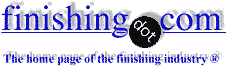
-----
Zinc Chromate Paint Replacements
Q. I have a serious galvanic corrosion problem where aluminum panels are riveted to steel plate. Previously, the steel plate was painted with a zinc dust ⇦ on eBay or Amazon [affil links] which worked OK. The current unsatisfactory system has an alkyd primer only on the steel. This application is truck trailers operating on salt laden roads in the upper Midwest.
What would be a paint replacement for the zinc chromate with comparable performance.
I am also curious about usage of zinc chromate primer ⇦ on Amazon (affil link)] . Is there much use today. If not, when did the use start to decline.
Thank you for any responses.
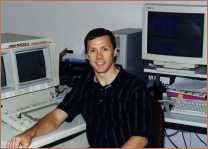
Larry Hanke
Minneapolis, Minnesota
1996
A. Larry,
The use of zinc chromate virtually disappeared from use because of the word chromate. Since hexavalent chrome is a known carcinogen, the world has gone the same way that it did when it found that if you gave a lab rat the equivalent of 500 cokes with saccharin,he would have a higher rate of cancer. Zinc chromate is still available to commercial users but not over the counter. Most painters do not want the hassle of chrome bearing waste disposal so went to substitutes.
If it were me, I would talk to at least three painting giants like Sherwin-Williams engineering departments. There are many better products than what you are using, but will cost more. Then, will your painter apply it?
James Watts- Navarre, Florida
1998
A. FYI
Quote: "P&W -UTC concluded that TT-P-664 [link is to free spec at Defense Logistics Agency, dla.mil]D High Solids (Zinc Phosphate) Primer and TT-P-645B Zinc-Molybdate Primer are both acceptable alternatives to zinc dust, with TT-P-664D being preferred, for providing galvanic corrosion protection for inserts and fasteners used in aircraft engines manufactured at P&W -UTC."
- Holly Springs, North Carolina
2006
May 26, 2013
Re."I have a serious galvanic corrosion problem where aluminum panels are riveted to steel plate."
A. 1. Either use all steel or all Aluminum. What you have is poor design. (Unless you are the vendor, it which case an automatically corrosive design designed for a short life is good).
2. Bolt sacrificial Cathodes (Zinc) onto the body. The cathode corrode and the body does not. Google "Cathodic Protection".
3. Do not waste your time with paint. It will never last in your environment. Too much wear on the paint for it to last.
- Santa Ana, California
Multiple threads merged: please forgive chronology errors and repetition 🙂
Q. I would like to know a safe (an approved) alternative to zinc zinc dust er TT-P-1757 [⇦ this spec on DLA] . Can you point me in the correct direction?
Dave Gubics1998
Q. It is my understanding that it is the chromate content of the paint that provides the corrosion protection for the aluminum.
Zinc or Aluminium rich paints protect steel wonderfully from corrosion by sacrificial means but do nothing for Aluminium alloys as the alloy corrodes to protect the paint. The chromate ions react with the Aluminium forming a tough skin over the surface.
As I am building a light aircraft I would like to see a safer system with equal performance to protect the all alloy structure
The alloys used are 2024 sheet riveted with 2017 rivets.
Any other comments?
Allan Gibson1998
I hope that it gives someone pleasure to know, that while I was barreling down some salt laden interstate in the upper Midwest, drinking my saccharin free soft drink, and some rivets pop off of the oncoming truck, that I will never get cancer from the chromate it didn't use. (Don't he look natural?)
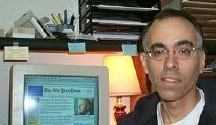

Tom Pullizzi
Falls Township, Pennsylvania
1998
A. Phosphating treatment may be a promising alternative to zinc zinc dust er.
Ling Hao- Grand Rapids, Michigan
1998
A. Colleagues:
Zinc chromate containing coatings are still readily available. However, with the drive to eliminate Cr+6 you may want to look for an alternative. General Motors specification GM7111M is a chrome-free product that performs exceptionally well against aluminum. Opel has another similar process as GME00255-B.
Edward Koneczny- Birmingham, Michigan
1998
![]() |
I have a big problem. I need to put the color blue zinc chromate on mild steel c12l14. The problem is that the chromate blue doesn't stick to the steel. Does anyone have a miracle solution for me? Christian F [last name deleted for privacy by Editor]1998 A. Christian: Zinc plated parts are virtually always chromate conversion coated. To answer your question, if I am understanding the situation: a blue chromate works on a zinc plated surface, not on a steel surface. There is a chemical reaction between the zinc and the chromate, and it is the reaction products that "stick" to the surface of the zinc, not the chromate solution per se. So, in brief, the way you will get it to stick is to zinc plate the parts. Also, note that a "blue" chromate will only be very faintly blue. This is a carcinogenic, EPA-regulated chemical, and you really shouldn't get it without the tech data sheet and the MSDS. You may be stuck with a bill to legally dispose of it. Good luck. ![]() Ted Mooney, P.E. Striving to live Aloha finishing.com - Pine Beach, New Jersey 1998 |
Q. I understand that there is a micaceous iron oxide based paint that has been used on road chassis on trucks for many years. Is this true?
Why does it work and where can I get some?
Thanks in advance.
Hans Waltl- Durham, North Carolina
1999
Ed. note: This RFQ is outdated, but technical replies are welcome, and readers are encouraged to post their own RFQs. But no public commercial suggestions please ( huh? why?).
Q. I'm trying to find a Zinc zinc dust er that I can apply to bare copper wire. I have installed copper wiring inside a doll house, and I need to seal it so when I apply a water base paint or wallpaper to the walls, the copper will not turn green. Currently the only size available to me is in one gallon size. Is there any other product available to do the same thing as the zinc chromate. Any help with this problem will be greatly appreciated. Thanks,
David Roth- Carrollton, Texas
2000
Ed. note: This RFQ is outdated, but technical replies are welcome, and readers are encouraged to post their own RFQs. But no public commercial suggestions please ( huh? why?).
A. Hi, David. brass lacquer ⇦ on eBay or Amazon [affil links] would probably be the thing to use on copper to preserve its appearance. G.J. Nikolas [a finishing.com supporting advertiser] specializes in this, but it sounds like you just need one little can. Good luck.
Regards,
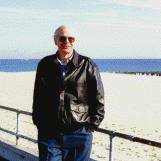
Ted Mooney, P.E.
Striving to live Aloha
finishing.com - Pine Beach, New Jersey
Q. Is zinc chromate suitable to use on steel to stop rust?
david navaille- Meraux, Louisiana
2000
A. Hi David. Yes, it will deter rust. But as you can see, the question of whether it is 'suitable' is rather complex.
Regards,
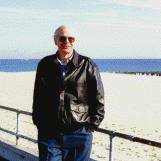
Ted Mooney, P.E.
Striving to live Aloha
finishing.com - Pine Beach, New Jersey
Q. I want to know various options to protect Mild Steel surfaces, aluminium surfaces, and stainless Steel surfaces exposed to
1) high moisture conditions
2) saline moisture conditions
The options should be weighed over constraints like eco friendly, cost, and availability in this part of world.
- Mumbai, Maharastra, India
April 15, 2008
April 17, 2008
Hi, Neeraj.
For steel your choices include organic coatings such as paint and thermoset or thermoplastic powder coating on top of phosphatizing or electrocoating; and galvanized or electroplated inorganic coatings of some 20+ different metals, plus their alloys. For aluminum, eliminate the galvanizing but add chromating as an alternative to phosphating; and add anodizing in the inorganic category. For stainless, all of the alternatives for mild steel, plus passivation, electropolishing, or anodizing. And this list is just the beginning as there are hundreds of other specialty finishes.
All of these are valid alternatives and are widely used, and none can be eliminated in an abstract discussion. If you describe a particular piece part of a particular size & particular production volume, and add all of the additional constraints on the finish, the list may be shortened sufficiently that you can compare a few specific finishes. Otherwise, your question sounds like an excellent description for a 4-year degree program :-)
Good luck!
Regards,
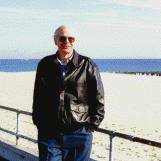
Ted Mooney, P.E.
Striving to live Aloha
finishing.com - Pine Beach, New Jersey
Q. I am preparing some 2024 aluminum parts for painting and carpet adhesion in an aircraft. The yellow zinc zinc dust er spray can I had bought for this project turned out to have a defective nozzle and wouldn't spray. Not wanting to leave the aluminum unprotected after stripping, cleaning and Scotchbriting, I used a zinc rich primer that I had left over from another project for undercoating galvanized steel. Only after I had used it did I realize that it specified galvanized steel and not aluminum. Will I need to re-strip this zinc-rich paint, and re-apply one formulated for aluminum? Have I done any damage to the aluminum by using this primer instead of a zinc chromate application for aluminum?
Coleman Weidenbusch- Plattsmouth, Nebraska, USA
April 3, 2010
A. A plethora of information is available on alternate primers.
Since there are so many experts all over the USA in the coatings field. I propose that we should have an annual get together at different sites, where we all can get together and exchange ideas, verbally in an informal setting, much like the Gordon Conferences in Chemistry.
Let me know what you all think.
Regards
- Novi, Michigan, USA
November 15, 2011
Q. Comparison between the application procedure between Zinc phosphate & Zinc Chromated
Mohammed Hafeezur Rehman- Abha, Saudia Arabia
July 17, 2012
A. Hi, Mohammed. I don't know if you are asking for a comparison between painting with a zinc phosphate based paint vs. painting with a zinc chromate based paint (if so, what is the material and condition of the substrate), or whether you are asking about phosphatizing vs. chromating zinc diecast parts or zinc plated parts, or whatever.. Please take the time to explain your situation, always using more words in your question than you want in the answer :-)
Thanks.
Regards,
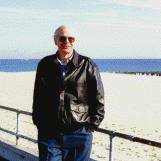
Ted Mooney, P.E.
Striving to live Aloha
finishing.com - Pine Beach, New Jersey
July 17, 2012
Q. I was wondering if Zinc zinc dust er is toxic to touch after priming is complete IE: left bare and unpainted over.
Pyotyr Prepka- Hauppauge, New York, USA
January 29, 2013
A. Hi Pyotyr,
If I seem a little circumspect with my answer it is because I don't want to give you the impression that there is an easy answer.
Zinc chromates, indeed virtually all hexavalent chromates are considered to be toxic to some extent or another. As well as being skin sensitisers, respiratory sensitisers and generally nasty fellows, the main concern is the possibility of hexavalent chromium compounds to cause cancer.
Most chromates are considered to cause cancer by inhalation, in fact that is the usual classification, but there is quite strong evidence that they may cause cancer by ingestion.
Chromated primers are designed to slowly release the chromates over time to aid in corrosion prevention so there will more than likely be a slow release of the zinc chromate over time. This is where things get woolly, it comes down to the release rate of the chromate and how much of this is available to come into contact with humans, the concentrations involved and the form of release. We cannot as an anonymous group of engineers really advise you exactly how dangerous is the application as we do not have access to the parts in question to carry out a risk assessment.
If you are really worried I would suggest you contact your local EPA office and get them to carry out an assessment or contact the OSHA for a more definitive statement on the potential toxic hazard posed.
Aerospace - Yeovil, Somerset, UK
February 15, 2013
Is black zinc chromate paint "better" than yellow zinc chromate primer ⇦ on Amazon (affil link)] ?
Q. Yet another piece of the zinc chromate paint question. I am also building a light aircraft. Traditional zinc chromate paint, to be thinned with toluene and applied in a very thin coating on bare aluminum, has been the corrosion protection of choice for decades (particularly for mating surfaces that can trap moisture but are not exposed to abrasion) and is still available. Two colors are common, yellow (just zinc chromate) and green (with lampblack added). I am trying to nail down the reasoning behind the difference, besides appearance. Many accounts assert that the pigment is somehow light sensitive and black is added to give some UV protection. Is there any basis for that? Is there any reduction in corrosion protection qualities with a change in color?
David Josephson- Santa Cruz, California USA
August 15, 2014
A. Chromate pigment is broken down by by a photocatalytic reaction. Example ZnO +hv → ZnO (h+ + e- )
(1) Cr2O72- + 14H+ + 6e- → 2Cr3+ +7H2O
(2) 2H2O + 4h+ → O2 + 4H+
(3) H2O + h+ → OH + H+
(4) Cr(VI)+H2O2 + H+ →Cr(III)+H2O+O2
By adding a UV blocking pigment (like lamp black) you can slow down the process. For a long lasting protection, when exposed to light, you will need a UV resistant top coat. The best is to use a tested paint system which usually consists of a base coat for adhesion, a corrosion protective coat (zinc chromate) and a top coat for UV and mechanical protection. You can also get chrome free alternatives that are easier on the environment and your health. http://www.duncanaviation.aero/fieldguides/chromefreepaint/
Tomas Bengtsson- Jönköping, Sweden
December 3, 2014
Q. My situation:Hi, does zinc chromate coating have any advantages vs regular zinc coating (made by electroplating or hot dip) in corrosion prevention if items are in indoor swimming pool far away from the water so corrosion is mainly caused by chloride ions?
Keem Pava- Warsaw, Poland
July 13, 2018
? Hello Keem.
Are you talking about zinc zinc dust er PAINT, and thus asking for a comparison between painting vs. plating? Or are you talking about zinc plating with a chromate conversion coating? Zinc plating and galvanizing invariably receive a chromate conversion / chromate quench, so that question wouldn’t really make much sense since you're unlikely to find zinc plating or galvanizing (designed for final service) that doesn't include the chromate conversion coating :-)
Regards,
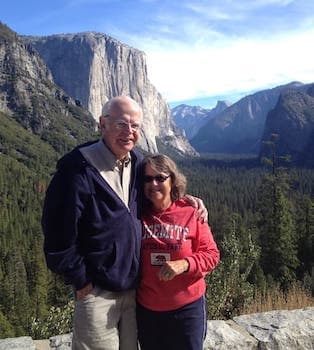
Ted Mooney, P.E. RET
Striving to live Aloha
finishing.com - Pine Beach, New Jersey
July 2018
Q, A, or Comment on THIS thread -or- Start a NEW Thread