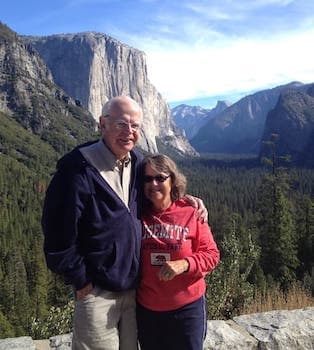
Curated with aloha by
Ted Mooney, P.E. RET
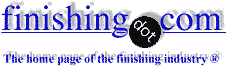
The authoritative public forum
for Metal Finishing 1989-2025
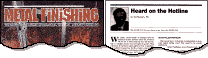
-----
Hard wear surface for 17-4 PH stainless steel, or wear coatings for it
Q. I am in search of a wear reduction coating, to be applied mainly to 17-4 PH stainless steel. I currently have a situation where several pivot areas such as linkages contain all 17-4 PH parts, which either gall or wear prematurely. I would like something that is fairly easy to apply (if possible), but above all longevity is my biggest concern. The stainless steel parts are used in a marine environment, so they will see salt spray, as well as fine airborne sand particles which are very abrasive.
Any information on this subject would be greatly appreciated.
Thank You.
Noel Wareham- Minneapolis, Minnesota
1998
A. Chrome would be my first choice, followed by electroless nickel or some type of vacuum deposit (PVD, etc.)
All need to be professionally done. Setup is not cheap for any of them. Electroless nickel would be the cheapest way to go for a small plating facility. Less EPA grief vs initial start up cost.
James Watts- Navarre, Florida
1998
A. For corrosion and wear resistance you might try a chrome with an interlayer to CrN. There are companies that could probably do that for you by PVD methods.
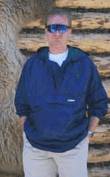
John Davis
- Berthoud, Colorado, USA
1998
A. You might investigate vapor deposited chromium oxide coatings. These are very hard and reportedly provide excellent corrosion and galling wear resistance.
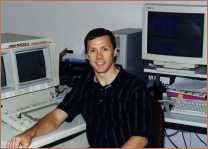
Larry Hanke
Minneapolis, Minnesota
1999
A. In response to Noel Wareham's question, quoting: "currently have a situation where several pivot areas such as linkages contain all 17-4 PH parts, which either gall or wear prematurely. I would like something that is fairly easy to apply (if possible), but above all longevity is my biggest concern. The stainless steel parts are used in a marine environment...."
The problem here can be solved by a materials change rather than trying to back-fit parts, unless there is no chance that new parts will be made. 17-4 PH is not a good choice for running against itself in an unlubricated environment, especially when all the parts are probably the same hardness.
Possibilities for new or rework include pressing in a bronze bushing. These can be obtained impregnated with oil as well. A limitation may be found if the high strength of the 17-4PH is a requirement, as bushings have a limited bearing load (maximum). Of course, 17-4 PH galls when run under significant loads as you have found.
Another possibility is the use of galling-resistant materials for one side or both of the wear couple. The Carpenter Technology line of Gall-Tough PLUS, or the Armco Nitronic 60, are high strength (higher than 300 series stainlesses, in some cases approaching 17-4 PH) galling-resistant grades. Literature can be requested at http://www.cartech.com/products/home_lit.htm and associated locations, or Armco at http://www.armco.com/artoday/artoday_form1.htm
I realize that this is the FINISHING Hotline, but sometimes it's best to start with a good material than trying to Band-Aid a bad one.
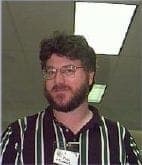
Paul Tibbals, P.E.
gas & electric
San Ramon, California, USA
(My opinions are not related to nor a statement of my employer's)
1999
Q. We are building small harmonic drive units for some miniature research robots (5 cm scale). The harmonic drives function with a cup-shaped "flexspline" with external spline teeth mating to a fixed spline ring with a slightly larger number of internal teeth. Rollers cause the spline contact point to walk around, producing output rotation of the flexspline due to the difference in numbers of teeth. Grease is used on the spline surfaces.
We need a material with good strength, wear resistance and machinability. We have tested 12L14 free-machining steel, but its strength and wear-resistance seem poor. We have found that 17-4 PH stainless machines nicely and can be hardened with minimum distortion, but I understand that galling may be a problem when it is run against itself. So we're considering surface treatments to minimize wear and galling. One recommended treatment is a "thin-dense" or "nodular" chrome plating that is reportedly very thin and uniform, with buildup of .0001-.0002" and surface hardness of about 72 Rc. Part tolerances are on the order or a ten thousandth or an inch, so a thin uniform buildup is needed.
I'm seeking comments on this treatment, and recommendations for other treatments that would be good.
Thanks,
H. Ben Brown, Jr.Carnegie Mellon University - Pittsburgh, Pennsylvania
2001
A. Galling is most common when you try to run the same metal against the same metal.
Your original choice was a free cutting steel and would not have a good wear resistance. I think that you can easily get by with 4140 or 4340 or similar hardenable steel. Depending on shape, it may distort in heat treatment, so it is common to leave some grind stock for touch up. This material needs to be hardened in a vacuum furnace or one with a controlled atmosphere or wrapped up in a special SS foil bag to keep the surface from having a lot of heat scale. Sometimes they are copper plated to prevent decarburization on the surface. You might consider having it nitrided or case hardened. S-2 or D-2 should work well also, but are a lot higher priced and tougher to machine.
I really do not think that you need any coating. Chrome, EN and vapor depositions have their place, but I do not think that you need it for here, if I picture your part correctly.
James Watts- Navarre, Florida
2001
A. Hello Ben!
I think using 17-4 makes a lot of sense, for ease of machining and hardening reasons. As you say, little distortion in hardening, combined with pretty good mechanical properties, and corrosion resistance to boot. Are you using the H900 condition? The HRC 40-47 is attractive, but beware low ductility- that's one of the reasons that aerospace use of the material is commonly limited to H1025 & H1075.
My gut feeling is that you shouldn't have much of a problem, if your loads are sufficiently light and you keep the teeth greased. Galling tests that I've run here show 15-5 galls easily (280 psi) if clean, yet is very resistant (over 10 ksi load to gall) if oily. Those load paths are also the type that are forced to rub against each other- yours sounds like it can roll, giving you less of a problem. So, you may want to try out your device to see if your premonition is warranted.
When I have galling concerns, I too strongly consider chromium plating- we use it all the time on our 17-4 and 15-5 actuators. If your contact loads are low, then thin dense chrome plating per AMS 2438 will (not "should", but "will") work well. Further, you don't have to grind after coating. My contact loads are often higher than the thin dense chromium can tolerate on a 17-4 substrate, so I go with a thicker layer; say, 2 mils (50 microns) or so, after grinding. We electroplate on more, and grind off the extra, to ensure getting uniform coverage. To find a place that will do the work, look for "thin dense chrome" or "AMS 2438" on the supplier advertising. I'd guess there are firms that advertise here at finishing dot com which offer this service, so I'll not step on their toes and recommend someone else. Be sure to let the plater know that they're trying to plate stainless steel, so they can activate the surface properly.
Among the alternatives I'd consider would be nitriding the 17-4, to about 5 mils depth. Here you'd likely need to grind afterwards, because the surface gets ugly: you'd also likely get some microcracking on the surface, especially in the crown of the teeth. Another disadvantage would be that you lose most of your corrosion resistance of your stainless steels. Along a different tack, you might consider a galling resistant stainless steel, like nitronic 60 or Gall-tough, which have lower strengths (about 60 ksi yield, 100 ksi tensile).
I enjoyed my years at Carnegie (76-78), so I'd be happy to help if you've more questions or need something heat treated. Contact me at lgearhart@moog.com. And if you see Rick or Kathleen Carley, give them my regards!

Lee Gearhart
metallurgist - E. Aurora, New York
2001
Q. I am looking for a stainless steel with much more wear resistance than 316L has. The corrosion resistance in 316LSS is adequate. The application I am using is a drum that spins recylables which includes paper clips, staples, etc. that wear the drum and cover. I was thinking 17-4 PH would be a good fit? Do you have any suggestions?
Tammy Madore- Millinocket, Maine
December 3, 2009
Q. Hello,
I look for a Scratch test chart Frictional force vs. Load for nickel coating on stainless steel. But nickel, chromium, tin, or zinc on any steel would be also interesting. Can you give an article title or a book where I could find something like that?
Best regards,
Jurek
- Lodz, Poland
May 11, 2013
Low friction wear coatings for steel and aluminum
Q. My application is one where we want "everything": extremely low friction, high sliding and rolling wear under high stress, High temperature and of course resistance to corrosion. There are 3 different types of substrates: HR 60+ carbon steel, 6160 & 7075 Aluminum and spring steel 1095 or 716
The aluminum substrate never rolls or slides against other aluminum (aluminum always against the Ferrous alloys)
I would like to solicit expert opinions on the best coating to achieve the low friction very high wear characteristics. Currently using WS2 as the top coat and considering MoS2 as alternative. It would be nice to get everything we want in one shot (but that is a wish rather than a "must have").
P.S.: There is a combination we are currently using but not disclosing so as not to skew the responses. Thank you in advance to all that respond.
- San Jose, California, USA
November 14, 2015
November 15, 2015
A. With no further information, I'd say hard chrome on the steel and hardcoat on the aluminum.
Electroless nickel, heat treated, would also work on both steel and aluminum, but not on both simultaneously. Better to have a different coating on each of the two rubbing surfaces.
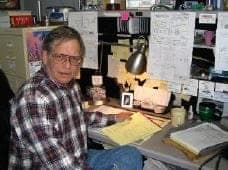
Jeffrey Holmes, CEF
Spartanburg, South Carolina
I would think for the steel parts bright nickel electroplating and trivalent chrome for corrosion resistance, with sputter-deposited MoS2 or DLC top layer for low friction would be the best combination, keeping in mind that MoS2 does not like water, whereas DLC cannot function in an extremely dry application (such as a vacuum).
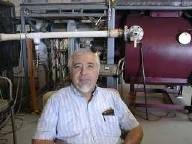
Jim Treglio - scwineryreview.com
PVD Consultant & Wine Lover
San Diego, California
November 16, 2015
Aluminium-to-aluminum steering shaft spline
Q. Hello all,
I am an automotive engineer developing a steering shaft for a lightweight vehicle. I would like to use aluminium (7075-T6) as a material for the shafts. The idea was to use an aluminium inner and outer spline and to coat both with WS2. Will this work or will the WS2 coating not withstand the loads?
The spline will be axially loaded by means of the front suspension, so every bump in the road will cause the spline to slide. Radial loads will not exceed 80Nm. I hope I have given enough information.
Design Engineer - Netherlands
November 23, 2015
Hi. I'm no automotive engineer, just a guy who has seen a lifetime of aluminum-on-aluminum galling, fretting, and seizing.
Years ago, when colored aluminum keys were the rage, I had a new garage door put in, and the contractor warned me that the lock had aluminum parts, so don't use an aluminum key. I didn't tell my wife, who immediately had a spare key made and tried it out. The aluminum key went into that half-day-old lock and spent its next 10 years there despite all our efforts to remove it :-)
And I can't believe an aluminum-on-aluminum spline fitting would be a good idea.
Regards,
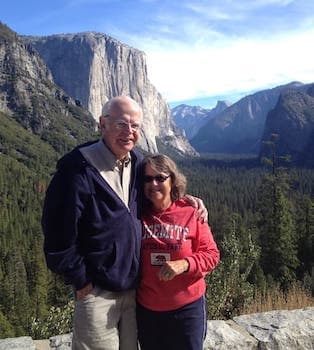
Ted Mooney, P.E. RET
Striving to live Aloha
finishing.com - Pine Beach, New Jersey
November 2015
Q, A, or Comment on THIS thread -or- Start a NEW Thread