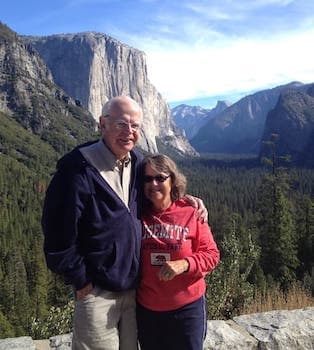
Curated with aloha by
Ted Mooney, P.E. RET
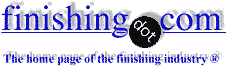
The authoritative public forum
for Metal Finishing 1989-2025
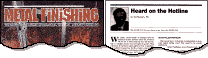
-----
PVD plating onto nickel plated articles
Q. Can you please inform me the precautions or surface preparations required before PVD plating in vacuum chamber for nickel plated articles.
C.Lokanathan- Mumbai, India
2001
A. Before any PVD coatings are applied, the substrates must be very thoroughly cleaned. Any oil or grease on the surface will greatly reduce coating adhesion. This includes oils from your hands. Some practitioners acid etch the surface, others do a grit blast to remove the native oxide. These are not required if your PVD process includes a good sputter clean step.
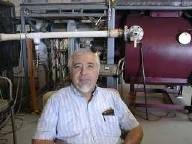
Jim Treglio - scwineryreview.com
PVD Consultant & Wine Lover
San Diego, California
2001
A. Dear sir,
Precaution prior to PVD plating on Nickel plated Items is not very critical. Only activation of passive nickel layer to be removed either by dipping in 25% HCl solution for 1 minute then three water rinses & drying them by hot air'; or dipping the Ni plated items in NaCN 10% cold solution for 5 mins then rinse in raw water and finally in DI water, then dry them with hot air blower. But after activation don't keep the cleaned item in open area for more than 30 mins. I hope this could help you in processing the nickel plated items.
Madanjeet Prasad- Valsad, Gujrat, India
2003
How to PVD coat over electroless nickel without de-lamination problems
Q. Having trouble PVD, DLC coating over .0005 electroless nickel. Parts are delaminating. Need a solution quick.
kevin Burnsmanufacturing - usa
January 27, 2015
A. Hi Kevin. Is this fresh clean electroless nickel that was just plated, or has it been hanging around a while? Hopefully Jim will chime in, but from his previous posting it sounds like sputter cleaning would be a solution.
Regards,
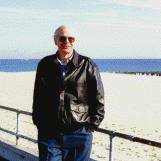
Ted Mooney, P.E.
Striving to live Aloha
finishing.com - Pine Beach, New Jersey
January 2015
Q. Originally the parts were fresh but since this has happened the parts have been sitting a while. I will pass this info on to my plater. Is temperature a contributing factor or only cleanliness?
Thanks
Kevin
- San Carlos California usa
January 27, 2015
A. It seems like a stress-related problem. The nickel is likely in tensile stress, and the PVD coating in compressive stress. Not a good situation. It could actually be worse than you think -- we've had similar issues, but the coating didn't delaminate until the part was thermally cycled. Check with your plater to see what he can do to reduce the tensile stress in the nickel. Are your coatings decorative or functional? If decorative, you might reduce the PVD and DLC stress by lowering bias voltage or reducing coating thickness.
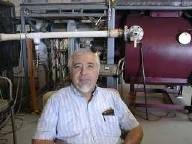
Jim Treglio - scwineryreview.com
PVD Consultant & Wine Lover
San Diego, California
January 28, 2015
Applying Nickel to Aluminum by PVD
Q. Are PVD coatings applied to aluminum cookware? If not, why not? I'd like to apply nickel PVD to die cast aluminum garlic presses. Thank you for your advice.
Stephan Bianchiproduct development - Santa Cruz, California, USA
October 23, 2017
A. Hi Stephen. I have very little PVD knowledge, but if you read between the lines, decorative PVD finishes are done on top of electroplated nickel (like "lifetime" brass colors) rather than PVD nickel, probably partially because of the low melting point and softness of aluminum. But aluminum is routinely electroplated with nickel, why do you prefer PVD?
Regards,
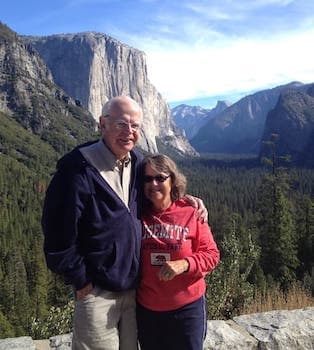
Ted Mooney, P.E. RET
Striving to live Aloha
finishing.com - Pine Beach, New Jersey
October 2017
Q. Hi Ted. Thanks for your reply. Decorative plumbing fixtures are routinely coated with PVD to eliminate tarnishing and scratching, so it seems like it would be perfect for kitchen utensils - decorative objects subject to rough handling. I'm curious as to why it seems uncommon in that industry.
Stephan Bianchi [returning]- Santa Cruz, California, USA
October 23, 2017
A. Hi again, Stephan. I think we're on slightly different wavelengths here. While plumbing fixtures are indeed routinely coated with PVD, my understanding is that they are FIRST electroplated with nickel and chrome and THEN receive a tarnish and scratch resistant PVD finish like titanium nitride. I'm not sure which PVD finishes are considered food-safe. But we do have some PVD experts who stop in here occasionally, and hopefully they'll see your post and respond.
Regards,
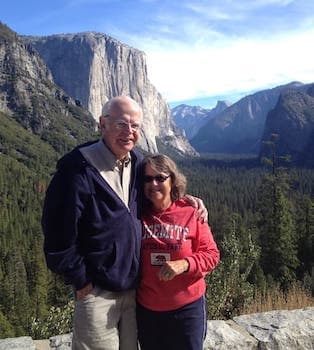
Ted Mooney, P.E. RET
Striving to live Aloha
finishing.com - Pine Beach, New Jersey
October 2017
Thanks, Ted! That is my understanding as well - that they are plated first, then covered with a thin nitride coating. We'll see what others might have to contribute!
- Santa Cruz, California, USA
October 24, 2017
Vintage Garlic Presses on eBay
A. This applies to this as well as the previous question. Decorative & hard coatings like TiN can be deposited on aluminum or zinc. But they may not be of much use as the substrates are soft and do not have load bearing capacity. Though the coatings are hard they are highly susceptible to scratches on such substrates. So one should deposit a relatively thick (15 to 20 microns) plating like E-Ni or hard chrome on Al & Zn substrates before depositing a something like TiN. Being low melting point substance zinc can easily contaminate the coating chamber. PVD coating will have to be deposited at a sufficiently low temperature.
H.R. PrabhkaraBangalore Plasmatek - Bangalore, Karnataka, India
November 12, 2017
Thank you, H.R.!
- Santa Cruz, California, USA
November 15, 2017
A. I agree with Mr. Prabhkara ... and one another thing I want to tell you: generally utensils are daily use items and must be cleaned every day by rubbing with alkali soap or liquid -- so TiN coating didn't endure a long time.
Rajesh Patel- ahmedabad, gujarat, India
November 18, 2017
A. There is some confusion here between decorative PVD coatings and functional PVD coatings. Decorative coatings are less than one micron thick and deposited at very low temperatures, so they offer only minimal wear protection. Functional PVD coatings are much thicker and deposited at very high temperatures. It is possible to protect aluminum from scratching with a PVD hard nitride, but there are serious issues beyond the low hardness of the aluminum. To begin with, aluminum has a much higher coefficient of thermal expansion than any PVD coating. Applications which entail thermal cycling, i.e., frying pans, can result in the PVD coating delaminating from the aluminum. Then there is the huge difference in ductility. PVD coatings, being largely ceramic materials, are very stiff. They can handle compressive stress but not tensile stress. Any significant convex bending of the coated aluminum can crack the PVD coating. Cyclic bending also can lead to cracking and delamination of the PVD coating.
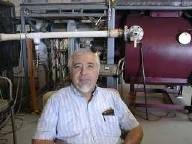
Jim Treglio - scwineryreview.com
PVD Consultant & Wine Lover
San Diego, California
January 25, 2018
Q. Rajesh and Jim,
Thank you for your advice! My immediate interest is application to a garlic press, so these are my impressions: Decorative fixtures are typically brass. They may be cleaned daily, but not harshly. They wouldn't be subjected to conditions like those in a dishwasher. I could make a press of brass - it would be heavier than aluminum, but might be acceptable. It might be cleaned more strenuously than plumbing fixtures, but wouldn't be subjected to great heat. So it seems a PVD finish might be inappropriate for my application, but I haven't yet ruled it out absolutely.
- Santa Cruz, California, USA
January 27, 2018
Q, A, or Comment on THIS thread -or- Start a NEW Thread