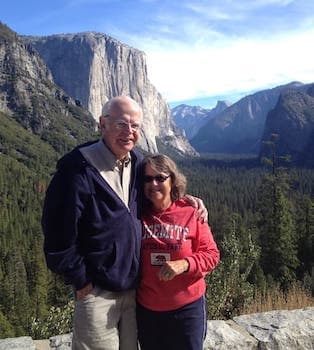
Curated with aloha by
Ted Mooney, P.E. RET
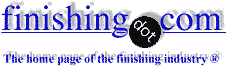
The authoritative public forum
for Metal Finishing 1989-2025
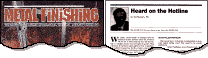
-----
Environmental stress cracking resistance of plastics
I am looking for appropriate method for chemical resistance of plastics (Environmental stress cracking resistance). I need information on any laboratory/organisation conducting these type of testings.
Vishvajit Juikar- Banglore, Karnataka, India
2001
2001
Hi Vishvajit !
Re your query on environmental stress cracking of plastics, the corrosion resistance data given out by the manufactures sometimes indicate that a given thermoplastic in a given environment at a given temperature may not be suitable.
For the polyoelfins, they do sometimes indicate stress cracking potential, particularly with oxidizers. ie. Polyethylene containing nitric.
However, this stress cracking is enhanced enormously, I feel, on the actual process. For instance (going by memory) Polyethylene may not be recommended for 20% nitric BUT if it was moulded (i.e., a stress free product such as a tank made using the Engel process), then it is probably very good UNLESS, UNLESS ... you start welding it! Then you will get failure around the welding! Ditto for Polypropylene.
Chlorine ... liquid, that is ... will attack most plastics yet I.C.I. proved that if one had a massive wall, the attack peters out and a resistant boundary layer is formed. A thin swimming pool vinyl liner (for chromic acid, for example) should well have a far, far shorter life than something 2 times thicker or heavier.... which bears out I.C.I.'s experiment somewhat.
There is a method where one can actually SEE stress lines! Someone, a long time ago, said that this was called the saccrimeter test ... something to do with sugar production.
You need 2 things. Some acrylic sheet ...and 2 small pieces of polarized glass/plastic. The sheet can have cemented areas, a heat bend and some welding. You place the sheet between the polarized pieces (which have to duly rotated as you will find out!) and then you can see the stress lines. If you get a thin piece of acrylic and force bend it, you can see the stress lines appear and disappear. A highly educational tool regarding welding techniques.
Getting back to environmental stress cracking, it seems that heat and a heavy oxygen content are contributory to failure where welding/fabrication has been done. By the same token, s.s. 3l6 weld failures (supposing ideal welding and passivation) must surely be due to a structural change in the properties but, I feel, BUT ... also due to some loss of some of the alloying ingredients. However, this 'loss' effect doesn't, I think, apply to plastics, thermoplastics, I mean.
The welding temperatures for plastics vary depending on the type of welding gun and tips used. Probably 350 to 450 degr. except for the weldable fluorocarbons which demand more heat.
But with stainless, you have 4 main 'alloys' but each has its own melting temperature. So ask yourself, if one uses a certain welding temperature, is there not a chance that some alloys can be reduced or even, in certain cases, totally disappear? Hence welding knowledge is very important. For good PVC welders, you should achieve over 85% of tensile. PVC being the yardstick by which you can relate to all the other plastics... and my favourite, too.
I hope that this might help you a little ... I have some real doubts that any 'labs or organizations' are going to impart any useful/honest data because of the variabilities of a fabricated item due to fabricating/welding techniques.
If you have any further questions, fire away.
Cheers !
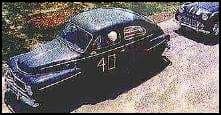
Freeman Newton [deceased]
(It is our sad duty to advise that Freeman passed away
April 21, 2012. R.I.P. old friend).
Q, A, or Comment on THIS thread -or- Start a NEW Thread