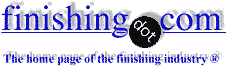
-----
Anodizing and Sealing Aluminum
We use aluminum cases for housing a new line of DC/DC converters. These cases are anodized, dyed blue, and then sealed with nickel acetate.
Recently, we received our first lot of these cases and after exposure to sunlight via the window, they have begun to fade severely. No fading has occured in past anodized prototypes. I've found that the dye loses color when exposed very briefly to nitric acid (which I've been told is a good seal test for nickel acetate).
The company that anodized the parts denies the possibility that cases were shipped without sealing. After re-sealing two cases, the nitric acid had the same effect--which doesn't completely surprise me since it had been 2 months since anodizing (and the supposed first seal). Yet, cases faded in the sun (which continue to fade in fluorescent light) seemed to stand up to the nitric acid.
Can anyone explain what may be occurring here? Previous cases have been exposed for months without fading. Also, does tumbling or sandblasting aluminum inhibit anodization? Are there questions that I should be asking the electro-plating company?
Thanks in advance for any help on this!
Jason Benfer- Blacksburg, Virginia
2001
Color fading is usually from either:
1) The part is not properly sealed. I know that the blue dye we use in house requires a long nickel acetate seal to pass the seal test. Most of our work gets 5 min seal - the blue requires 10-15 min to pass.
2) There are many different blue dyes out there for the anodizer to purchase. Each one has a lightfastness rating that rates how well the dye holds up to light. Some are not at all suitable for outdoor use.
David A. Kraft- Long Island City, New York
2001
2001
You should ask your anodizer for the following questions :- Does the parts being properly sealed?
You need to seal the dyed parts in a hot nickel acetate type sealant solution( at least 85 C or above)for a number of minutes, the sealing time depends on the thickness of the anodic coating.
If the dyed part (Not a deep shape part) is not sealed properly, you may be able to test it by using a simply method ; Use an ink pen to scratch slightly on the sealed surface, wait for a little moment, wipe off the ink by a good absorbent paper. Observe if there is any ink left on the surface. If there is, the sealing is not enough to resist the ink penetrating into the anodic coating. If no stains is found, the sealing is O.K..
Usually, the lightfastness of the dye increases with the depth of the shade. If this part is blue, a deep shade can be more resistance to fading than the light shade parts.
S. Y. Yuen- Hong Kong, China
One other possibility that Dave didn't mention was the thickness of the coating.. you want to make sure the coating is thick enough to fully absorb the blue dye. The other thing I wanted to mention, is that a 50% nitric acid solution (not straight nitric) should be used to test the seal quality. This should be left on the part for 2 min, then rinsed off. The part may then be "pumiced". If after that, you still notice a stain from the nitric acid, then the seal quality is not good. Your anodizer should be responsible for doing these tests, not you. We do this test on a daily basis, to ensure a good quality seal.
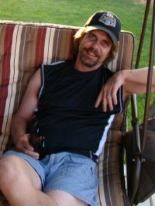
Marc Green
anodizer - Boise, Idaho
2001
You should consider two main points:
1) The quality of the blue dye-stuff used to color the anodic film. The dye-stuff must be resistant to sun rays against fading. The anodizer should use an architectural dye-stuff for outdoor exposure.
2) The anodic film thickness should be 15 microns minimum to absorb the pigments in the dying solution.
Timur Ulucakaluminum extrusions & finishing - Istanbul, Turkey
2001
Q, A, or Comment on THIS thread -or- Start a NEW Thread