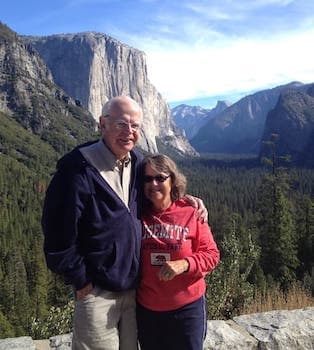
Curated with aloha by
Ted Mooney, P.E. RET
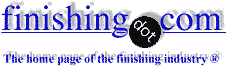
The authoritative public forum
for Metal Finishing 1989-2025
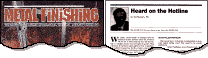
-----
Bright Zinc Finish Specifications
I am an Engineer with AMF Bowling. We produce a lane conditioning machine that has a large bent tubing handle (made from 1" thin wall steel tubing) that has always specified a "bright zinc, commercial quality finish". The handle used to have a really bright finish, but after switching vendors (the old vendor is no longer available), we began to get a really dull gray finish. The new vendor says that the finish on a sample I sent him of the originally finished handle had a "Nickel Chrome Plated" finish, not a "bright zinc" at all. I am not real comfortable with specifying finishes. I'm looking for some help in specifying a finish for this handle that will: 1)have a bright, mirror-like finish, and 2) provide enough corrosion resistance to last the life of the machine.
Adam B [surname deleted for privacy by Editor]AMF Bowling Products, Inc. - Mechanicsville, Virginia
2001
Your new vendor may be correct. Nickel chrome has a much nicer appearance than a bright zinc finish. You may have been getting that type of plating even though you were supposed to be getting bright zinc. Not everyone who buys plating is knowledgeable about it, and might not care about spec details if what they are getting works.
Zinc deposits can be bright and very nice-looking, but I don't think you will get "mirror-like". It is sometimes hard to control the brightness of a zinc plating. A plater needs to add brightener additives to the plating bath to improve the plating appearance. A big problem is that one can not easily measure, and therefore control, the amount of brightener in a tank. Too much brightener can cause the plating to lose adhesion and peel off. Nickel chrome may be better if the main concern is appearance. However, in general, zinc will be cheaper than nickel chrome.
Nickel chrome is available in multi-layer systems (dual, tri, quad, etc). More layers equal better corrosion resistance. You need to establish guidelines as to how protective the finish needs to be. You should specify a number of hours in salt spray ( ASTM B117 ) for zinc platings. You could also use salt spray hours for nickel chrome, but CASS (ASTM B368 ) is a more appropriate test for nickel chrome chemistry.
You should get samples of both platings and compare cost, color, corrosion resistance, and appearance. Then you can make a decision.

Tim Neveau
Rochester Hills, Michigan
2001
Everything Tim said is correct as far as I know. The only footnote I would add is that it is possible that the original vendor was doing acid zinc plating, which is quite bright and "almost" looks like nickel-chrome as long as the two finishes aren't side by side, whereas the new vendor is doing alkaline zinc. Alkaline zinc is a superior finish in a number of ways but is far duller than bright acid zinc.
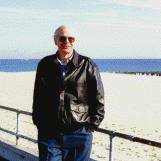
Ted Mooney, P.E.
Striving to live Aloha
finishing.com - Pine Beach, New Jersey
2001
Ted is correct, Alkaline zinc is much duller and most platers add the min. of brightener because of adhesion of plating, adhesion of paints to plating etc. Powder coatings have come a long way towards esthetics. Powders are now available in chrome like finishes. Thus, if you were to phosphatize and powder coat, you would maximize you quality finish in a cost effective manner.
Sincerely,
- Montreal, Canada
2001
Q, A, or Comment on THIS thread -or- Start a NEW Thread