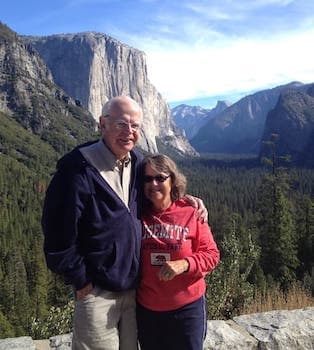
Curated with aloha by
Ted Mooney, P.E. RET
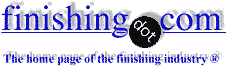
The authoritative public forum
for Metal Finishing 1989-2025
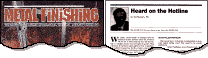
-----
Zinc Ammonium Chloride Solution Heating
2001
I am a consultant working for a hot-dip galvanizing facility on some process improvements. The main concern is the temperature of the zinc ammonium chloride preflux tank. The desired tank temperature is 160 F; heating water is available at 190 F. The ONLY metallic material the owner has found that withstands this solution is AL6XN stainless steel. Unfortunately, the low temperature differential results in a lot of heat exchange area. Since AL6XN seems to only be available as tube stock, this results in an inordinate amount of serpentine (bent tube) heat exchange coils. Plastic coils would withstand the solution (the tank itself is PP) but again result in a huge amount of heat exchange area due to poorer thermal conductivity of plastic as opposed to metallic materials.
How have other companies avoided this problem? Any help would be appreciated.
Stephen Angstadt- Leesport, Pennsylvania, USA
2003
We are working with a local galvanizer who swears by plate and frame heat exchangers with Alloy C-22 plates for heating zinc ammonium chloride solution.
The heat exchanger is piped outside the tank and the solution recirculated with a plastic pump.
These units are available from at least one major plate and frame heat exchanger manufacturer.
manufacturers - Beaverton, Oregon
2005
Titanium Coils are used to heat zinc ammonium chloride flux solution with an expected lifetime of 20 years.
Dr. Thomas H. Cook
Galvanizing Consultant - Hot Springs, South Dakota, USA
Do any Material Safety Data Sheet for this flux?
Tomas Kandrastudent - Slovakia
October 29, 2008
Q, A, or Comment on THIS thread -or- Start a NEW Thread