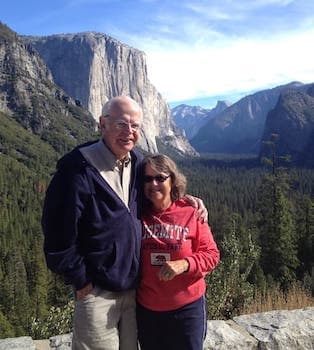
Curated with aloha by
Ted Mooney, P.E. RET
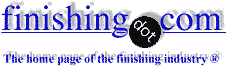
The authoritative public forum
for Metal Finishing 1989-2025
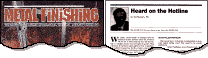
-----
Problems soldering on nickel and gold plated electronics
Q. Can anybody please share soldering method for TO-8 Packages having flash gold with 0.2µm gold with electroless nickel undercoat of thickness 2.5µm, Kovar base material?
Meghal DesaiEngr. - Gujarat, INDIA
July 25, 2023
A. Hi Meghal. Could you please try to make it a bit less abstract by telling us what you have been trying and what problems you are seeing ... and what kind of gold plating you are doing? Thanks.
Luck & Regards,
Ted Mooney, P.E. RET
Striving to live Aloha
finishing.com - Pine Beach, New Jersey
⇩ Related postings, oldest first ⇩
Q. Can someone tell us how to clean nickel with a gold flash on it prior to soldering? The problem appears to be excessive nickel oxide or nickel hydroxide on the surface.
We routinely reflow lead-tin solder contacts to electroless nickel overplated with a thin electroless gold flash (around 4 microinches). The solder is deposited in a paste form with acid flux in the paste. The solder is eutectic, and the reflow has to be done at low temperature (less than 230 °C).
The solder usually adheres well, but in some cases the bond is not strong. Solder will adhere to most of the nickel area, but peels off other parts. When we analyze the defective areas we find that there is residual nickel oxide and 9 to 11% phosphorus. In some cases we also see boron.
The gold flash usually shows nickel oxide on its surface, either from incomplete rinsing or pinholes.
- San Diego CA
2000
A. If I understand your problem correctly, first of all you should not see any pinholes exposing nickel or its oxide on a gold surface. Exposed nickel probably oxidizes during/after hot soldering process. You may just need a thicker gold flash. If the gold is peeling off from the nickel surface, and you could see it on the peeled solder, the acid dip before gold plating is inadequate.
Mandar Sunthankar- Fort Collins, Colorado
Multiple threads merged: please forgive chronology errors and repetition 🙂
Q. Dear Friends:
Has anybody ever faced soldering problems on Printed circuit boards that have finishing electroless Au over Nickel? I have a strong problem by trying to solder on these PCBs produced 1 year ago. I identified that there is oxidation on the Nickel surface when I drop down a board with 4 BGAs and one of them Jumps up. We tried to HASL the boards we succeeded, but now I am afraid that we are facing the black nickel phenomenon and it is not possible at all to solder specifically small joints even with soldering iron and aggressive fluxes.
I would appreciate any help form anyone.
Regards,
Spyros PallesIntracom SA - Peania, Attica, Greece
2001
A. Two suggestions:
1. Are you using electroless Au or immersion Au? This actually becomes a thickness issue.
2. Have you checked the Au deposit porosity?
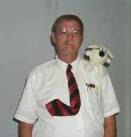
James Totter, CEF
- Tallahassee, Florida
Multiple threads merged: please forgive chronology errors and repetition 🙂
Q. Hi,
I'm a QC Manager for an electronics manufacturing. One of our products is PCBA, pure SMT, for cell phones. It has a gold finish and the problem is that the solderability looks really bad. The solder is very rough and not so shiny. All process parameters have been checked and the same parameters yield good results with HASL PCBs. I suspect that the PCB gold finish is too thick. Could this be what's causing the problem? Thanks.
Jay Chavez- Manila, Philippines
2001
A. Jay,
I have a lot experience with solderability. Most my experience is for silver, tin and tin-lead alloy on surface mount components. Let me see if I can help.
It is highly unlikely that too thick of a gold plating can cause your solderability problem. In fact, too thin of a plating will show failure after steam age solderability. Solderability has two failure modes which are de-wetting and non wetting. de-wetting can be caused by oxidation on the base metal material that you are soldering to, surface contamination underneath the final coating, or final protect coating is too thin or doesn't provide the protection during the steam age process. Non wetting is the top coating (gold) doesn't wet or take solder. This could be by surface contamination of the gold surface. In this case, a good activated flux or surface cleaning can fix this problem. Other things to check for, is to make sure your solder pot is in spec and free from contamination.
Hope this helps!
Karl Weyermann- Lebanon, Kentucky
A. Hi Karl,
Doesn't the gold eventually become a contaminant in the solder pot? So long term, thick gold plating may end up being the limiting factor for the life of the solder pot, "causing", in a way, the solderability problem. If the pot remained within specification for gold contamination, then the only problem is wasted gold.
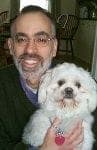

Tom Pullizzi
Falls Township, Pennsylvania
A. Tom,
Yes, eventually gold will become a contaminant in a solder pot, and it may affect solderability. However after this point, everything will start failing solderability using the same solder pot. Not just parts with thick gold. Solder pots need to be changed regularly. In fact, it is cheaper to change most solder pots, with fresh solder, than to perform analysis to check for foreign contamination.
Karl Weyermann- Lebanon, Kentucky
A. Perhaps a good starting point is to define is how thick is the gold? Then is it too thick? Since gold is soluble in a "solder pot" assume tin/lead....60/40 ...90/10 The gold is only there to protect the solderability of the underlying base metal.i IF the underlaying base metal is free of oxides and in a "solderable" condition then the gold is the Saran Wrap to preserve it. Gold does enter the equation as it is soluble and can contribute to brittle solder joints but that gets to be blah blah blah to this situation. Dull solder from poor cooling or bad wetting angle all are another subject.
Jon Quirt- Fridley, Minnesota
2002
A. I think, as the first poster, that it is a contamination on the surface. Usually it will be removed when running the PCBs in an acid cleaner.
Peter Fogel- Sweden
2002
Q. Hi
I'm a QC inspector, I facing a problem with the gold plating with solderability.
If gold plating gets stuck with mold flash will it become non wetting after solderability test?
electronics - Singapore
2005
A. A few years ago, I requested gold plating on one of our PCBs as part of changing over to surface-mount technology. The solderability was terrible. I was told that gold plating above a certain thickness creates bad joints because the gold dissolves in the solder and creates a brittle, nasty-looking joint. The next iteration, I went with "Immersion gold" which is much thinner. Solderability was excellent, and we have done all boards with immersion gold since then.
Paul Boisseau- Lexington Massachusetts USA
August 4, 2008
Q. Currently I have an application that uses gold-plated nickel posts as an interconnect between two components. Gold thickness is ~15-50 microns. Solderability of the gold is fine and the process works well overall.
As part of a cost saving initiative, we thought of eliminating the gold. Any concerns with pure nickel solderability? Any "watch out" I need to be aware of?
- Minnesota
September 13, 2012
A. For solderability, from my experience, electroplated nickel is better compared to electroless nickel. And for electroless nickel, the higher the P content, the lower the solderability. Good luck.
SK Cheah- Penang, Malaysia
A. With standard tin/lead solder, gold dissolves in the melt to form intermetallic compounds, particularly AuSn6. On cooling, this forms acicuclar (needle like) crystals which give a grainy appearance to the solder surface. They are also brittle and thus greatly decrease the strength of the joint.
If the gold is thin it can completely dissolve before the intermetallic concentration is enough to cause problems. On thick gold, intermetallic formation is enhanced by too high soldering temperature and/or time.
Specifying thick gold and trying to do a 'better' soldering job are both counter productive. 15-50 microns is far too much. 5 microns or less is more normal, possibly one over 5 microns of nickel would be better. Immersion gold, which is too thin to measure, is fine provided there is good. Control the solder bath/iron at about 200 °C. If you cannot achieve a good joint in under a second you need better flux.
coverage of the nickel to prevent it oxidising.
Mold flash is a disaster. You cannot solder onto plastic!
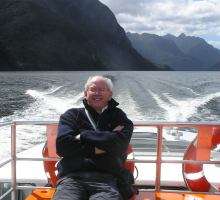
Geoff Smith
Hampshire, England
A. Yes. The gold thickness is way too high for a solder joint. It does effect the strength of the solder joint.
From ASTM B488 Standard Specification of electrodeposited coatings of gold for Engineering use, X1.1.4 Solderability - Type 1 golds are preferred for solder application. Oxidation of co-deposited metals can make soldering more difficult. It is strongly recommended that gold coating thicknesses not exceed 0.5 micron for solder application. There is evidence to show that when the gold content in the tin-lead solder joints exceeds about 3% by weight, embrittlement occurs leading to potential solder joints failure.
- Penang, Malaysia
Solder testing failure
Hi all,
Can all of you help me why after solder test we found a hole? Ni-Au plated.
- Kuala Lumpur
June 16, 2017
Q, A, or Comment on THIS thread -or- Start a NEW Thread