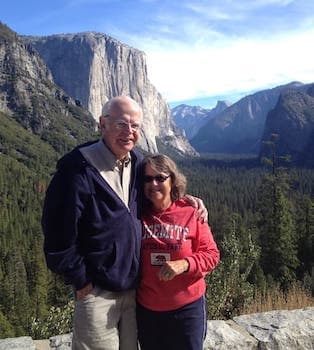
Curated with aloha by
Ted Mooney, P.E. RET
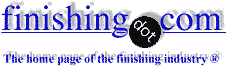
The authoritative public forum
for Metal Finishing 1989-2025
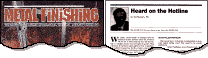
-----
Surface characteristics in Electropolishing stainless steel
2001
Has the subject of surface characteristics (Ra, peak count, bearing area, etc.) been explored in detail in relation to stainless steel electropolishing as it has been done for surface treating and painting of automotive body panels?
We supply 304 to a customer electropolishing who claims that in the same tank at the same time, our material sometimes comes out with a slight but noticeable haze while competitor material is shiny. Is doing detailed surface roughness testing barking up the wrong tree?
Is it possible that the protective PVC film is leaving a residual that causes a slight difference in post-electropolishing surface?
So many variables...so few concrete facts...
Alex Millar- Seattle, Washington
I think your problem with hazing of the elecropolished surface is probably due to metallic impurities. Electropolishing solutions by nature build in nickel and chrome because they are constantly being dissolved in the solution. In electropolishing the part being is anodic which means you are removing metal from the surface.
A standard practice of electropolishing is to decant the solution periodically and adding back fresh solution to dilute the impurities. If this is not done, hazing and an irregular surface result.
Another problem is that if the specific gravity is reduced by drag-in of water, electropolishing effectiveness is reduced. This requires heating the solution sufficiently to drive off excess water from the solution.
Hope this helps.
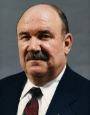
Daryl Spindler, CEF
decorative nickel-chrome plating - Greenbrier, Tennessee
2001
Q, A, or Comment on THIS thread -or- Start a NEW Thread