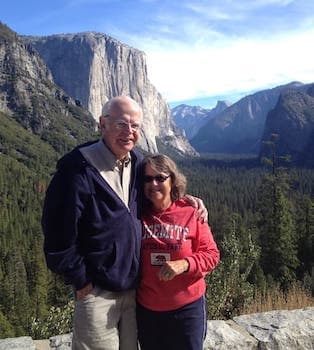
Curated with aloha by
Ted Mooney, P.E. RET
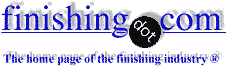
The authoritative public forum
for Metal Finishing 1989-2025
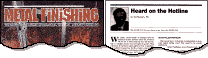
-----
Current carrying capacity of copper
Q. Can somebody explain to me precisely the relation between area of copper, the current it carries and the temperature rise.
In short the question would be: What is the area of cross section of copper I am to use if I were to pass 1 amp of current for x hours. Assume that I permit a temp rise over ambient of 40 °C. Also assume that the copper is 99% pure.
Hariharan Rajgopal- Bangalore, India
2001
A. The answer is complicated by the fact that there is some thermodynamics involved in the solution, and unless you can specify wire resistivity, ambient conditions including insulation, humidity, etc. for heat loss, an expert mechanical engineer will not be able to do the simulation job for you, and you may still have a theoretical answer of no use. So I would simplify things this way:
1) According to wire gauge, each wire/strand is rated for a certain current limitation. Just look at the table. Somebody has done this work for us a century ago. You may extrapolate information you need from this table.
) For your specific ambient and insulation conditions, do an experiment. Get a variable current power supply and pass increasing current through the wire of interest. Attach a thermocouple to the wire and measure the temperature. An engineering college lab could help you in the case you do not have the set up.
3) A typical 0.25" (6.35 mm) dia. pure copper rod can handle up to 150 amp current without getting hot at 75 °F ambient and no insulation. See if this helps extrapolate.
Mandar Sunthankar- Fort Collins, Colorado
2001
Hard chrome plating rectifier bus bar sizing
2004How do you size the bus bars (from rectifier to tank).?
The end-user is using 100 x 10 x 3 Aluminium bus bars for 3000 A and 16 V.
Another rectifier is 100 x 4 x 3. 1500 A and 10 V.
Can you please advise on any selection table for sizing of bus bar and also the losses with Al bus bar and Cu bus bar?
How do you measure the current in these bus bars? Which portable meter will provide reasonably accurate values?
Kumar
KumarEnergy Engineer - Bangalore , Karnataka, INDIA
Full name please, Kumar -- this is a place of camaraderie not anonymity :-)
The quick way to size bus is (in english units) 1000 A / sq. in for copper and 600 A/ sq. in for aluminum. Bus sizing is irrespective of voltage within the common range for plating.
Charts and more detailed calculations comprise the "Anode and Cathode Rod and Bus Systems" chapter of the Electroplating Engineering Handbook ⇦ this on eBay, AbeBooks, or Amazon [affil links] .
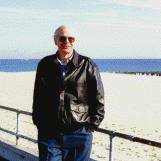
Ted Mooney, P.E.
Striving to live Aloha
finishing.com - Pine Beach, New Jersey
2004
2006
A. As far as I know, (I heard it from someone working in my company):
First you should know the current density of the conductor; let's take, for example, copper has 4.02 Amp/sq. mm. as current density. So you want to pass a 2A current thru a copper conductor then you need a conductor of area:
area = current in Amps/current density.
area = 2/4.02
area = 0.5 sq.mm
They use this formula for calculating the thickness of the busbar that they use in big electrical panels.
- Mumbai, India
A. Copper current density allowable is 1.6 A/mm2
Swamulu Saluvadi- Hyderabad, Andhra pradesh, India
February 1, 2013
A. Hi folks. The allowable current carrying capacity is actually defined as the amount of current that can be carried without melting the conductor or the insulation. Googling "current capacity of copper conductors" will immediately produce a dozen sites with the same definition and same charts.
But in many cases we don't want to put nearly that much current through the conductors. In the electroplating industry we have always used an allowable current of 1000 A / square inch for bare DC busbar, which equates to 1.55 A/mm2 -- essentially the same as Swamulu's number. This is empirical, based on the recognition that we don't want a large voltage drop across the conductors because it would interfere with the plating process, and waste a lot of energy, and a hot bare bus bar introduces the real possibility of operators getting burned or starting a fire.
I think Mandar's & Rajiv's numbers may be valid for some applications but are much too high for low voltage DC bus bars. Please see thread 50556, "Copper Bus Bar Sizing for DC low-voltage high-amperage" for further discussion of low voltage bus bar runs.
Regards,
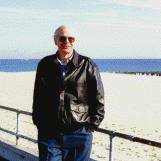
Ted Mooney, P.E.
Striving to live Aloha
finishing.com - Pine Beach, New Jersey
March 5, 2013
Multiple threads merged: please forgive chronology errors and repetition 🙂
Bus bar power loss calculations
My interest behind this question is to find out the actual losses occurs in aluminum busbar. I have 13 nos furnace transformers of 500KVA ratings. its I/P voltage ratings are 6600/60-160 volts, 57.57/3600 amps. Transformer secondary is connected to the top & bottom electrodes through the aluminum busbars. the busbar specifications are thickness-10mm, width-100mm, length-6000mm. for this one length of busbar I want to calculate the actual power loss which may in this much area. The continuous current flows through bus bar is 2500 Amp. So by using this information can anybody help me to find out the actual losses of aluminum busbar.
Santosh JagaleElectrical engineer - Bharuch, Gujarat, India
June 30, 2008
June 30, 2008
Hi, Santosh. This site serves the metal finishing industry where aluminum bus bar is used to carry low-voltage high-amperage DC. I am having trouble following whether you are speaking of AC or DC, but for DC the power loss is simply I^2R, and R is simply rL/A. You need to know the resistivity of the specific aluminum alloy you are using first.
Regards,
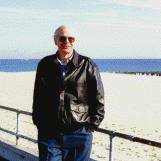
Ted Mooney, P.E.
Striving to live Aloha
finishing.com - Pine Beach, New Jersey
Q. Hi friends,
I want to know wall thickness and x-section area and dia. of copper bus bar which we are going to buy. We require 72m bar per phase, which are coming in 12m 6 parts for each phase, and we are going to connect 04 stepup 60MV 50HZ 132kv transformers to that bus bar and 250mw power to transfer through this bus. Please help me. I also need maximum current rating at 80 °C normal operation?
Thanks a lot.
- lhr, Pakistan
November 23, 2015
Q. I want to design Air circuit breaker with breaking capacity of 65kA@415V AC with current rating of 2500A. How can I calculate current path such that temp. rise @2500A does not exceed 780C?
mayank vijay- noida, U. P. India
May 17, 2019
May 2019
A. Hi Mayank. You are welcome to post your question and anyone is welcome to answer it, but this is a metal finishing site and may not attract electrical engineers experienced in the rather specialized field of air circuit breaker design.
Regards,
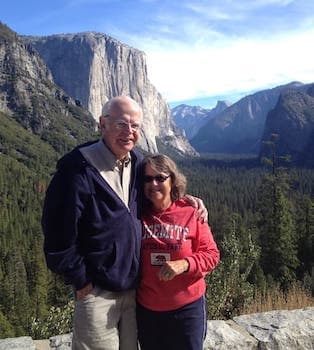
Ted Mooney, P.E. RET
Striving to live Aloha
finishing.com - Pine Beach, New Jersey
Q, A, or Comment on THIS thread -or- Start a NEW Thread