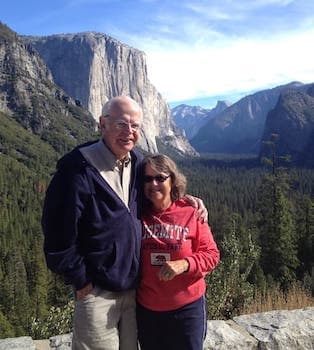
Curated with aloha by
Ted Mooney, P.E. RET
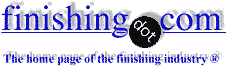
The authoritative public forum
for Metal Finishing 1989-2025
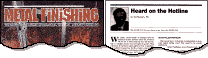
-----
HOURS OF CORROSION RESISTANCE
2001
Dear Sir,
We would like to know the number of hours the following metals/finish will withstand salt spray test/natural corrosion.
- SS 403
- SS 304
- PRECOATED METAL SHEETS
- POWDER COATED CRCA SHEETS
- NI-CR PLATED CASTINGS (12 MICRONS)
- ZINC PLATED (12 MICRONS) ON CRCA (YELLOW & BLUE PASSIVATION)
Thanks
KARTHIK SOMANATHAN- Bangalore, India
Why not run some salt spray tests, Karthik? That's the only way to get real answers; as card players say: a peek is worth a thousand finesses :-)
If you can describe your real-world situation, I think you'll get more satisfactory responses than I can give you in response to these abstract questions.
Note that a powder coated sheet will have much better salt spray resistance than a zinc plated one, yet highway guard rails are usually zinc plated or galvanized. 12 microns is a fairly heavy thickness for zinc plating, but very light for nickel-chrome plating. Salt spray is not a useful test for nickel-chrome except as a go/no-go porosity test. I believe that a given grade of stainless steel will either remain rust-free or rust immediately in a given environment--I don't think it's a matter of how long it retains rust resistance before giving out. Please try to make your questions "real world" and you're likely to get better answers. Good luck!
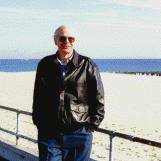
Ted Mooney, P.E.
Striving to live Aloha
finishing.com - Pine Beach, New Jersey
2001
Are you looking for the first sign of red rust? There are many ways to measure how long something lasts in salt spray. Some look at white corrosion instead of red rust, and some look for 5% instead of the first sign of corrosion.

Tim Neveau
Rochester Hills, Michigan
2001
Sir,
The subject of corrosion is somewhat complex.What is good for one situation may not suit the other. There is aesthetic and functional values to be preserved in some cases. In some of them one may be more important than the other. You may kindly see the galvanic series in the web site, www.powers.com/CarbideBit/2.3.htm
[Ed. note 11/27/06: that page is apparently no longer functional].
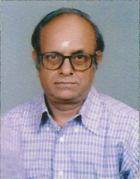
Subramanian Ramajayam
consultant - Bangalore, India
2001
Q, A, or Comment on THIS thread -or- Start a NEW Thread