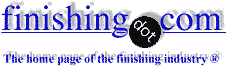
-----
Gold (Au) plating peels off of nickel plating
Q. I have faced Au peeling problem. The defect percentage is about 1 out of 25.
The base substrate is Cu and then Ni and finally Au. The Ni layer is very thin, just as a barrier for Cu diffusion.
Since we have not done the Au plating immediately after Ni plating, we have tried to use sulfuric acid (10% for 10 second) to clean the Ni surface before Au plating.
What is the cause for this Au peel off? For the same process flow, I have not found this problem before.
Please advise me if anyone knows the answer. Thanks.
- Hong Kong
2000
A. Is it just the Gold that is peeling off? Are you using a Strike between the Gold and Nickel layers? Are you trying out something new or was it an established process and suddenly you are encountering problems?
Mark Camilleri- Malta
2000
A. Kelvin. Au can peel off if you use too much brightener in nickel solution. Regards,
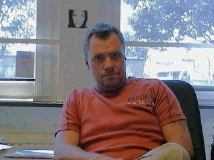
Anders Sundman
4th Generation Surface Engineering
Consultant - Arvika,
Sweden
2000
A. 10 seconds seems like a very short time in your acid dip to reactivate the nickel plate which you have allowed to go passive. Try at least a minute and use 10 to 20% HCl instead.
Neil BellAlbuquerque, New Mexico
2000
A. As mentioned before, you are having an activation problem on the nickel. This should be quite easy to solve.
Try electrolytic activation with the work cathodic for 60 seconds at 3 or 4 volts. If the acid etches the part too much lower the voltage or shorten the time.
If this does not solve the problem completely then I would electroclean the parts is an alkaline electrocleaning solution for 2 minutes with the work cathodic, rinse, rinse then electrolytic activation for 60 seconds.
Another solution would be to gold plate immediately after nickel plating.
Gold Touch Inc.

Cleveland, Ohio
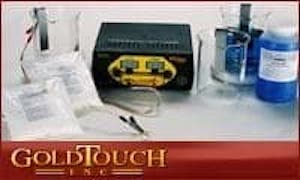
2000
![]() |
Q. We have a similar problem with a few exceptions: Defect rate 1 out of 250, Plate Gold immediately after Electrolytic copper build with NO nickel build. I was given a possible solution that I have not been able to test yet but it's along the lines of what Anders is talking about: Add Activation step to remove any brightener film that may be present. Use a 2% Sulfuric Acid, 0.25% Peroxide (33% grade) at room temp for 60-90 seconds. This will darken part but thats okay. Like I said, I haven't tried this yet so I'm kind of hoping someone will respond to this possible solution. Thank you. Tom Greifenkamp- Cincinnati, Ohio USA 2000 |
Multiple threads merged: please forgive chronology errors and repetition 🙂
2003
Q. Hi! can someone help, we are doing flexible PCB with the Nickel/Gold finishing,we facing the gold peeling from gold to nickel peeling problem recently on certain plating panels. Normally, we use plating rack for gold plating, every loading is 4 panels. The gold peeling pattern is total 4 panels per same loading will have gold peeling,some loading don't found any gold peeling. Is this mean the plating rack have problem?
1] In term of chemistry, what kind of situation the specific chemical can cause this problem?
2] In term of nickel passivation; what should be the possible cause? How to identify the root cause of nickel passivation? Is it only happen on certain period during different panel loading?
3] Why only certain loading have the gold peeling problem & others do not?
4] If water rinse is the main cause of nickel passivation? What is the deionize water quality requirement? How far is the flow rate affected the nickel passivation?
5] Whether the plating current cause the gold peeling from nickel? How this happen?
6] May this cause by the gold plating bath chemistry? If the chemical parameter within spec.; what else can cause the problem? Please help on this.
Thank you.
Regards,
- Thailand
A. GOLD PEELING IS BECAUSE OF INACTIVE SURFACE OF NICKEL , SURFACE TO BE ACTIVATED IN 1%HYDROCHLORIC ACID OR 5%sulfurIC ACID THEN IT HAS TO BE PLATED. PLATE AT LOW CURRENT DENSITY AS HIGH WITH HIGH CURRENT DENSITY LEADS TO GRAINY DEPOSIT WHICH IS SUSCEPTIBLE TO PEEL, SO PLATE AT LOW CURRENT DENSITY TO HAVE A LAMINAR DEPOSIT.
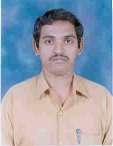
Panjala Mukesh
fashion jewelry mfgr.
Hyderabad, India
2003
Q. Is there any chances of facing upper plating layer peeloff (gold plating) if higher amount of brighteners used in nickel ( Under coating )?
Naveen kumar- Bangalore, Karnataka , India
November 5, 2014
A. Hi Naveen. We appended your inquiry to a thread where Anders has answered it directly. Of course, this is not the only possible reason for poor adhesion. Passive nickel is another common cause, and anything is possible. Please describe your own situation. Thanks.
Regards,
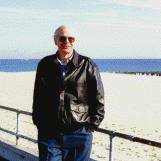
Ted Mooney, P.E.
Striving to live Aloha
finishing.com - Pine Beach, New Jersey
December 2014
Gold Plating Peel off from Nickel Surface
Q. Hi Guys, we are doing soft gold for substrate application and are facing gold peel off. We are doing soft gold plating on nickel surface. The Gold Plating peels off randomly from the Nickel Surface, almost all peel off areas are circular, the peel off is detectible after few days of plating. Nickel surface in peeled areas shows Fluoride in SEM/EDX. Nickel bath shows high C content >3000 ppm, with AAS
⇦ on
eBay
or
Amazon [affil links] analysis along with 3 ppm of Fluoride. So far we have not been able to find the source for the contamination in Nickel bath (Fluoride, C).
Is the peel off related to impurities in Nickel bath, if yes what could be the source of contamination? can it be city water supply?
shop employee - BKP, Malaysia
October 26, 2018
A. Hi Iqbal. Nickel plating baths usually operate at 140 °F (60 °C) so, over time, they accumulate and concentrate the impurities in city water. DI water is a safer bet.
But regardless of AAS or SEM/EDX findings, the first step is to observe whether the process is being run properly. As you can see from this thread, passivation of the nickel from too long a delay before gold plating, or excessive brighteners in the nickel bath are common causes of the gold peeling from the nickel.
Is this rack, barrel, or strip plating? I was once involved with a problem of gold plating peeling which was caused by excessive barrel rotation speed -- the parts were spending too much time fluttering down from the top of the barrel while the nickel was busy passivating itself.
Regards,
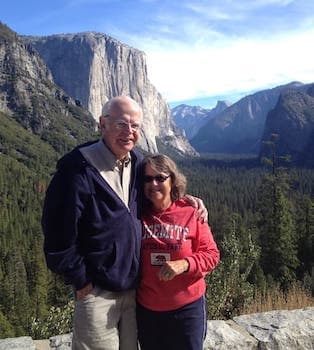
Ted Mooney, P.E. RET
Striving to live Aloha
finishing.com - Pine Beach, New Jersey
October 2018
Q. Dear Ted,
Thanks for your reply, based on your reply I understand that Fluoride & Inorganic contamination are not the root cause for the gold peel issue.
To reply to your other points this is a new "Rack" plating line and no brightener is being used in Nickel bath. All other parameters (concentration, temperature, dwell times) are within specs. The peel off is detected by tape test as per IPC Test Methods.
Is there any test method to check Nickel passivation.
Regards,
- BKP, Malaysia
October 27, 2018
A. Hi Iqbal. I did not mean to imply that fluoride or inorganic contamination cannot possibly have anything to do with the problem, but my experience is that, if brighteners are not used, the problem is usually passivation of the nickel.
Sorry, I don't know any good methods to measure such passivation, especially because it is directly proportional to the time since nickel plating.
How many rinses between nickel and gold plating? How much drip time in the air and how much rinse time from leaving the nickel tank to entering the gold tank. Have you actually watched this rack line in operation and verified that there is no situation where those times get extended? Good luck.
One more thought is that nickel can go passive even in one second if it becomes anodic due to stray currents, bipolar effects, etc. Do you ever remove a rack from the plating tank while others remain behind, or add a rack to the gold tank with other racks already present? You might try attaching a lead to the load during its exit from the nickel plating tank to check if that solves a stray/bipolar current problem.
Regards,
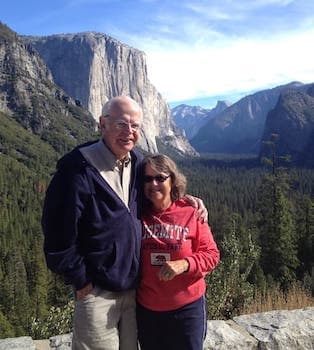
Ted Mooney, P.E. RET
Striving to live Aloha
finishing.com - Pine Beach, New Jersey
October 2018
November 1, 2018
Q. Dear Ted,
Thanks again for your valuable comments, to answer your questions on drip time between Nickel & Gold Plating, the flow is like below
After nickel plating, 25 sec drip time
water rinse cell 1, 15 sec drip time
water rinse cell 2, 30 sec drip time
nickel activator tank, 25 sec drip time
water rinse cell 1, 15 sec drip time
water rinse cell 2, 28 sec drip time
gold strike tank.
Please review & advise if above looks okay.
The drip time includes move up/down & transfer to next tank.
Regarding bipolar effect, stray currents allow me some more to check with my team.
Regards,
- BKP, Malaysia
A. Hi again Iqbal. Those rinse and drip times seem a bit long but not extraordinary. The 'nickel activator' is a non-electrolytic process, I assume, rather than being Wood's Nickel? I am a generalist rather than a specialist with a lot of experience with gold peeling off nickel -- perhaps another reader can chime in.
But maybe you were on the right track being concerned about fluoride. And since you note that the peeled areas are circular, I wonder if there is any possibility that your maintenance department is using a teflon lubricant, a tiny mist droplet of which might fall into one of those tanks, disperse into a circle and float on the surface? When something has a particular shape rather than random shapes, there may be a physical principle driving that shape. Sorry I can't help further.
Regards,
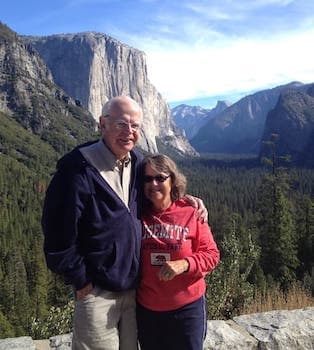
Ted Mooney, P.E. RET
Striving to live Aloha
finishing.com - Pine Beach, New Jersey
November 2018
A. Hello Ibqal, I have had quite a bit of experience with gold plated peel from Nickel. As Ted mentioned, a lubricant can be your problem, if one is used on contacts or anywhere above or around the tank. I have also seen undissolved salts cause peeling. You want to make sure the Ni activator salts are totally mixed before plating. When we used to make up a new activator solution those salts would take forever to dissolve. Make sure your rinse tanks are clean. Manual agitation from side to side also helps in rinses for rack plating. You employ a Au strike, which is good. Another note is to check for adequate filtration in all tanks that have filter systems. Changing filter tubes on a regular basis is important. The best way to look at a process is: it worked fine for us at one time, what has changed? With problems like these, we would put the process under Engineering Control to rule out operator error and be able to watch things more closely without the pressure an operator may feel getting the work out on time.
Mark BakerElectronics plating - Phoenix Arizona USA
November 4, 2018
November 7, 2018
Q. Dear Ted,
Thanks for your comments, our Nickel Activator is non-electrolytic. Shall check on the lubricant angle.
The Nickel & Rinse baths have air agitation for the liquid, and Rack has mechanical agitation. Regarding the circular shape my hypothesis is that the air bubbles cause the circular shape.
Dear Mark,
Thanks for chipping in,
The filters have been checked and are working fine, agitation system is also okay.
Shall follow your advise on lubricant & Activator salt dissolution in the bath.
- BKP, Malaysia
A. Hi Iqbal. Sorry, but when you said the plating was peeling off in circular shape I did not envision anything anywhere near as small as a gas pit. If photos are available they would probably help.
But if the peel-off is gas pit size, I think you should try to pull a part off the rack after nickel plating but before gold plating and see if in fact there are any gas pits present. Good luck.
Regards,
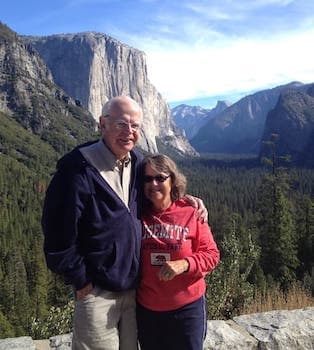
Ted Mooney, P.E. RET
Striving to live Aloha
finishing.com - Pine Beach, New Jersey
November 2018
November 7, 2018
Dear Ted,
Please find below the picture of gold peel-off, the diameter of the circular shapes is up to 75 micrometers
Regarding your advice on checking the board surface, just before entering the gold tank. I will let you know as soon as I have some feedback from my production team.
Best Regards
Iqbal MS [returning]- BKP, Malaysia
A. Hi Iqbal. I can't claim experience in any similar problems, but the micrograph sure does look like a filled gas pit :-)
Gas pits in the nickel plating will be shiny hemispheres of somewhat varying sizes. They are not from an air agitation system but from generation of hydrogen at the plated surface. They are solved with wetting agents and better agitation (including air agitation). Good luck.
Regards,
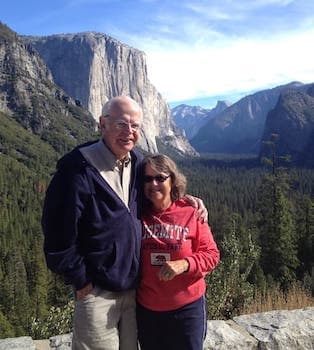
Ted Mooney, P.E. RET
Striving to live Aloha
finishing.com - Pine Beach, New Jersey
November 2018
November 27, 2018
Q. Hi all, FYI we are doing soft Au plating also on nickel surface. We are using nickel sulphamate bath without any wetting or brightener for matte plating. We do go through strike Au before Soft Au with the total thickness of 0.15-0.2 µm.
In our situation, gold peeling does not happen directly after gold plating even after baking test when doing tape test.
After gold plating we do pass through a few processes as below :
gold plating > stripping of dry film > lamination (to cover gold surface) > imaging > developing > window etching (FeCl3, alkaline etchant, etc.) > stripping
We found gold peeling issue happens right after window etching and the patterns were the same as Iqbal's shown above.
Is there any possibility of chemical attack during etching? If chemical attack, does it mean that lamination does not protect properly?
If due to bubble issue, is it need to present or found out peeling after peeling or baking? Does high boric acid content also cause the high amount of H2 gas produced?
As the gold peeling can be seen even by the naked eye, does gas pitting cause such big of peel in circular area ?
Regards
CWT - Penang, Malaysia
? Hi Rick,
Do you mean good peeling happens right after window etching or stripping as gold surface should be covered by lamination right after window etching and remove during stripping per your describe?
Regards,
David
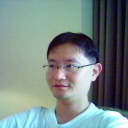
David Shiu
- Singapore
November 27, 2018
Q. Hi David ,
Yes, Gold peels off as a circular shape after undergoing window etching whereas this does not happen directly after gold plating.
After gold plating, there will be lamination process to protect the gold from window etching.
After window etching, we go for stripping to remove the dry film followed with tape test.
Gold peels off at this time.
CWT - Penang, Malaysia
November 28, 2018
? Hi Rick,
May I know window etching step is to remove copper or other metal? Is your substrate merely nickel with selective gold plating or copper with selective nickel & gold plating?
Regards,
David
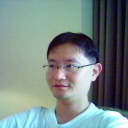
David Shiu
- Singapore
December 4, 2018
Q, A, or Comment on THIS thread -or- Start a NEW Thread