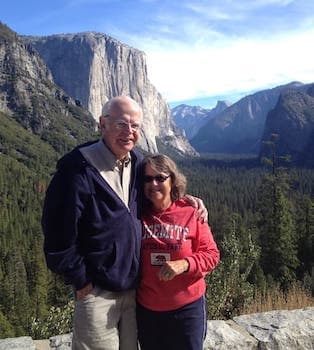
Curated with aloha by
Ted Mooney, P.E. RET
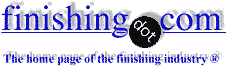
The authoritative public forum
for Metal Finishing 1989-2025
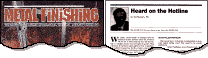
-----
Inconel Thread Coating Required
We have had some galling problems in the past with a 410 SS to 22% duplex threaded connection (highly torqued). We solved most of the galling problem through use of a teflon coating on the threads combined with a nickel-based anti-seize thread lubricant grease.
We now want to change both of the base materials to Inconel 718. What is the recommended coating (and lubricant, if any) for this connection?
Andy HansonMaster Flo - Edmonton, Alberta, Canada
2001
Within the oil industry the currently accepted method of reducing galling when connecting premium threaded tubulars, Manufactured from Cr steels and ancillary equipment some of which have Inconel thread inlays is to copper plate the box end (female thread) leave the pin (male thread) uncoated or occasionally abrasive blast (the jury is still out on the merits or otherwise of abrasive blasting). Then torque the components up using API (American Petroleum Institute) Dope (A type of grease).
The problems you can get when applying bonded teflon coatings on threads (if that's what you're doing), is that if for any reason you have to back of and re make a connection. The results can be inconsistent, we have seen in the field the teflon coat spall due to high torque loads and high thread interferences of some types of premium threaded components The also rely on a metal to metal sealing action to make joints gas tight, as the pin end is bucked onto the coupling or ancillary, which can gouge the teflon coat through to the substrate.
Regards,
Richard Guise- Lowestoft, U.K.
2001
Q, A, or Comment on THIS thread -or- Start a NEW Thread