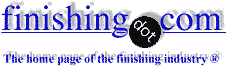
-----
Electrically Conductive Aluminum Anodizing
Q. I NEED TO SPEC A FLAT BLACK ELECTRICALLY CONDUCTIVE ANODIZE FINISH FOR AN ALUMINUM FRONT PANEL (IT HAS TO MEET EMI REGULATIONS). IS THERE ANY SUCH FINISH AVAILABLE? GARY
GARY H [last name deleted for privacy by Editor]DESIGN SERVICE - WILLOW GROVE, Pennsylvania, USA
2001
Treatment &
Finishing of
Aluminium and
Its Alloys"
by Wernick, Pinner
& Sheasby
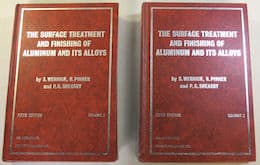
on eBay or Amazon
or AbeBooks
(affil link)
A. An anodized surface is an aluminum oxide surface, Gary; aluminum oxide is often selected because it is non-conductive, so anodizing would not be the most obvious finish for conductivity.
You might be able to apply a black chromate conversion coating, but I don't know if it would be attractive enough or robust enough. Another possibility might be to black chromium plate or black nickel plate the panel. But this would require zincating, followed by copper-nickel-chrome plating.
Or you might chromate conversion coat the inside of the front panel to keep it electrically conductive, then anodize and black dye the outside? This involves masking and might be more costly than you'd like though.
I guess my opening question should have been why do you want it anodized? Good luck.
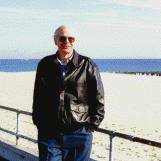
Ted Mooney, P.E.
Striving to live Aloha
finishing.com - Pine Beach, New Jersey
2001
A. I may be wrong ... but I seem to remember a company, a few years ago--I believe it may have been Metalast--that offered a "conductive" anodizing ... I believe that Ag was added to the bath to make the coating conductive. Once again, I may be wrong on the company, but I know someone out there was advertising conductive anodizing. But this may fall into the same category as Teflon "Impregnated" Anodizing.
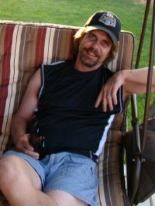
Marc Green
anodizer - Boise, Idaho
2001
A. Metalast does have an Ag bath that "seals" the anodic "pores", color varies from gold to brown depending on oxide thickness and alloy. This process lowers the resistance of the anodize and does NOT make the anodize conductive as the barrier layer is not penetrated.
Bill Grayson- Santa Cruz, California, USA
2001
Thanks Marc. Thanks Bill.
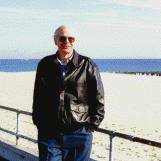
Ted Mooney, P.E.
Striving to live Aloha
finishing.com - Pine Beach, New Jersey
2001
![]() |
A. If you can afford an added process, simply coat the inside/backside of the parts with an EMI shielding paint. These typically contain silver, but there are nickel and carbon filled compositions as well. We have developed a composition that is based on conductive polyaniline that can be formulated with either silver or carbon to enhance the shielding effectiveness. Of course, for proper material selection, you will need to know the frequency range of the incident EM radiation and the level of shielding required. David Strawser- Ramat Gan, Israel 2001 |
A. There is such a thing as an electrically conductive hard anodize. The maximum thickness is about 1.0 mils.
Joe Mathews- Sterling Heights, Michigan, USA
2007
A. Gary,
I stumbled across this thread while researching a similar need for the same reasons for my work in the semiconductor industry. US Patent 6228241 applies to the multi-step anodize process required to achieve a conductive anodized coating on aluminum. The patent was filed in the late 90's and there are several companies that provide that service.
Regards,
Stephen Coomer, ME/EE
- Tempe, Arizona, USA
October 8, 2010
Q. Would it be possible to put a conductive coating after the sealing process? I have customer also asking a conductive surface after anodizing and dyed it black.
S. Y. Yuen- Hong Kong, China
2001
Multiple threads merged: please forgive chronology errors and repetition 🙂
2001
Q. I am looking for suitable plating processes for plating an Al cast electronic enclosure:
The plating requirements are:
- Electric: Conductive coating (EMI/RFI shielding);
- Physical/chemical: Inorganic plating
- Corrosion resistance: up to 85% relative humidity qualification.
- Manufacturing/cost: repeatable for volume production (particularly the far East);
- Cosmetic/thermal: Homogeneity required; black (preferably matte) appearance for thermal emissivity purpose; We have tried electroless nickel (8 micron thick), followed by electrolytic black chromium. The surface finish appearance (cosmetic) was not great...
Do you know of any other alternatives that would fulfill our requirements?
Hoping to hear from you soon, I thank you in advance.
Goncalo Amorim- Ipswich/Suffolk, UK
A. Hi Goncalo. Is this a diecasting, pressure casting, or sand casting? Diecastings and pressure castings (automobile wheels for example) are routinely electrolessly plated or electroplated after zincating. Choices include zinc with black chromate, zinc alloy (such as zinc-iron, zinc-cobalt, or zinc-nickel) with black chromate, black nickel, or black chrome; there are several black precious metal platings, but they probably won't be affordable enough. We probably have many applicable threads on all of these subjects; please search the site.
It's hard to comment on your "appearance not great" because we know nothing about the casting method or quality yet, nor about how much skill and time & effort went into the attempt to plate with electroless nickel and black chrome. If you've spent months on the plating effort and it's not working, it's not working; but if you gave it a single shot and weren't happy with the result, that's pretty much to be expected of every finish :-)
Luck & Regards,
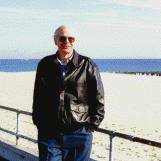
Ted Mooney, P.E.
Striving to live Aloha
finishing.com - Pine Beach, New Jersey
A. I think Metalast has a process that can give you hard coat anodizing with the conductivity you need.
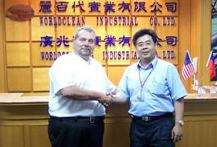
Drew Nosti, CEF
Anodize USA

Ladson, South Carolina
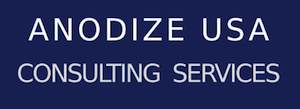
2001
2001
A. Cast aluminum can be a nightmare to plate because of its porosity. Common approaches are a heavy copper plate after zincate followed by nickel or electroless nickel and then the chrome. You need help from a specialist to get this down to a cold hard science as minute variables make a lot of difference.
Another approach would be to use a special formulation of the EN that could bridge the pits better. This may give you blisters later.
Finally, vacuum impregnation before plating has been used by several with good luck.
A better quality of casting might be the cure.
You might have to go to a high quality forging.
Possibly a less porous grade aluminum of aluminum casting metal (alloy).
Anodizing that is impregnated with silver to make it conductive may work. It would require testing to find out. Not many companies have that process. Metalast International is one. If you made your request more specific, people may be able to tell you.
James Watts- Navarre, Florida
Multiple threads merged: please forgive chronology errors and repetition 🙂
Electrically conductive Hard Anodized Aluminum?
Q. Is there a way to make hard anodized aluminum electrically conductive?
Greg Trepko- West Caldwell, New Jersey, US
2002
A. NO.
You can mask an area off to ground to and have it chem-filmed for some corrosion protection, but anodize is an electrical insulator and I know of no way to make it conductive.
Guy Lesterplating co. - Ontario, California, USA
2002
A. The best way to make it electrically conductive is to leave bare unanodized areas such as threaded holes. Another option would be electroless nickel. Electroless nickel offers the same as-plated hardness as hardcoat with better lubricity and is electrically conductive.
Todd Osmolski- Charlotte, North Carolina, USA
2002
A. Hard anodize is an electrically insulating coating.
You have 2 possible options:
1- You could mask off areas you need conductive, & finish those masked areas with a chromate conversion coating, & hardcoat the balance of the part.
2- METALAST - supposedly offers a way to restore conductivity to anodize / hard anodize coatings, but I know nothing about it.
David A. Kraft- Long Island City, New York
2002
Special Circumstance/ Electrical conductivity through coated 6061
2003Looking for "methods" to obtain electrical conductivity via a coating that can be applied over type III class 2 anodize.Coating will not be subject to outside environment issues as the compartment is o-ring sealed .
Build up should be minimal <.001". Item is a "cap". Threaded connection .75 X 24TPI with spring pocket : ass'y screws into A260 brass fitting installed in Delrin housing.This ass'y constitutes battery connection on one end of CR123 batt.Would like to spray or partial dip to get desired coating as to keep the Black finish on outside (visible) part of cap. Coating would need to coat threads and ID of cap to include spring pocket to complete current path, and be resistant to the rubbing forces at the threaded connection of the cap for repeated replacement of the batt.
If this "method" not doable ,please suggest all options including a masking technique( OD threads seem to cause problem: Dip protectant? one made?) for the area of current path that can let the whole part be anodized and the masking removed easily to expose the bare aluminum. Thanks in advance for your time.
Mark CarnifaxR&D thermal imaging/machine shop - Melbourne, Florida, USA
Earlier entries on this thread might be of interest to you; it discusses methods to make the anodize coating itself conductive.
Good luck,
Jim GorsichCompton, California, USA
2003
Multiple threads merged: please forgive chronology errors and repetition 🙂
Achieving 'electrically conductive' Satin finish for Aluminum
2007Q. I need to put a soft Satin finish on Aluminum machined knobs. Problem is that it needs to be electrically conductive. Out goes Anodizing. And Hard Anodize is cosmetically not a choice. My thinking is an acid etch (similar to first etch in anodizing) then Clear Chromate. Am I whistling Dixie here or does a "tried and true" solution exist.
Fred MayChief Engineer - Product Design - Balmain, NSW, Australia
A. Hi Fred,
Your thinking would work.
Anodizing: You may achieve the required cosmetic finish, but more than that the anodic layer is Bad conductor of electricity.
Regards,
- Chennai, India
2007
RFQ: Does anyone here know the contact details of the companies that offer the conductive anodized aluminum mentioned above?
Ojie Julian- Laguna, Philippines
August 1, 2014
A. Hi Ojie. One company was already mentioned 5X on this page; google them. This forum is free for us because supporting advertisers generously provide it for camaraderie & technical information exchange, and it's already pushing the envelope to mention their competitor 5X. Billing them the cost of maintaining contact details for that competitor might be a bit too much generosity to request :-)
Regards,
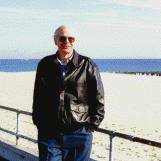
Ted Mooney, P.E.
Striving to live Aloha
finishing.com - Pine Beach, New Jersey
August 2014

Q, A, or Comment on THIS thread -or- Start a NEW Thread