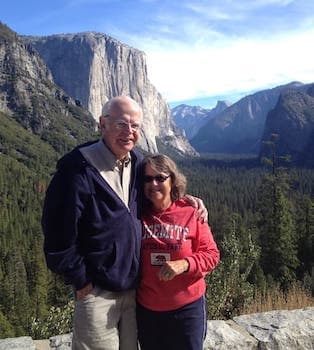
Curated with aloha by
Ted Mooney, P.E. RET
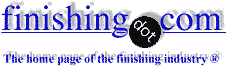
The authoritative public forum
for Metal Finishing 1989-2025
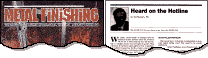
-----
Corrosion of SS316 in seawater RO desalination plant
Q. We are having a corrosion problem in the high pressure (800-900 psi) stainless steel piping of a recently commissioned seawater reverse osmosis plant. The corrosion started within one month of commissioning in the form of pinhole leaks at weld joints and also in the parent material. We are having trouble identifying why corrosion occurred so fast. The material used is SS 316L which is the predominant material used in similar plants in this area without such rapid rates of corrosion being observed. (OK, it's not the best material, but everybody else is using it around here, and we're not aware of anyone reporting corrosion so fast, and so extensively.) The feed salinity is about 40-42 g/l, and the concentrate salinity is probably around 60-63 g/l. Corrosion has occurred both on the feed and brine piping. Feed pH ranges from 6.4 to 6.9 after dosing of H2SO4 for scale prevention. We also dose 3 mg/l ferric chloride ⇦ this on eBay or Amazon [affil links] , FeCl3, as a coagulant. One reference mentions that FeCl3 is corrosive because it reacts with water to produce HCl, but at a dosage of 3 mg/l we don't think enough HCl will be generated to have a significant effect.
If anyone has any comments as to what the cause of this problem may be, some factor that we may have overlooked, or some reference or contact, we would highly appreciate it.
Sharaf F. Al-Sharif- Jeddah, Saudi Arabia
2001
A. The problem could be the original condition of the inside surface of the pipes. More rapid attack at the welds suggests that oxides from welding may have been left on the surface, which would accelerate corrosion. Other contamination away from the welds would also cause crevices that could initiate corrosion pitting.
Was the piping cleaned or passivated after fabrication? I doubt the FeCl3 is a problem unless it is added as a solid that somehow deposits on the surface. You have plenty of chlorides for corrosion without it. Are you sure that the pH has not gotten out of control and dropped below 6?
Hope this helps. Good luck.
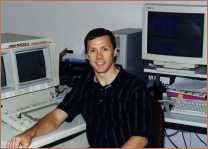
Larry Hanke
Minneapolis, Minnesota
A. We agree that if the welds were not passivated prior to exposure to the salt water, you probably have a problem. The welds will not be austenitic. Also, if it was not passivated, you could have free iron on the surface of the stainless that can start corrosion on the flat surface under these conditions. Once the corrosion starts, it can cause pit corrosion. We have seen this condition on 316L under saline conditions.
Let us know if we can help.
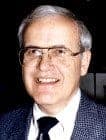

Lee Kremer
Stellar Solutions, Inc.

McHenry, Illinois
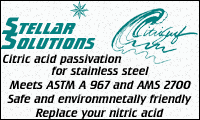
A. The problem is most likely intergranular corrosion. If the pits are small and deep you are in for some real trouble. Even 316L will experience this problem, welded or not. Salt water is very unpredictable around 316.
If the areas affected are localized, check for any contact points outside that provide any kind of electrical conductivity that can be eliminated.
Next, never place anything that will prevent airflow around the surface, even on the outside of the pipe. Insulation or even another welded on "tab" of 316 material inside or outside will cause this problem.
Eliminate any "battery" effect of dissimilar metal contact on the outside. We found that insulating with plastic/rubber to other materials made the problem even worse.
We have done work on medical vessels that stored salt water buffers, and most of the tank would be fine, but wherever mount pad was on the outside, the inside had spiderweb like pinhole corrosion adjacent to the pad/mount that was devastating. After we removed the parallel surfaces that existed on the outside, we experienced only a few spots some time later. We were able to trace those spots to how the tank rested against other objects (outside the salt water!), once again thermal insulation, and contact with another 316SS vessel.
Also,we have seen numerous boats using 316, passivated and electropolished, that exhibited pinhole corrosion but ONLY where there was contact, ie, under an insulation wrap, mount tab etc. There was no surface rust anywhere, only these pinholes that looked like a laser beam had pierced into the metal. Welding proved futile, the pattern only spread.
I spoke with a metallurgist from Westinghouse who had seen the same problem, but still couldn't explain it any better than this. He used 316 on our nuclear sub fleet and was quite interested in the problem.
Jeff Olson- San Leandro, California. USA
A. We had a different corrosion problem, but possibly similar phenomena, where we had sulfuric acid containing rinse water that was neutralized to a pH of 8.5 using sodium hydroxide, to floc out "heavy metals". When some tabs were welded to the outer (dry) mild steel shell of the lamella clarifier used for concentrating the floc, in-house, this resulted in rapid pin holing at those spots. The inner surface was asphalt painted, but the welding did not appear to have damaged this. The slurry water is fairly "salty", of course, as the floc does not contain, or remove the sodium, and other "light" elements, which are OK to discharge. Replacement lamellas were specified with similar tabs factory installed before an inner coating was applied, and the problem is solved.
W. Carl Erickson- Rome, New York
A. Sharaf, I'm sure I've seen this 'problem' on finishing.com before but never replied because of the very high pressures involved. But what Carl Erickson said about a 'coating' got me thinking.
From a corrosion standpoint, PVC is absolutely ideal but useless at high pressures and it has temperature limitations, too. But wasn't it DOW who used to supply, maybe still does, steel pipe LINED with rigid PVC? All flanged connections. Inner surface of the steel pipe was striated in some form or another to 'restrain' the PVC from thermal movement. In my field I recall some 12" dia. PVC:FRP pipe rated @ 200 psi which I supplied for some mine in B.C. The fibreglass outer (bonded!) wrapping is designed to take the pressure ... which could be much higher than 200 psi ... the weak 'link' in the chain, so-to-speak, is the connection, in that case the flange had to be pretty heavy.
I recall also in my 'metal' days the problems with super alloys of NiCr (not lowly 316 L stainlesses!) where the Moly would 'disappear' when the materials were welded, denudification, said the Chief Metallurgist at Henry Wiggin. Maybe, irrespective of post treatments, some of the stainless 'ingredients' also 'denudify' slightly when welding is done which leads to failure at welds. I dunno. The N.A.C.E. (National Association of Corrosion Engineers) organization would be able to help. However, back in the 70's they were a very BIASED group when it came to plastics! They held a conference in San Diego in '98 (or was it '97) where many dual laminate Companies from Canada and the USA were represented... & I gave them a copy of the first ever paper on dual laminates which came out around '74.
Have fun!
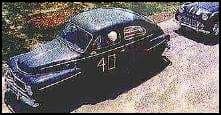
Freeman Newton [dec.]
R.I.P. old friend (It is our sad duty to
advise that Freeman passed away 4/21/12)
A. Before deciding any preventive action you may search for microbiological corrosion. Anaerobic environments may cause such corrosion problems.
Good luck
- Istanbul, Turkey
A. You are most certainly suffering from pitting corrosion. It is very aggressive because the localized pit is anodic to the whole rest of your system. SST304 and 316 stainless has a self-healing oxide that forms the first barrier against corrosion. 316 has the addition of molybdenum to increase its corrosion protection. You have 316L which is designed to stabilized against heat during welding; the alloying elements are less likely to migrate out of solution and into the grain boundaries. An earlier response mentioned that the welds might not be austenitic, and this is indeed possible in the heat-effected zone of the welds. But if this were the problem, I believe that you would be suffering from knife edge corrosion, that is, a thin line of corrosion/erosion that is at the boundary between the welds' heat effected zone and the base material. Your description really screams of pitting corrosion. Passivation of 300 series stainless was mentioned in several of the responses.
Passivation, typically nitric acid passivation, really is just a good aggressive clean for 316L, and will not provide any additional barriers to corrosion. Given a little time, 316L will form its self-generating protective oxide on its own. Acid passivation will remove ferrous debris that might be loosely adherent to the ID but gets flushed out in use, exposing unoxidized and vulnerable 316L to the elements. You may be able to flush the system with a citric-based product to achieve the same type of "passivation" or aggressive clean. Citrus based products (such as Citrisurf) are non-toxic to the environment once the pH is adjusted and have a chelating action that scavenges free iron rather well.
I think the biggest problem you have is that this aggressive environment is made worse by the ferrous chloride. Chlorides in general make SST304 and SST316 susceptible to pitting corrosion and ferrous chloride seems to make it even more aggressive. You may want to prove this to yourself in a simple experiment. If you can get three material samples of 316L and three plastic basins to hold them in. In one tub fill 2/3 with water (DI water if you have it) and add enough salt to approximate the salinity of your system. In the second, add 2/3 water and 2%-5% laundry bleach ⇦ bleach/sodium hypochlorite in bulk on eBay or Amazon [affil links] . In the third tub, add an appropriate amount of ferrous chloride to the water to model the concentrations in your system. Place your material coupons in the tubs and let them sit a couple of days. If you have access to an air line (or fish aquarium bubbler) you can gently circulate some air in the baths to speed up the reaction. On your daily checks of the samples, you will probably find no change to the salt bath sample, you may find some pitting corrosion on the bleach sample, and you certainly find lots of pits on your ferrous chloride sample.
Biological attack is a possibility, and some interesting work has been done in Mexico on the subject.
The PVC lined pipes mention sounds like an excellent idea, but I believe that Teflon lined SST hose and tubes are available and more compatible with your system.
Good Luck.
Chris FitzSimons- Lombard, Illinois
A. This may not apply because of the pressures involved but check any anti-seize compound or gasketing materials you use against the other companies that are using this metal.
Nuclear grade anti-seize is not as good as regular anti-seize but it was discovered that it reacted with some of the metals in the system. Hence nuclear grade anti-seize.
David Domm- Rochester, New York
A. It may be possible to protect by using sacrificial corrosion anodes. The anodes need regular replacement
Deval Yashawantelectroplaters - Pune, Maharashtra, INDIA
A. G,day Sharaf,
I don't know for sure. But, it sounds like cavitation.
Richard Bancroft- Parkdale Victoria, Australia
A. Hi Sharaf,
Once again. Ignorance is bliss, say some. Now I find out that, ah, large Companies have apparently been using very high pressure POLYETHYLENE in a steel pipe.
One mode is using heat(By British Gas, apparently) and another is a so-called friction fit. Again, I'm only repeating what I have been told but currently a Company called Prolite (Maple Ridge, British Columbia) say they are working on 3 different projects one of which has 5" dia. pipe running at 1,000 psi, a slurry application for an Alaskan mine. Their 'edge, they say lies in the connectors. Apparently this friction fit system has been done, they say, on a l,000 feet of pipe at one time. But then these are all mining applications where abrasion is more of a problem than mere acids or weak saline alkalies.
If you go on the internet and hit 'Plastic lined steel pipe' you'll find quite a few Companies offering this option but mainly with the far superior but FAR, FAR costlier fluorocarbons which would also have a MUCH, MUCH thinner wall than the Pe!
The crux, in my opinion, would be the connectors. The big advantage a Polyethylene mine piping specialist would have is that they really know a lot more about abrasion and sufficient bend radii and the demand, in this industry, for totally smooth connectors to prevent premature abrasion.
There may be doubts that these Poly:steel pipe systems would be good for vacuum but they should be vastly inexpensive, I'd guess, compared to most others and perhaps should cost less, too, than even a high grade 3l6 stainless.
Interesting, eh? Food for thought, anyhow. And no, I am in no way involved with that Company!
Cheers!
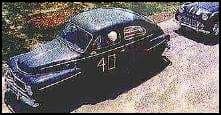
Freeman Newton [dec.]
R.I.P. old friend (It is our sad duty to
advise that Freeman passed away 4/21/12)
A. Sounds like you had something hard in the pipe pre start-up or something broke on start-up. If the inside of the pipe is scratched then it will pit quickly due to cavitation. The welds are a different problem. Anyone who leaves something in a high pressure pipe probably did not finish treating the welds.
Geoff Croker- Melbourne Australia
August 19, 2008
A. The leak may be of the improper Welding.
The filler material used may be of wrong one.
- Hosur, India
May 10, 2009
A. I am operation manager of water desalination company in iran. In all of our plants installed near persian gulf (SWRO)
we have the same problem but we offered hpp pipe duplex (2205) and after 2 month corrosion started from welding point and Victalic connection.
In my opinion corrosion may occur in case of oxygen in water, and oxygen in sea water acts the same as a battery and the welding point becomes an anode.
- tehran, iran
April 9, 2011
Multiple threads merged: please forgive chronology errors and repetition 🙂
Q. We manufacture desalination plants. Pressure vessels used are of fiberglass. All pipework is done with Duplex Stainless (S31803). We have found some corrosion on the duplex close to welding seams. There is an alternating magnetic field present inside pressure vessels. Can the magnetic field be the cause of corrosion?
Johan MullerPlant manager - Singapore
2003
A. Hi Johan,
Re your question on magnetic fields, I haven't got a clue! But would not think that that would be a cause.
Please go the archives and have a gander at 19760, as this might throw some light on your problem.
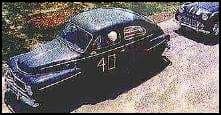
Freeman Newton [dec.]
R.I.P. old friend (It is our sad duty to
advise that Freeman passed away 4/21/12)
A. CP titanium is the answer.
Skip Schaeferheaters and controls - Oxnard, California, USA
Q. We manufacture commercial and industrial reverse osmosis water purification systems. Most are for brackish feed water but we do make some sea water systems. We have one such system on Catalina Island in California that is giving us unusual corrosion problems. The high pressure fittings -800 psi - on the system are all 316 SS. On most of them we are seeing severe reddish corrosion or oxide at the connections. On other SS mechanical parts near the fittings we see white powder buildup which could be salt. The fittings appear secure with no visible leaking. The city of Avalon on Catalina Island has two water systems, one fresh potable water and the other filtered sea water (for toilet flushing). The company that services our system reports that the sediment prefilter on the sea water feed to our system is always deep orange/red when changed indicating iron in the feed. It is possible that the sea water distribution system used GI pipes when is was put in many years ago. Could this be contributing to our corrosion? Also, we have been using Rectorseal No. 5 as thread sealant on the high pressure SS fittings and the thread joints seem to be the site of the worst corrosion. Does anyone know if the sealant could be a factor? Thanks for any advice.
- San Marcos, California, USA
May 4, 2012
Q. Do you know the chemical reaction taking place with sea water, SBS, sodium meta bisulfite to neutralize chlorine?
the type of chlorine can be hypochlorite or chlorine dioxide
OCl- ClO2
How do people in industry typically operate the dosing of the SBS?
employee - Atlanta, Georgia, USA
May 15, 2012
Q, A, or Comment on THIS thread -or- Start a NEW Thread