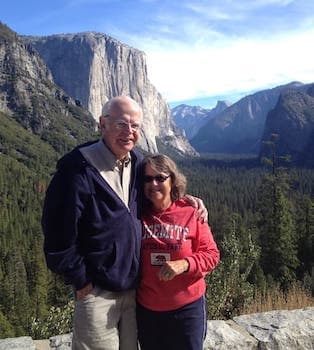
Curated with aloha by
Ted Mooney, P.E. RET
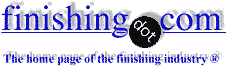
The authoritative public forum
for Metal Finishing 1989-2025
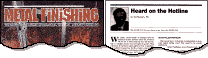
-----
Is Copper a Problem in Boiler Feedwater?
Q. What is the effect of high copper content in steam boiler feed water? Would it cause small holes in tubes.
Doug McMann- Stockton, England
2001
A. Doug - Yes copper in boiler feedwater can cause problems.
The boiler chemicals that are used are there to help form a magnetite coating on the boiler tubes and protect them from corrosion. Magnetite is black oxide and most black oxide chemistries have rectifiers in them to help control metals that otherwise would inhibit the black oxide conversion.
The pitting is because you have incomplete formation of the magnetite and are probably getting some scale and subsequent pitting.
I would look at blowing down the water in the boiler more often, and talk to your chemical supplier to see if they have any ideas for an additive to your current chemicals.
Good luck.
chemical process supplier - Gurnee, Illinois
2001
2001
A. Dear Sirs,
Copper can cause severe damage. In the lower part of the boiler with the highest heat input a rapid galvanic corrosion can take place (Cu2+ + Fe(s) => Cu(s) + Fe2+). But the copper also can with a higher content of oxygen act as a catalyst for magnetite formation (Shikorr effect) which will become a catastrophic oxidation.
Cutting out tube samples will reveal waterside corrosion and the formation of small needle shaped particles consisting of pure copper. A chemical cleaning of the boiler is necessary in these cases where copper has start to create damage.
Further, any attempt to perform weld repairs with high copper on the water side will can give brittle welds as copper will form in the grain boundaries of the weld and the material will therefore become weak and failures will appear brittle (liquid metal embrittlement).
It is therefore essential to keep the feedwater system with as low copper content as possible. As discussed below, just dosing chemicals a dangerous way to go. One should instead increase the knowledge and gain a better control of your condensate system.
The reason for copper contamination can be several but is normally originating from the return condensate, from heat exchangers or condensers made in copper or copper alloys.
Copper release is caused by too high local pH in the condensate system, high local concentration of dosing chemicals, high flow rate and/or high oxygen content. The maximum copper level into a boiler should never exceed 0.005mg/l (low pressure boilers <40 bar 0.01 mg/l)
Copper is sensitive too high pH especially in combination with ammonia ⇦ this on eBay or Amazon [affil links] solutions. The copper release can be multiplied with a high oxygen content. The pH in the condensate system should have a max target value of ph 9.3 (lower if the system has a non pressured parts) and oxygen level of max 10 ppb. Copper release is also sensitive to the flow rate and the temperature of the media. e.g., 2 m/s at 25 °C but only 0.8 m/s at 60 °C etc.
The fact that you have copper contamination is normally a sign of not controlling your condensate system. Instead of adding another chemical to your system do an audit and ensure that the analyses taken of the system waters are actually correct. Lab procedures, instrument calibrations, sample points and coolers can all contribute to erroneous analysis readings.
By better control and thereby possibility of improving the environment of the condensate system, e.g., the boiler water system will also gain. Depending on your type of mill, return condensate is a common source of contamination, e.g., oxygen, various corrosion products or process chemicals. By gaining control of your condensate system you might up saving on dosing chemicals and reduce dumping of contaminated condensate, which in many mills are big money.
Karl-Walter Edgren- Singapore
Q. Dear Sir,
How do you rate single filming amine boiler feed water treatment against conventional TSP based co-ordinated treatment ?
VISHWAS PATILMumbai, M.S. , INDIA
2005
A. There are two questions under this heading.. I will address both:
1) the response regarding copper in feed water originating from condensate was on target. There are many things that may contribute to this occurrance. Dissolved oxygen at levels of 7 ppb (or less)has been known to resulted in copper corrosion... Modern, well designed, DE-AERATORS can lower DO to 2-7 ppb without chemicals and..BELIEVE IT OR NOT.. A LITTLE OXYGEN @4-5 ppb IS GOOD FOR PREVENTING CORROSION! Mostly from ammonia or amines "degradation" used for pH elevation... from copper or "yellow metal" alloys in condensers. The pH should be maintained in the 9.2-9.4 range while realizing that a false positive pH result may be possible, depending upon corrosion products in the sample, temperature,etc.
2)Filming amines and TSP serve two (2) entirely different purposes and they should never be confused with each other. Think of filming amines as you would a thin film of animal fat covering the surface and TSP (trisodium phosphate ⇦ this on eBay or Amazon [affil links] ) as a chemical reactant with a metal atom (ion).That binds to that atom (most likely calcium).
John White- Beaumont, Texas
2007
Q. Sir,
Can anyone clarify what is the carryover factor for Cu in steam?
The reason for the question is, I have Cu in feed water as 0.01 mg/kg, but I need to guarantee in Steam is 0.003 mg/kg.
Is it possible to achieve 0.003 mg/kg in saturated steam with a feed water Cu of 0.01 mg/kg.?
Siva
- HYDERABAD, ANDHRAPRADESH, INDIA
March 26, 2013
Q, A, or Comment on THIS thread -or- Start a NEW Thread