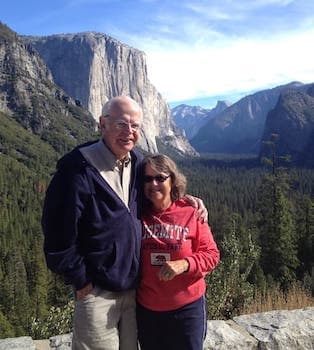
Curated with aloha by
Ted Mooney, P.E. RET
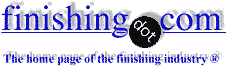
The authoritative public forum
for Metal Finishing 1989-2025
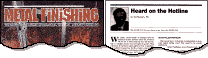
-----
Zinc vs. E-nickel Thickness
Q. Good Day,
I would like some opinions on Zinc w/clear chromate vs. Electroless nickel. At .0002" to .0005" thickness zinc will outperform e-nickel during a standard ASTM B117 salt spray test. At greater thicknesses(e.g. .010") the e-nickel barrier type coating will be superior.
Here's my question: At what thickness will e-nickel outperform zinc w/clear chromate over 12L14? Our mfg. processes all use costly pre-plate gages and I would not have to re-tool them if I could know that, say, .0005" - .001" e-nickel will outperform zinc.
I would appreciate any feedback.
Thanx and have a good one.
Daniel J. Rogers- Minneapolis, Minnesota
2001
A. All EN is not equal, even from the same tank on the same day. But, 0.0015 of High Phosphorous EN will be very resistant to salt spray as there are no pores that run from the surface to the substrate. 0.001 will do for a lot of things, but that is typically 0.0007 to 0.0012. There is literally 100% difference between the two values in salt spray resistance. EN is an excellent barrier and zinc is sacrificial. EN would be my choice.
James Watts- Navarre, Florida
2001
A. Dan:
I definitely agree with the Electroless Nickel approach instead of the conversion treated zinc. What I don't understand is why, if you said that your tooling is expensive, are you so worried about thickness turning point. If there is no cost concern go to 2 or even 3 mils. of EN. You obviously will have to start with undersized gages and coat them. If the tolerances are not met go on and grind or lap back. Sounds right or I missed the point? I'll be glad to keep this interchange of ideas on this forum.
Guillermo MarrufoMonterrey, NL, Mexico
2001
Q, A, or Comment on THIS thread -or- Start a NEW Thread