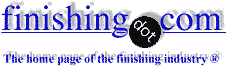
-----
Penetration And Growth Ratio on Aluminum Oxiding
Could I get an answer on penetration and growth ratio on aluminum oxiding set up to run in the proper conditions in accordance with MIL-A-8625 / MIL-PRF-8625 [⇦ this spec on DLA] type two and type three anodizing?
I know hardcoat is a lot thicker, but what is the ratio on both types? I have heard that hardcoat anodizing has 50% inward (penetration), 50% outward (growth) and regular anodizing is 1/3 inward and 2/3 outward. Is this correct?
A response would be greatly appreciated. Thank You!
Charles Schwartz- Madison Heights, Mi USA
2001
2001
The percent dimensional increase of an oxide formed under 'typical' Type III conditions (200 g/L sulfuric acid, 24 to 40 ASF, 32 °F) is about 50%. The penetration and outward growth are roughly equal. For Type II coatings the current density affects the percent dimensional increase (higher current density = more outward growth) but a 33 to 40% dimensional increase is to be expected.
You will have about 1/3 growth and 2/3 penetration, which is the reverse of what you have written. The difference in outward growth between Type II and Type III oxides is largely attributed to the increase in solvent action of the sulfuric acid as the temperature of the electrolyte is increased.
Here's a recent paper on the question. L.Zhang and S.H. Zhang, "Dimensional Changes of Anodized Aluminum", AESF SUR/FIN '99 Conference, Cincinnati, OH, June 1999.
Feel free to contact me for a copy.
Sjon Westre- Minden, Nevada
Q, A, or Comment on THIS thread -or- Start a NEW Thread