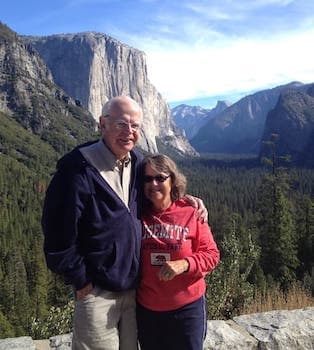
Curated with aloha by
Ted Mooney, P.E. RET
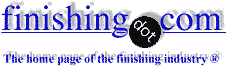
The authoritative public forum
for Metal Finishing 1989-2025
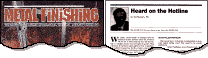
-----
What are some proven ways for dealing with air compressor condensate?
Q. Our company is looking for a way to deal with condensate from our air compressors. What are some proven ways to deal with this? Do the oil/water separators work well? How are other companies deal with this problem? Our oil used in our rotary screw compressors is a non-emulsifying PAO synthetic blend that is supposed to work well with separators. Before I buy one I would like to know how well they work.
Any help would be appreciated.
Thanks,
Chris Ballew- Newport, Tennessee
2001
A. Hi Chris,
Firstly, I've never had to 'work' on your problem ... because of involvement with the corrosion resistant plastics along with mist eliminator design.
One of the reasons why people who use compressors for 'air' for plastic welding guns have problems is due to maybe the oil but certainly the moisture content, especially for Pe & PP.
The oil/water separators have been around for a coons age but how good they really are, I dunno. However, the first thing you have to do is to COOL down the exhaust. Then you will get condensate which is easier to get rid of.
If your particular process demands a good degree of 'air purity', consider a high efficiency sine curved mist eliminator blade design (vertical fitting for horizontal airflow) BECAUSE, if well made, you can knock out droplets to way below 20 microns. These could be quite compact. Again, you have to have some tortuous piping to cool down the exhaust, therein lies a greater success of capture.
Food for thought, anyhow.
Cheers !
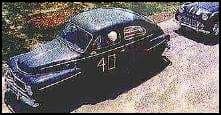
Freeman Newton [deceased]
(It is our sad duty to advise that Freeman passed away
April 21, 2012. R.I.P. old friend).
Chris,
It's a problem with just about anyone who needs pure air for their processes. I've found that by putting a heavy duty separator directly after the compressor will help cut down on most of the oil and water from the compressor. It has to be inspected and cleaned regularly. For condensate that occurs inside the pipes you can try a disposable in-line filter or mount a replaceable cartridge unit at each connection area.
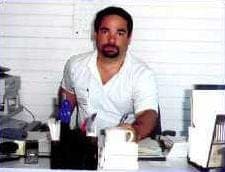
Jim Conner
Anoplex Software

Mabank, Texas USA
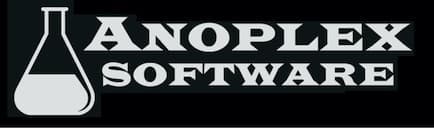
To resolve your issue you will need an after-cooler and an air dryer. Most rotary screw compressors have after-coolers built in. The dryer choice is based on your requirements. For general shop air a refrigerated dryer normally will suffice. This will take your dew point down to around 34* F. For instrument air a regenerative dryer is usually used. This will take your dew point down to -30 °F. After filters and separators can be used at your line drops.
Hope this helps.
Gordon Vidt- Heath, Ohio, USA
Chris:
We experienced this heaviest in the warmer months. We found a "floating" aggregate that sits overnight in the barrel, rises to the top and clumps the oil together and then simply skimmed off with a small hand screen. The water can be disposed of as a non-hazard and the aggregate treated like spent oil-dry.
Terry Rielly- Lindenwood, Illinois
You have two problems. First is a water condensate, generally the larger fraction. Second is an oil/water emulsion. The emulsion will typically float on the top of the water. Coalescing oil water separators work most effectively on free oil, not emulsified oil. To separate the oil/water emulsion and generate the free oil it is necessary to "crack" the emulsion. The most common cracking technologies are: heat, acid, salt, magnesium sulphate (epsom salt), organic polymers (emulsion breaking), and/or time. Some of the emulsions from rotary screw compressors, using synthetic lubricants (diester base), cannot be broken using any and all of the above mentioned methods. If you are able to crack the emulsion the coalescing oil water separator will work. With a stable emulsion you may decant the free water and absorb the oil on a special clay.
Gary W. Davis- Itasca, Illinois
2003
Recommendation:
1) Installing a cooling pipe (in the shape of a coil, in order to increase trajectory time), and then,
2) Using a separator, with a baffle (this should break the emulsion enough)
3) Once you have gotten rid of the liquids, you can install a dryer, and/or molecular sieve, if necessary (it all depends on the desired air quality)
- Mahopac, New York
2004
Check the compressor oil viscosity. If you are running the compressor indoors or in warm conditions be sure you are using a heavier summer grade oil.
A substantial receiver tank in a shady cool area will increase the time required to allow the hot air from the compressor to cool. A large receiver tank will also provide a calm area in which the velocity of the air is substantially reduced, allowing droplets to literally fall out of the air.
Depending on the air demand, a large receiver tank - or two - could reduce compressor run time by providing a level of capacitance to the system. This could also help to produce slightly cooler compressed air as the compressor could have time to cool a bit between cycles.
If the compressor inlet air can be as dry as possible this will also usually help to reduce condensate. The dryness of the inlet air usually relates to its coolness - cooler = drier.
- Surrey, BC Canada
2006
Hi, we have similar problems with oil/water emulsion in our rotary compressors. we have series of oil filters in our discharge lines and air dryers but still we get a lot of condensation and oil/water emulsion which clogs the condensate drain valves. humidity may also be a factor. we only have these problems in the summer where humidity reaches up to 95%. locating the compressor in a clean dry space will help and the best way to do is regular inspection and cleaning of filters.
John Rutherford- UAE
June 13, 2010
Q, A, or Comment on THIS thread -or- Start a NEW Thread