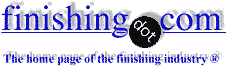
-----
Hardness Testers
2001
WE HAVE TWO WILSON DIGITAL HARDNESS TESTERS. FOR THE PAST FEW MONTHS THEY HAVE BEEN GIVING ERRATIC READINGS. THEY ARE KEPT IN A ROOM WHERE THE AMBIENT TEMP VARIES FROM 30-42 DEG C. WE FIND THAT THERE IS A VARIATION OF EVEN 4 TO 5 RC AT TIMES ( ON STD WILSON TESTBLOCKS WITH ± 0.5 RC) .
THE LOCAL AGENT SAYS THAT THE HARDNESS TESTERS SHOULD BE KEPT IN A AIR CONDITIONED ROOM. MOREOVER THE AGENT SAYS THAT HE CAN GUARANTEE AN ACCURACY OF ONLY ± 2 RC ON THE MACHINE AND ADDS UP THIS TO THE TOLERANCE ON THE BLOCK (±0.5) AND SAYS THAT THE TOTAL ACCURACY WHICH CAN BE GUARANTEED WILL BE ± 2.5 RC. THIS TRANSLATES TO 5 RC.
DOES THIS NOT DEFEAT THE VERY PURPOSE OF HARDNESS TESTING AFTER HEAT TREATMENT? CAN WE ACCEPT SUCH MACHINES ACCURACY? OR DO WE NEED TO REDUCE THE HARDNESS RANGE ON THE COMPONENTS TO accommodate THE HARDNESS MACHINES TOLERANCE ?
CAN SOME ONE THROW SOME LIGHT ON THIS. ?
R.HARIPANTH- Chennai,Tamilnadu, India
2001
The expected accuracy of the machine will be somewhat dependent on the hardness that you are testing. According to the ASTM E18 specification for Rockwell hardness testing, I think that the tolerance is ±0.5 HRC for >60 HRC and ± 1.0 for < 60 HRC. The variation of the values that you measure for the test block should be within the range for the test block, i.e. ± 0.5 for test blocks harder than 60 HRC.
I suspect that you have a problem with either your testing technique or the tester. The temperature range that you report is pretty extreme, but I don't think that it is the problem. Our tester, which is probably over 20 years old, is in a space where the temperature varies almost that much over the year cycle and calibrated right on the money last week.
The first thing that I would check is the condition of the elevating screw and bearing surfaces. If these surfaces are not clean with a light oil on the screw threads, you can get the variation that you describe. There is a special oil that should be used on the screw. If this has not been maintained regularly, this oil may have hardened. I would expect that you would see hardness values generally lower than the test block value if this were the problem.
Good luck.
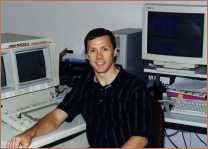
Larry Hanke
Minneapolis, Minnesota
Q, A, or Comment on THIS thread -or- Start a NEW Thread