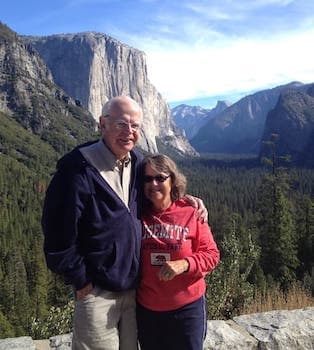
Curated with aloha by
Ted Mooney, P.E. RET
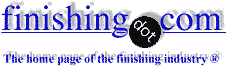
The authoritative public forum
for Metal Finishing 1989-2025
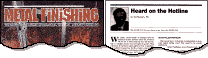
-----
Stainless Steel Contamination During Welding
Q. Help, I have to provide an on site training program explaining the do's and don'ts during stainless steel process pipe welding.
Problem, rust appearing after several days in an open and exposed lay down area. There is no question after surveillance that the operators are using carbon contaminated power brushes.
Since this facility is regulated by the FDA, OSHA 1910.119 and EPA Part 68, (Process Safety and Risk MGT), I would like to address the serious down the road issues of mechanical integrity.
Walter Shelton- Knoxville, Tennessee, USA
2001
![]() |
A. I don't know that carbon contamination on the brushes is a big problem, but if they are not using stainless steel brushes, that is a problem. Steel brushes, or even stainless steel brushes that have been used on plain steel, leave free iron contamination that can lead to corrosion. The risk is probably more likely to be pitting corrosion and leaks in the pipe rather than a mechanical integrity problem. Surface oxides from welding can also be a cause of reduced corrosion resistance. Chemical passivation of the weld zone is the best preventative measure. ![]() Larry Hanke Minneapolis, Minnesota 2001 A. I think that you will find that it is the iron in the power brushes that is the problem. Even 410 brushes will promote rusting. Try a very coarse grit on the scotch-brite insert Scotch Brite grinding pad [affil links]. James Watts- Navarre, Florida 2001 A. Walter, You have a tough task ahead of you. Trying to teach construction welders that merely touching a stainless steel brush to carbon steel will contaminate it is something they have always heard but don't really understand, much less believe. But, it's real. Talking about invisible chrome oxide films just goes in one ear and right out the other for some (though not all). I have seen rust on process equipment just from welding or grinding on carbon steel in the general proximity. Grinding stainless steel welds with mild steel brushes will have the pipe looking like a dalmatian dog in no time. Once the rust has bloomed, it is my opinion that if left untreated, the rust can progress into pitting corrosion. Then, the galvanic differential between the passive metal and rusty surface makes overall passivation very difficult. The rust will haunt you from that point on. In Oklahoma recently, I saw a tank that now has pinhole leaks in the weld zone, apparently from improper heat tint removal on the interior welds. The same is true for cases of MIC- microbiologically induced corrosion. In time, the weld zones are weakened to a point that there is very much a safety issue at stake, particularly with process safety management applications. I have also found the corrosive process environment around one specific vented tank caused all welds in the area to bloom with rust. At the time of construction, these welds had all been polished properly (no carbon steel brushes). After a decade of production, all the welds still looked great with the exception of those within 12' of this specific tank. Not only is it crucial to remove the heat discoloration, further chemical or electro-chemical passivation may be needed as well. How corrosive the environment (both inside and outside the tank) will dictate the type passivation required. Todd Turner- Monroe, Louisiana 2001 |
A. I had a similar problem with rust on welds that had been cleaned with type 302SS brushes. I finally resolved this by doing testing with a salt spray chamber. Here's what I found: Brushes made of 302SS are pure poison, 304SS will leave small amounts of rust on the surface. 316L works flawlessly, as does scotch-brite types of abrasives. The larger diameter bristles were the worst for contamination.
My theory is that with power brushing the end of the bristle can become sensitized and smears iron rich material across the surface. I believe this to be true since we can take a hand brush and clean a weld with a type 302SS bristle, this will pass a 24-hour salt spray test. Go figure!
Since my testing we strictly use 316L brushes or abrasive impregnated polymer fibers (scotch-brite), and we haven't had any problems.
Best of luck with your training,
Bradford P. Maas- Northfield, Minnesota, USA
2001
A. Everyone is saying the same thing to you in different ways, you have free Iron on the surface & have destroyed the "oxide film" on your Stainless steel, you need to remove the free iron and re-passivate the Stainless. In-situ electropolishing using an experienced operator is the best answer, learning to do it yourself and purchasing the necessary equipment will solve all future problems.
Regards

John Tenison - Woods
- Victoria Australia
2001
Q. Gents,
We are just about to receive in our fabrication shop Carbon Steel and Stainless Steel pipe for our current project in Nigeria
Can anyone give me a safe minimum distance to segregate CS and SS316.
I have always segregated CS and SS without really understanding why.
Thanks for the previous tips.
- Port Harcourt, Rivers State, Nigeria
September 22, 2011
A. Contamination can occur simply from steel dust in the same area as stainless steel fabrication and welding. Always do your welding in a clean swept up area in the shop or plant as far a distance as possible from other metals. Use a coated stainless wire with corresponding gas for MIG or FLUX CORE, and purge inside when welding pipe or vessel. TIG process is sometimes more difficult to keep free of ions. Wipe weld areas first with mild acid solutions and have good ventilation. Clean with a Walter or other electro charged cleaning machine (it may clean ions from surface). CLEANLINESS IS NEXT TO GODLINESS.
Edward BananeCornwall Consultants - Mississauga Ontario, Canada
March 14, 2015
Just wanted to say what a great resource this place is and how helpful all of your opinions are on this subject. I work for a metal manufacturer and wanted to learn more about how to avoid stainless steel contamination and this discussion has really been helpful in my understanding. Cheers!
Estimator - Yorba Linda, California USA
February 10, 2015
Thanks for the kind words, Don!
For readers who just happened to stumble upon this page, we have 50,000 other threads about metal finishing, so remember us whenever you have a finishing question :-)
Regards,
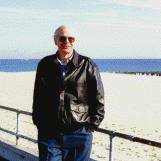
Ted Mooney, P.E.
Striving to live Aloha
finishing.com - Pine Beach, New Jersey
February 2015
Q, A, or Comment on THIS thread -or- Start a NEW Thread