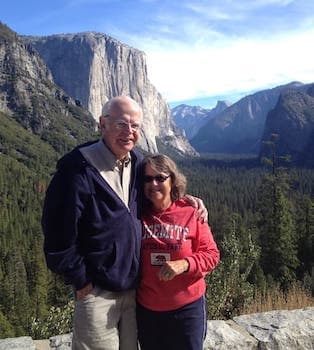
Curated with aloha by
Ted Mooney, P.E. RET
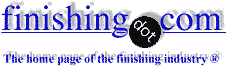
The authoritative public forum
for Metal Finishing 1989-2025
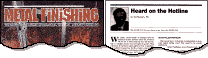
-----
Hot-Dipped Galvanizing Appearance
Q. I am interested in the aesthetic value of hot-dipped galvanizing. I have been told to expect a mottled color, & that an even grey color with this process is impossible. Is this true? I would like to see a galvanized object that has an even color & does not require a paint topcoat to make it look nice. I am well aware the protective abilities of galvanizing is not compromised by it's visual appearance, but that is not the question. Any information will be greatly appreciated.
Thanks.
Mark Taber- Boston, Massachusetts
2001
A. Is that a mouse grey or pearl grey? Steel Chemistry will have the final word on what galvanized structural members will look like. Galvanizing is a zinc-iron alloy that can represent a wide range of "colors" based on ranges of steel chemistry (silicon, phos, carbon...). Of course galvanized sheet can provide more consistent coatings that can range in different spangles and appearances (galvannealed). A galvannealed coating would tend to be a flat grey color that is consistent. I guess it depends on your steel supplier and your part/ steel that you are using as to whether I could show you something that is consistent in color. Galvanized steel will change in appearance over time as the material "weathers." If you can be more specific of the part or application I might be able to speculate if you can achieve this "gray even color."
M Stroia- Canton, Ohio
2001
Q. Here are some of the specifics: Finish applied to structural members, not sheet steel. Uniform "frosted window" look desired, shiny not mat. What causes a matte grey finish instead of a shiny reflective one? Or a shiny surface mottled with matte grey? I don't have a reference for a 'mouse grey' vs. 'pearl grey', & need more info. to respond to that question. I appreciate your response.
Mark Taber [returning]- Boston, Massachusetts
2001
A. Hot dip Galvanizing is an iron alloy layer comprised of different combinations of zinc and iron. The eventual appearance of the product will depend on steel chemistry of the product being galvanized, time of product in the kettle, and the retention of heat in the product after withdrawal. Silicon, Phosphorous, Carbon and Manganese in steel have the most profound affect that can lead to heavy and potentially brittle coatings if in excess (ASTM ASTM A385). This coating will most likely be dull and frosty. When these levels are exceeded the iron in the zinc-iron alloy coating comes to the surface. When a product is brighter the pure zinc layer comes to the surface leaving a brighter coating. The pearl grey and mouse grey reference was a little sarcastic, since it is very difficult to project the result of a product without knowing steel chemistry or the product. Different galvanizers use different additives to the zinc bath such as nickel, bizmuth, aluminum, and tin to change the appearance of a coating and to aid in the types of products that they run in there area. The American Galvanizers Association can help you with some technical question as well as provide literature to explain this a little better.
M Stroia- Canton, Ohio
2001
How does galvanized steel get its look?
Q. My situation: Hi everyone. My first post here so apologies for the newbie question. I've searched online and in this forum but couldn't find an answer to "how does galvanized steel get its looks?".
I understand the process (molten zinc bath) but I don't understand how the 'dots' with several tones of grey get formed. What influences the size of the dots? And the color? and why is it not homogeneous? Any way to achieve the same look without the molten zinc bath?
Thanks for the support.
metal researcher - Dendermonde, Flanders, Belgium
July 2, 2018
A. Hi Francisco. I am not a galvanizing expert, but I don't think the mottled, crystalline look of galvanizing is a lot different than that of hot-dipped tin or a frosted windowpane. As the molten metal or the condensed water cools, crystals start growing simultaneously from a number of spots … and eventually they run into each other. The lightness or darkness is probably due to the orientation of the crystals (exactly perpendicular to the surface or the reflected light or somewhat askew).
People may have tried to control the mottled look via different amounts of silicon, galvanizing temperature, immersion time, withdrawal speed, or whatever to control the number of seed points but personally I know nothing about that. When soldering a wire in place if you accidentally let it wiggle at just the wrong time you get an unreliable "cold solder" joint with a mottled or grainy gray look.
Regards,
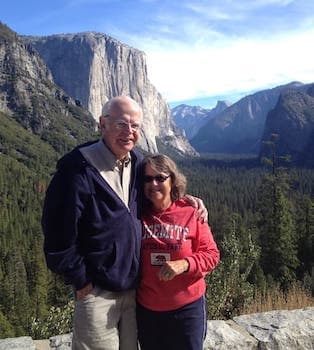
Ted Mooney, P.E. RET
Striving to live Aloha
finishing.com - Pine Beach, New Jersey
July 2018
A. I'd recommend that you go to galvanizeit.org (the website of the American Galvanizers Association) and put 'spangle' in the search box.
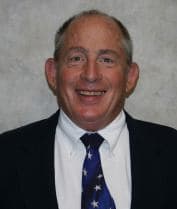
Tom Rochester
CTO - Jackson, Michigan, USA
Plating Systems & Technologies, Inc.

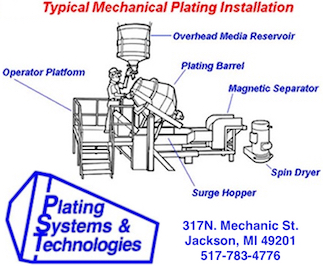
July 16, 2018
A. Some things "just are" ! How does tree bark get its look?
Galvanizing is zinc alloyed to steel. That alloying varies in nature as steel varies a lot from one piece to another - the chemistry is different in minor ways, but enough to affect the formation of that alloy formed which is galvanizing. Si is especially influential, but P also has a part to play. Examining test certificates of steel shows the varying chemistry, even within one grade of steel.
That variation changes the way the crystals of zinc and alloy form, and that changes their appearance.
Colour changes can come from two main sources. The composition of the alloy (can be up to 10%Fe, 90% Zn), and the level of oxide formed, or deposited on the surfaces.
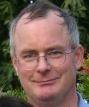
Geoff Crowley
Crithwood Ltd.
Westfield, Scotland, UK
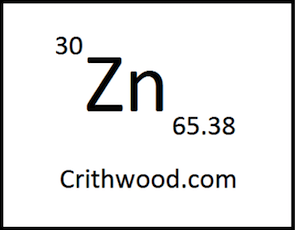
August 15, 2018
Q, A, or Comment on THIS thread -or- Start a NEW Thread