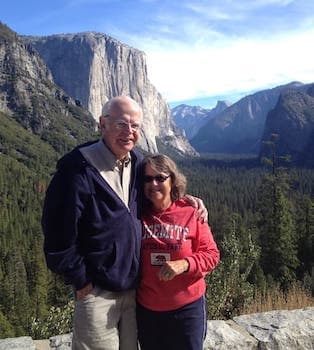
Curated with aloha by
Ted Mooney, P.E. RET
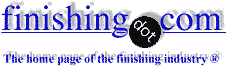
The authoritative public forum
for Metal Finishing 1989-2025
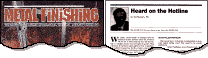
-----
Hard Chrome Plating of Piston Crowns
Q. Our company is about to start a Hard Chrome Plating (HCP) project, which needs to design & construct (or purchase) a "Rotating" HCP machine. The product part is a Piston Crown, whose shape is cylindrical, has a diameter up to 1 meter and weigh up to 1500 kg. Such piston crown has 4 Ring Grooves, whose width is in the range of 8 mm ~ 28 mm, and 0.4 mm thickness of chromium is expected to be deposited only onto the surface of the Ring Grooves, not the whole piston crown.
Our company is currently using the traditionally dipping method, but the quality cannot be easily controlled. We have heard that a "Rotating" chrome plating approach (i.e. holding the piston crown in a bath and allow it to spin) is a good way to obtain a more even chromium distribution. We would like to have your opinion on whether such "Rotating" approach is popular one, and any information that could help us to explain our objective needs would be deeply appreciated. Thank you.
Andrew Ning- Hong Kong
2001
A. Have you ever tried to use auxiliary anodes so as to have a better metal distribution over the LCD region? Also, Sergent bath is not as good as the catalytic type in metal evenness.
Jason Wu- Hong Kong SAR
2001
A. It's an excellent process but the plant will cost you !
Be sure to use mesh titanium anodes which are curved to the cylindrical shape of your roller, below the roller and, if possible, on the sides -- covering at least 50 % of the area.
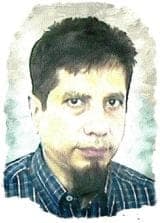
Khozem Vahaanwala
Saify Ind

Bengaluru, Karnataka, India
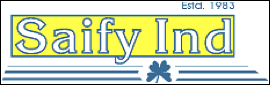
2001
A. I do not know if it is a popular one, but sure it works, and you do not need titanium anodes, just use lead.
You will have to make a lot of different anodes for all possible diameters and types of piston crowns (usually from 350 to 900 - Mitsubishi, Pielstick, Sulzer etc.) and adjust them precisely every time.
Keep in mind that it is difficult (or shall I say impossible?) to get a uniform coating, especially for such a thickness as 0.4 mm, and the coating would be thicker from the bottom of the groove to the edge. Also, it takes a great deal of time in the bath and of course the grooves require subsequent grinding.
Hope you make it and get the best out of it.
Christos Sigalas- Athens, Greece
2001
2001
Thanks to Jason, Khozem and Christos for your help.
Jason & Khozem, we are already using ëhalf-circleí shape anode. Also, we are currently investigating the possibility of using a plating additive. Any suggestion?
Christos, we do have to keep stock of different size of anodes for all possible diameters and types of piston crowns. That is still fine since we do have space available to store them. The main problem for us is the long plating time, which can be more than 60 hrs.
Thanks again for your help.
Andrew Ning [returning]- Hong Kong
A. I worked for a U.K.company which plated ships pistons for Sultzer and Doxford. We partially submerged the pistons and fitted auxilary anodes. The piston was rotated whilst plating. There is obviously a lot more to the plating of pistons which cannot be easily written down.
Norman Evans- U.S.A.
2001
2001
Thanks for your response, Norman.
I agree that there are many parameters that can affect the plating outcome. In order to find out the range of operating conditions, did you use a small scale experimental setup or through trial-and-error method? (For example, what is your opinion on the rotary plating speed for a Sulzer RND90M piston?)
In terms of plating time & evenness of chromium distribution, what is the difference between rotary & non-rotary process? And apart from the piston rotary action, any extra agitation is needed?
Your experience would be deeply appreciated & valued.
Andrew Ning [returning]- Hong Kong
A. Dear Andrew,
It's been a long time but if you read this it would be interesting to exchange opinions. I want to ask you what you have done until now and if it worked.
Since in the company I work we face the same problems (very long deposition time, uneven distribution of the chrome layer etc.), I am curious to know if you have found a proper solution for solving these.
Thank you
Christos Sigalas- Athens, Greece
2002
Q. Dear Christos Sigalas,
Our company only started the rotary plating investigation in January 2001. A rotary machine has been constructed. Numerous trials have been performed and the results showed that chromium has been deposited in a more even manner. However, the hardness of the such deposited chromium only is between 700HV ~ 800HV Vickers, where our requirement is between 760HV ~ 960HV. It may be down to the error of the measuring equipment, but we don't know. Any suggestion to increase the hardness?
Andrew Ning [returning]- Hong Kong
2002
by Robert K. Guffie
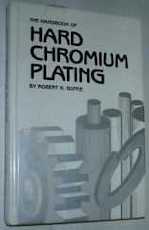
on AbeBooks
(rarely)
or eBay
(rarely)
or Amazon
(affil links)
Q. We are doing marine diesel piston repair and we do the grooves by welding. My question is whether piston groove plating technology and equipment are available.
Ismail Ozalp- Istanbul, Turkey
2003
! To all interested,
We are currently developing a unit that will chrome plate piston grooves rotating. The idea is to make the unit plug and play, as things are looking now we will be building a prototype later this year.
Main issues are, surface of groove covered by anode, keeping the plating solution "clean", type of hard chrome process (no Fluorides!), maximum current density, plating time < 20 hours. Material of anodes to be used is a big issue!
In the Netherlands rotating piston groove plating has been done for many years and with great success.
- Emmen, Netherlands
June 29, 2010
Q. We have hard chrome plating,
For past few days, am undergoing problem while hard chrome plating on piston crown ring groove area; I am facing problems like:
a. Chrome bonding is proper , but inside the ring groove area in some places chrome is not plating properly.
For e.g., If am measuring thickness of the chrome; outside the ring grooves it's showing .6, but if I am measuring inside or near to recess groove it shows .4 , so I came to know that chrome are not equally bonding, but I can't solve or I can't find the real problem. For this can you offer feedback?
Regards
chrome plating (industrialist) - Singapore
April 18, 2011
Q. Dear sir,
Good day, we are doing hard chrome plating since 2007, our chrome plating type is not a rotary type, so I have to modify our current structure into rotary type, can you please give me any idea or suggestion, how to make rotating type hard chrome plating.
Regards
hard chrome plating - Singapore
April 29, 2011
April 29, 2011
A. Hello,
Look at a normal plating barrel and try to imagine your component as the barrel. You will need an identical drive mechanism that conducts the current as well as rotates the part.
A conforming platinized titanium mesh at the bottom of the tank will be better than just at the sides.
Plan for a cover for the tank that totally encloses the top of the tank during plating whilst having a good exhaust system vacate the fumes from the inside.
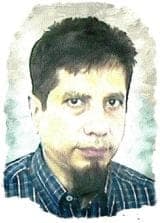
Khozem Vahaanwala
Saify Ind

Bengaluru, Karnataka, India
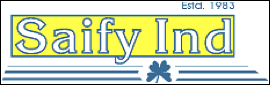
Q. Before anything else, my many many thanks and my salute to all the EXPERTS in this very supportive metal finishing community. THANK YOU SO VERY MUCH!!!
Here I am again with my query regarding HARD CHROMING. Is it possible to use perforated ORDINARY FLAT SHEET as "auxiliary anode material" for hard chroming of aviation piston rods? Also, are there manufacturers of this NO-MASK anodes which we can import? We welcome recommendations for this matter.
Kind regards to you all.
- Jeddah, Kingdom of Saudi Arabia
December 18, 2012
A. Hi,
First I will say you can't use titanium anodes, because they will be anodized and no current will go out from them. Different chrome layers are coming from the part not being heated to the solution temperature. A perforated anode of lead/antimony is great to have a bigger anode area than the part. In USA is a company with the name Hard chrome technique can help you with the anode construction.
It's no problem to get a hard chrome deposit with a uniform thickness. It's only to have the right length of the anode.
Regards
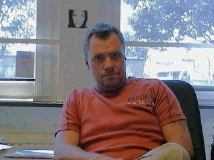
Anders Sundman
4th Generation Surface Engineering
Consultant - Arvika,
Sweden
Thanks a lot for the response. If my company here will agree with me, we would like to ask for an electroplating training for aviation technicians. Please recommend us to a certified training institution. Again, to all the experts here, SALUTE!
aviation - Jeddah KOSA
December 28, 2012
A. Hi Sam. In the USA, the National Association for Surface Finishing (www.nasf.org) conducts on-site and web based training; Anders mentioned Hard Chrome Plating Consultants in Cleveland, Ohio (www.hard-chromesystems.com); and you might contact Kushner Electroplating School.
In the U.K. there is the Institute of Metal Finishing (www.uk-finishing.org.uk), and in India there is the Metal Finishers' Association of India (www.mfai.org). Other readers may have additional suggestions. Good luck.
Regards,
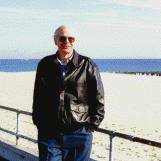
Ted Mooney, P.E.
Striving to live Aloha
finishing.com - Pine Beach, New Jersey
December 28, 2012
A. A while back I went looking for Hard Chrome Plating and could find nothing current. Junior ran it for a while after Clarence died, as a supply house, but I think that is even gone.
I would love to be corrected.
Jim
- Navarre, Florida
December 31, 2012
December 31, 2012
Hi James. Their website is still "live", but I guess a phone call or e-mail would be required to determine how viable they actually are.
Regards,
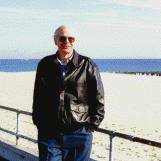
Ted Mooney, P.E.
Striving to live Aloha
finishing.com - Pine Beach, New Jersey
A. 1. HARD CHROME PLATING WILL NOT STICK TO OIL SURFACE'S LIKE PISTON GROOVES.
WHAT YOU NEED TO DO IS LIQUID HONE (GLASS BEAD BLAST WITH WATER) THEN CHROME WILL BOND TO METAL.
THE SAME GOES WHEN REPLATING LIQUID HONE BEFORE.
2. CHROME IS BLIND. YOU NEED ANODES TO DIRECT CHROME IN GROOVES.
IF YOU PUT FIVE PISTON'S IN YOUR TANK AND ONE RECTIFIER CHROME WILL GO WACKY UNEVEN CHROME BUILDUP
CONNECT ONE PISTON TO ONE RECTIFIER YOU WILL GET 0.001 PLATING ON THE NOSE IT'S CALLED BLUE PRINT CHROME PLATING
HARD CHROME PLATING - S. PLAINFIELD, New Jersey USA
July 17, 2015
Q. Hi dear,
I work in the hard chrome plating for piston crown. past ten years. I saw the pits and peel off on ring groove face. I tried my best, but I can't solve this until now. So I need a solution for this.
Thank you
production engineer - SINGAPORE
October 28, 2017
November 11, 2017
A. Hi,
Use high temperature degreasing as a first step after cleaning from old chrome. Grind if necessary, and shotpeening after that.
Regards
Anders Sundman
4th Generation Surface Engineering
Consultant - Arvika,
Sweden
Q, A, or Comment on THIS thread -or- Start a NEW Thread