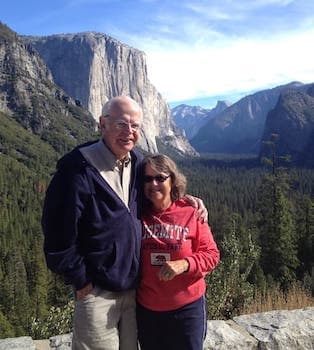
Curated with aloha by
Ted Mooney, P.E. RET
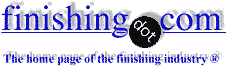
The authoritative public forum
for Metal Finishing 1989-2025
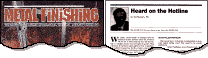
-----
A solution to a Stainless Steel Passivation problem
In Vol. 95 No.2, Feb. 1997 of Metal Finishing Anne Baic reported a problem found while attempting to passivate stainless steel. Other contributors concurred that they had experienced problems too, even with different types of stainless steel...
A. Reading the articles brought vivid memories of the same problem. I am the plating chemist at Robertshaw Controls. We were passivating 400 series SS that had been machined on a high speed lathe. The plating technicians had brought the problem to my attention and I tried all the standard investigations; temperature, concentrations, alloy check, impurity and cleanliness check, nothing explained the seemingly randomness of the vicious acid attack.
I am also responsible for Pickling operations and general metallurgy so I'm very experienced with the nature of acid reactions, and I have an extremely talented co-worker Reggie B. that knows machinability properties of stainless steels. He gave me the clue to solving this puzzle. I asked him what could be the difference between the good and bad sets of parts. He almost immediately suggested that grain structure, hardness, and surface profiles could be affected by the quality of the machine setup, the amount and the effectiveness of the cutting oil coolant, and the amount of wear on the cutting tools. Reggie explained that the part can get very hot and change hardness or in the case of a dull tool with plenty of cutting oil coolant,the surface can distort and the tool drags metal off instead of cutting it, thereby creating a distorted finish. I went to investigate the difference between different machines and took samples to test for microhardness and grain changes. In the MET lab I found no telltale hardness changes, but I noticed that the sectioned metal was hard to etch, I had to use a powerful etchant that is common to most metallurgists, a nitric - alcohol etch. The nitric acid by itself wouldn't etch the SS in a hundred years but I knew that the addition of a drop of alcohol, glycerol, or OIL would create a Organic acid that dissolve the part in seconds if allowed to remain in contact. - aha! The etchant reacted in the same way as the parts that were attacked by the 50-2-48 Nitric-Bichromate Solution. I took a sample of the cutting oil and mixed a drop of it with the passivation solution in a beaker [beakers on eBay or Amazon [affil links] at room temperature. The metal reacted vigorously, - all pieces, not just the problem lots. Thus I had a good clue as to the culprit - but still had one problem. The parts didn't look or feel oily, and they are alkaline washed just before the passivation process. I inspected the surface of the problem parts under the electron microscope and I found a very rough pitted surface, enough pores to cause a great problem in cleaning. The dull tool had not burnt or hardened the part but cutting oil was being trapped in the pores and being sealed into the surface.
I found that the length of time in the alkaline degreaser and vapor degreaser was proportional to the percent of good passivation lots. With a vapor degrease and a hot 4 hour alkaline soak we were able to save all of the lots, albeit this much time and effort was costly. The only real solution was to maintain tighter machining control and to change out tool bits more often. Reggie insists that the Tool bit regrinds helped contribute to the problem too.
What an interesting challenge!
Mitchell G. Lee- Friendsville, Tennessee
1998
Mitchell,
Thanks for sharing your knowledge with the rest of us. Most of us do not have the toys to do the level of checking that you did. It surely agrees with the experience (bad) that I have had. Jim
James Watts- Navarre, Florida
1997
! Just a brief comment...
DON'T try mixing alcohols (or any other organic chemicals) with concentrated nitric acid. You can generate potentially explosive mixtures - which may not react immediately.
Tony Fulford- Reading, U.K.
1998
1997
A. The passivity of stainless steels is attributable to a strongly adsorbed layer of oxygen. Sulfides (and probably Selenides) in acid media are even more strongly adsorbed, and destroy passivity by displacement of adsorbed oxygen. In the manufacture of TiO(2) by the sulphate process, I have observed that the presence of sulfide, in low ppm concentrations, causes activation and severe corrosion of SS316 in titanium/iron sulphate solution in which the alloy is normally completely passive.
A more curious example of this effect is a commercial household device which appears to remove the odor of onions and garlic from the hands. It consists of a stainless steel block shaped and used like a bar of soap.
Free-machining grades of stainless may respond more favorably to the alkaline-acid-alkaline procedure described in the ASM Metals Handbook Vol. 13 'CORROSION' ⇦[this on Amazon affil links] p 552, as follows:
1) After degreasing, soak the parts for 30 minutes in 5% wt of sodium hydroxide (NaOH) at 70-80 °C (160-180 d°F).
2) Water rinse.
3) Immerse the part for 30 minutes in 20 vol % HNO(3) + 22 gpl (3 oz/gal) Na2Cr2O7. 2H2O at 50-60 °C (120-140 °F).
4) Water rinse.
5) Immerse for 30 minutes in 5 wt % NaOH at 70-80 °C (160-180 °F).
6) Water rinse.
Free machining grades should not be used in acidic environments without thorough testing, due to the internal passivity - destroying effects of sulfur or selenium.
Very truly yours,
David HawkeQ. Found the article very interesting. Would have liked to hear Lee's opinion on recycling pickling waste from stainless steel industries, where companies like my own can perhaps some day work with an enterprise that utilizes the acid waste by removing the iron oxides. Please respond if you have any ideas or knowledge of such a practice.
Thank you.
Victoria L. Smith- Washington, Pennsylvania
1998
Hi Victoria. You might want to work with a company to try to recycle your waste so that you can use it again yourself, but the era of industrial waste exchanges is essentially over. Cradle-to-grave legislation has had the unintended consequence that no one will touch anyone else's waste products with a ten foot pole.
Regards,
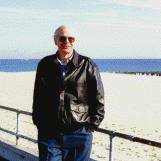
Ted Mooney, P.E.
Striving to live Aloha
finishing.com - Pine Beach, New Jersey
Q. We are considering the possibility of utilizing citric acid as an alternate passivation solution. Anyone who can share supporting references would be greatly appreciated.
Best Regards,
Stanley J. Oakley1998
Q. Due to the cancellation of QQ-P-35C (canceled) [link is to free spec at Defense Logistics Agency, dla.mil], our company is evaluating the proposed citric acid treatments in ASTM A967. Has anybody had any success with citric acid ? We have tested several coupons, and have not been able to produce any successful results.
Best Regards,
Jennifer GiedeA. I haven't used it myself, but Stellar Solutions [a finishing.com supporting advertiser] offers their Citrisurf brand of proprietary citric acid passivation solutions.
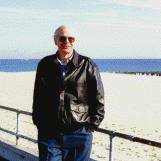
Ted Mooney, P.E.
Striving to live Aloha
finishing.com - Pine Beach, New Jersey
1998
Q. I am seeking information on maintaining corrosion resistance of 316 alloy after welding. The procedures that I have on hand are AISI booklets dated prior to 1980. Perhaps more recent information is available? My research indicates that electrode alloy 316LSi is recommended for welding 316 (from B & R Welder Repair Service, Inc.). Our stainless steel products are immersed in plain (tap) water for use, over a period of years.
The information on this web page has also been of great value to me. RSVP someone.
Paul K. Monaghan1998
Q. I need info about passivation and relative corrosion of 304 Stainless Steel in trimetylborate and pceudocumene.
I appreciate any help, thanks!
Laura Perasso- Genova, Italy
1998
Mr. Monaghan, Ms. Perasso:
I'd be happy to help you if I could, as would many of our readers. But specialized data of this sort tends to not be information that you will find on the web for free. If you don't get any good responses here, my suggestion would be to contact ASM-International (www.asm-intl.org) who have thousands of specialized texts available on corrosion subjects. Good luck.
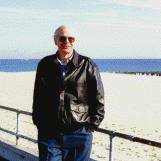
Ted Mooney, P.E.
Striving to live Aloha
finishing.com - Pine Beach, New Jersey
1998
The Importance of Chemical Treatment Associated with the Welding of Stainless Steel and Aluminium
Presented to the Philippine Welding Society, 11th October 1997 by John W. Hill BA (Chem) General Manager Specialty Products, Callington Haven Pty Ltd, Sydney, Australia.
1. INTRODUCTION
Stainless steel has found widespread applications in industry in areas such as process plant and equipment, building facades, railing, storage tanks and piping in food and pharmaceutical factories, and many others.
Stainless steel is often perceived as being resistant to corrosion, relatively inert and requiring minimal treatment in fabrication, and little maintenance.
The term passivity refers to the natural corrosion resistant property of many metals and alloys including chromium, titanium and stainless steels.
Passivity is conferred on stainless steel by an invisible nanometre thick film of chrome oxide. The stability of this film depends largely on the corrosive environment in which the stainless steel is found.
In a clean environment the passive film forms spontaneously following its removal over a period of at least 8 to 24 hours. This means that stainless steels are self passivating "under favourable conditions".
Disruption of the passive film by chemicals, mechanical action, embedded iron particles, or oxygen starvation can readily occur in the workshop or during fabrication. Surface free iron particles, dust, grit and iron oxide contaminants arise from handling, fabrication/forming, welding, grinding, machining, paint and crayon marks, polishing, tumbling and workshop cross contamination.
These contaminants penetrate the passive film, absorb and generate chlorides, ferric chloride ⇦ this on eBay or Amazon [affil links] or produce inorganic chlorides by the decomposition of organic compounds such as PVC and marking materials.
Chemical treatment of stainless steel is important to maximise product quality in all stages of the fabrication life cycle, from initial cleaning, to spatter protection, pickling, passivation, waste treatment and final cleaning of the finished product.
Aluminium also requires specific chemical treatment prior to welding, following welding to remove weld scale and burn marks, spatter protection and final surface cleaning of the finished product if required.
2. STAINLESS STEEL CLEANING PROCESSES
All stages of the fabrication life cycle of stainless steel require specific chemical cleaning treatment. These include :
- surface preparation, cleaning and / or degreasing
- weld spatter protection
- descaling / pickling
- passivation
- treatment of acidic waste for trade waste compliance
- cleaning of finished product
- deoxidising of surface corrosion for maintenance
Chemical treatment agents for the stainless steel fabricator
- solvent degreaser / cleaner
- anti spatter spray
- pickling solution or paste
- passivating solution or paste
- neutralising solution for waste acid treatment
Solvent cleaners
Traditionally, readily available and low cost petroleum based products such as white spirits, kerosene, thinners or chlorinated solvents have been routinely used for surface cleaning and degreasing.
In many countries today, occupational health and safety and environmental regulations have focused attention on safer non toxic and biodegradable alternatives to these flammable and/or toxic chemicals.
Solvents are generally preferred over water based detergents in order to minimise the presence of water which may aid corrosion in some cases, especially when held in crevices and corners.
Typical applications can include removal of adhesive protective laminates, finger prints, permanent marker pen or crayon marks and machine oil.
Anti Spatter Chemicals
Welding of metals often results in molten spatter falling on the surface of the steel being welded. This spatter solidifies leaving hard lumps which can only be removed by abrasion or polishing.
Mechanical treatment of the spatter deposits is time consuming and can be avoided by the use of special anti spatter sprays.
Solvent based products are preferred for stainless steel, while water based products are now emerging for treatment of mild steel.
Pickling solutions and pastes
Pickling is the removal of the oxide film from the surface of the metal by chemical means. An exposure to high temperature (e.g. during welding or heat treatment) will scale the surface. In the case of stainless steel, such high temperature scale has inferior corrosion resistance and must be removed. Pickling using formulations of hydrofluoric (HF) and nitric (HNO3) acids, removes the scale and helps to restore corrosion resistance through auto passivation providing the ambient conditions are appropriate. For applications in aggressive environments, it is advisable to develop full corrosion resistance by a passivation treatment subsequent to pickling operation.
Pickling agents can be sprayed over an entire surface, used in dip applications or as a paste applied to the weld and heat affected zone.
Pickling of stainless steel welds helps to remove both the oxide scale and free iron contamination. Once the pickling paste is completely rinsed away, the treated area will be chemically clean. As such, the surface has an enhanced ability to react with atmospheric oxygen to spontaneously passivate, providing the area is free from dirt and outside sources of contamination
Where the aesthetic appearance of the stainless steel is important, the pickling process will remove unsightly discoloration, leaving a clean professional finish.
Why passivate?
The failure of stainless components due to corrosion can reach catastrophic proportions. The cost in time, materials, rectification and lost production can be tremendous.
If passivation is not carried out stainless steel can rust due to surface free iron, and since chlorides are also often absorbed from the atmosphere, some ferric chloride ⇦ this on eBay or Amazon [affil links] will be produced.
Prolonged contact with ferric chloride ⇦ this on eBay or Amazon [affil links] will eventually initiate pitting and crevice corrosion on the stainless steel surface.
Therefore, proper passivation with a nitric acid based agent will dissolve the surface contamination and assist in the optimal restoration of the chrome oxide passive layer.
It should be understood that this passive surface condition is not a static situation. The chrome oxide layer is constantly affected by the environment and is slowly lost, but at the same time it reacts with oxygen to reform. The process is in dynamic equilibrium. Only when the balance is brought towards loss of the passive film does corrosion occur.
Passivating Solutions and Pastes
Pickling not only removes the scale around the heat affected area, but it also removes chrome oxide and surface iron and metal contamination, and therefore leaves the surface of the steel readily available to react with atmospheric oxygen to restore the passive field (i.e. auto passivation).
The passive film restoration is dependent on the availability of oxygen for its formation, and also subject to inhibition by atmospheric pollution, airborne chlorides (present as sodium chloride - NaCl - especially near coastal areas) and the presence of mild steel in the same workshop if not strictly controlled.
Where the chromium content is in excess of 12.0%, the formation of a chromium oxide passive film on the surface is possible either through auto-passivation or enhanced passivation with nitric acid.
Enhanced passivation with a nitric acid based passivating agent is recommended following grinding, pickling or polishing of stainless steel where the surface has been made more active by these processes. The passivating agent enhances the passivation process in a more uniform manner to restore the chrome oxide film and help to prevent future corrosion following installation of the fabricated product.
When stainless steel is commissioned into high corrosion environments, such as at sea, near the sea, in polluted environments, etc., then use of a passivating agent is highly recommended to ensure a resilient passive film is achieved.
If stainless steel is corroded in situ, it may be repaired by either polishing or chemical deoxidisation. In either case, the surface of the steel will be active and require a passivation treatment.
Neutralising solutions for trade waste compliance
Many companies now face the implementation of ISO 14000 Environmental Management Systems and ISO 18000 Occupational Health & Safety Systems.
Environmental and occupational health and safety issues are strongly impacting industrial firms which discharge liquid waste, especially pickling and passivating chemical waste.
Low cost alkaline solutions or pastes can be used to remove these chemicals after use from the surface of the steel, or added to holding tanks containing the acidic waste prior to discharge into the sewer or water system.
Pickling chemicals contain hydrofluoric acid and nitric acid and are hazardous. Removal of the pickling agent using a neutralising solution also helps to aid worker safely.
3. ALUMINIUM CLEANING PROCESSES
Most stages of the fabrication life cycle require some form of chemical treatment, including:
- pre weld cleaning
- weld spatter protection
- treatment of acidic waste for trade waste compliance
- cleaning of finished product and prior to painting
- deoxidising of surface corrosion prior to welding for maintenance
Chemical treatment agents for the aluminium fabricator
- pre weld cleaner
- post weld pickling agent
- surface brighteners
- solvent degreaser
Pre weld cleaner
Pre weld cleaning is very important for aluminium to ensure an oxide and water break free surface is obtained to maximise the quality of the weld.
This can be accomplished with an aluminium compatible solvent or non etching acidic detergent.
Acid cleaners are generally composed of either organic or inorganic acids such as phosphoric or gluconic, for example, along with water miscible solvents and organic wetting and emulsifying agents. Soil is removed by etching, wetting, emulsification or dissolution.
Best results for pre weld cleaning usually achieved by hand wiping.
Post weld pickling agents
Mild etching of aluminium after welding can be used to remove heavy oxides, corrosion products and heat discoloration. Hydrofluoric and sulfuric acid solutions or pastes can effectively treat the weld area and heat affected zone.
It is important that stainless steel pickling agents are not used on aluminium as they are far to strong and would result in significant and excessive etching.
Aluminium Brighteners
Aluminium pickling acids or an appropriate acidic detergent will remove oxides and corrosion products without etching the aluminium surface and leave a clean bright surface.
Application by immersion, brushing, spraying or hand wiping.
Removal of corrosion prior to maintenance
Aluminium pickling solutions or pastes can also be used prior to welding to remove resilient surface corrosion and oxides which would interfere with weld quality.
SUMMARY
Quality finish during fabrication of stainless steel and aluminium can be enhanced by chemical treatment prior to and after welding.
In particular, corrosion resistance can be maximised through the passivation of stainless steel following pickling, grinding or polishing during fabrication or maintenance.
New chemical treatment technologies has proven to be more cost effective than traditional mechanical and labour intensive methods for stainless steel and aluminium pre and post weld treatment.
REFERENCES
Full details of the pickling and passivation processes are available in ASTM A380 -94a, Standard Practice for Cleaning, Descaling and Passivation of Stainless Steel Parts, Equipment and Systems
The Australian Stainless Steel Development Association - Australian Stainless 1996 Reference Manual
Guide to Stainless Steel Passivation - Halide Technology Pty Ltd
Metal Finishing - Guidebook and Directory Issue '93
Proprietary Test Data - Callington Haven Pty Ltd, Sydney
Callington Haven, AUSTRALIA
Wow, John. Thanks for the great paper.
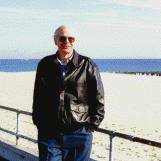
Ted Mooney, P.E.
Striving to live Aloha
finishing.com - Pine Beach, New Jersey
Q. I experienced some trouble while passivating 316 stainless: initially the parts were polished, and after the treatment, the corrosion resistance was improved, but the part had a grainy aspect (maybe due to the removal of the inclusions) and therefore its aspect was no more acceptable. How could I improve this aspect, without loosing the gain of the removal of the inclusions?
Edouard Mignon1998
![]() |
Q. I need some advice. I have a large new 304 SS tank used for the storage of pasteurized milk. The internal finish is better than Ra 0.6 - near mirror finish. Due to the polishing of the surfaces, SS particles are embedded in the surface. I have tried de-greasing, I have tried 5% caustic at 80 °C for 2 hrs followed by rinse and 3% nitric at 60 deg C for 1 hr. The particles are still evident when the surface is wiped with a white paper towel. The resulting black on the towel are present only at the sites of welding and polishing. The main sheet material areas show no traces. The only treatment I have not tried is passivation with 20% nitric at ambient. Could anyone comment if this would solve the problem, or is there a different approach to the embedded SS particles. Dennis Wieckowski1998 A. Dennis Wieckowski : In our opinion, the best process for smoothing and passivating milk handling and storage equipment is electropolishing. In your case, the surface might also have to be given some mechanical polishing to achieve the desired results. It sounds as though the existing mechanical finish might be part of the problem. Please look up our listing on this web site under the suppliers directory. We might be able to suggest a company to handle the electropolishing, depending upon your location. Regards, Ed BayhaMetal Coating Process Corporation - Charlotte, North Carolina 1998 RFQ: Seeking RA20 finish for a Stainless Steel Dairy Model. I have a few demonstration models that I would like to have polished to the Dairy standard. Quick turn around is necessary. Roger S [last name deleted for privacy by Editor]Plymouth, Minnesota 2002 Ed. note: This RFQ is outdated, but technical replies are welcome, and readers are encouraged to post their own RFQs. But no public commercial suggestions please ( huh? why?). |
Q. Can any one offer advice on the following:-
Two different manufacturers of 316L stainless steel supply stainless steel to our company. These are manufactured into stainless steel tanks. One manufacturer's stainless steel will be acid cleaned and passivated to a dull grey color in 90 minutes. The other brand requires twice the time.
Surface analysis of the two steels indicate that the stainless steel which is easily passivated is depleted in chromium at the surface. The steel which requires the longer time to passivate is not depleted in chromium at the surface.Moreover, this material has a higher CPT (ASTM G150). It is suggested that the easy to passivate material is processed through the steel maker's acid bath too quickly.How can we reduce the acid processing time in 20 deg;C nitric/hydrofluoric acid.
Nitric hydrofluoric acid solutions.
MICHAEL ERIC WARDSTAINLESS STEEL TANK MANUFACTURE - ENGLAND
1999
Q. I have a question regarding treatment of stainless steel with acid. I am interested in a acid that would not extract any metals from the stainless steel. Is this asking too much? We are trying to remove a polymer bound material and current analysis requires treatment with 6N hydrochloric acid but certain metals are also extracted and are interfering with the analysis. Any suggestions?
Perry Calias- Cambridge, Massachusetts
1999
A. Perry,
50% by volume of nitric acid is an option if you are dealing with 300 series stainless steels. However, different from HCl, nitric acid is a strong oxidizing agent. You should be very careful with handling the acid, making up the solution, and using the solution. You have to acknowledge all the safety issues regarding nitric acid before starting to use it.
Good luck.
Ling Hao- Grand Rapids, Michigan
1999
1999
"It depends"! Any can mean not enough to bother me to absolutely zero.
316L is not bothered by 6N HCl anywhere near what 410 or even 304 SS is. There are some specialty SS that is virtually unaffected.
Assuming that you mean 304, there is probably no acid that will do what you want it to and not react at least a tiny bit with it.
Some are less aggressive than others, but will they do what you want? 6N HCl is aggressive.
James Watts- Navarre, Florida
Q. What is the best passivating treatment of welds in ss pipe/tube after fabrication? Also, we have noticed some slight discoloration of the body of ss components after installation outside. Does this have anything to do with not passifying after polishing to a #4 finish? Most of our work is done with 304 ss.
G. Curry- Bloomington, Indiana
1999
Q. I am using 304 STAINLESS pipe for food process water. Is there a standard practice or requirement for circulating a pickling solution in erected pipe or is it even necessary? Thanks.
George Bennett- Charlottetown, PEI, CANADA
1999
Q. I do not have anything to contribute to this discussion but I need help. Since you are very experienced on stainless steel passivation, may you have some comments on our production problem. We are a chromic acid producer and we are using 9 mt long and 0,9 mt ID SS316 indirect (LPG combustion gases) heating furnace. Chromic acid production raw materials are sodium bichromate plus sulfuric acid (98%). After 6 months we have seen that the corrosion inside the drum like wound and after 8 months some holes in different points of the drum. My doubt is because of insufficient passivation. (Heating medium 600 °C combustion gases outside the drum, inside is around 140 - 210 °C. Thank you very much in advance for your comments.
F.Tamer Akkoseogluchemicals factory - Mersin, Icel, Turkey
2000
2001
Q. Dear sir,
Recently we got a test results concerning electropolishing and passivation on SS316L double melted material. Our desired figures are that CrO/FeO ratio is over and 3.0, Total Cr/Fe ratio is over and 2.0 after electropolishing and passivation with nitric acid. But we failed to get this continuously.
Our passivation conditions are as follows;
Nitric Acid 68%, Soaking Time 60 minutes.
And the results are CrO/FeO = 1.8~2.2, Cr/Fe=1.8~1.9
I will appreciate greatly to advise me to improve these ratio.
Thank you in advance and best regards,
Kim Yeong-Ho- Busa, Korea
March 30, 2012
Q. Dear sir.
I have a simple question --
We are a pharmaceuticals manufacturing company; we purchase new SS316L pipes and after connecting the pipes using orbital welding, we want to do passivation:
My question is:
Is it correct to start the passivation with water cleaning to remove foreign parts remaining after welding?
What is the first step we have to do after finishing orbital welding?
Regards
- Amman, Jordan
A. Shadi,
What do you mean by foreign parts? You do need a clean, bare metal surface in order to passivate it. It is not uncommon to preclean with an alkaline cleaner.
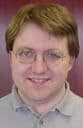
Ray Kremer
Stellar Solutions, Inc.

McHenry, Illinois
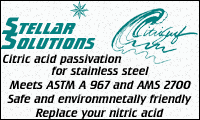
May 4, 2012
Q, A, or Comment on THIS thread -or- Start a NEW Thread