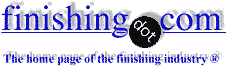
-----
Control Of Copper Ion In Descale and Pre-dip baths Prior to Tin/Lead Plating Onto Alloy 42
Presently we are Sn(86%)/Pb electroplating (Automatic plating system by AEM) on Copper lead frames (semiconductor products). We plan to start plating Sn/Pb onto Alloy 42 lead frames by mid June. We know the problems of copper's presence in both the Descale and Pre-dip tanks prior to the Sn/Pb plating bath. If copper ion is present in either the Descale (Sulfuric acid, plus Act 96, and D.I. water) bath or in the Deflash (Methyl sulfonic acid plus D.I. water) bath, Cu will plate out as a fine powder having poor adhesion onto an alloy 42 lead frame. There will exist problems at the interface of the Cu lead frame and Sn/Pb solder plate. We know the best solution to this problem is to replace each of the 2 baths to remove any and all Cu ions. We know we can plate onto alloy 42 lead frames first then follow up with any copper lead frames after going through the same solutions. If we need to do Alloy 42 again, fresh Pre-dip & Descale solutions must be used which will be copper ion free.
Question: Is there a way to pull out any and all copper ions from the Pre-dip & Descale solution baths once exposed to copper lead frames? Can copper be singularly precipitated out by addition of some chemical or possibly introduce some electrochemical means to the baths with out disrupting the solutions for further plating onto alloy 42 or pure copper?
The solving of this problem may be impossible without additional equipment although we want to "KISS" (Keep It Simple Stupid) without adding additional costs to the present operation.
If someone has a practical solution, please help me as we have limited time to experiment and revise the system.
Best regards
Aaron EpsteinIPAC - San Jose, California
2001
I came across your email as I was searching for pretreatment process for alloy 42. Our plating machine was designed to handle both alloy 42 and copper. There is a separate descale cell/tank for each substrate. But they share the same solution for the other processes - deflash to post-plate. Most of our products (IC, HED) use copper. But we have recently started plating alloy 42. Our problem now is blistering on some of our plated alloy 42 parts after they are subjected to oven curing (after our marking process). We are using a sodium persulphate-based descale chemical.
I am interested in how you were able to address your problem and prevent blistering on your plated parts. Hope you could share info.
Amy Bancudsemiconductor component assembly - Philippines
2004
August 4, 2009
Hi Aaron,
Normally descale and activation are changed regularly due to Cu content which accumulates through time. Though recovering the Cu is a cost effective solution, it still poses risk what if there is still significant level of Cu left. And of course not mentioning the effect on productivity and quality which is priceless.
Characterization of the Cu content on these baths were my first project as a plating engineer. And it has solve a lot of problem including blister (and others).
Regards,
- Philippines
Q, A, or Comment on THIS thread -or- Start a NEW Thread