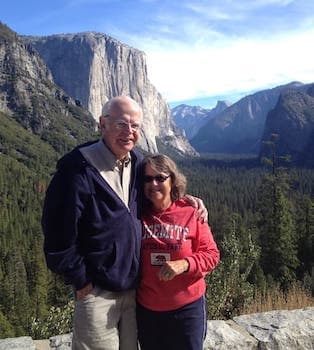
Curated with aloha by
Ted Mooney, P.E. RET
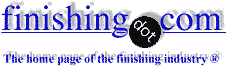
The authoritative public forum
for Metal Finishing 1989-2025
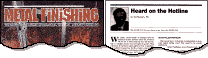
-----
Plating aluminum with copper
Quickstart: Aluminum is an 'active' metal which immediately oxidizes, growing a oxide coating which makes electroplating onto it difficult & unreliable.
So before electroplating, an intermediate step is done to dissolves those oxides and replace the oxidized aluminum with zinc (or tin). This 'zincating' involves dipping the aluminum into a concentrated, highly alkaline, zinc solution which causes that displacement/replacement process. For some alloys & conditions better results are obtained by 'double zincating', i.e., zincating, stripping the zinc with nitric acid, and re-zincating.
This discussion covers zincating details, copper plating details, and everything related.
Q. I do double zincate then plate with pyrophosphate copper but it peels off after baking. But if plated with Watts nickel the adhesion is quite good.
How can I solve this problem? -- my customer requires that the first layer is pyrophosphate copper after zincating.
Thanks,
- Bangkok, Thailand
June 21, 2023
A. Hi Aon. I'm personally unfamiliar with plating pyrophosphate copper onto zincate (which doesn't mean it's wrong or rare) -- I'm just more familiar with cyanide copper plating.
It might be that copper pyrophosphate on zincate just will never work as well as Watts nickel. But if you search the site with "copper pyrophosphate zincate" you will find replies from people who are familiar with this process :-)
Luck & Regards,
Ted Mooney, P.E. RET
Striving to live Aloha
finishing.com - Pine Beach, New Jersey
Q. Thanks for your reply.
What about cyanide copper on zincate? Will it work? My work pieces are 6101 T63 aluminum of two types with surface area the same.
• 1st is original surface from aluminum raw material,
• 2nd is the CNC machine after plating cyanide copper on zincate.
Just only the 1st area adhesion fails but the 2nd area gets good adhesion. I thought about the aluminum oxide from heat treatment so I tried to remove that by using various acids and alkalis overall, following ASTM B253. It did not work. But immediately getting good adhesion when the workpiece is ground with sand paper before going to plating process . Is it aluminum oxide? How can I improve the adhesion by using chemicals?
Thanks
- Bangkok, Thailand
A. Hi again. The pretreatment before plating on aluminum is the same as the pretreatment before anodizing or chromate conversion coating:
vibratory or tumble finishing, non-etch caustic cleaning, etch in caustic soda, desmut ... and then single or double zincate, then cyanide copper.
Luck & Regards,
Ted Mooney, P.E. RET
Striving to live Aloha
finishing.com - Pine Beach, New Jersey
⇩ Related postings, oldest first ⇩
Q. I am fabricating 6 inch dia. aluminum mirrors and would like to plate them with copper. I have never electroplated anything before but have brushed up on my university electrochemistry. I tried a sample piece of polished aluminum with copper sulphate
⇦ this on
eBay or
Amazon [affil links] solution and a battery charger
⇦ this on
eBay or
Amazon [affil links]
but the build up was very pulpy and did not adhere to the aluminum surface, flaking off when I tried to polish it to a smooth finish.
What can I do to produce a mirror like quality smooth layer of copper over my aluminum blank?
Any and all suggestions greatly appreciated.
Thank you.
Note: These mirrors will be used to reflect IR (heat) from an oven to focus the energy and may be operating at a very high temperature.
- Canada
1996
sometimes on
AbeBooks or Amazon
(affil links)
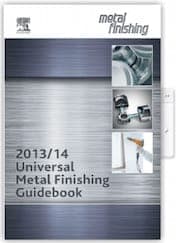
free pdf is currently available from academia.edu
A. Dr. Dovigi:
The surface of aluminum items almost instantly oxidizes, so that the surface is not active and not amenable to plating. A solution is to zincate the item first, replacing the aluminum surface with a zinc surface, which is plateable. Even then, copper is far more noble than zinc and will immersion deposit pulpy and non-adherently from a copper sulphate solution. You would need to cyanide copper plate or copper pyrophosphate plate before you do the acid copper. There is a lot to the process, and you may want to read a few chapters on this from a plating text before starting.
But I wonder if you are approaching things the best way? My limited understanding is that infrared reflectors are usually bright dipped, anodized, and gold dyed, rather than copper plated (which is simpler, less expensive, and more reliable if it performs adequately).
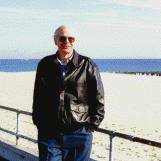
Ted Mooney, P.E.
Striving to live Aloha
finishing.com - Pine Beach, New Jersey
Q. Dear Ted,
Thank you for your reply and information. I know a gold surface is a much better reflector at infrared wavelengths. The only reason for using copper was to try and keep the costs down. Being a dentist I have worked with gold foil and considered this an option to plate the finished surface of the mirror blank, but again I ran into the problem with the gold foil not adhering to the aluminum surface. Now that you have explained why (aluminum oxide coating forming) I understand why this failed as well. Can you offer any suggestions on the most cost effective way to go about plating my mirrors?
Thank you Al
- Canada
A. Sir,
As an anodizer I agree with Ted ... hardly any of the platers I know plate on Aluminum. We process many reflectors here with bright dip and clear and colored anodize.
- Long Island City, New York
Q. Thank you for your reply and information on trying to electroplate aluminum with copper and why I failed. I have also tried to coat the aluminum surface with gold foil but it failed to adhere to the surface. I understand now the oxide coating is the source of the problem.
Any suggestions on how to overcome this problem and to coat the reflecting surface of my aluminum mirror with gold foil?
Thank you.
Note this mirror will be operating at high temperatures. Will thermal cycling pose a problem with adhesion?
- Canada
A. Hi again. To plate them you would mechanically finish, then etch, then desmut, then zincate, then cyanide copper plate, then nickel plate then gold strike, then gold plate.
But again, please research whether David & I are right that bright dipping, anodizing and gold dyeing will deliver the infrared reflectivity you desire ... because it doesn't make sense to struggle to invent a very complicated process if a well developed, cheaper, simpler, & more robust method already offers what you need. Good luck!
Regards,
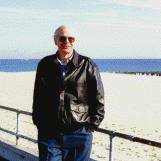
Ted Mooney, P.E.
Striving to live Aloha
finishing.com - Pine Beach, New Jersey
Q. I have a brush plating system and do gold and chrome plating of car emblems. My question is how can I gold, chrome or nickel plate aluminum emblems or motorcycle parts using a brush system?
Also where may I get info on designing brush plating equipment and tank plating systems.
1998
A. Plating on aluminum usually requires a zincating step. Your supplier, or brush plating suppliers like Gold Touch [a finishing.com supporting advertiser] can provide the zincate if needed. The actual process is to clean the aluminum, etch it with caustic, desmut with an acid appropriate for the particular alloy, zincate, cyanide copper plate, acid copper plate, nickel plate, then gold or chrome.
I don't know of any articles that quite tell you how to design brush plating systems, but
• Rubinstein's "Electrochemical Metallizing" [on
eBay,
Amazon,
AbeBooks affil links] is a full encyclopedia of info about brush plating, and
• the "Electroplating Engineering Handbook" ⇦ this on
eBay,
AbeBooks, or
Amazon [affil links]
, edited by Larry Durney is all about designing tank plating systems
Best of luck.
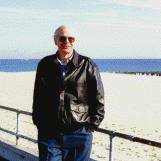
Ted Mooney, P.E.
Striving to live Aloha
finishing.com - Pine Beach, New Jersey
A. All of the major brush plating vendors have methods for plating on aluminum.
At least one vendor has a procedure for plating on aluminum (simple shapes) without the zincate and claims good adhesion. You have to be quick and good to do it however.
- Navarre, Florida
Q. I am with a company active in HF PCB as electromagnetic field radiators. These boards have very few soldering points and therefore I laminated plastic substrates with aluminum foil instead of expensive copper. My idea was to plate copper 1-2 microns thick after etching off the extra aluminum on the sides of the board leads.
The etching shop that supports our R&D initially was positive about prospects to have another massive project in a little while, but after three weeks of experimenting is not giving me anything.
Meanwhile I learned of a "Aluminum Bonder" - material that allows copper built up on the brushed with it aluminum.
Will appreciate any kind of advice, offer to cooperate.
- Rosh Ha'Ayin, Israel
1999
A. Dear Mr. Ostrovsky,
Thank you for your letter.
It sounds to me that you want to make the circuit paths of a wiring board using aluminum, and you just want to plate "tabs" at the soldering points using some kind of copper plating. Using a robust activation system using a metal cleaner, then a zincate as you describe as the aluminum bonder, followed by an aluminum tolerant electroless nickel, then a electroplated copper, then electroplated tin should provide a solderable surface for your connections.
Regards,
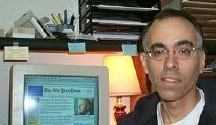

Tom Pullizzi
Falls Township, Pennsylvania
Cyanide Copper Strike Bath
Q. Hi! I have a couple of questions about a cyanide copper strike bath: When comparing a "standard" strike bath with a low efficiency Rochelle
⇦ this on
eBay
or
Amazon [affil links]
bath; which one of them is "kindest" to the zincate layer. That is, which one is the least aggressive to zinc? If so, I have the following questions: What possible interference/contaminants can have a negative effect on the previously applied zincate immersion layer? In other words, what can destroy or dissolve the zinc layer when I immerse the work in the copper strike bath?
If possible, I'm also interested in the chemical explanation involved.
Tips about books and articles about this subject would be great.
- Sweden
2001
A. Dear Stefan,
It's the other way around. In my experience the Rochelle baths don't work well once you use zincate covered parts in them . A Standard bath works better, has better LCD coverage when using zincate or zinc diecast parts.
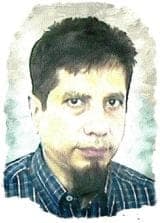
Khozem Vahaanwala
Saify Ind

Bengaluru, Karnataka, India
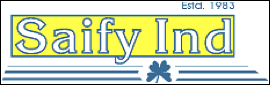
A. Hi Stefan,
The best copper solution to use for plating on zincate is follow copper solutions:
Alternative No. 1. Copper cyanide 41 g/l, Sodium cyanide 56 g/l, Rochelle salt 60 g/l, sodium carbonate 30 g /l, pH-range 10-10,5, Free Cyanide 8,0-10,0 g/l, Temperature 45-60 °C., Current 2-3 A/dm2
Alternative No. 2. Copper cyanide 26 g/l, Sodium cyanide 32 g/l, Rochelle salt 30 g/l, Sodium carbonate 30 g/l, Free cyanide 1,5-3,0 g/l, Temperature 45-60 °C. Current 2-3 A/dm2.
You should also use pre-contact when you plate on zincate in electrolytic solution. The zincate dissolves in copper solution. Zincate is only one protection for eliminate at the aluminum shall oxidize and thereby create bad adhesion between copper and aluminum. It is only a very thin zincate films on the aluminum substrate under copper deposit.
Regards,
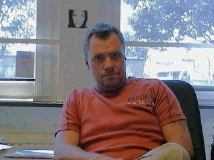
Anders Sundman
4th Generation Surface Engineering
Consultant - Arvika,
Sweden
Multiple threads merged: please forgive chronology errors and repetition 🙂
Q. I am trying to coat copper on Aluminum foam using copper cyanide, potassium cyanide solution, KOH, rochelle salt and potassium carbonate and platinum counter electrode.
I do standard pretreatment to aluminum substrate before coating and my problem is after plating (one day) foam start to getting black/blue color. Looks like copper is slowly reacting.
Is it a usual thing?
Is there anything I could do to avoid this happening?.
I would appreciate if someone can answer my question.
student - Lansing, Michigan , USA
2003
A. I can tell you general plating method of copper on aluminium:
1. etching(NaOH)
2. desmut(HNO3)
3. zincate
4. strip(HNO3)
5. zincate
6. copper cyanide strike
7. copper cyanide(high concentration)
8. acid copper
9. nickel
10. chrome
Why use Pt anode? Copper ion source are solution and anode.
Thank you!
- KOREA
2003
Copper plating an aluminum bike
Q. Hi,
I would like to ask, which method should I use for creating a copper plating on aluminum.
I've decided to turn my racing bicycle to little bit of an 'art-project'. The goal is to cover AN6 aluminum frame with a layer a copper and let it get some natural patina over time. The method should be non-destructive to the thin-walled frame tubes.
Thank you for your opinions.
All the best,
hobbyist / designer - Bratislava, Slovakia
2007
A. Hi Michal,
I think you should be able to more simply "paint" your bike with a system of primer, copper-based paint, and patinating solution instead :-)
Electroplating is more industrial science than hobbyist art, and your facilities, training, & experience aren't clear to me, but plating copper onto aluminum would require zincating, followed by cyanide copper plating, followed by bright acid copper plating. Our "must-have booklist" will cover each of these subjects in depth.
Good luck with it.
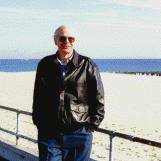
Ted Mooney, P.E.
Striving to live Aloha
finishing.com - Pine Beach, New Jersey
Coating aluminum with copper for conductivity
Q. Hi,
I am trying to coat copper on aluminium. I want to know if the resultant conductivity is more than the parent metals?
Thanks
- Vizag, Andhra Pradesh, India
February 6, 2013
A. Hi Venkata. Aluminum bus bar is commonly copper plated because the copper has better surface conductivity (because aluminum quickly oxidizes in air to form an insulative aluminum oxide coating on its surface). But the copper plating is usually not thick enough to significantly alter the DC capacity of the bus bar. For example, if an aluminum bus bar has 50-60% of the conductivity of a copper bus bar of equivalent size, then it will still have 50-60% of the conductivity of a copper bus bar after plating it with copper.
But we have to be careful with general terms like "conductivity" because there is thermal conductivity vs. electrical conductivity, surface conductivity vs. solid conductivity, the fact that high frequency currents are carried by the skin rather than the core of a conductor, etc.
Regards,
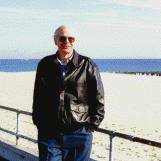
Ted Mooney, P.E.
Striving to live Aloha
finishing.com - Pine Beach, New Jersey
Best formulation for cyanide copper strike over double zincated aluminium
Q. I operate a small electroplating shop and frequently process mainly decorative aluminium pieces, which are ultimately finished in gold or platinum. I use a very basic cyanide copper strike (50 g/l copper cyanide, 90 g/l Pot cyanide) after double zincating and sometimes experience blistering of the copper (and subsequent deposits). Could anyone please suggest the most suitable and reliable cyanide copper formulation for this application?
Many thanks,
- Plymouth, Devon, UK
A. Hi Jonathan. We appended your letter to a thread where Khozem Vahaanwala and Anders Sundman have already offered their opinions on optimum formulation. We'll see whether a third opinion is forthcoming. Good luck.
Regards,
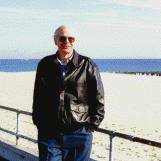
Ted Mooney, P.E.
Striving to live Aloha
finishing.com - Pine Beach, New Jersey
Want to copper plate anodized aluminum
Q. I am trying to copper plate anodized aluminum. Any ideas?
John Allegro- Dallas texas
September 14, 2015
Hi John. Please introduce yourself (student, post-doctorate research, plating shop owner, hobbyist with no plating experience) and what you are trying to build. We don't like to be in the position of instantly losing a beginner by omitting the basics, nor of talking down to someone who may know 10X as much about the subject as I do :-)
But assuming that you're a beginner, anodized aluminum is non-conductive, non-metallic, and non-plateable in the normal course of things. Get back to us with your situation please and we can get the discussion rolling.
Regards,
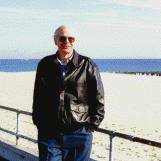
Ted Mooney, P.E.
Striving to live Aloha
finishing.com - Pine Beach, New Jersey
How to do cyanide-free plating of copper onto aluminum
Q. Hi,
I'm Research student and I have a problem with coating of copper on the aluminum substrate. The adhesion is weak and copper cyanide is not suggested on my research because of the toxicity. Do you have any suggestions in order to produce good copper coating on aluminum substrate?
MARA Technology University - shah alam, selangor, Malaysia
November 15, 2015
Hi Mohammad. After zincating the aluminum you can try pyrophosphate copper or proprietary solutions from companies like EPI / Electrochemical Products Inc. [a finishing.com supporting advertiser]. Good luck.
Regards,
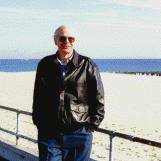
Ted Mooney, P.E.
Striving to live Aloha
finishing.com - Pine Beach, New Jersey
A. To avoid oxidation on my metals I do the cleaning and plating all in an argon gas bath, I'm sure there are lots of explanations on this if you google it.
Nick scott- Bangor, Maine, United states
June 2, 2016
Q. I want to electroplate aluminium.
I have Al zincate from Growel,
I also have copper cyanide bath.
Kindly suggest the process
electroplaters - Mumbai, India
April 18, 2017
A. Hi Amish. Clean, etch, desmut, zincate or double zincate, copper cyanide plating. We appended your inquiry to a thread which already answers it. But get back to us if anything is unclear to you.
Regards,
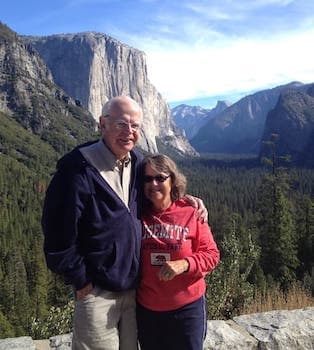
Ted Mooney, P.E. RET
Striving to live Aloha
finishing.com - Pine Beach, New Jersey
April 2017
Q. Dear Respected Sir,
I hope you are fine.
I would like to copper plating on aluminum so I have tried an experiment to achieve coating but failed. My electrolyte composition is CuSO4 200 g/L + 120 g/L Sulfuric acid;
I have put the aluminum M24 section piece about (6" * 2") and get 18v AC Current. After anodizing as a result brownish particles appear on aluminum surface roughly. Please tell me if any think there are other techniques which can improve it. So please tell me now, I shall be waiting on your answers.
Pfizer Aluminum - lahore, Pakistan
March 10, 2018
A. Hi Kamran. I am trying to understand what you have said, but I am a bit confused.
First, you have used the word "anodizing", but I think you meant "electroplating", not the separate & different process of aluminum anodizing? Second, DC voltage is required for electroplating, not AC. Third, 18V is way too much; more like 3V would be right. Fourth, the aluminum must be prepared by cleaning, etching, desmutting, and zincating before plating. Fifth, you cannot use a copper sulphate plating bath on aluminum (actually on zincate).
My apologies if you really did mean "anodizing" and if you are meaningfully using 18V AC (we are having a little bit of language difficulties). In any case, we added your question to a topic about plating copper onto aluminum. Good luck.
Regards,
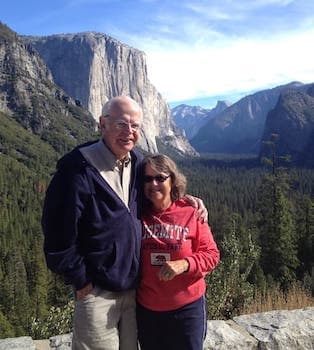
Ted Mooney, P.E. RET
Striving to live Aloha
finishing.com - Pine Beach, New Jersey
Q. Dear Ted Mooney,
What is desmutting, zincating -- please tell me more about this terms. And I explain my plating process step by step for you --
Degreasing
Rinsing
Etching
Rinsing
Neutralizing
Rinsing
Anodizing (H2SO4)
Rinsing
Plating (CuSO4+Acid)
But I am not gaining sufficient coating. I require 10µm copper thickness.
Pfizer Aluminum - lahore, Pakistan
A. Hi Kamran. Desmutting is a step which is often used in between etching and anodizing (dependent upon the particular aluminum alloy you are treating) to remove alloying materials from the surface because the etch dissolves aluminum but leaves any silicon, copper, and other alloying materials behind on the surface. Apparently you are trying to electroplate copper onto an A.C. anodized surface. Zincating doesn't seem to have anything to do with your experiment, so there's no sense confusing it.
I've never heard of attempting to electroplate onto a sulfuric acid anodized surface, so the ball is in your court. Where did you get the idea for this process, what papers did you read about it (when experimental plating methods remain only experimental methods, it's usually because they didn't work well). Why are you trying to electroplate copper onto aluminum in this odd way instead of using production proven methods? What is the end use of this copper plated aluminum?
Regards,
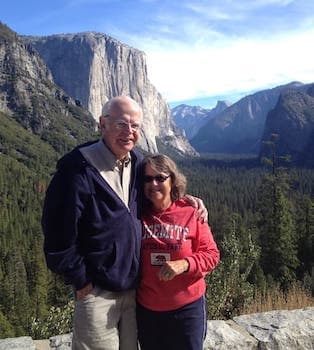
Ted Mooney, P.E. RET
Striving to live Aloha
finishing.com - Pine Beach, New Jersey
A. Hi Kamran
Anodising produces an oxide layer on aluminium. Aluminium oxide is non conductive to electricity. I am very surprised that you get any copper deposited. It is presumably down to the fact that you plate copper immediately after anodising and before the pores in the oxide layer are sealed. Whatever the reason, the adhesion must be very poor.
Can you explain the reason for anodising?
If you are simply aiming to plate copper on aluminium, the zincate process is standard practice and has been for many years.
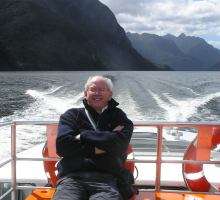
Geoff Smith
Hampshire, England
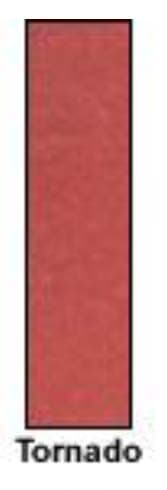
Q. Sir Geoff Smith & Sir Ted Mooney, thank you so much for your replies. I am very glad for your kind replies. Firstly I will explain that I am achieving tornado color on our aluminum
1. "Where did you get the idea for this process?". Actually I have seem another company's aluminum section plated by copper so I am trying it.
2. "Why are you trying to electroplate copper onto aluminum in this odd way instead of using production proven methods?" Because I have successfully plated tin on aluminum by this process; then I would try to do copper plating on aluminum.
3. "What is the end use of this copper plated aluminum?" In the making of door/window profiles.
4. "Whatever the reason, the adhesion must be very poor." Sprinkling (shining Bubbles) appears in the electrolytes when passing electricity by which adhesion must be poor from my requirement.
5. "Can you explain the reason for anodising?" Actually in my company firstly aluminum section is anodized then plated by tin (acid bath) thus I was anodizing it.
My neutralizing tank composition is 80 g/L H2SO4+ 50g/L HNO3, is it desmutting or not?
Pfizer Aluminum - lahore, Pakistan
A. Dear all,
This is very interesting reading, I had by chance to ponder upon plating copper onto aluminium as well, recently. I would go the way of using any of the new alkaline baths with organic binders/complexers, that is completely cyanide-free.
I will not go into detail as there are many competing designs (I mean compositions and usage parameters), some more exotic than others, starting with baths very similar to classical acid or alkaline baths, ending with baths of ionic liquids.
As someone above said: removing all traces of aluminium oxide is the most non-trivial task imaginable, someone above went as far as aerating baths with Argon gas to get rid of all traces of oxygen imaginable!! That is expensive.
Also expensive is what was mentioned above and involved two or three nitric acid baths (yuck!). But then, that process works.
To learn to plate a mixed substrate such as aluminium alloys (unetched) and get SOME adhesion, it would be necessary to learn some or all of the chemistry that is used in semiconductor industry to plate copper onto silicon and similar materials. It requires non-trivial understanding of the competing additives and a lot of reading (not that much, really after reading 100 useful pages out of 1200 found you will have a pretty good understanding of the processes involved), after which you will get the idea how to get to designing your own process (because the bath, substrate, impurities, current density and a myriad of additives interact differently on various alloys).
The keyword here is Damascene process. It can plate and level a 10-nanometer wide pinhole, up to 0.15 mm blind holes (!!) But the additives there are competitive; a mismatch and you're done without understanding what to do.
Alternatively, a similar process of electroless copper deposition can be used, but that also, is very expensive and not to mention instability, heating and limited lifetime of a bath. If you end up activating the surface with SnCl2 and palladium ions, it gets even more expensive.
I do not think that half of the companies offering copper plating on windows use plating in the right sense of the word, you can get copper color onto material in various other, much simpler means. Many special synthetic varnishes would latch onto anodized aluminium, and these could have copper flakes/powder/platelets, etc, together with another additives to keep the copper shiny. (not telling, bwahaha) (...and there are faithful plastic copper imitations as well...)
But honestly, I would try to avoid dangerous stuff, like nitric acid, etc, and as my interest is in simpler shapes (cylinders), I would use mechanical copper blasting to prepare the aluminium surface, or even incorporate copper into it. If you had the money, HVAF would be able to blast as much copper onto aluminium as you'd like. Just clean, shine and protect it afterwards.
And, to add: ANYONE TRYING PLATING ALUMINIUM MUST UNDERSTAND THAT ALUMINIUM WILL QUICKLY FALL APART WITHOUT THE OXIDE LAYER.
Thus, trying to plate aluminium is like trying to paint a burning house. BUT, If the house isn't on fire, it is covered with teflon and your paint won't stick.
I hope the analogy is reasonable.
P.S. When I think about this: anodizing before copper plating does sound like an invitation to a damascene process, as anodizing would create a honeycomb structure into which the copper could be deposited into the deep holes. But then you are in the area of semiconductor specialists, and your level of understanding chemistry of quaternium nitrogen compounds and organosulfur compounds and aromatic rings... would need to catch up, if you want to provide a reliable process.
The dosing of the additives starts at ppm (parts per million) levels, and best if calculated at molar concentrations relative to other key constituents of the plating bath. I have seen pictures (taken by electron microscope), where 0.35ppm of an additive would do one thing and 1.0 ppm would do something else. And if you added 1 ppm of some other additive, it completely counteracted the first additive.
Did I mention that current density vastly changed what was going on in the bath as well? That too needs to be controlled, unlike at anodizing, which doesn't care.
Again: the current density per square decimeter needs to be well controlled, the adequate anode area must be provided, the bath agitation must be provided.
- Vienna, (The Coffee City), Austria
A. Even more: using process similar to classical photography:
1) soak copper salt or complex into the fresh anodized pores -- it must be compatible with the anodizing bath
2) drip off, soak in developer bath (reducer to change copper salt into copper and a soluble salt or complex)
(( alternatively 2a) change copper salt into insoluble precipitate like CuO by a redox reaction, 2b) convert CuO to Cu))
3) leach or wash soluble products sufficiently away
4) neutralize, passivate, seal, varnish, etc. in a usual manner.
I tried a variant of this in a sample of the alkaline complexed bath. First adding alcoholic solution of methylene blue [affil links] seemed to precipitate nanometric black CuO, after some time the dispersed crystals grew, the optical density of solution decreased. Then, dripping in a type of mouthwash, the floating microcrystals seem to grow even more into a metallic glitter instead, which on paper show as red color copper with a very pleasing metallic shine and glitter. The crystals can only move over surface of the paper, while the (blue) liquid soaks into the paper.
Jane D. Stanton- Vienna, (The Coffee City), Austria
July 20, 2018
A. 3 more notes:
>90% of the published new (=innovative) research on copper and nickel plating, and various compositions of alloys plated (Such as Ni-P-Cu, Ni-P-Sn, etc.) is from 2016, 2017 and newer.
Copper imitation over eloxed aluminium would be best done utilizing the fresh unsealed pores in the oxide, filling them with copper particles. As the pores are small, special size particles have to be used. Solvent: ultra-low viscosity such as dimethylketone (=UN1090, =acetone) or methanol
[affil links] or such should be used. Copper passivator must be present in the bath. For me, it is easier to manage a highly flammable solvent in one bath than working with a set of 13 dangerous baths. Pressure spraying/mixing might be tried to increase impregnation, or electrophoretic deposition.
I have tried one complexed bath and oh my, you do need to think before mixing ingredients, order is important. Second, the complexed bath is of exactly methylene blue color, very, very deep. You won't see the sun through 1 inch of liquid.
Jane D. Stanton
- Vienna, (The Coffee City), Austria
Q. Thank you,
this is a good discussion about the plating of aluminum.
Most of the books that talk about aluminum plating recommend first zincating the aluminum; I think two zincates is very good, but first one needs to desmut using HNO3.
In my country it's hard to find nitric acid so, is there an alternative desmut not using HNO3?
- amman jordan
December 20, 2020
A. Hi Qwee. This is a very interesting question, not just with regard to double zincating (which is addressed many times on this site, notably as topic 4074), and as a desmutter for copper-bearing alloys, but because nitric acid & nitrates have many other uses in metal finishing as well. I hope to hear some good suggestions for your problem!
![]() |
The reason for the bans is probably because it can be used in explosive-making and meth-cooking and other bad stuff. So, more expensive, more environmentally harmful substitutes will surely be found for the rest of us as nitric acid grows harder to get. ![]() |
Luck & Regards,
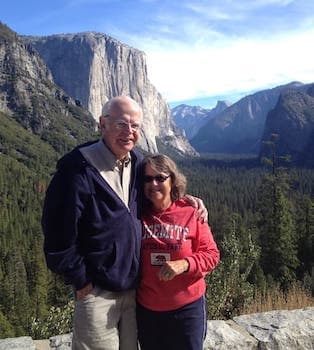
Ted Mooney, P.E. RET
Striving to live Aloha
finishing.com - Pine Beach, New Jersey
Q. Dear sir, I have tried to coat interior of hemisphere of silicon-based aluminium alloy. I have used auxiliary anodes. My requirement was about 100 micron copper layer. I use alkaline cleaning, etching, double zincating, cyanide strike then acid copper coating. There appeared blisters in lower half of my piece. Please guide how can I get rid of this issue. Thanks
Dr. Irfan- Islamabad Pakistan
May 24, 2021
Q. I am interested in plating some diecast aluminum car parts.
I have been watching videos on the specifics of aluminum. I think I understand the zincating, but I am unclear on another step.
The video I have been looking at has these parts:
1. zincate - rinse
2. copper strike - rinse
3 electroform acid copper
I see the formulas for the acid copper solution online, but I can't find anything for the "copper strike"
What is the difference?
Is it simply the same solution, minus the acid?
I made some copper solution by adding pure copper to a heated 50/50 mix of peroxide and vinegar
⇦in bulk on
eBay
or
Amazon [affil links] . It worked well for adding a fast thin layer of copper. Could this be used to "strike" the part after zincating?
Obviously I am not a professional
- Los Angeles, California
January 13, 2022
A. Hi Paul. I have never heard of a plating solution comprised of copper, peroxide, and vinegar ... but I'm not going to say it won't work, especially when you are saying that you've done it. If it works on zincated aluminum, yea!
From dealing with thousands of hobbyist plating situations here over the years, I think that, second only to considering the safety of what you are doing, the single most important piece of advice I can offer is to practice and learn on scrap. If your peroxide-vinegar solution appears to work, go ahead and apply it to a piece of scrap and then try to plate heavy copper onto it. Don't ruin your hard-to-replace car parts. Only after you are successfully plating onto scrap should you expose precious parts to these experimental solutions.
As a matter of semantics and common usage, the word 'electroforming' is wrong: you are 'electroplating'. It's called electroforming if the plated layer is an object of its own rather than being a plated layer on an object. If you were making hollow gold earrings by plating onto wax then melting the wax away, or bellows by plating onto aluminum and dissolving the aluminum away, or plating onto a leaf or flower, that would be electroforming.
Luck & Regards,
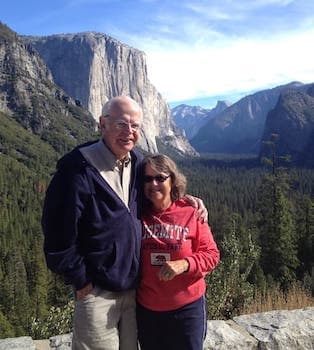
Ted Mooney, P.E. RET
Striving to live Aloha
finishing.com - Pine Beach, New Jersey
Q, A, or Comment on THIS thread -or- Start a NEW Thread