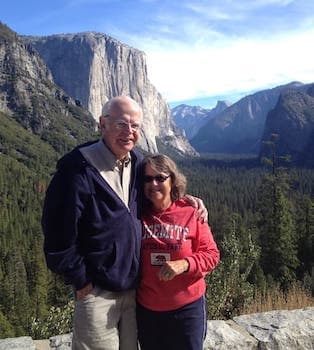
Curated with aloha by
Ted Mooney, P.E. RET
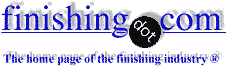
The authoritative public forum
for Metal Finishing 1989-2025
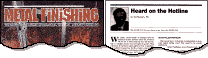
-----
Help in making aluminum mirrors by vacuum coating
2001
Hi, all:
I need some help/suggestions on making aluminum mirrors by vacuum coating.
My problem is: the adhesion is not good enough, the aluminum layer does not survive the tape peeling test.
My running conditions are:
--Pressure: around 10^-5
--temperature: around 30 C
--Al thickness: 500 A
I do have oil backstreaming to the chamber from the diffusion pump since we do not have a cold trap there. So, does any of my friends have any ideas of what the adhesion problem is?
Any input/suggestions/responses are highly appreciated.
Thanks in advance.
Charlie Smith- Texas
I'm not surprised that you have poor adhesion. To get good adhesion you need to deposit on a very clean surface. One good step would be to add a water-cooled baffle between the pump and the chamber. You can also help if you bombard the substrate with ions both before and during the deposition. Ion bombardment at energies around 1 keV before the deposition will sputter away contaminants; during the deposition, ion bombardment densifies the coating and mixes the interface (ion peening). If your substrate is a conductor, you can use a negative bias to create a glow discharge (you'll need to backfill with argon gas to 3-10 mtorr). An alternative is to use an ion beam, if the geometry permits. The ion beam is needed if your substrate is an insulator.
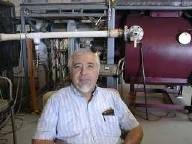
Jim Treglio - scwineryreview.com
PVD Consultant & Wine Lover
San Diego, California
2001
Jim:
Thank you very much for your reply. I definitely will need the cold trap there. Thanks for all your advice.
One more thing, if possible: when making aluminum mirror, what would be the thickness of aluminum? I have seen records of 1000nm of aluminum being used, while I was using 70 nm. A friend told me that 70nm is too thin. What would you suggest?
Once again, thank you in advance for any more advice.
Charlie Smith- Texas
2001
Q, A, or Comment on THIS thread -or- Start a NEW Thread