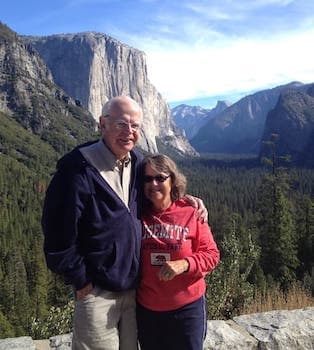
Curated with aloha by
Ted Mooney, P.E. RET
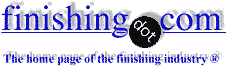
The authoritative public forum
for Metal Finishing 1989-2025
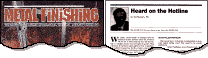
-----
Electropolishing Solution Purification
2001
My question concerns the maintenance of electropolishing solution used for electropolishing 300 series stainless steel and incolloy components.
Per our suppliers' recommendation, we maintain the solution at an iron content of less than 3%. When the solution reaches this level, we lower the iron content by decanting a portion of the working solution and replacing with fresh electropolish solution. The decanted solution is sent to waste treatment. As you are aware, this is "throwing out the baby with the bath water". I am looking for alternate methods to lower the iron content without decanting. Our supplier says they are not aware of any alternate methods.
I would think it would be difficult to circulate the undiluted solution through an ion exchange cartridge as it is very viscous. The solution is approx. 95% phosphoric acid, with the remainder additives and water.
Any suggestions would be appreciated.
Thomas Kemp- Erie, PA, U.S.A.
Insoluble impurities are easily settled out and decanted so that particulate can be removed. However, dissolved metallics are another issue. The dissolved metals are extremely difficult to remove, as the acids used in this electrolyte are very concentrated.
Iron will not precipitate from the electropolish solution by addition of a coagulant. Ion exchange is impractical since the high concentration of the aids used in the electrolyte drive the equilibrium reactions used in ion exchange in the wrong direction.
Bleed and feed becomes the most viable, economical choice. It is possible that an electrodialytic method might be used, but the capital equipment cost would be very high in relation to the cost of solution saved and waste treatment cost. The payback time would be very long.
Charles R. Reichert CEF-SE- Seattle, Washington
2001
Q, A, or Comment on THIS thread -or- Start a NEW Thread