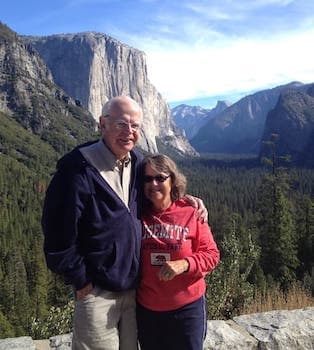
Curated with aloha by
Ted Mooney, P.E. RET
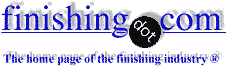
The authoritative public forum
for Metal Finishing 1989-2025
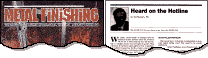
Thread 04/49
Direct Metallization on ABS
ABS = Acrylonitrile Butadiene Styrene, a type of plastic especially well suited to plating onto (more later).
What does "electroless plating" mean? It probably doesn't mean quite what you think if you are new to this field :-)
To regular practitioners in this field it doesn't mean any & all plating which occurs without electricity; rather it is shorthand or lingo for one specific type: "autocatalytic" plating, so let's explain ...
Many people have seen back in science class or elsewhere that a nail will acquire a copper-colored coating when immersed in a solution of blue copper sulphate, even with no electricity applied. In an environmentally less enlightened age, scrap automobiles were sometimes placed in steams downstream of chemical plants to remove copper from the water in a similar way. You can similarly coat copper with silver, silver with gold, aluminum with zinc, etc. What happens is the more noble metal is able to steal electrons from the less noble one. In the first example the copper ions (ions are atoms which have been stripped of one or more of their electrons and therefore are dissolved in solution rather than in metallic form) steal electrons from the iron in the nail, and having acquired them become metal atoms whereas the iron atoms from which the electrons were stolen dissolve into the solution as ions. Professionals therefore call this "displacement plating" or an "immersion deposit".
One of the limitations of displacement plating is extreme thinness of the coating ... once there is a very thin layer of copper, the solution is no longer touching any iron so the reaction fizzles to nothing. Contrarily, in what we call a 'catalytic reaction' the presence of some catalyst is required for the reaction to occur. For example, in electroless nickel plating the solution is 'spring loaded' with a reducing agent like hypophosphite which will supply any electrons needed to reduce dissolved nickel ions to metallic nickel atoms if a catalyst like iron is present. "Autocatalytic" means that the nickel metal itself is also a catalyst for the reaction, so even after the iron is completely covered, the nickel serves as a catalyst and the reaction will continue until the solution runs out of nickel or hypophosphite (or the parts are pulled out).
Back to ABS: this plastic has properties making it well suited for 'plating on plastic', like the grills of most automobiles. Probably it's most essential characteristic is that the butadiene is present as tiny balls dispersed in the plastic which can be dissolved in acids, leaving millions of small semi-spherical holes into which plating can grow for outstanding adhesion of the plating.
UPDATE 2014 "Direct Metallization"
There are numerous ways to metallize non-conductive materials for electroplating, including simply painting them with a conductive paint, and then electroplating the paint. Most of those methods are mentioned in our FAQ "How do you electroplate flowers, leaves, animal skulls, and other organic materials?"
But traditionally -- until about 1996 or so -- there was only one method which offered sufficient adhesion and reliability for difficult industrial applications like nickel-chrome plating of exterior automotive components or metallizing the "thru-holes" that connect the layers in circuit boards. That method is generally known as "electroless plating" and it is quite complicated; it involves applying a layer of palladium and tin "seeds" to infiltrate the nooks and crannies of the plastic surface, then immersing the surface into autocatalytic (electroless) copper or nickel -- which causes the copper or nickel to begin plating on the seeds, and then build from there to cover the whole surface with copper or nickel -- which can subsequently be electroplated.
In addition to the complexity of this electroless copper or electroless nickel approach, the waste from the process solutions is difficult to treat, so other approaches which would offer the same or better adhesion and reliability have long been sought.
Beginning in about 1996, good techniques began to be developed to apply graphite based processes or conductive polymers to the plastic, which could subsequently be reliably directly electroplated without the intermediate electroless plating layer. Several presentations on the subject were offered at Interfinish '96, AESF Week '96, SurFin '96, and Sur/Fin '97. The process is now called "direct metallization", and rapidly grew in popularity. All major suppliers of plating process chemistry presently offer direct metallization systems.
Historical postings on this topic, oldest first
1996Q. Does anybody hear any news about direct metallization on ABS and ABS/blended polymer ? How does it compare with conventional plating on plastics ?
Best Regards,
publicly reply to Ricks W. Lambert
A. Ricks, What does that term "direct metallization" mean to you? You can't plate plastics without some form of "metallization" onto the plastics before actual plating. We use silver nitrate
⇦ this on
eBay or
Amazon [affil links]
to "metallize" the ABS before plating.
Sincerely,
- Rhode Island
1996
publicly reply to David Guleserian
1996
A. Dear Ricks,
About a year ago I've done a large process design project for electroless (autocatalytic) plating on ABS and some other plastics. Almost any "metallization" can be done after pretreatment. I found it to work the best coupled with plasma etch.
If you need some more info, please let me know.
publicly reply to Dr. Ilya E.Popeko
A. Ricks, I agree, you must describe what you mean by: "Direct Metallization." ABS is easily metallized via Electroless Ni after providing Pd nuclei via standard processes. Alternatively, you can Vapor Deposit a Ni thin film then coat with E'less Ni although adhesion is not as good as the Pd route.
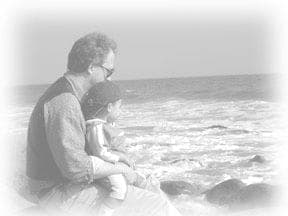
Dave Kinghorn
Chemical Engineer
SUNNYvale, California
1996
publicly reply to Dave Kinghorn
by American Society for Electroplated Plastics
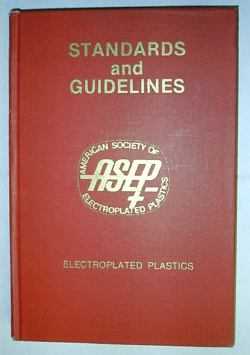
on AbeBooks
or eBay or
Amazon
(affil links)
A. Dear Ricks,
There is a new system on the market for plating directly on ABS and ABS-PC substrates. The difference to conventional plating technologies is that this process does not require any electroless metallization (e.g., copper or nickel). The first metal layer is directly plated acid copper. The ABS substrates are treated to achieve an electrical conductivity on the surface. This conductivity is good enough to start directly with electroplating of copper.
Best regards
- Germany
1998
publicly reply to Stephan Hempelmann
1998
A. Ricks & fellow tank jockeys:
I have recently undergone a baptism by fire on all current direct metallization processes. Here is what I have learned: Direct metallization was developed for the printed circuit industry as an alternative to E'less Copper to get rid of the "allegedly" toxic formaldehyde used as the reducing agent in E'less Cu. Direct Metallization ("DM" from now on) is used to metallize through-holes and blind vias so that a conductor is present on the thru-hole ("TH") surface and now the TH can be electroplated with normal current-driven plating processes. Electroless Cu was used previously for this step. It is still widely in use in many shops as there are pitfalls in the usage of the various DM processes which must be balanced from a production point of view against the usage of the more robust Electroless Cu from the environmental point of view.
DM process GENERALLY fall into two classes: 1. Those that deposit Carbon as the conductor onto the non-conductor that you wish to render conductive, and 2. those that deposit metals. Of the metal depositing process, Palladium is the favorite. Some deposit it as finely dispersed pure palladium clusters, and others deposit it from colloidal forms. One process subsequently converts deposited Pd into the semiconductor PdS, while others build "mounds" of Pd, while still others build interconnected Pd cluster networks. Common to all processes is that when exposing your workpiece to the DM, the conductors and non conductors alike get DM. Then expose the workpiece to an etchant to back etch the conductors through the DM layer to remove the DM from the metallic conductors while leaving the DM on the nonconductors. This enhances bond strength of subsequently electroplated layers to the Cu or whatever conductors are used. The DM layer on the non-conductors remains since there is no conductor underneath it being attacked by the etchant. Then electroplate. Works great every time.
DM processes GENERALLY have the following properties: 1. Carbon DM: Adhesion is poor, but process control is unreasonably simple. Seriously. Just pour it then walk away. Come back in a few months and pour some more. 2. Pd DM: Adhesion can approach that of E'less Cu, but process control is complex and involved. They are both expensive. And they are both messy.
With regards to ABS etc, all DM will work but ABS has a long successful history of metallization by standard Sn/Pd. Only reason to change is to get rid of the chromic acid etch step, but it will still required on all DM processes if you want to maintain adhesion strengths (although vendors may deny this).
Hope this (late) info helps out. Contact me for details if you are still interested.
Regards,
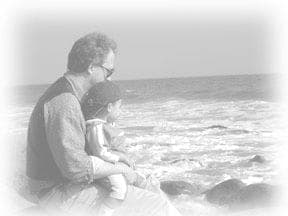
Dave Kinghorn
Chemical Engineer
SUNNYvale, California
publicly reply to Dave Kinghorn
A. Dave gave a comprehensive explanation on DM. It works fine for PCB and ABS. On ABS blends and on geometrically complicated parts there are some difficulties so Pb/Sn is still the most reliable process.


Sara Michaeli
Tel-Aviv-Yafo, Israel
1998
publicly reply to Sara Michaeli
A. According to my experience, the two methods David K. mentioned are usually used in PCB (Printed circuit board), for the through hole metallization. Actually, conductive polymer is also widely used for the direct metallization for PCB.
But for the metallization of ABS substrate, excellent conductivity is needed. All the three methods used for PCB, e.g.. black carbon, PdS and the conductive polymer cannot meet the requirement of ABS.
The direct metallization used for the ABS is colloid Pd followed by copper replacement reaction, which could provide good conductivity for further metallization, like acid copper plating. No electroless Nickel or electroless copper is needed for this Direct Plating process.
For David G: how can you use silver nitrate to "metallize" the ABS before plating? How to conduct?
Kevin Zhu- Shenzhen, Guangdong Province, China
February 18, 2009
publicly reply to Kevin Zhu
Hi Kevin. David G. is referring to something like the Brashear process, similar to how mirrors are made: a two-gun system applies silver nitrate and a reducing agent to deposit a thin film of conductive silver metal. This process was very widely used in vinyl record manufacturing to metallize the lacquer master. To my knowledge it has no applicability to printed circuit boards though.
Regards,
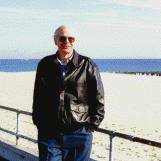
Ted Mooney, P.E.
Striving to live Aloha
finishing.com - Pine Beach, New Jersey
publicly reply to Ted Mooney
Can't fill 20-25 µm Plated Thru Hole
Q. I am a process engineer of copper plating line and we are currently encountering voids on filling the Plating Through Hole (PTH) with 25 µm top diameter and 20 µm bottom diameter with 50 µm thickness of Polyimide (PI). The material to be plated is 4 µm Cu / 50 µm PI / 4 µm Cu in terms of thickness. We have metallization process prior electrolytic copper plating. The machine we are using for Copper plating is vertical plating and we have separate control on the current for the left and right side. We have tried using a low current density to slowly fill the PTH but still voids is encountered.We have also tried closing the small diameter first by applying current on small diameter side only using low current density and then reversing te orientation on the bigger diameter side still using low current density but still voids were encountered. Since this product is new to us and I am also new in copper plating , Can anyone help me on how to fill this PTH with copper without voids? Thanks a lot...
Meredith DelfinadoSubstrate Manufacturing - Philippines
2006
publicly reply to Meredith Delfinado
A. Pare,
Perhaps you could describe the exact voiding you are observing. Do you see interrupted plating down inside the via? For example incomplete sidewall coverage? Or does the entire via fail to plate? These may have different root cause. 25 micron diameter is a VERY unusually small dia. via in a 4/50/4 micron PI substrate. Are you just blasting right thru the metal & PI together with a YAG or Eximer? My first suspicion would be failure of the Direct Metal Process (or sputter) to properly cover the sidewalls. Direct Metal processes all have unique process windows that you need to determine by experiment for that very small via you are trying to process. And these DM processes RARELY operate at high yield at the manufacturer's recommended parameters. You need to find your own optimum. My second guess would be the photoresist or laser slag not well developed or cleaned out of the via prior to DM, and this presents a loose fragmented surface for the DM to deposit onto and as result the crevices present are problematic to the DM & Plating process.
Hope it helps, Pare
Manong Dave
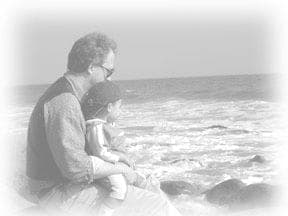
Dave Kinghorn
Chemical Engineer
SUNNYvale, California
2006
publicly reply to Dave Kinghorn
Update: What is the best metallization for ABS today?
Q. I wanted to know the best metallization process for ABS plastics. Also its feasibility in today's world. And will the metallization process affect the properties of the plastic in any way?
RAMEEZ MALIKNational Institute of Technology - ROURKELA, ODISHA, India
January 31, 2014
publicly reply to RAMEEZ MALIK
A. Hi Rameez. Although this thread includes some old postings, I think it's still useful.
But there is no such thing as "best" or there would not be multiple approaches. If you mean what is the most robust process, I think automakers are still using the old traditional chromic-sulfuric etch, followed by Pd/Sn seeding, followed by electroless nickel plating before copper-nickel-chrome for exterior automotive parts.
Yes, the process affects the properties of the ABS, turning the surface spongy, followed by metallic ... but I think the ABS retains good mechanical properties. Good luck.
Regards,
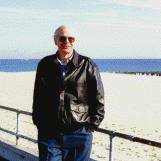
Ted Mooney, P.E.
Striving to live Aloha
finishing.com - Pine Beach, New Jersey
January 2014
publicly reply to Ted Mooney
Q. Thanks Ted. There is still one more question that I'd like you to answer. I have heard that plasma etching is a good metallization process for ABS plastic as it does not wear off with time. Do you have any idea regarding this? And since I will be experimenting on the plastic after metallizing it, changing of the properties is a concern.
RAMEEZ MALIK [returning]National Institute of Technology - Rourkela, Odisha, India
February 3, 2014
publicly reply to RAMEEZ MALIK
A. Hi Rameez. I was under the impression that "plasma etching" was an alternative to chromic-sulfuric etching to roughen the surface. Although a lot of plastic is vacuum metallized, even down to mylar party balloons, my understanding of vacuum processes is limited to book knowledge.
Still, as I say, for the most robust application, automotive exteriors, I don't think OEMs use vacuum processes in lieu of the palladium seeding and copper-nickel-chrome electroplating. And I do remember several messes the automotive industry got themselves into in their eternal lust to replace expensive copper-nickel-chrome electroplating with vacuum processes.
Regards,
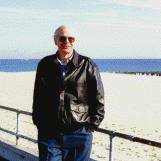
Ted Mooney, P.E.
Striving to live Aloha
finishing.com - Pine Beach, New Jersey
February 2014
publicly reply to Ted Mooney
A. Hello,
The problem with plasma etching is that you do not get any polarity at the plastic surface.
Etching has two objectives:
1. To make the oxidation of butadiene
2. To make the surface hydrophilic, because the surface of plastic is hydrophobic.
Plasma etching does NOT make the plastic hydrophilic.
- Oradea, Romania
April 4, 2014
publicly reply to Vlad Manta
Alternate to Electroless Nickel for Plating on Plastics
Q. Hi all,
I am searching for alternate to electroless nickel plating on ABS plastics.
At present process is etching, PdCl2 activation, electroless nickel plating, copper plating, nickel plating and last chrome.
I am searching alternate to electroless nickel.
- Mumbai, India
August 20, 2019
publicly reply to Vishal Shah
A. Hi Vishal. I assume you are not simply talking about replacing electroless nickel with electroless copper, but you want to consider direct metallization technology. So we added your inquiry to one of several threads about this.
You may also be interested in topic 46403 and topic 10887. Good luck.
Regards,
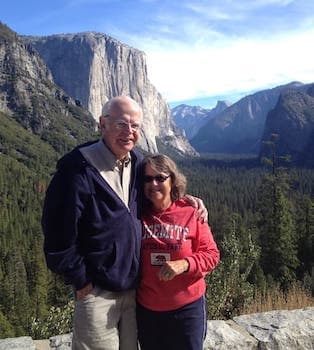
Ted Mooney, P.E. RET
Striving to live Aloha
finishing.com - Pine Beach, New Jersey
August 2019
publicly reply to Ted Mooney
Q, A, or Comment on THIS thread -or- Start a NEW Thread