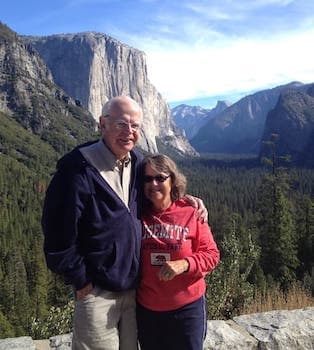
Curated with aloha by
Ted Mooney, P.E. RET
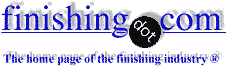
The authoritative public forum
for Metal Finishing 1989-2025
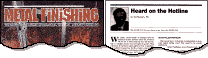
-----
D2 Tool Steel To Make A Sword Blade
Q. I WISH TO MAKE A SWORD BLADE FROM 'D2' TOOL STEEL AND OBTAIN A HIGH POLISHED FINISH. IS THIS POSSIBLE AND WHAT MIGHT BE THE CORROSION PROBLEMS. IF ANYONE CAN HELP I WOULD BE OBLIGED.
GEORGE KEITH- LONDON, U.K.
2001
A. I don't know what D2 is but I do know how to make a good conseling sword, but you would need a Dremel ⇦ this on eBay or Amazon [affil links] to cut the metal.
Lain G [last name deleted for privacy by Editor]- Springfield, Virginia, USA
2001
A. As you probably already know, the D2 tool steel is basically a high-carbon, high-chromium cold work tool steel. It is quite easy to make if you have casting facilities. Just add the appropriate amounts of carbon (1.4 to 1.6%), manganese (0.60%max), silicon (0.60%max), nickel (0.30% max), chromium (11 to 13%), moly (0.7 to 1.2%), and vanadium (1.1% max), and the rest is iron of course. If you want the procedure to do this (it's pretty simple so I'll assume you know how) just let me know and I'll figure out the exact order and temperature you need to use.
You're not going to want to normalize this tool steel, you're probably going to want a high toughness (it's a sword, right?) combined with high hardness (will keep a nice sharp edge and be easily polished) and ductility (for forming and if you hit something you don't want the sword to shatter). To get these properties maximized, you need to anneal the tool steel at close to 900 °C (sorry no Fahrenheit, I'm Canadian)! for six hours, slowly cool the steel to room temperature not more than 22 degrees per hour, austenitize at 1000 degrees for 45 minutes, air quench as uniformly as possible (this is important, do not lay the sword down to let it cool since the cooling will not be uniform, instead try suspend it in the air), temper immediately after tool has cooled to about 50 to 66 degrees (still Celsius), do the temper at 350 degrees for 2 hours. Now let the steel cool to room temperature over a day or so before you continue. The sword should already be as long and thick as it needs to be because we don't want to mess with our properties as much as possible from here on in. Slight rolling may be acceptable but I do not recommend it.
Now all you have to do is finish forming the steel but cut off any unnecessary portions first, and then make the edge. You should not have any problem at all attaining a sharp edge using this material, and it should hold for a long time under normal use (only k!ill soft-boned mammals, don't try to kill the rock-hard body builders--just joking, haha). Add your desired handle and voila, you've made yourself a nice sword out of D2 tool steel!
Shoot, sorry, I got all excited and forgot to mention the corrosion characteristics. The D2 tool steel as I described will have very high wear resistance due to the content of C, Cr and V. Also, the Cr forms an oxide layer which also offers good corrosion resistance. Be careful not to add too much C though (stay in the range) or else the ductility and toughness will decrease dramatically. Also, be careful with the Mn additions as more than 2% will embrittle the steel. Any more info needed...
Chris VrolykUniversity of Alberta - Edmonton, Alberta, Canada
2001
A. You can buy a bar of d2 a little bigger than the blade you are going to make anywhere, you don't have to formulate it from atomic particles as the professor suggests, besides if you had your own foundry you wouldn't be asking the question in the first place. It is imperative that you sculpt sand and finish this piece to the point where it is almost flawless, because, once it is hardened you will severely regret not heeding my warning. A small scratch left in the ricasso area will become a major problem to remove. Then send it in for hardening, there are tons of places that do it . They only need to know the type of metal you are sending and its intended use and you're done. There is the Canadian knifemakers guild and all the answers are there, good luck.
Darren Chard- Toronto
2002
A. Sir,
I do not believe that D2 or any other "tool Steel" is a suitable material for a long knife. Gerber uses 41C stainless for it's blades and although they really hold an edge, brittleness is a problem. If I wanted a "super sword blade" I would pick a tungsten steel alloy.
Norman B. Czerski49th STS - Eagle River, Alaska USA
2003
A. D2 will make an excellent blade. I would recommend that you do not try to make the blade by taking a bar and shaping it with grinders and such. This will not make the qualities for a great blade. Take a bar of D2 and heat it in a coal forge until it is a high yellow color. Beat the steel flat against an anvil. Using the appropriate tools (smithing tools) fold the steel along its length. Reheat to high yellow and flatten it again. This process will weld each layer back to itself and will capture carbon between its layers. To make a very nice blade this process has to be repeated many times. It is not uncommon for a blade to have as many as 250 layers (or more). Remember that each time you fold the steel the layers double. So the last fold jumps from 125 layers to 250 layers. When the folding is completed hone the shape of the blade trying to stay aligned with the folded grain you have created. This can be accomplished by paying close attention to the lines found lengthwise on the blade created by the lines of carbon. If done correctly the blade will be very flexible and will maintain an edge as sharp as a straight razor. If You choose to just shape the blade from a bar of D2 steel, Nitriding can provide a hardened shell (up to about 0.024" thick) and it will give good wear characteristics and corrosion resistance. If the blade is ornamental this will probably suffice. If you are a samurai in training use the folding method.
Grant McGuffey- Springfield, Tennessee
2003
2003
A. Step one: Obtain a copy of Wayne Goddard's "The Fifty Dollar Knife Shop ⇦[this on Amazon affil links] and read it carefully.
Step two: Practice making knives (not swords, knives) from simple steels like 1081 until you begin to get the hang of the process.
Step three: Work your way up to larger and larger blades of more and more exotic steels until you get to your "D2 Sword."
Rule #14 for Beginning Blacksmiths: "Don't try to make a sword for your first project."
Quote from Dr. Jim Hrisoulas, internationally renowned maker of custom knives and swords: "Every bladesmith should at one time in his life undertake the task of forging a sword. It can be a very enriching and humbling experience."
There are a few websites you can take advantage of as well - you can find them using any search engine. One is called "Sword Forum International." Another is "The Custom Knife Directory" or "CKD." I also recommend one called "Primal Fires."
Good luck!
Lee Cordochorea- Portland, Oregon, USA
Q. I'm trying to make a short sword (about a 22 in. blade) out of a piece of mild steel. (wish it was Damascus, but I don't care) I want a 9th century Viking broad sword . I got the sword drawn, but I want to know how to get the balance right on the blade. I would also like to know if the steel will be good enough (if it won't break or bend over semi heavy use)for a sword. Please help
MatthewI'm an amateur blade smith - S. Amherst, Ohio, United States
2004
Q. Hello,
I am looking into making swords. I have inquired makers in the local Ren-fairs and have looked up info online at other sites. I would like to ask any advice that can be given as to a good starting point as well as certain specifics with the temperature difference necessary for engraving a blade as well as a good temp for tempering the blade. I know that the temps differ greatly I am just on aware of how great. If any help can be placed it would be appreciated.
Thank you,
Ari Schlesinger- Denver , Colorado, USA
2004
Q. OK I'm here for my Husband he loves making swords when he's not working,now here is my Question can you use a truck Axle to make a good sword ? or is springs better ?
Angel lynn Holthobbyist - Bushnell, Florida , USA
2004
A. Hello, I can't believe my eyes reading this forum.
At first: D2 is very, very poor steel for sword making. It is very hard and wear resistant, but also very brittle. You should use some spring steel such as 5160 or 9260 (excellent choice), or some carbon steel - 1050 or 1060.
At second: you CAN'T forge weld D2 steel due to its high chromium content.
Marek HorakPike - Brno, Czech Republic
2004
Q. How many times can you fold the steel on a blade before it becomes unable to retain it's structure and becomes unstable? So basically how many folds will it take to make the sword break apart?
Joe M. - Las Vegas, Nevada, USA2005
2005
A. My company deals with manufactured knives and swords, however I have been a collector of cutlery for the past 30 years. I designed a short sword and selected A2 tool steel, which is very similar to D2. I then had the late Bob Engnath make the blade and have it professionally heat treated. I'm not a blade smith, but I have had a few of my designs made for me. There are quite a few Blade Smithies who use D2 tool steel for swords and knives. So it can be done. From what I have been told D2 is a difficult steel to work with, however if you are patient and don't give up, your end result should be a durable blade.
Phil Hartsfield is a master blade smith and designer. All of his swords and knives are made from A2 tool steel at a 60 Rockwell scale rating (RC), which is very hard, yet his swords and knives are some of the sharpest and most durable around.
Bob Engnath said "D2 steel offers an air hardening tool steel, with 12% chrome and excellent, if not superb, wear resistance. The resistance also holds true in both sawing and grinding, even while the steel is fully annealed. D2 steel is for the advanced craftsman."
Now regarding The ladies question about using axel steel for making blades. I'm sorry to say that I'm not sure, however spring steel which is used on cars and trucks, is made form 5160 spring steel and is an excellent choice for making swords with. The recommend RC rating
(Hardness) is around the mid 50's with the edge brought up to 60 RC rating. This will produce a flexible blade with a sharp edge.
I hope this will help you. If you can think it, you can do it. Don't give up.
Tim
- Warner Springs, California
Q. I really love swords and I've already made 2 of them.
I want to know how to make the blade sharp and strong.
- Sri Lanka
2006
A. Use O-1 steel. Easier to heat treat and normalize. Knife maker and machinist for 20 years.
James Alexander- Arlington, Texas
2006
2007
A. Firstly, a sword can be made from D2. Furthermore, katanas can be made from D2. I personally professionally made quite a few D2 katanas by hand. They were razor sharp, fullered, quite lively in the hand and not at all brittle. Quite a few were bought specifically for cutting practice.
D2 contains 12.5% chromium. Chromium (above a certain percentage) can make a steel brittle by enhancing grain boundaries, and this level of chromium might, in other steels, rule out use as a sword steel. However, D2 also contains vanadium and tungsten which act as grain refiners, and thus oppose the effect of the chromium. Additionally D2 contains molybdenum and some nickel which, with the tungsten, makes D2 very tough and very hard. The nearest equivalents for edge holding are the cobalt alloy stellite and the stainless steel 440V. The latter however is far too brittle for use as a sword steel.
D2 is not particularly brittle -- on the contrary it was designed for toughness. I failed to either bend or break any of mine with normal testing. Admittedly I didn't take a sledgehammer to any, or stick any in a vice with several feet of pipe over the end to give me additional leverage, but that to me does not represent normal use. I might however reconsider this if anyone ever finds themselves regularly using a katana to defend themselves against people wielding sledgehammers.
D2 is not a stainless steel -- it is rust resistant, but not stainless. It is in fact is a very tough steel -- even annealed - that has exceptionally good edge retention properties when tempered. OK, some folk have characterized it as "taking a lousy edge, and keeping it forever." All I can say is that the critics didn't know how to put a good edge on it. Put a bloody awful edge on it, and it will keep it forever. Put a razor edge on it and it will keep that forever.
I achieved razor sharp edges on all my swords -- and on D2 knives, and D2 naginata. What's more, they stayed sharp -- I put them through their faces with some moderately challenging targets, which they cut, one stroke, with no effect on the blade. Repeated testing also had no effect on the sharpness of the blade.
None of which is surprising, given that it is a workhorse steel for professional knife makers. In fact the remarks that it holds a lousy edge forever surprised me, since it is nothing like my experience of the steel. In fact D2 can hold the sort of edge that is already well under the skin before you know that you've cut yourself. A good D2 edge might cut you just by holding the sharpened blade. Furthermore, it is very difficult to blunt it, and you won't chip it.
The first thing therefore is learning how to put a good edge on steel.
Next, you cannot forgeweld D2, nor is there any need to. The whole purpose of folding the blades was to get a consistent carbon content -- otherwise there is no inherent advantage to folding it. Indeed, fold it too many times, and you'll find that the quality of the metal goes down. Forget the myth about "capturing carbon between the layers" -- whilst carbon can be picked up from the forge, carbon is also burnt out of the steel during forging and welding.
Since D2 already has a consistent carbon content -- the very effect that the smiths were trying to obtain - why on earth would you want to forgeweld it, even if that were technically possible? It is unlikely to give you any improvement on the original steel. OK, it might be great for advertising purposes but even if it were possible it would be unlikely to improve the blade to any discernable degree.
It is, however, not possible to fold and forgeweld D2. For the record, it is not advisable to weld D2 at all, unless you immediately anneal it, because it will run the risk of cracking.
You can however forge D2, and there are some perfectionist advantages to putting the curve in that way. Always make sure that it is fully annealed before going on to the next step.
It should also be pointed out that you can't get a hamon by differential tempering with D2. Firstly the metallurgy will tends to suppress the formation of a hamon. Secondly D2 is an air hardening steel, so you can't use the traditional clay method of differential tempering. You could probably edge temper it by running an oxyacetylene torch round the edge - this has been done with the related A2 - but the results are not always ideal.
Even so, there are swings and roundabouts where edge tempering is concerned -- an edge of Rc 62-63 is very brittle, even when the back is softer. It is likely to chip if it hits something hard, and a severe chip can spell the end of that sword. Once the sword has been ground down to the temper line - or if a chip goes to the temper line -- the sword is dead and you might as well throw it away.
How would a D2 blade compare to a traditionally made katana? Well, it depends on who was using it, and who made the traditional forged katana; cutting technique is important. In addition, bear in mind that there is a lot of hype about Japanese swords -- to hear some of it you'd think that they were the next best thing to lightsabres! Japanese swords won't cut through plate armour - in fact there are accounts of Japanese swords chipping on Mongol armour, which wasn't as robust as the high point of plate armour development.
There were some brilliant swords made in Japan. There were also swords that were right rubbish, even in the period of smith made swords - I've seen them. There are also some that are very pretty - however, the point of a sword is not how pretty it looks, but how well it cuts, how well it keeps its edge, and how difficult it is to damage or break.
>From testing, the D2 swords that I made would have easily taken someone's leg off with one cut, with no effect being seen on the edge. No doubt any other competent knife or sword maker could do as well. Furthermore, the edges won't chip under extreme use, and it would take some serious abuse to dent them.
On balance therefore, I doubt that my D2 swords were giving away much; in fact I suspect that past Japanese smiths would have leapt at the material. But then, as one smith who makes superb traditionally forged Japanese blades recently remarked to me, "In functional terms, Western blades have surpassed traditional nihonto for quite some time."
On thing when working on a D2 blade -- get the sword 99% complete whilst it is in the fully annealed state. That means getting it as sharp and as smooth as you can before tempering it, as well as drilling the hole for the mekugi. All that you should have left to do after tempering is a little bit of belt sanding, refining the blade with oil stones, and polishing.
If you don't do most of the work when it is annealed, you'll find out how tough a steel tempered D2 is. You won't try working on tempered D2 more than once.
It polishes well -- you can get it up to a mirror finish. However, I would advise against getting the thick end of 3 feet of razor sharp blade tangled up with 3000 rpm of buffing wheel unless you're either tired of your fingers (and possibly one of your legs) or you know exactly what you are doing.
BTW, when you've finished making, sharpening and polishing the blade, you're only just starting. You still have to mount it -- there's the tsuka and the saya to make. Good wrapping isn't that difficult once you've mastered it -- you can wrap a tsuka in an evening whilst watching the TV -- but you have to master it. Your woodwork better be good for making a saya and a tsuka as well.
Finally, for the person who was going to make a Viking sword from mild steel - forget it. Mild steel does not hold an edge. If I were you, I'd start off with making knives, and then get up to making swords.
Apart from D2 you could use AISI/American 1050 (a plain carbon steel), AISI/American 5160 (a low chromium alloy tool steel), 50CRV4 (a good spring steel with small amounts of chromium and vanadium), 1086 steel, L6 steel, and spring steels such as 5160. You can also make excellent katana by forgewelding steel cable then edge tempering it. I'm not sure about 01 - I've made plenty of knives with it, but I've not seen a sword made with it.
Alternatively you could go really overboard and either try using damasteel, or else make wootz steel. However, the last is seriously advanced.
As a general rule, stainless steels should be avoided for making swords. That said, some custom swordmakers have successfully used CPM420V stainless steel. It has good edge holding capabilities, and you can make a a very aggressive edge with it. Knifemakers consider that it out-cuts all other steels.
- London, UK
2007
To follow up on my previous post:
Folding steel does nothing more than to homogenize an impure product. It was at the time the best method to attain uniform carbon distribution in the metal. The old Japanese smiths would have loved to have had our steels as a starting point. They wouldn't have been the perfectionists that they were otherwise.
Complex folding patterns like Kobuse and San Mai are completely unnecessary for the stresses placed on the blade of a katana. The resonances set up in the blade on striking a hard object do not require the soft core support seen in Kobuse, or the support of a springy skin, as in San Mai. Not only was this construction unnecessary, it did little more than add another potential area for weld failure.
Failed welds can be found from Japanese blades of all periods. Then there is the presence of enlarged granular structures (nie). While some smiths and collectors enjoy the look of nie, its presence reveals a weakened, compromised blade. A very pretty blade, to be sure, but weakened and compromised nevertheless.
Assuming everything else is equal, the following are true;
A katana made from any modern plain carbon steel, from any country, will when properly tempered and with the right blade geometry equal a traditionally made katana for cutting power.
A katana made from plain carbon steels containing vanadium will, if properly tempered and shaped, out-cut a traditionally made katana.
A katana made from plain carbon steels with the addition of both vanadium and nickel will both out-cut and out-perform a traditionally made katana - even if made from unfolded steel.
There are, BTW, several bladesmiths who would put the performance of their blades up against any Japanese blade, old or new.
- London, UK
Q. What if I started off using a hardox 400 plate steel for a sword?
Barry Powersfabrication - Gorham, ME, USA
February 1, 2008
A. Some of you have the metallurgy knowledge, clearly. I must dispute some of what is advised. D-2 is not a great choice for a sword. It can be done, but it is far from ideal. I would refuse to be around anyone who is actively using the sword. D2 was designed as a wear resistance tool/die steel. Not as one for high impact (Charpy). When it breaks it is comparable to a small explosion of sharp shards of glass at high hardness (high hardness is partially what it was designed for). If a person were to reduce the RC hardness to compensate then edge retention would be sacrificed. The presence of a small amount of vanadium counters this somewhat. But it would be like putting a V8 engine in a Volkswagen. There is also the significant issue of using such an expensive steel just to try to temper it back to a hardness and use in an application for which it was not designed for. There are many other alloys better suited and less costly. The typical stain resistant knife steels are less than ideal for a sword. A differentially heat treated carbon steel blade would be an excellent choice. If you don't have the ability to differentially heat treat, then some of the afore mentioned steels, and others should do fine. 5160, 6150, L6, O1, should be up for the task of impact with proper temper. Trying to differentially temper D2 with a torch is a very poor idea. There is a great possibility of inducing uneven stresses that could actually weaken the blade. D2 is a sensitive air hardening steel. Or worst case scenario you could easily make the back harder with a torch by reaching critical temperature. If you lack the experience you may not even know what that means and therefore should avoid it. If you want a good skinning knife, or if you need to stamp out 1,000 parts use D2. For a sword, it is near the bottom of my list. It DOES NOT polish well. Though there are techniques to avoid pitting you will be disappointed at the finish if you are looking for a mirror-like finish. My best advice is to contact a competent sword smith or instructing knife maker. Making a sword worthy of display or hard use is near impossible for a novice maker. Learning by beginning with knives was excellent advice. Safety procedures are of utmost importance in all aspects. D2 is not a safe sword steel under heavy use. All just my opinion of course. As for one of the other questions - mild steel (usually 1018) is a good structural steel, not a blade steel. Just like you would not build a bridge with D2. I would like to sit back and observe someone try to hand make a titanium sword for a good laugh.....
Tim Crocker- San Bernardino, California, USA
October 23, 2008
A. To the lady whose husband likes making swords..a lot of gm springs are 5160..By cutting spring down the middle with a small cutoff wheel, two swords can be made.Some grinding will need to be done to eliminate center hole. in both pieces a half hole will be left after cutting.
Homemade forges can be made with a hair dryer
⇦ this on
eBay or
Amazon [affil links] as an air supplier..this can be used for heating metal to straighten out springs curve..If an anvil is available at this time a quasi edge can be formed with a hammer and heat which will save some grinding time later on...I have hammered out a Honda driveshaft to make a large bowie and it turned out to be an excellent knife with good edge holding..However, I would advise that it takes considerable work to hammer it flat..though well worth the effort. I would not however recommend driveshaft knife making with all the very suitable flat steels laying around junkyards....Hal
- Wellington, PEI, Canada
March 23, 2009
June 22, 2009
A. Hello, Everyone!
I'm a (very much so) amateur bladesmith and knife maker. My first real project was a dagger made from some leaf spring steel, most likely a 5160. I had intended to make a sword, but simply found that the pieces I had were not large enough for what I wanted.
For those of you who want to make a sword FIRST, I recommend this site: www.livesteelarmor.com/how/warsword.html
Another good resource is this site here: www.knife-making-supplies.net/
That's where I started. I've also made a few knives, mostly from reciprocating saw blades.
I'm really happy to see that most of the experienced smiths here are encouraging and friendly. I would like to echo their advice of trying out knives first. Even though I started with a sword, I've found knifework to be more fun and certainly easier.
Good luck,
James
- Campbell, California, USA
A. Great to see the interest in knife and sword making with D2. I started making knives and swords about 15 years ago using a variety of materials including O1 A2 D2 saw blade (of various types) and forge welding my own Damascus from many different materials over time. I have ended up specializing in chef knives and almost exclusively use D2. I find it a practical compromise between the full stainless steels and plain(ish) steels like O1. I find it very easy to get a consistent hardness by colour in a gas furnace. I have forged and heat treated in coal but it is very easy to get hot spots and ruin what you have started.
When I started using D2 I was only able to source 6mm bar and forged it by hand into knife blanks. After about 8 months of this my back slipped a disk and I spent 2 months in bed. A local blacksmith told me I was to old to start hand forging a steel so hard. However, 2 months in bed was time enough to figure a design for my first power hammer. This was a life saver and also meant I could make larger pieces of folded steel.
The one thing I learned along the way that I try to pass on to anyone who will listen, is to ignore the naysayers. There is almost always a way around whatever problem you have and there is always someone who did it with less equipment than you. Practice and be prepared to fail. Above all, make what you enjoy and enjoy what you make.
- Christchurch, New Zealand
July 16, 2009
April 15, 2011
regarding making a sword out of D-2 : I would NOT recommend it. D-2 is hard to forge, hard to grind, and quite temperamental in heat-treatment, especially in something as long as a sword. it is a very good, hard-wearing die steel, but there is simply no percentage in investing so much effort in making a long blade out of it as it will not be more durable than say, 9260 spring steel. there is a tendency among many knifemakers to use steels designed for industrial purposes (die steels, high-speed steels, etc) for knives, as they feel that these steels, meant for severe uses, will make superior knives. this is often a mistake. knives require things like a keen edge, some flexibility, and ease of sharpening, and in the case of a sword ability to withstand shocks WHILE keeping a cutting edge. many tool steels, while excellent in industrial use, are quite unsuitable for knives, and in my opinion D-2 is one of those.
As to the posted posted recommendation to cast the sword... sorry, apart from the tremendous difficulty in casting a specific tool grade at home, that sword will have the life expectancy of a glass hammer. Steel swords are either ground or forged, never cast, as cast steel of such shape will simply lack any kind of structural strength. Any highly stressed steel part in a given piece of machinery is almost always forged, precisely for this reason.
good luck!
bridgetown forge -portland, oregon, usa
----
Ed. note: Readers may also be interested in
Letter 22763, "The ultimate perfect Katana".
A. Like someone said making a swords out of D2, its almost impossible for someone thats uses D2 for knives and small stuff, just too damn hard material to work with.
5160 and 9260 are great steels for swords because of silicone in the steel for flexibility.
Though the best steel for Noobs to attempt his first sword I would recommend AISI 1060, makes decent sword and is one of the easiest to work with. If you want something better check 1086 steel, more carbon better edge retention, a just little bit harder to work with.
Diogo Antunes, Portugal - Coimbra, Portugal
February 6, 2016
Q, A, or Comment on THIS thread -or- Start a NEW Thread