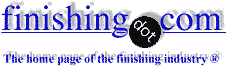
-----
Concentration of Passivate Bath (Nitric for Stainless)
Our stainless steel passivate bath (30% nitric) has caused severe dulling of the part. I am not sure that our bath is made up at the correct concentration. Could someone give me some guidance as to what the nitric concentration should be and why this dulling occurred.
Karen Phillips- Charlotte, North Carolina
2001
Different stainless alloys require different passivate "baths" to avoid damage or discoloration of the material.You can refer to the current spec. which is ASTM A967 -99 or the old standard, Mil-Spec QQ-P-35C (canceled) [link is to free spec at Defense Logistics Agency, dla.mil].
Good Luck.
Bill Grayson- Santa Cruz, California, USA
2001
![]() |
Run some samples on a 20% by volume of nitric acid with 2-3% of sodium dichromate. Ask your customer for process specifications on this particular part. The parts may dulled due to contamination in the bath. A good rule of the thumb would be to test a small batch of parts prior to start-up. Another reason the parts could dull can be load size. Regards, Joel Garcia- McAllen, Texas 2001 Hello Karen! To add onto Bill Grayson's answer: ASTM A967, AMS2700, and QQ-P-35 all list recipes for passivation solutions and recommendations for using which bath for which grade. Yet the olde, cancelled, federal specification QQ-P-35 is freely available on the Net. Go to assist.daps.mil to get to the ASSIST page, and use the Quicksearch button to get the search screen. Type in QQ-P-35, and you'll get the pdf file of the old spec. Table 1 has the recipes, table 2 has the recommended baths for various stainless grades. We "solved" our longstanding problem of etching on 416 and 440C grades by switching away from a type II bath, to a type VIII bath for those grades. I hope this helps! ![]() Lee Gearhart metallurgist - E. Aurora, New York 2001 |
2001
Karen:
You probably have one of two situations:
2) You have a "poorer grade" of stainless which can do this sometimes in nitric acid.
You can resolve either of these situations by using a citric acid bath which meets ASTM A967. Some formulations are safe for all grades and gives excellent performance compared to nitric.
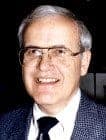

Lee Kremer
Stellar Solutions, Inc.

McHenry, Illinois
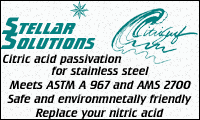

this text gets replaced with bannerText
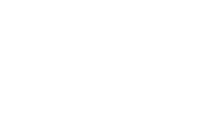
Q, A, or Comment on THIS thread -or- Start a NEW Thread