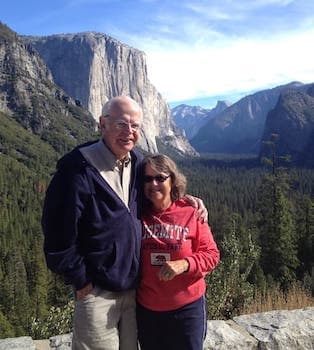
Curated with aloha by
Ted Mooney, P.E. RET
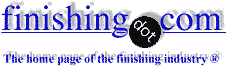
The authoritative public forum
for Metal Finishing 1989-2025
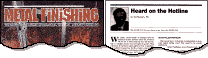
-----
How to do Nickel plating on an oxide surface
We have been trying, somewhat unsuccessfully, to plate the inside diameter of a cylinder of 304 L stainless steel that has an oxide coating (about 1 micron thick) on it. We are interested in measuring the thickness of the oxide, so we want to plate over it to preserve the thickness during subsequent preparation for viewing in a Scanning Electron Microscope (SEM). The preparation involves encapsulating the specimen in a two part room temperature curing epoxy, then grinding and polishing the surface to a sub-micron finish. What we end up with is a cross-section of the original part where we can view the oxide coating. I have tried electroless nickel coating the sample, but had no luck. I then tried applying a few hundred angstroms of AuPd to the surface and electroless nickel plating on that. I got a very nice 10 micron thick nickel plating on the part, but it blistered severely, leaving an undesirable gap between the nickel plating and the oxide layer of interest.
I am trying to find a way to plate these parts without destroying the oxide layer, and get good adhesion of the nickel to the inside diameter of our parts.
Alice K. [last name deleted for privacy by Editor]- Albuquerque, New Mexico, USA
2001
Plating on an oxide is a situation that most platers try to avoid with adequate pretreatment. An approach that may work with your particular problem is to treat the oxided surface as a plater would do for plastics. The object/surface is coated with a conductive coating; like lacquer and a powdered metal (palladium I think). Then a nickel strike and finally electroless plated to desired thickness. The lacquer is the actual bonding agent, but if the whole item is encapsulated with this process the epoxy solvents may not be able to dissolve the lacquer layer. Check w/companies that plate plastic bumpers for autos for the chemicals used in their process.
Daniel H. [last name deleted for privacy by Editor]- Sarasota, Florida, USA
2001
Have you tried using electroless copper over your oxide coating? Silver conductive paint is also an interesting possibility. I expect you have access to these coatings there at the lab but if not I may be able to help.
Neil BellAlbuquerque, New Mexico
2001
Q, A, or Comment on THIS thread -or- Start a NEW Thread