop me from trying; got a brush version of my own concoction working nicely in about '71 or '72) after my brother became a "certified" Selectron plater & taught me a few tricks. I looked into the '89 ed., the earliest version of the MFG&D on my bookshelf (w/o searching extensively in my "archives" (read garage) and did indeed find a strike formulation. No specific interest, but curiosity: when did this type of strike for steel become common? Was I simply uninformed/ignorant? Like I said; just curiosity.
Thanks
- Chandler, Arizona USA
A. Hi Patrick. Your history is probably right. I was working for M&T Chemicals in the early 1970's, and we were using our pyrophosphate copper in several large printed circuit shops. I was a newbie plating equipment engineer at the time, not actually involved in the chemistry, but I did know that it was our proprietary pyro.
We also did a large copper plating installation for a well-known manufacturer of oil well drilling tools for selective hardening like you mentioned -- we copper plated the steel drill bits for selective carburizing. I would assume it was our proprietary copper pyro, but unfortunately I can't actually remember for sure :-(
Luck & Regards,
Ted Mooney, P.E. RET
Striving to live Aloha
finishing.com - Pine Beach, New Jersey
Q. We are doing non-cyanide based alkaline copper plating 3-4 microns on steel components.
We find the blackish appearance of copper plating observed with loss of adhesion.
The plating is immediately removed by rubbing with fingers in wet stage.
It is kindly requested to suggest remedy.
- Nagpur, India
April 12, 2022
Q. Hi pankaj,
Did you solve your problem? Please share this -- same problem at my plant.
- KANPUR
February 5, 2023
A. Hi Amit. Everything must be right at every step for adherent plating, of course. Unfortunately, that means that something wrong at ANY step can result in non-adherent plating :-(
I would suggest scrubbing a few parts with pumice, as well as looking for water break on all of the parts, to assure yourself that the parts are properly clean. Also, plate some steel Hull Cell panels to determine whether the problem is within the plating step itself.
Luck & Regards,
Ted Mooney, P.E. RET
Striving to live Aloha
finishing.com - Pine Beach, New Jersey
Q, A, or Comment on THIS thread -or- Start a NEW Thread