"Finishing Technology Hotline BBS" Postings by Topic
Ed. note: before the internet existed, there was a time when "Sysops" (system operators) ran publics forums via dial-up modems and "BBS" (Bulletin Board System) software. Here is one such discussion from 1993.
Chromate Conversion Coatings
--------------------
Msg. #3831 in ** Ask Plater B**
Posted on 04/20/93 at 23:00:56
To: ALL From: KEN ROSENBLUM
- yellow chromate Does anyone control yellow chromates (cyanide zinc line) from the laboratory. Currently, the operator makes additions based on the color of the work as it comes out of the chromate tank. However, when running three shifts (it is a hand line), confusion develops. When the operator starts his shift, he never knows how strong the chromate is until he has run his first round. There is an analytical method, but as the chromate ages, the chromate strength does not correlate with the strength of color on the zinc plated parts. Thanks,.......Ken
--------------------
Msg. #3833 in ** Ask Plater B**
Posted on 04/21/93 at 07:36:07
To: KEN ROSENBLUM From: BERL STEIN
- Reply To 'yellow chromate'
Ken, if you have to make frequent additions to the bath, your operators are probably dragging in too much solution in it. That can be helped in several ways, including a more stable double-dip chromate bath. As far as assessing the performance of an aged bath
- nothing is better than a set of test parts you run through it, after all you're not interested so much in the chromate concentration, you want to know if the bath performs, which depends on a number of variables including the contamination level. Plater B
--------------------
Msg. #3846 in ** Ask Plater B**
Posted on 04/25/93 at 22:04:29
To: BERL STEIN From: KEN ROSENBLUM
- Reply To 'yellow chromate'
What is a double dip chromate? We only use single dip chromates. Are they commonly used? Thanks,,,,Ken
--------------------
Msg. #3848 in ** Ask Plater B**
Posted on 04/25/93 at 22:49:48
To: KEN ROSENBLUM From: BERL STEIN
- Reply To 'yellow chromate'
Ken, a double dip chromate isn't particularly common, but is used occasionally to extend bath service life and give a more consistent color. The idea is to have a higher concentration of acting ingredients in the first bath, which brightens up the deposit by somewhat polishing it, and maintaining the second one at a low level, mainly through dragin from the first one. This second stage serves for color development. One such composition was developed by my brother in Russia some time ago and was awarded a Russian patent. He used it on his zincate plating line, they probably still continue using it to this day, except my brother is plating something else these days in Montreal, P.Q. Cheers, PLater B
--------------------
Msg. #5388 in ** Ask Plater B**
Posted on 07/15/94 at 20:51:00
To: ALL From: TED MOONEY
- Fading black chromate. One of my clients recently installed a good size automatic plating line with alkaline zinc, and silver-based black chromate. The chromate looks excellent when shipped: glossy dark black. BUt within 2 to 3 weeks it fades to an olive or brown color. They are not neophytes in plating or black chromating and are quite puzzled. My suggestion was unracking some parts after plating, and chromating them on their manual lines; and plating some parts on their manual line, then chromating them on the automatic to see if a clear assignment of the problem can be made to the chromate solution or plating solution. Has anybody seen a similar problem?
--------------------
Msg. #5400 in ** Ask Plater B**
Posted on 07/22/94 at 08:14:18
To: TED MOONEY From: STEVE RUDY
- Reply To 'Fading black chromate.'
There are some general reasons for this problem. First and commonly is the silver content being under concentrated. Next look at the quality of rinsing before and after the chromate. It's important to consider quality of the water used. Specifically does it contain chlorides, which readily complex the silver. Also what is the metallic contamination level of the zinc and chromate baths? Copper would initially enhance black color of the chromate then fade into a brown colored film. Low silver or chloride s would affect the chromate by inducing iridescence. Light induced discoloration is also common. Specifically the oxidative action of sunlight on the chromate film. I hope these areas will assist in correcting the problem SFR
--------------------
Msg. #5834 in ** Ask Plater B**
Posted on 12/08/94 at 08:06:34
To: ALL From: GORDY SEPPANEN
- Zinc Chromate Coating I am searching for a coating to apply to black chromated zinc to prevent dehydration of the chromate during baking. My customer has a part which requires at least one bake at 200 degrees F and a vacuum bake at 160 degrees which discolors the chromate. The original coating was cadmium and was switched to zinc for long term availability. The chromate was switched at the same time from clear to black because they had discovered that low light reflection was needed. Zinc is preferred because the base material is an iron alloy and corrosion protection by a sacrificial coatings is very desirable. Painting with a black powder coating worked but was labor intensive due to masking. Plating Al by IVD methods were considered but thought to be too expensive. The intent with Al was to hardcoat the Al after deposition. The customer considers most other coating choices which result in an acceptable black surface as insufficient corrosion protection. The 200 degree bake is for 2.5 hour and the vacuum bake is for 8 to 16 hours
--------------------
Msg. #5837 in ** Ask Plater B**
Posted on 12/08/94 at 08:56:33
To: GORDY SEPPANEN From: TED MOONEY
- Reply To 'Zinc Chromate Coating'
Easier said than done, I know, there are logistic problems, butÑ-- The thing to do, I've heard, is to zinc plate and bake the parts, THEN chromate them.
--------------------
Msg. #5840 in ** Ask Plater B**
Posted on 12/08/94 at 12:10:53
To: TED MOONEY From: GORDY SEPPANEN
- Reply To 'Zinc Chromate Coating'
That is a good suggestion but unacceptable because at the time of baking the part is filled with an electronic assembly. I cannot think of a way we could dip the part without some risk, plus at that time the interior would be unchromated zinc.
--------------------
Msg. #5864 in ** Ask Plater B**
Posted on 12/11/94 at 21:06:20
To: GORDY SEPPANEN From: KEN ROSENBLUM
- Reply To 'Zinc Chromate Coating'
Why does the part need to be baked?
--------------------
Msg. #5866 in ** Ask Plater B**
Posted on 12/11/94 at 21:11:48
To: GORDY SEPPANEN From: KEN ROSENBLUM
- Reply To 'Zinc Chromate Coating'
There might be a lacquer that could be applied after black chromate that would prevent oxidation of the black chromate that is causing the change in color.
--------------------
Msg. #5875 in ** Ask Plater B**
Posted on 12/12/94 at 13:53:39
To: KEN ROSENBLUM From: GORDY SEPPANEN
- Reply To 'Zinc Chromate Coating'
The interior electronics need to be moisture free prior to sealing the package.
--------------------
Msg. #5906 in ** Ask Plater B**
Posted on 12/15/94 at 10:27:36
To: BERL STEIN From: RON LANDRETTE
- Reply To 'BAKED chromate'
I once ran a cad line with qqp416 spec plate,the chromate used to look real nice till bake and then took on a chalky dark green color with variations to the finish. THIS WAS CONSIDERED NORMAL. I would expect that any company requesting a baked chromate would expect the baked finish
--------------------
Msg. #5915 in ** Ask Plater B**
Posted on 12/15/94 at 22:48:04
To: RON LANDRETTE From: KEN ROSENBLUM
- Reply To 'BAKED chromate'
According to QQ-P-416, chromate should take place after baking.
--------------------
Msg. #5939 in ** Ask Plater B**
Posted on 12/19/94 at 14:15:29
To: KEN ROSENBLUM From: RON LANDRETTE
- Reply To 'BAKED chromate'
CHROMATE after bake? hmmm well,I couldn't tell you on that,I was a line operator in those days taking orders from my boss. We would nickel cad plate with olive drab chromate,then bake, the chromate after plate sure would have left the parts a lot nicer looking
--------------------
Msg. #5945 in ** Ask Plater B**
Posted on 12/19/94 at 21:46:59
To: RON LANDRETTE From: KEN ROSENBLUM
- Reply To 'BAKED chromate'
Chromate after baking also gives much better corrosion protection. The heat breaks down chromates.
--------------------
Msg. #5949 in ** Ask Plater B**
Posted on 12/20/94 at 13:52:53
To: KEN ROSENBLUM From: RON LANDRETTE
- Reply To 'BAKED chromate'
well,i was sure there was a reason,just didn't remember what it was
--------------------
Msg. #6617 in ** Ask Plater B**
Posted on 06/30/95 at 07:39:45
To: ALL From: TED MOONEY
- Testing MIL-C-5541 Chromate I am looking for information on chemical conversion coatings on aluminum and aluminum alloys. The issue that is in question is the MIL-C-5541E Military specification requirement to verify class 3 chemical conversion coatings by running an electrical resistance test per MIL-C-81706. This procedure involves applying an electrode pressure of 200 psi to the coating and measuring for
< 5000 microhms per square inch. Our company wants to find a test method that can verify compliance of our stock of parts without elaborate (costly) test setups. If you can help, it would be greatly appreciated. [a caller from an aerospace company on the Internet]
--------------------
Msg. #6635 in ** Ask Plater B**
Posted on 07/07/95 at 11:03:58
To: TED MOONEY From: RON LANDRETTE
- Reply To 'Testing MIL-C-5541 chromate'
An average tool shop could supply a jig for the 200 psi spec using an air cylinder,or a torque wrench style assembly set for 200 # a clarification would be required on the electrode style required to meet the mil spec. lastly,finding a meter that can measure 5000 microhms will be a feat in itself. this will likely be the most costly part of your "test assembly"" you might want to check with a company called "Dermitron" they produce test equipment,very simple to use, that test coating thicknesses for plating. the "resistance" measurement is very similar in principle to their std equipment and they may be able to produce something along these lines
--------------------
Back to finishing.com Home Page 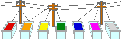