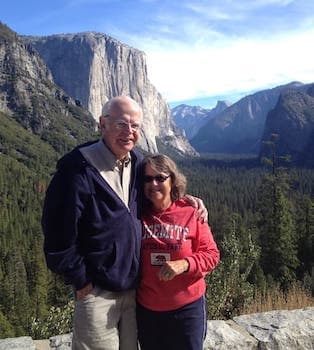
Curated with aloha by
Ted Mooney, P.E. RET
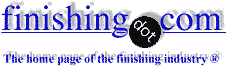
The authoritative public forum
for Metal Finishing 1989-2025
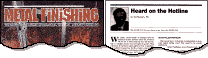
-----
Concentration of phos/nitric acid in bright dip for aluminum?
Q. I have a small aluminum furniture and design company in wichita with our own experimental anodize line. That is, we use this line mainly to experiment with different chemicals and processes in order to achieve new/unusual finishes on aluminum. I'm trying to find out a general concentration of nitric/phosphoric acids in a bright dip solution for type II aluminum anodizing. Also, I've been told that etched alloys tend to anodize better than highly polished alloys. If this is true, will there be any problems with dying high lustre parts?
Heath Beemanfurniture and design - Wichita, Kansas
2000
Treatment &
Finishing of
Aluminium and
Its Alloys"
by Wernick, Pinner
& Sheasby
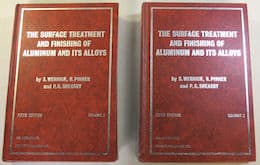
(note: this book is two volumes)
on eBay or
AbeBooks
or Amazon
(affil links)
A. You might check with a supplier of bright dip chemicals .
Please be advised that a bright dip, even a small one, is very dangerous since you are dealing with concentrated acids at very high temperatures. Use the appropriate safety gear. In addition, an operating bright dip typically has a scrubber system attached to the exhaust to prevent the release of nitrous oxides into the atmosphere.
As for the second question, considerable amounts of mechanically polished, chemically polished and/or electropolished aluminum is anodized and dyed. If the polishing and finishing are performed correctly you should have no problems.
- Minden, Nevada
2000
2000
A. Hi Heath !
Sjon Westre's comments about checking with your suppliers hits the nail on the head! I was never sure about the nitric concentrations, about 4% to 6% I thought, but you sure need a scrubber. 'tis the nitric that's a problem.
When the parts are removed you get excessive and heavy fuming. For large aluminum sheets, I've seen what looks like a tunnel with a top rail track. This tunnel is a total enclosure or shrouding that extends PAST both the beginning and the end of the bright dip tank AND it has 'curtains' (ss or plastic) to prevent the sudden billowing out of the fumes.
At the top of this 'tunnel' one had a plenum, PVC, to suck up all the fumes.
For small operations make sure your hood design is kopasetic, this is v. important, I think, in order to capture fumes at source.
At the same time why not also vent the sulfuric etch into this common scrubber although a good horizontal airflow l2 micron PVC mist eliminator will do the job more cheaply, I'd think.
However,I don't think that the system temperature rises significantly otherwise PVC would be nbg for the hood and ducting.
Food for thought. Cheers !
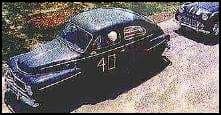
Freeman Newton [deceased]
(It is our sad duty to advise that Freeman passed away
April 21, 2012. R.I.P. old friend).
The safety factors as mentioned above probably preclude you from "trying" this bath out, however to answer your question bright dip solutions require fairly sophisticated controls to be run effectively. There are essentially two type bath compositions used; the first utilizes nitric 2.5-3.5% and phos acids 75-80%, dissolved aluminum 20-30 g/l, water is used to control the specific gravity. The second uses sulfuric 16-17%, nitric 8% and phos acids 75%, with trace amounts of copper .3 g/l usually obtained in situ from the form copper nitrate
⇦ this on
eBay
or
Amazon [affil links]
. Temperature control is critical. Both baths use fume suppressants typically diammonium phosphate, however a scrubber is still required! The chemical controls involve not only the concentrations of the chemicals but the control of the specific gravity which is based upon the dissolved aluminum content which varies over time.The best bath I have worked with was a scratch bath tightly controlled using the three acids and copper. However, unless you have a chemist setting up and controlling the bath, my suggestion would be to use a proprietary and I believe the one I have seen commonly used with good results is called Phosbrite and it was either
172 or 174 I forget which.I have been told on this website that the Bright Dipping booklet put out by Albright and Wilson is no longer available but I suspect you can still find a copy of it. It is pretty descriptive. I would also recommend an article written by Arthur Brace from Metal Information Services England titled The Role of Added Metals in the Chemical Brightening of Aluminum in a Phosphoric-sulfuric-Nitric Acid Mixture.
The two shops I have worked at which performed custom color anodizing used bright dipping frequently for recreational items such as bicycle parts, ski poles, rifle scopes and roller blades to name a few. Bright dips are an excellent way to achieve a high lustre brightly colored parts. If you use polished aluminum be sure to not etch after soak clean but to remove polishing compound through an ultrasonic cleaner or by hand washing. Otherwise the buffing or polishing compounds are a bear to remove prior to anodize. My suggestion is to use an experienced color anodizer who is set up to do this. I don't believe there is one in Wichita, the closest good ones I know of are in Colorado.
aerospace - Wichita, Kansas
2000
A. Don't fool yourself into thinking the only way to achieve a bright anodised finish is to use a chemical brightener; careful polishing and correct anodising controls can give far superior results
Keith Tranmerengineering services - England
2000
Thanks for the input, Keith, but could you be a little more explicit in what you are saying? Hundreds of millions of street light reflectors, other optical components, and general items of brightwork have been created by brite dipping and anodizing. It is hard to maintain that something else gives far superior results unless we qualify it pretty exactly. Electropolishing is an alternative which can give greater reflectivity on the correct (pure) aluminum alloys, but is more expensive. Thanks.
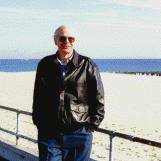
Ted Mooney, P.E.
Striving to live Aloha
finishing.com - Pine Beach, New Jersey
August , 2007
Can 2-year-old chemical polishing bath for aluminum be used?
October 10, 2016Q. Dear Sir,
As I have repeated many times without any doubt I am great fan and follower of this forum. 2 years back I prepared a bath for chemical polishing which involves chemical like Nitric acid , sulfuric acid and oath phosphoric acid. But due to some reason I could not operate it for more than 20 hours.
Now I wish to start again the same bath, I am facing quality issues in that bath. My queries are as follow :-
1) Streaks or flow marks of chemical are appearing on the aluminium profiles after brightening, what can be the problem ?
2) Does using bath after 2 years hamper quality? I mean do the chemical properties of bath get disturbed as it was unused for 2 years?
3) The bath emits less NOx fumes.
Please guide me, will 2 year old bath be the same or it needs to be discarded in ETP system ?
Thanking you in anticipation.
Regards
- Maharashtra, India
A. Hi Sumit. I'm not sure whether you are asking us whether a two-year-old bath will fume less, or you are telling us that it is fuming less. But I think that that's a hint to the answer. It seems to me from a general understanding rather than specific knowledge that NOx probably evolved as a gas from this bath over a period of two years and that you may be low on nitric acid. Do you have the ability to analyze this brite dip to see where it stands?
Regards,
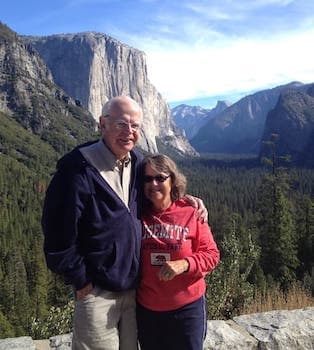
Ted Mooney, P.E. RET
Striving to live Aloha
finishing.com - Pine Beach, New Jersey
October 2016
A. Hi Sumit,
You should be able to restore the bath to working condition.
Unless it was sealed from the atmosphere it will have absorbed water and have a low specific gravity. It will be necessary to heat the bath to evaporate off this water. You need a hydrometer to check when the SG is optimum. If you will tell us the amounts of phosphoric and sulfuric acids that you used I can suggest a working SG range.
Nitric acid will be lost by evaporation and chemical reaction and will need to to replenished at least daily. So, it will be too low unless you have made very recent additions. Do you have the means of measuring nitric acid? It really is important to be able to do so.
You don't say, buy did you also add a copper salt in the make up and if so, which and how much?
One final point. As I have said, if you heat the bath nitric acid will be lost. Stainless steel relies on nitric to passivate it and prevent it dissolving. So, keep the nitric acid at 2% by volume even if you are not processing aluminium.
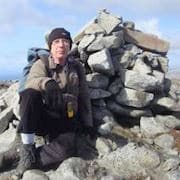
Harry Parkes
- Birmingham, UK
October 15, 2016
October 17, 2016
Q. Hello Mr. Ted,
To begin with , thanks for your reply and guidance. I think you are right the bath may contain low quantity of Nitric acid. When it was new and fresh, loads of NOx fumes used to emit from that dragin bath. But now hardly any fumes comes.
Can some one please help me to analyse this bright bath?
Hello Mr. Harry,
The specific gravity of the bath is 1.55. I don't know how to measure nitric in it. Can you please help me to give the titration method to measure nitric in the bright bath.
Phosphoric acid was something around 80-82%, sulfuric was about 7-10% Nitric was about 5% and rest was water. Its around 4000 litres of bath. I am heating upto 98 °C. Some times its viscosity increases, so for that I am adding water to it.
I have added copper sulphate
⇦ this on
eBay or
Amazon [affil links] around 4- 5 kgs in this bath.
Please help.
Thanking you in anticipation.
Regards.
- Ahmednagar Maharashtra India.
A. Hi Sumit,
I am assuming that when you quote additions of acids you are talking about 1.7 SG Phosphoric acid, 1.84 sulfuric acid and 1.4 SG nitric acid.
My preference would be to use rather more more sulfuric. I would add Phos and sulfuric acid in a ratio by volume of 5.5:1
The copper sulphate is low. I would add 16 kg per 4000 litres of Phos/sulfuric mixture aiming to get 1 g/l copper as Cu.
Nitric acid and water would be by analysis.
The SG is far too low: it should be 1.75 rather than 1.55.
Water should not be added by viscosity but by SG.
There are a couple of web links which I recommend. Particularly look at Table 3, Page 5 of the first item. It gives some very useful information on running brighteners.
You will also find the method for the analysis of nitric acid.
One warning I will give you regarding this method. The end point (a dark brown) relies on there being some nitric acid being present. If most of the nitric has been boiled off the you will not get the end point colouration and go on titrating until you have used up all your reagent!
Links:
• www.potashcorp.com/media/bright_dip_manual.pdf
Harry
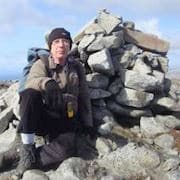
Harry Parkes
- Birmingham, UK
October 19, 2016-- apologies, finishing.com misfiled this reply, and didn't post it until December 1
Q. Hello Mr. Parkes
I owe you and this website a lot. I am really amazed the depth of knowledge. You people are really fantastic.
The answer to the post is really fruitful. I am just confused with a few lines of yours.
"My preference would be to use rather more more sulfuric. I would add Phos and sulfuric acid in a ratio by volume of 5.5:1"
The above lines are extract from your post.
I think word Phos is missing in first line and you mean to say that I should add Phos more than sulfuric in ratio of 5.5 : 1 . Please guide .
Once again thanks a tonne.
Your replies are highly appreciated.
Regards
N M Coating - Ahmednagar Maharashtra India.
You could test the bath:
1) Determine total acidity by titration with 1.0N NaOH [1N NaOH on
Amazon [affil links]
to methyl orange
⇦ this on
eBay or
Amazon [affil links]
endpoint.
2) Determine sulphate by Ba(NO3)2 precipitation.
3) Determine phosphate by Ca(NO3)2 precipitation.
2, and 3 via gravimetry.
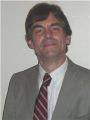
Dave Wichern
Consultant - The Bronx, New York
A. On reflection, barium phosphate is not terribly soluble, either. Saturation is at about 13 mg/l. BaSO4 is much less soluble. One would have to be very judicious as to sample size.
One could also determine PO4-3 via colorimetry.
Or, there is the titration of nitrate with ferrous sulfate
⇦ this on
eBay or
Amazon [affil links] , in ice cold sulfuric acid. Then:
1) Nitrate titration
2) Gravimetric determination of sulphate, with a very small sample.
3) Colorimetric PO4-3
Knotty problem!
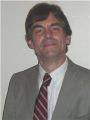
Dave Wichern
Consultant - The Bronx, New York
December 2, 2016
A. Hi Sumit,
Sorry for the further delay in replying after Ted's posting of 1st December.
Brightener is added to replace drag-out losses. I am not an analyst and mainly relied on specialist analysts. I know that they were unhappy about the methods described by Dave Wichern. My preference was to add phosphoric acid, sulfuric acid and copper sulphate in a set ratio to make up for drag-out and not need analysis of the working mix. Nitric acid, which is consumed by chemical reaction and evaporation, would be analysed daily as would be specific gravity (to control water). Aluminium content would be checked occasionally.
Purist chemists would probably prefer to measure the acid additions by weight. If you have a means measuring by weight than use it. But delicate mechanisms and bucket chemistry seldom make good bedfellows! So my preference would be for carefully calibrated volumetric vessels.
Hence, my suggestion that you make additions of 5.5 parts by volume 1.7 SG phosphoric acid to one part by volume 1.84 SG sulfuric acid.
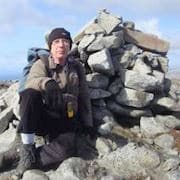
Harry Parkes
- Birmingham, UK
December 8, 2016
Q. Hello,
My question is about the working concentration of nitric acid used to brighten aluminum parts.
In our company we have nitric acid of concentration 50-55% so I need to know for example in a 500 liters tank how much nitric acid should I use.
Best regards,
Chemist Ahmad Gad
Maadi company for engineering industries - Cairo, Egypt
August 6, 2018
A. Hi Ahmad. We found a thread which discusses your topic in excellent detail, and appended your inquiry to it. After digesting it, please get back to us with any questions.
Regards,
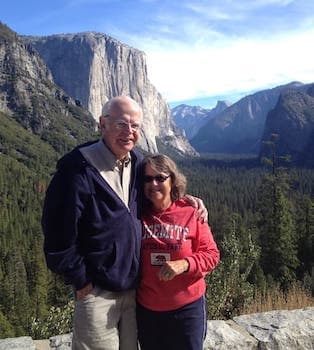
Ted Mooney, P.E. RET
Striving to live Aloha
finishing.com - Pine Beach, New Jersey
August 2018
Q. Sorry Sir, but I couldn't find this helpful as I was searching for concentration of nitric acid used for cleaning aluminum only (not as a prior step to anodizing) as all I want is cleaning and Brightening aluminum and without adding any chemicals like phosphoric or sulfuric acid to the tank, solely nitric acid is required.
How much nitric acid is needed in a 500 litres tank for example (available nitric acid in our site is 50 - 55%)
Best regards
Maadi company for engineering industries - Cairo, Egypt
August 6, 2018
A. Hi again Ahmed. Although I'm not familiar with using nitric acid for actual 'cleaning', it is sometimes used as a 'desmut' for aluminum, to remove traces of alloying copper and magnesium, at a concentration of maybe about half of your 50% to 55% stock solution. But two things to note …
First, you don't make up tanks from book knowledge; you do jar tests (beaker tests) with your grade of aluminum, your immersion times, and other factors, then you scale up from your successful finding to the production volumes.
Second, readers will generally not help you with "the math" of how much to add to your tank because there is a lot of potential for misunderstandings based on whether people are thinking of percentage by weight, or straight percentage by volume, or percentage by volume of a 'standard' but not 100% pure stock solution, etc … and some of our readers note rather insistently that if someone needs help with the math it's evidence that they have not have been trained sufficiently in chemical safety.
Please let us know what you learn from the jar test. Thanks!
Regards,
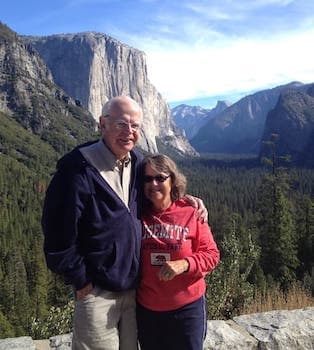
Ted Mooney, P.E. RET
Striving to live Aloha
finishing.com - Pine Beach, New Jersey
August 2018
February 14, 2019
Q. Dear Sir,
I have a small business for bright dipping for aluminum before entering the anodize process. My question is whether bright dipping solution can be operated at room temperature? Because of inadequate equipment, so far I have done it at 212 °F with the formula:
phosphoric acid - sulfuric acid - copper sulphate- Urea - water
80 - 3.9 - 0.1 - 2.0 - 4. if it can be done at ambient temperature, do you need to modify the formula?
Please help.
Thanking you in anticipation.
Regards.
Small Workshop - Jakarta, Indonesia
A. Hi Wahyu. Wernick, Pinner, & Sheasby discusses a number of formulations which operate at slightly lower temperature, but I don't think I saw anything there that works at ambient temperature or anything close to ambient.
by Larry Durney
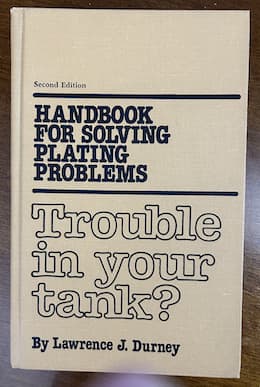
on Amazon
(currently UTL
on AbeBooks & eBay)
(affil links)
Bright dipping is rather hard to do robustly & consistently, totally free of small areas that didn't chemically polish correctly. A point that Durney makes in "Trouble in Your Tank" is that when you run into trouble, and everybody does, the only thing that will keep you from flailing about aimlessly is to start by making sure everything is exactly within spec ... and you're not going to be able to do that.
If you think that it's within your capability to develop a novel way of chemical polishing that doesn't require heated tanks, go for it! -- we all want better, simpler, ways to do things. But if you're asking how you can get reliably get satisfactory work from a known process without complying with the control parameters of that process, especially temperature, the answer is you can't :-)
Regards,
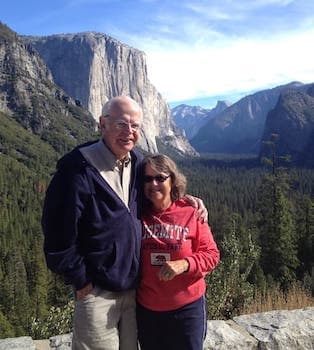
Ted Mooney, P.E. RET
Striving to live Aloha
finishing.com - Pine Beach, New Jersey
February 2019
A. If you come up with something that actually works there are an uncounted plethora of shops that would pay dearly to have it. For now we are stuck with the nasty stuff! And NO, electropolish isn't close enough
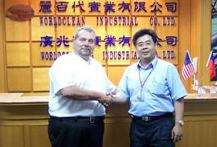
Drew Nosti, CEF
Anodize USA

Ladson, South Carolina
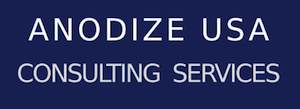
February 26, 2019
Q, A, or Comment on THIS thread -or- Start a NEW Thread