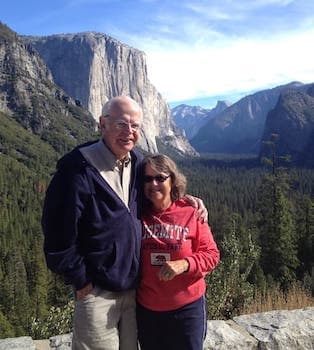
Curated with aloha by
Ted Mooney, P.E. RET
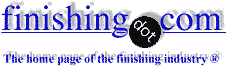
The authoritative public forum
for Metal Finishing 1989-2025
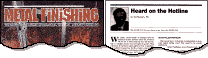
-----
Polyacrylic Acid, Cleaning, Phosphating, Metal Pretreatment
2001
Hi there can anyone shed some light on this subject?
I work with a 5 stage pre-treatment process for Galvanised steel. (Cleaner, rinse, phosphate, rinse, chrome passivation)
The phosphate stage contains phosphoric acid, zinc compounds, nickel nitrate and hydrofluoric acid)
Does anyone know of a cleaner/phosphate treatment that can be done all together - but that still can achieve 500-1000 hours of salt sprays which we are achieving at present?
I have read an article about a solution called ECOPHOR A/477 that can both degrease parts and provide a phosphate coating in one go. Has anyone heard of this?
I have also read an article about advanced zinc phosphate metal pre treatment that can increase protection up to 2000 hours salt spray. This method uses polyacrivic acid along with the zinc phosphate metal pre-treatment - the result to eliminate the hexavalent rinse without sacrificing any performance. Does anyone know anything about this?
Your comments on either of these topics would be greatly appreciated.
Lisa WallaceFG Wilson - Belfast, Northern Ireland
Actually, Ms. Wallace, it's probably more common to do the cleaning and iron phosphating together in one stage of a 3-stage sytem than it is to use a 5-stage iron phosphate system. More common ... not better. Zinc phosphating, to my knowledge, never combines cleaning and phosphating--for which reason it is done in 5-stage and 7-stage processes.
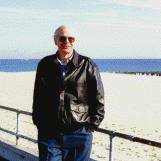
Ted Mooney, P.E.
Striving to live Aloha
finishing.com - Pine Beach, New Jersey
2001
2001
Hi
There are indeed dry-in-place coatings that will achieve well in excess of 1000 hours ASTM B117 salt spray under powder. They can be applied after cleaning (alkali or mild acid) and can be used by immersion or flood coating. A major advantage is effluent reduction and water savings, not to mention reduced control and maintenance.
I believe that ECOPHOR is a solvent based degrease-coater used in a vapour degrease type plant.
R
Roger BridgerWalterisation (UK) Ltd - Croydon UK
Hi Lisa,
Ecophor is a one tank process that works at ambient temperature. Version A448 is exempt from UK emmission regulations due to its very low VOC content. It produces no effluent. It can treat steel, aluminium, galvanised steel.
It produces better results in salt spray tests than conventional iron phosphate, but it is not as good as full zinc phosphate. The process can be enhanced to produce improved results but this would make it a 2 stage process.
In mechanical tests it would prove superior.
The process is extremely economical to operate as it requires no heating, no rinsing and no effluent is produced. Furthermore it requires no daily analytical tests to be carried out.
David JonesMorgan Newmark Ltd - Telford, United Kingdom
2002
Q, A, or Comment on THIS thread -or- Start a NEW Thread