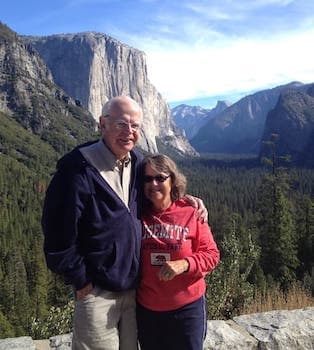
Curated with aloha by
Ted Mooney, P.E. RET
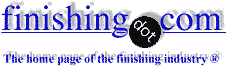
The authoritative public forum
for Metal Finishing 1989-2025
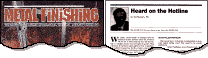
Thread 98/83
Ammoniacal leaching process for waste F006 sludge
2001
I am writing on behalf of the EPA's Small Business Innovative Research (SBIR) grant program (I am a contractor to that program). One of the companies receiving an EPA grant is trying to develop an ammoniacal leaching process to remove metals (specifically Copper, Zinc, Nickel, Cobalt, and Cadmium) from hydroxide sludges, or F006 wastes, which typically come from plating shop waste water treatment processes. I am trying to determine whether the plating or finishing industry would be interested in a technology that could remove these metals from the sludge onsite. The benefits could be reduced sludge volume, reduced sludge toxicity, and potentially improved value of the reclaimed metal. I am trying to determine what, in particular, needs would have to be met in order for this technology to be adopted. For example, not increase waste volumes, pay for itself in X years, not increase regulatory burden, or significantly reduce regulatory burden, etc.
Any insights you might have would be helpful for this company, since they believe the plating and finishing industry could benefit from this technology.
Thanks for your time.
Lisa Dufresne- New Bedford, Massachusetts
publicly reply to Lisa Dufresne
2001
Ooh, boy; now you've gone and done it, Lisa! You've presented an inquiry which asks some interesting technical and commercial questions, but which is couched in a way to offer everyone in the metal finishing industry the perfect opening to rail against everything about the EPA :-)
In the abstract, ammoniacal leaching sounds interesting and a potentially nice way to recover rather than landfill valuable metals, but here are some of the, ahem, "roadblocks" to introduction of that technology:
1. Platers have been arrested for at little as putting a steam coil into a tank of waste to reduce its volume. Until Pres. Bush personally appears on TV to announce that it's okay, a plater would have to be certifiably loony to try to recover metal from his F006 sludge.
2. "Reduced sludge toxicity" is a nebulous term which, in this age of joint and several liability for waste, offers zero economic incentive. If a plater has any money, and any of his waste is in a landfill, he is responsible for the cost of cleaning up everybody else's waste. Why on earth would he spend money to reduce the toxicity of the stuff he puts in when he has no control over the other 99.999 percent of the waste?
3. Regarding "reduced sludge volume", most plating shops are very interested in keeping the metal content of their sludge up, not down, so that they can find someone who will promise to recycle it, thus relieving them of eternal responsibility for it. Again, a plater would be crazy to separate his sludge into recyclable vs. land fillable if he has any possibility whatsoever of sending all of it to a recycler even at high cost. Some shops deliberately try to not reduce their dragout because the metal content of their sludges barely hovers on the border of recyclable. In the upside down world of current law and regulation, reducing waste can be a disaster.
4. I have personally never seen a single technology successfully developed for the metal finishing industry through these SBIR projects, and consider it all to be paper-pushing makework for grant mills -- so an SBIR is the last place I and some others would look for a real-world solution. But please prove us wrong: as long as the tax money is being spent anyway, we'll be watching to see when ammoniacal leaching becomes a practical recovery technology for plating shops :-)
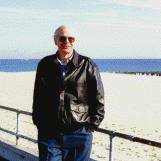
Ted Mooney, P.E.
Striving to live Aloha
finishing.com - Pine Beach, New Jersey
publicly reply to Ted Mooney
2001
This is an interesting theory, but has not been applied well in practice, even in the mining industry. Most metals do not form soluble complexes with ammonia, so its hard to consider it as a useful tool in reducing sludge volumes. Most mines use sulfuric acid for leaching ore that I am aware of, which is a significant step up from using cyanide. The use of ammonia ⇦ this on eBay or Amazon [affil links] has been looked at to separate copper from other heavy metals as a means of coarse purification, however it is beset by drawbacks - none the worse that the removal of metals from these ammonia leach solutions is by liquid ion exchange solutions. These LIX solutions are then mixed in a sulfuric acid solution, and the metals are stripped back out into the acid, and electrowon from the acid. Its a neat process, but it also makes lots of organic waste by-products - and sludge.
Also, the reduction of nitrogen (i.e. ammonia) has been an emphasis for the last several years, especially with the advent of TRI (toxicity release inventory). So why in gods green earth would anyone think that an ammonia leaching process would work on a mixed metal goop like F006 sludge? More than that, why would anyone fund it?
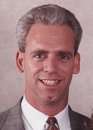
Tom Baker
wastewater treatment specialist - Warminster, Pennsylvania
publicly reply to Tom Baker
2001
I appreciate all of your responses, and you bring up some great points (I will not be addressing the question of who would fund it, however...):)
The EPA funded the research into the technology, and metal plating sludge was one of the applications that the company chose to pursue (mining was another possibility). It has become clear, from your postings and my research, that there are hurdles to overcome. However, what if this technology were used at a central location, where smaller companies could send their sludge rather than sending it to a smelter? Would it make more sense to look at this technology as an alternative to smelting, and let whomever licenses the technology worry about running the process as a recovery business?
Thanks!
Lisa Dufresne- New Bedford, Massachusetts
publicly reply to Lisa Dufresne
I think so.
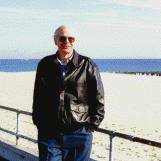
Ted Mooney, P.E.
Striving to live Aloha
finishing.com - Pine Beach, New Jersey
2001
publicly reply to Ted Mooney
2001
Hello,
I just wanted to reply to the comments in the previous posts. It turns out that I am the person doing the SBIR project Lisa mentioned - I just stumbled across this doing a web search.
I am very much interested to hear these comments. In my own defense, however I have to say however that the real focus of this work is the mining industry, primarily (but not exclusively) related to metals recovery from sludges produced from treatment of acid mine drainage. If you don't know, AMD is produced by oxidation of disturbed sulfide rock, consisting of dilute sulfuric acid and metals leached into solution. It's probably the number one environmental problem facing mining companies these days, all over the world. Generally when AMD starts it cannot be stopped, and there are many companies faced with treatment of large volumes of water literally forever. They generally use lime since it is cheap, and not only removes metals but reduces sulphate considerably as gypsum.
AMD in the eastern U.S. usually contains only iron and aluminum and maybe manganese as major contaminants. In the western U.S. and many places in the world, it contains a much wider variety of more valuable metals, including those forming strong complexes with ammonia (Cu, Ni, etc.). What I'm really trying to do is come up with a process to recover metals from those sludges, not really electroplating sludges so much. Lisa, the original poster, was contracted by EPA to help with commercialization work (a little premature in my opinion but that's EPA for you). Since she was unfamiliar with the mining industry but had some experience with electroplating, I asked her to focus on electroplating and I would handle the rest.
Note that ammoniacal leaching of sludges is not a new idea. It was examined in the '70s and '80s by a few people (these were electroplating sludges) but recoveries were disappointing. I had done some research in the last few years while getting a graduate degree that showed that better recoveries could be seen by doing some redox-related things during leaching. In addition, many new solvent extraction reagents have been developed since the '70s, some specifically for metals separation from ammoniacal solutions (note that solvent extraction does not result in alot of organic waste as one poster said, and note also that SX is becoming more and more widely used - about one third of the world's copper is produced by the heap leach/SX/electrowinning route). These two items were the basis for the SBIR proposal.
Also note that ammoniacal leaching is pretty old and proven technology in the mining industry, having been used for over 80 years, mostly for copper recovery (either metallic copper or copper sulfide with oxidation) but also for nickel and cobalt recovery (after reduction roast, with oxidation). The selectivity it provides over other metals is exactly why it has been used. In fact, as far as hydroxide sludges, there is a big Australian nickel/cobalt project (the Cawse project owned by Centaur Mining) suffering through startup woes right now in which they do an autoclave acid leach to get everything into solution, then partially neutralize it to get rid of iron etc., then precipitate a Ni/Co hydroxide, and THEN leach it with ammonia. They're investing big money in that one.
Anyway, sorry to be so long-winded but I thought you might be interested. If you have any feedback/comments I'd like to hear them.
Brian Park, P.E.- Butte, Montana, USA
publicly reply to Brian Park, P.E.
Q, A, or Comment on THIS thread -or- Start a NEW Thread