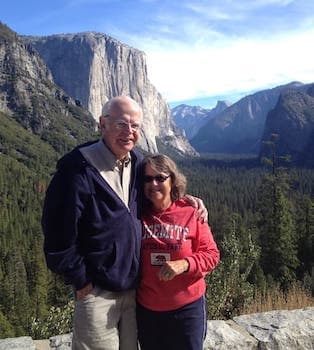
Curated with aloha by
Ted Mooney, P.E. RET
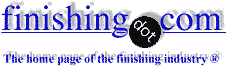
The authoritative public forum
for Metal Finishing 1989-2025
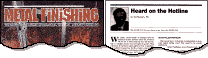
-----
Surface finish standards for aluminum anodizing Q&A, topography
Q. At present we are doing Anodizing through Sulfuric Acid Electrolyte on Aluminum Alloy parts. The roughness observed after Anodizing is RA 2. How can we reduce this to less than 0.5?
Harish- Punjab, India
August 5, 2024
Tip: This forum was designed to build camaraderie through sharing of tips, opinions, pics & personalities.
When people withhold their info, readers may be less likely to believe that they will share in turn.
for Shops, Specifiers & Engineers
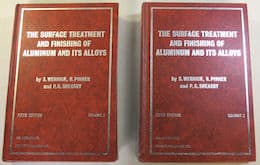
avail from eBay, AbeBooks, or Amazon
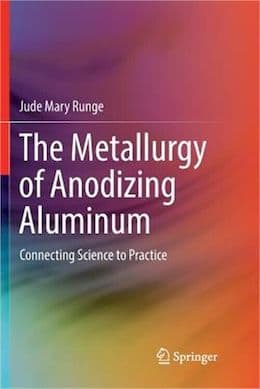
avail from eBay, AbeBooks, or Amazon
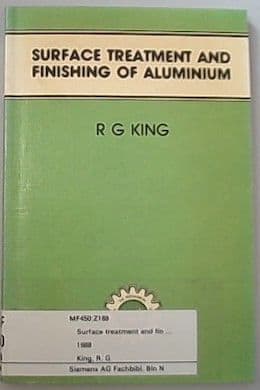
avail from eBay, AbeBooks, or Amazon
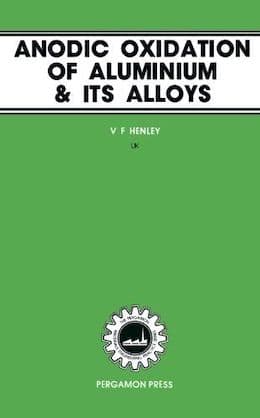
avail from eBay, AbeBooks, or Amazon
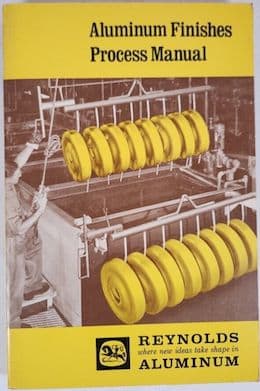
avail from eBay, AbeBooks or Amazon
(as an Amazon Associate & eBay Partner, we earn from qualifying purchases)
A. Hi Harish,
Presumably you are speaking in metric units, such that the observed roughness is 80 Ra in English units and you are aiming for 20 Ra; this should not be a great challenge if you can start at about 10 Ra English, 0.25 metric.
Thread 51222, "Maintaining a Smooth Surface Finish after Anodizing", and thread 17401, "Polish Hard Anodized Surfaces" may be helpful.
Thinner anodizing, more polishing before anodizing, and/or polishing after anodizing will help.
Can you tell us about the parts: material (castings, extrusions, machined surfaces), alloy type, surface finish before anodizing, shape of parts and how it relates to polishability, and target anodizing thickness?
Luck & Regards,
Ted Mooney, P.E. RET
Striving to live Aloha
finishing.com - Pine Beach, New Jersey
⇩ Related postings, oldest first ⇩
Q. We are finding it difficult to get "straight" answers from manufacturers, so hopefully you can help. We have a part that starts out as a solid piece of 6061-T6 aluminum which is milled out on a CNC machine, gets "finished", then black anodized. The final product needs to be free of any machining marks, and have a durable surface that will not show fingerprints, etc. when handled (i.e., must appear
"cosmetically pleasing").
The problem we are experiencing lies in the interpretation of our intent when we state the "surface must be free from machining marks and smooth prior to anodizing". One source is saying this must be done using a glass bead blast to achieve the desired result, while another says NO to bead blasting; it creates a surface that is like a fine grit sandpaper - shows a white residue when a finger is run across the surface.
Is there a metal finishing standard we could call out on the print to specify what "smooth" is? Thanks for your help.
- Puyallup, Washington, USA
2000
A. You have a couple of options, depending on the tolerances of your parts. "Machine" marks, to me..mean mill marks, etc..these can be either sanded, or tumbled out. Most anodizers etch their parts prior to coating, and any tumbling/sanding marks will be removed during the etch process (you can specify to your coater to etch these long enough to achieve the desired look, though, this may require a couple of sample parts, to make sure your tolerances aren't affected. Bead Blasting is pretty labor intensive, and if not done right, can leave a splotchy looking coating if the blast is uneven. Typically a finish of 32-64 Ra would leave "cosmetically pleasing" finish, if anodized properly.
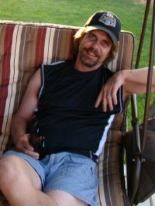
Marc Green
anodizer - Boise, Idaho
A. I agree with Marc that you have a couple of options, but the most common one prior to plating is mass finishing. The normal interpretation of a good surface finish prior to anodizing is a 16 RMS. This is accomplished using at least a medium grade plastic media. If your parts are very rough, exceed 35RMS, you may have to perform a 2 step operation of a coarse media first. The smoother the finish, the finer the appearance, but 12 to 18 RMS is common to anodize.
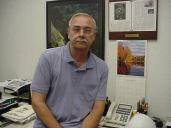
AF Kenton
retired business owner - Hatboro, Pennsylvania
Q. I would appreciate any information regarding how the anodizing process influences the surface topography of an aluminum alloy. After studying samples using a SEM I am interested in reducing the surface roughness by changing the actual anodizing process. Can anyone help or point me in the right direction? Thank you in advance.
William WoolnoughUniversity - Exeter, Devon, UK
2005
A. The aluminum on the surface is converted to aluminum hydroxides and other products, which occupy more volume than the original aluminum, so the topography is certainly affected. There are a number of different kinds of anodizing, including phosphoric acid anodizing, chromic acid anodizing, boric acid anodizing, and oxalic acid anodizing in addition to sulfuric acid anodizing. We know what you don't want to do (increase surface roughness more than necessary), but what do you want to do? In other words, why are you anodizing, and what properties are you seeking from the finish?
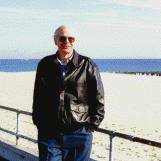
Ted Mooney, P.E.
Striving to live Aloha
finishing.com - Pine Beach, New Jersey
Q. We anodise primarily for decorative reasons combined with the enhanced protective properties it gives to the surface. At present this is done to BS AA15.
William Woolnough [returning]- Exeter, Devon, UK
2005
Aluminum surface finish
Q. Hi,
We have a machine shop for job work. We machine aluminum blocks for various valves on milling machine using a 45 degree shoulder mill cutter.
The finishing is some times not very good which results in poor quality black anodizing leaving white marks where the machining is a little rough.
How do I measure the machining surface finish , so that we may maintain a consistent finish without any anodizing problems.
MACHINING - VADODARA, GUJARAT, INDIA
February 18, 2009
A. I am not sure that I will go along with a rough surface being the ONLY cause of the anodize problem. I think that it could be the cutting fluid being retained in the groves and not properly rinsed off. A remote possibility is some of the prep step chemicals are being retained in the groves.
The answer to your question is to buy a moderate priced profilometer and then establish a go-no go roughness from practical experience.
- Navarre, Florida
A. It does sound like a corrosion or residue issue rather than surface roughness. Raw bare aluminum must not remain dirty or moist before finishing.
Leo Herringon- Grand Rapids, Michigan
A. Lokesh
If your cutter isn't sharp, the feed and speed not dialed in, and an adequate flow of quality coolant provided, you easily could be smearing the aluminum. The smearing will re-deposit pieces of aluminum back onto the surface that may or may not anodize properly. It also can entrap coolant in cavities caused by the smearing, that can effect the quality of the coating.
- Colorado Springs, Colorado
March 5, 2009
Q, A, or Comment on THIS thread -or- Start a NEW Thread